Top 12 Operations Manager Skills to Put on Your Resume
An Operations Manager plays a pivotal role in ensuring the smooth running of an organization's daily activities, requiring a unique blend of skills to effectively manage resources, processes, and people. Highlighting the top skills on your resume can significantly enhance your candidacy, demonstrating your ability to streamline operations, improve efficiency, and drive business success.
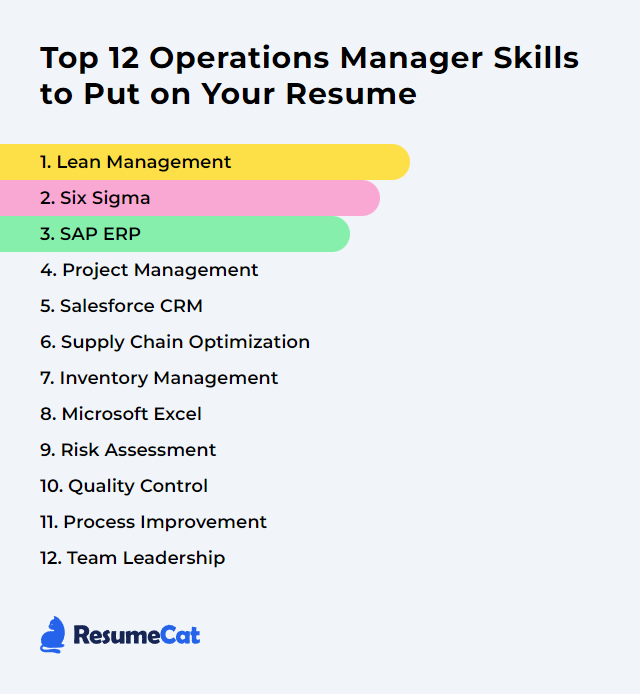
Operations Manager Skills
- Lean Management
- Six Sigma
- SAP ERP
- Project Management
- Salesforce CRM
- Supply Chain Optimization
- Inventory Management
- Microsoft Excel
- Risk Assessment
- Quality Control
- Process Improvement
- Team Leadership
1. Lean Management
Lean Management is a systematic approach focused on reducing waste, improving process efficiency, and maximizing value to the customer, all within a continuous improvement framework. For an Operations Manager, it involves streamlining operations, optimizing resources, and enhancing productivity to achieve operational excellence and customer satisfaction.
Why It's Important
Lean Management is important for an Operations Manager because it streamlines processes, reduces waste, enhances efficiency, and improves quality, leading to increased customer satisfaction and higher profitability.
How to Improve Lean Management Skills
Improving Lean Management, particularly for an Operations Manager, revolves around streamlining processes, eliminating waste, and enhancing value to the customer. Here are concise strategies:
Continuous Improvement: Embrace the Kaizen philosophy by encouraging continuous, incremental improvements. Empower employees to identify inefficiencies and suggest improvements. Kaizen Institute
Value Stream Mapping: Use Value Stream Mapping to visualize and understand the flow of materials and information as a product or service makes its way through the value stream. This helps in identifying bottlenecks and waste. Lean Enterprise Institute
Implement 5S: Deploy the 5S system (Sort, Set in order, Shine, Standardize, Sustain) to organize and maintain a productive work environment. It lays the foundation for disciplined work and quality products. ASQ - 5S
Adopt Just-In-Time (JIT): Implement JIT inventory management to reduce waste and improve efficiency by receiving goods only as they are needed in the production process. The Toyota Way
Empower Teams: Foster a culture of empowerment where teams are given the autonomy to make decisions and solve problems at their level. This increases engagement and accelerates problem resolution. Harvard Business Review - Empowerment
Leverage Technology: Utilize lean management software tools for process mapping, project management, and performance tracking to enhance visibility and control. Smartsheet - Lean Management Tools
Customer Focus: Regularly seek feedback from customers to understand their needs and expectations better, ensuring that the organization's focus remains on delivering value. Forbes - Customer Feedback
By systematically applying these strategies, an Operations Manager can significantly improve Lean Management in their organization.
