Top 12 Maintenance Mechanic Skills to Put on Your Resume
In today's competitive job market, standing out as a maintenance mechanic requires more than just a basic understanding of tools and machinery. A well-crafted resume highlighting a blend of technical expertise, problem-solving abilities, and soft skills can significantly enhance your job prospects, positioning you as a versatile and valuable candidate in the field.
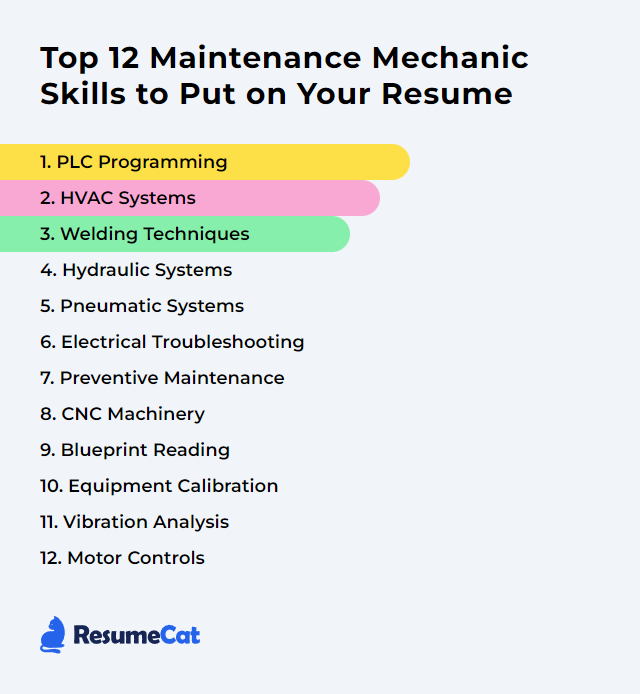
Maintenance Mechanic Skills
- PLC Programming
- HVAC Systems
- Welding Techniques
- Hydraulic Systems
- Pneumatic Systems
- Electrical Troubleshooting
- Preventive Maintenance
- CNC Machinery
- Blueprint Reading
- Equipment Calibration
- Vibration Analysis
- Motor Controls
1. PLC Programming
PLC programming involves creating and modifying computer instructions to control the operations of machines and processes in an industrial setting, enabling automation and efficient control of machinery for maintenance mechanics.
Why It's Important
PLC programming is crucial for a Maintenance Mechanic as it enables the automation of machinery, resulting in increased efficiency, precision in operations, and reduced downtime by facilitating quick troubleshooting and repairs of automated systems.
How to Improve PLC Programming Skills
Improving PLC programming skills, especially for a Maintenance Mechanic, involves understanding both the theoretical aspects of PLC systems and gaining practical experience. Here are concise steps and resources to help you improve:
Learn the Basics: Start with understanding the fundamentals of PLCs including how they work, basic programming concepts, and hardware components. Online courses and tutorials can be beneficial. PLC Academy is a good starting point.
Practice Programming: Get hands-on experience by practicing programming. Use simulation software like RSLogix 500 for Allen-Bradley PLCs or TIA Portal for Siemens PLCs to write and test codes.
Understand Ladder Logic: Most PLC programming involves Ladder Logic. Familiarize yourself with its symbols, structure, and how it’s used to represent electrical circuits. PLCS.net offers free resources and tutorials.
Study Real-world Applications: Examine real-world PLC applications within your industry. This can help you understand how to troubleshoot and modify programs effectively. Websites like AutomationDirect provide various application examples.
Continuous Learning: Technologies and standards evolve, so it's important to stay updated. Join forums like PLCTalk where professionals discuss issues and solutions.
Get Certified: Consider obtaining certifications from recognized bodies or manufacturers. This can validate your skills and knowledge. For example, Rockwell Automation offers training and certification for various levels of expertise.
Hands-on Experience: Nothing beats actual hands-on experience. Volunteer or take on projects that allow you to work directly with PLCs. This practical experience is invaluable.
By following these steps and utilizing the linked resources, you can significantly improve your PLC programming skills.
How to Display PLC Programming Skills on Your Resume
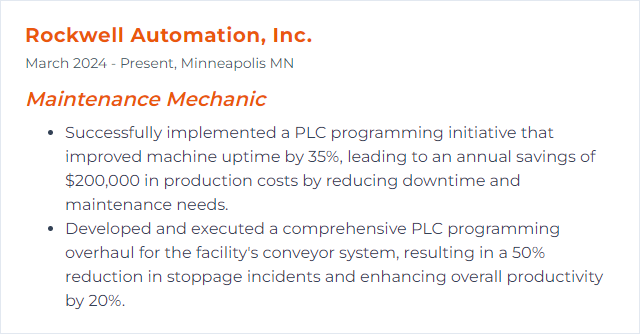
2. HVAC Systems
HVAC systems, standing for Heating, Ventilation, and