How to Display Lean Management Skills on Your Resume
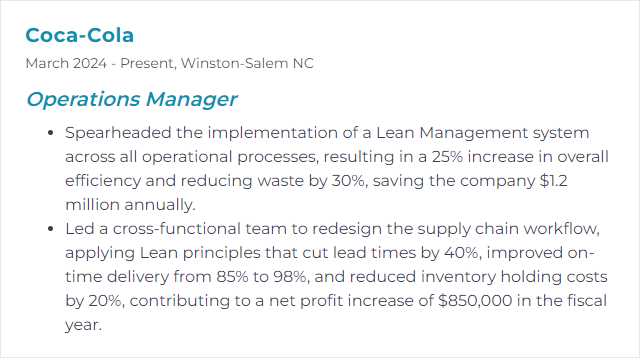
2. Six Sigma
Six Sigma is a data-driven methodology and set of techniques for process improvement aimed at reducing defects and variability in operations to improve quality and efficiency.
Why It's Important
Six Sigma is important for an Operations Manager because it provides a systematic approach to reduce defects and variability in processes, leading to improved quality, efficiency, and customer satisfaction, while also lowering costs and enhancing overall operational performance.
How to Improve Six Sigma Skills
Improving Six Sigma as an Operations Manager involves focusing on continuous improvement, team engagement, and leveraging technology. Here’s a concise guide:
Continuous Learning: Encourage and participate in ongoing Six Sigma education to stay updated with methodologies and tools. ASQ's Six Sigma Training is a good resource.
Process Automation: Use technology to automate repetitive tasks, minimizing errors and freeing up time for value-added activities. UiPath offers solutions for process automation.
Data-Driven Decision Making: Leverage advanced analytics tools to analyze process data, helping identify inefficiencies and improvement opportunities. Tableau can enhance your data visualization and analysis.
Cross-Functional Teams: Foster collaboration across departments to ensure the Six Sigma initiatives align with overall business goals. Monday.com facilitates project management and team collaboration.
Customer Feedback: Regularly collect and analyze customer feedback to align process improvements with customer expectations. SurveyMonkey is a tool to gather insights.
Benchmarking: Regularly compare processes against industry standards or leaders to identify areas for improvement. Research through Benchmarking Network can be valuable.
Implementing these strategies can significantly enhance Six Sigma efforts in operations management, leading to improved efficiency and customer satisfaction.
How to Display Six Sigma Skills on Your Resume
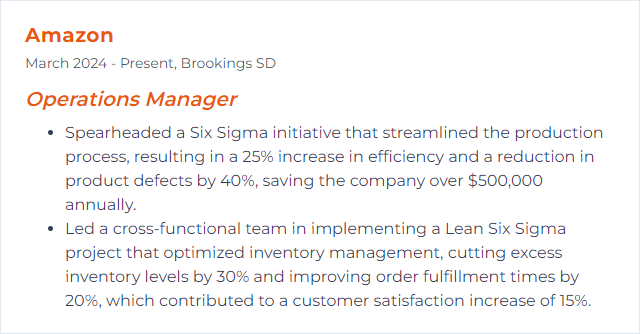
3. SAP ERP
SAP ERP is an enterprise resource planning software that integrates core business processes such as finance, HR, manufacturing, and supply chain, enabling operations managers to streamline operations, improve efficiency, and make data-driven decisions.
Why It's Important
SAP ERP is crucial for an Operations Manager as it integrates core business processes, enhancing efficiency, improving decision-making with real-time data, and streamlining operations across the organization, leading to reduced costs and increased productivity.
How to Improve SAP ERP Skills
Improving SAP ERP for an Operations Manager involves optimizing system performance, enhancing user experience, and integrating new technologies. Here are concise strategies:
Streamline Processes: Reevaluate and simplify workflows and processes within SAP to improve efficiency. SAP Best Practices can guide optimization.
Training and Support: Invest in regular training and support for users to ensure they are utilizing SAP ERP features effectively. SAP Learning Hub offers resources and training modules.
Data Management: Implement strict data management and quality practices to ensure accurate and reliable data for decision-making. SAP Master Data Governance can help in maintaining high-quality data.
Integrate New Technologies: Explore and integrate new technologies like AI, IoT, and machine learning for predictive analytics and automation. SAP’s Intelligent Technologies offers insights into these innovations.
Regular System Audits and Updates: Conduct regular system audits to identify areas for improvement and ensure the ERP system is up-to-date with the latest patches and updates. SAP Notes and Support can be a resource for updates and fixes.
Customization and Scalability: Customize SAP ERP to fit specific business needs while keeping scalability in mind. Consider SAP’s Custom Development services for tailored solutions.
Feedback Loop: Establish a continuous feedback loop with users to gather insights and make necessary adjustments. Tools like SAP User Experience Management by Knoa provide valuable user feedback for system improvement.
By focusing on these areas, an Operations Manager can significantly improve the efficiency and effectiveness of their organization's SAP ERP system.
How to Display SAP ERP Skills on Your Resume

4. Project Management
Project management involves planning, organizing, and overseeing tasks and resources to achieve specific goals within a defined timeline, ensuring projects are completed efficiently and effectively. For an Operations Manager, it means coordinating operations to meet project milestones while optimizing performance and resource allocation.
Why It's Important
Project management is crucial for an Operations Manager as it ensures efficient organization and execution of projects, enabling the delivery of quality outcomes within budget and time constraints, while aligning with the strategic goals of the organization. It facilitates optimal resource allocation, risk management, and process standardization, enhancing overall operational performance and competitiveness.
How to Improve Project Management Skills
Improving project management, especially from an Operations Manager's perspective, involves a strategic blend of planning, execution, and monitoring. Here are concise tactics to enhance project management skills:
1. Define Clear Objectives: Establishing clear, achievable goals is fundamental. MindTools offers insights on setting SMART goals.
2. Prioritize Projects: Use prioritization tools such as the Eisenhower Matrix to focus on what's urgent and important.
3. Embrace Project Management Software: Tools like Asana or Trello enhance collaboration and tracking.
4. Improve Communication: Adopt strategies from Project Management Institute (PMI) to foster clear, open communication channels.
5. Monitor and Adjust: Utilize KPIs and regular reviews to track progress, making adjustments as needed. Scoro provides a list of KPIs to monitor.
6. Learn from Every Project: Implement a lessons-learned process to continuously improve. ProjectManagement.com discusses structuring this process.
7. Invest in Professional Development: Ongoing training in project management methodologies can be highly beneficial. Consider certifications or courses from Coursera or PMI.
By focusing on these key areas, Operations Managers can significantly improve the efficiency and effectiveness of their project management efforts.
How to Display Project Management Skills on Your Resume
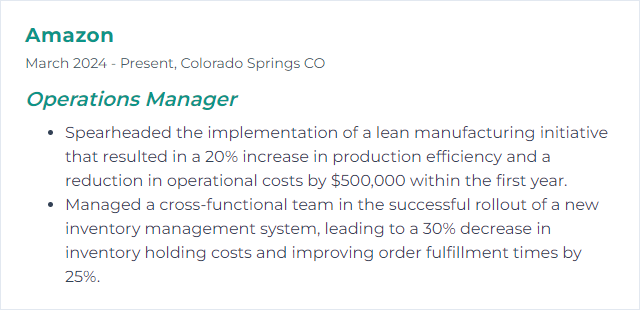
5. Salesforce CRM
Salesforce CRM is a cloud-based platform that centralizes customer information, streamlines sales processes, and improves customer service, enabling operations managers to efficiently manage business operations and make data-driven decisions.
Why It's Important
Salesforce CRM is important for an Operations Manager because it streamlines customer data management and business processes, enhancing efficiency, improving customer satisfaction, and driving sales growth.
How to Improve Salesforce CRM Skills
To improve Salesforce CRM as an Operations Manager, focus on these key areas:
Customization: Tailor Salesforce to match your business processes by customizing objects, fields, and layouts. Use Salesforce's customization guide for detailed steps.
Integration: Enhance efficiency by integrating Salesforce with other business tools (e.g., marketing automation, ERP systems). Explore available integrations on the Salesforce AppExchange.
Automation: Implement automation with Salesforce's Workflow Rules and Process Builder to streamline operations and reduce manual tasks. Start with the Automation Guide.
Training and Adoption: Boost user adoption by providing comprehensive training and support. Salesforce offers resources through Trailhead, its interactive learning platform.
Data Quality: Ensure high data quality by establishing data entry standards and using tools like duplicate management. Refer to Salesforce's Data Quality Guide for best practices.
Analytics and Reporting: Utilize Salesforce reports and dashboards to gain insights into your operations and make informed decisions. Learn more through the Analytics Basics.
Regular Reviews and Updates: Keep your Salesforce CRM optimized by regularly reviewing and updating configurations, permissions, and user needs.
Focusing on these areas will help maximize the efficiency and effectiveness of Salesforce CRM within your organization.
How to Display Salesforce CRM Skills on Your Resume
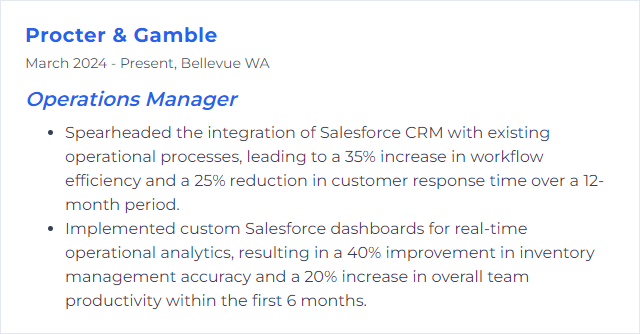
6. Supply Chain Optimization
Supply Chain Optimization refers to the process of enhancing the efficiency and effectiveness of the supply chain operations by minimizing costs and maximizing customer satisfaction. For an Operations Manager, it involves strategically managing and coordinating the procurement, production, inventory, and distribution aspects to meet customer demands while optimizing resources and reducing waste.
Why It's Important
Supply chain optimization is crucial for an Operations Manager because it directly impacts the efficiency and cost-effectiveness of operations, ensuring timely delivery of products, minimizing waste, and enhancing customer satisfaction, thereby improving the company's competitiveness and profitability.
How to Improve Supply Chain Optimization Skills
To improve Supply Chain Optimization, an Operations Manager must focus on several key areas:
Demand Forecasting: Enhance accuracy by leveraging advanced analytics and AI. Tools like IBM's Supply Chain Insights can help in predicting demands more accurately.
Inventory Management: Implement Just-In-Time (JIT) inventory practices to reduce holding costs and increase efficiency. Kanban Tool offers visual management software to streamline this process.
Supplier Relationship Management: Foster strong relationships with suppliers to ensure reliability and cost-effectiveness. Platforms like SAP Ariba can streamline collaboration with suppliers.
Technology Integration: Adopt technologies such as IoT, blockchain, and cloud computing for real-time tracking and better transparency. Oracle's Blockchain Supply Chain can help secure and streamline supply chain operations.
Lean Practices: Implement Lean manufacturing principles to minimize waste and optimize processes. The Lean Enterprise Institute offers resources and workshops on applying lean principles to supply chains.
Continuous Improvement: Encourage a culture of continuous improvement (Kaizen) to constantly refine and enhance supply chain operations. ASQ's Continuous Improvement offers strategies and tools for ongoing optimization.
By focusing on these areas and leveraging appropriate tools and technologies, operations managers can significantly improve supply chain optimization.
How to Display Supply Chain Optimization Skills on Your Resume
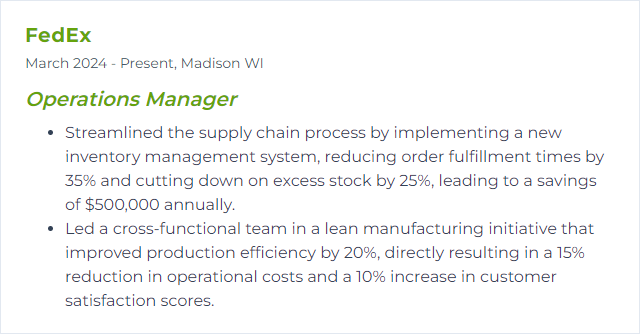
7. Inventory Management
Inventory Management is the process of overseeing and controlling the ordering, storing, and use of components or products an organization uses in production or sells. It involves managing stock levels, optimizing storage costs, and ensuring timely availability of items to meet customer demand without overstocking, for efficient and cost-effective operations.
Why It's Important
Inventory management is crucial for an Operations Manager as it ensures the right balance of stock is maintained to meet customer demand without overstocking, thereby optimizing operational efficiency, reducing costs, and maximizing profitability.
How to Improve Inventory Management Skills
Improving inventory management involves a strategic approach to optimize stock levels, reduce costs, and enhance customer satisfaction. Here are concise steps for an Operations Manager:
Implement an Inventory Management System: Adopt a robust inventory management software that offers real-time tracking, forecasting, and analytics. Shopify's guide provides a comprehensive overview.
Regular Auditing: Conduct regular audits (physical counts, spot checking, or cycle counting) to ensure inventory accuracy. TradeGecko elaborates on different auditing methods.
Demand Forecasting: Use historical data and market analysis to predict future sales trends. This improves stock levels and reduces holding costs. IBM's insights on demand forecasting offer valuable strategies.
Optimize Stock Levels: Implement Just-In-Time (JIT) inventory to minimize holding costs and reduce waste. Kanbanize explains JIT in detail.
Supplier Management: Develop strong relationships with multiple suppliers to ensure reliability and negotiate better terms. Harvard Business Review’s article on supplier onboarding offers insights on improving supplier relationships.
Continuous Improvement: Adopt a Kaizen approach for continuous improvement in inventory management processes. ASQ provides a primer on Kaizen and its benefits.
Leverage Technology: Integrate advanced technologies such as IoT, RFID, and AI for efficient tracking and management. Zebra Technologies discusses RFID applications in inventory management.
Cross-Functional Training: Ensure your staff is well-trained across different functions to improve flexibility and understanding of inventory processes. MindTools offers strategies on cross-training employees.
By strategically implementing these steps, operations managers can significantly improve inventory management within their organizations.
How to Display Inventory Management Skills on Your Resume
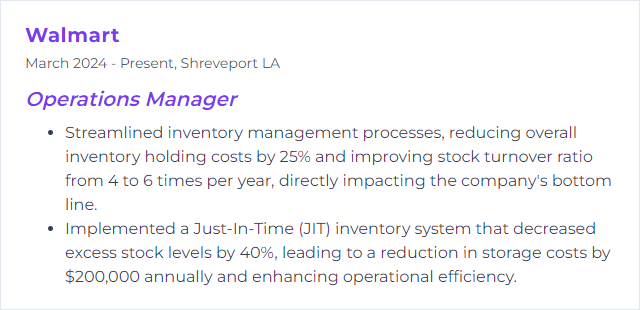
8. Microsoft Excel
Microsoft Excel is a spreadsheet software used for organizing, analyzing, and storing data, crucial for operations management tasks such as inventory tracking, budgeting, and scheduling.
Why It's Important
Microsoft Excel is essential for an Operations Manager as it facilitates efficient data analysis, budgeting, forecasting, and resource allocation, enabling informed decision-making and operational optimization.
How to Improve Microsoft Excel Skills
To improve Microsoft Excel skills for an Operations Manager, focus on mastering the following:
Advanced Formulas: Understand complex formulas that can automate tasks and analyze data efficiently. ExcelJet Advanced Formulas Guide.
PivotTables: Learn to summarize, analyze, explore, and present your data quickly. Microsoft PivotTable Tutorial.
Data Visualization: Enhance your ability to present data visually using charts and graphs. Data Visualization in Excel.
Power Query: Use Power Query to import, transform, and automate your data preparation. Getting Started with Power Query.
Macros and VBA: Automate repetitive tasks and enhance Excel's functionality. Introduction to Macros and VBA.
Data Validation and Conditional Formatting: Improve data integrity and highlight critical information. Data Validation Guide, Conditional Formatting.
Focusing on these areas will significantly enhance your Excel skills, making data management and analysis more efficient and effective for operational management.
How to Display Microsoft Excel Skills on Your Resume
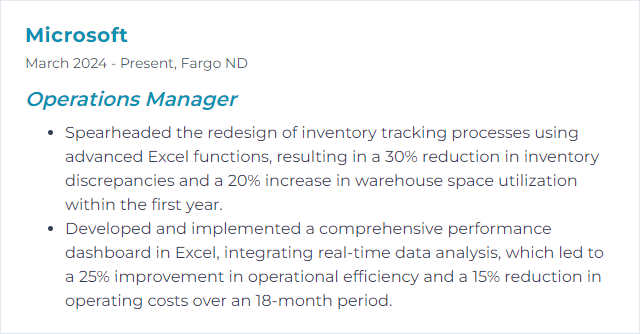
9. Risk Assessment
Risk assessment is the process of identifying, analyzing, and evaluating potential risks to minimize their impact on an organization's operations, ensuring smooth and efficient workflow and safeguarding assets and personnel.
Why It's Important
Risk assessment is important for an Operations Manager because it helps identify, analyze, and prioritize potential risks to the operation, enabling the development of strategies to mitigate, manage, or eliminate these risks, ensuring business continuity, safety, and regulatory compliance.
How to Improve Risk Assessment Skills
Improving risk assessment involves a systematic and continuous approach to identifying, analyzing, and mitigating potential risks that could impact operations. As an Operations Manager, focus on the following key steps:
Identify Risks: Use tools and techniques like SWOT analysis (SWOT Analysis Guide) and PESTLE analysis (PESTLE Analysis Guide) to systematically identify potential risks.
Analyze Risks: Assess the likelihood and impact of identified risks using qualitative and quantitative methods. Tools like Risk Matrix (Risk Matrix Guidelines) can be helpful.
Prioritize Risks: Prioritize risks based on their severity and likelihood. The Risk Impact/Probability Chart (Risk Impact/Probability Chart) is a useful tool for this step.
Implement Controls: Develop and implement strategies to mitigate high-priority risks. This could involve preventive measures or contingency plans. The ISO 31000 (ISO 31000:2018) provides guidelines on risk management principles and strategies.
Monitor and Review: Continuously monitor the risk environment and the effectiveness of your risk management strategies. Adjust as necessary to address new or changing risks.
Communication and Consultation: Ensure continuous communication and consultation with stakeholders throughout the risk management process. This ensures that everyone is aware of the risks and the steps being taken to manage them.
Documentation: Keep detailed records of the risk assessment process, including identification, analysis, decisions made, and reasons for those decisions. This will help in future assessments and in demonstrating compliance with regulations.
For a deeper understanding and more extensive strategies, consider exploring resources and training offered by the Project Management Institute on risk management practices.
How to Display Risk Assessment Skills on Your Resume
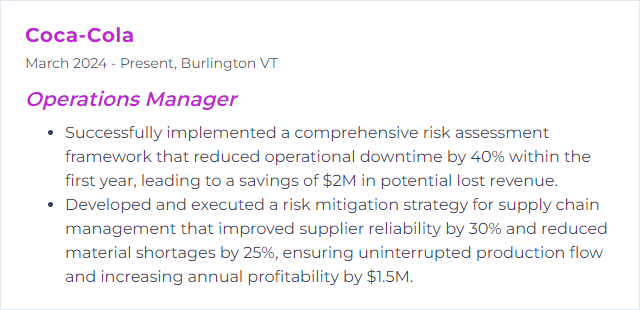
10. Quality Control
Quality Control (QC) is a process by which an Operations Manager ensures that the products or services produced by a company meet the required standards of quality. It involves the systematic inspection, testing, and verification of processes and outputs to detect and correct defects, aiming to minimize errors and enhance customer satisfaction.
Why It's Important
Quality Control is crucial for an Operations Manager as it ensures product/service consistency, reduces waste and rework, enhances customer satisfaction, and maintains brand reputation, ultimately leading to higher profitability and competitive advantage.
How to Improve Quality Control Skills
Improving Quality Control as an Operations Manager involves a strategic approach focused on process optimization, employee involvement, and continuous improvement. Here are concise steps to enhance your quality control measures:
Define Quality Standards: Clearly outline the quality standards for products and services based on customer expectations and industry benchmarks. Learn more about setting quality standards.
Implement Process Controls: Use statistical process control (SPC) tools to monitor and control manufacturing processes. This helps in identifying process variations early. Explore process controls.
Employee Training: Regularly train employees on quality control procedures and the importance of quality standards. Empowering employees with the right knowledge and skills is crucial. Check out training tips.
Supplier Quality Management: Ensure your suppliers adhere to your quality standards. Implementing a supplier quality management system can help in maintaining quality in the supply chain. Understand supplier quality management.
Regular Audits and Inspections: Conduct regular quality audits and inspections to identify non-conformances and areas for improvement. Audit and inspection guidance.
Feedback Loops: Establish a feedback loop with customers and employees to continuously collect insights on quality issues and improvement opportunities. Learn about establishing feedback loops.
Continuous Improvement: Adopt continuous improvement methodologies like Six Sigma and Lean to systematically reduce waste and improve quality. Introduction to continuous improvement.
Utilize Quality Management Systems (QMS): Implement a QMS like ISO 9001 to standardize quality control processes across the organization. ISO 9001 fundamentals.
By following these steps and leveraging the resources provided, Operations Managers can significantly improve quality control within their organizations.
How to Display Quality Control Skills on Your Resume
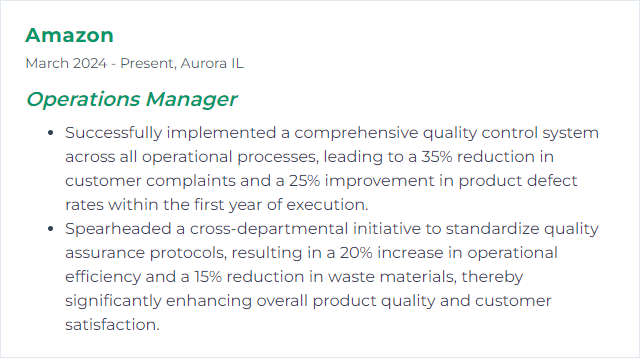
11. Process Improvement
Process Improvement is the systematic approach to enhancing the efficiency and effectiveness of business operations by identifying, analyzing, and optimizing existing processes to reduce waste, increase quality, and achieve better performance outcomes. For an Operations Manager, it involves continuously seeking ways to improve operational workflows and procedures to boost productivity, reduce costs, and enhance customer satisfaction.
Why It's Important
Process improvement is crucial for an Operations Manager as it enhances efficiency, reduces costs, increases productivity, and improves product or service quality, ensuring competitive advantage and customer satisfaction.
How to Improve Process Improvement Skills
Improving Process Improvement as an Operations Manager involves a strategic approach to enhance efficiency, reduce waste, and improve quality. Here's a concise guide:
Identify Key Processes: Begin by identifying and mapping out critical processes that impact operational efficiency and customer satisfaction. Tools like Process Flowcharts can be instrumental.
Set Clear Objectives: Define clear, measurable goals for process improvement. Objectives should align with broader organizational goals and customer expectations.
Implement Lean Principles: Adopt Lean methodologies to minimize waste and maximize value. Focus on streamlining processes, eliminating non-value-added activities, and improving flow.
Utilize Six Sigma: Incorporate Six Sigma techniques to reduce process variation and enhance quality. This data-driven approach aims to achieve near-perfection in process outputs.
Leverage Technology: Invest in technology solutions that automate repetitive tasks, improve data accuracy, and facilitate real-time monitoring. Explore options like ERP systems and process automation tools.
Encourage Team Involvement: Engage your team in the process improvement initiative. Foster an environment where employees can contribute ideas and feedback. Tools like Kaizen promote continuous, incremental improvements.
Measure and Analyze: Track progress against your objectives using Key Performance Indicators (KPIs). Utilize data analysis tools to identify trends, bottlenecks, and areas for further improvement.
Iterate and Refine: Process improvement is ongoing. Regularly review processes, incorporate feedback, and make necessary adjustments. Stay agile and be prepared to iterate based on changing business needs or new insights.
By focusing on these steps, Operations Managers can drive significant improvements in process efficiency, quality, and overall operational effectiveness.
How to Display Process Improvement Skills on Your Resume
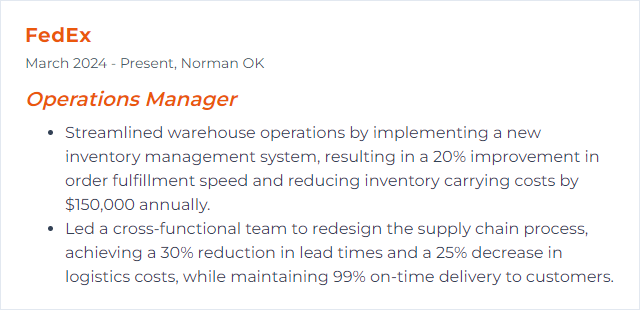
12. Team Leadership
Team leadership, in the context of an Operations Manager, involves guiding, motivating, and directing a group of individuals towards achieving operational goals efficiently and effectively while fostering collaboration, improving performance, and ensuring the alignment of team efforts with organizational objectives.
Why It's Important
Team leadership is crucial for an Operations Manager as it directly influences the team's productivity, efficiency, and morale, ensuring alignment with organizational goals and smooth day-to-day operations.
How to Improve Team Leadership Skills
Improving team leadership, especially for an Operations Manager, involves a combination of clear communication, effective delegation, fostering a positive team culture, and continuous improvement. Here are concise strategies:
Clear Communication: Ensure goals, expectations, and feedback are communicated clearly and regularly. MindTools offers techniques for improving communication skills.
Effective Delegation: Delegate tasks based on individual strengths and capabilities, allowing team members to grow. Harvard Business Review discusses the importance of delegation.
Positive Team Culture: Build a team culture based on trust, respect, and collaboration. Forbes provides strategies for cultivating a thriving team culture.
Continuous Improvement: Encourage and facilitate continuous learning and improvement for yourself and your team. LinkedIn Learning offers courses on leadership and management for ongoing development.
Feedback and Recognition: Regularly provide constructive feedback and recognize accomplishments to motivate and guide your team. Gallup explains the impact of recognition on employee performance.
By focusing on these areas, an Operations Manager can enhance their leadership skills, contributing to a more effective, motivated, and cohesive team.
How to Display Team Leadership Skills on Your Resume
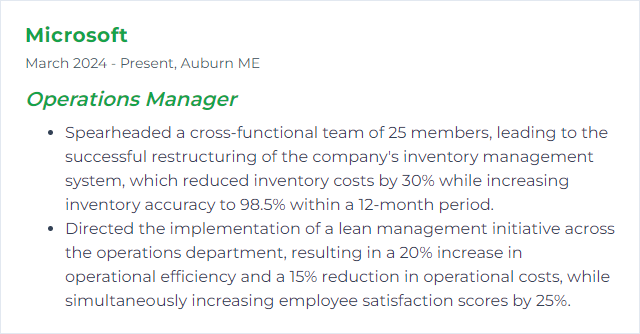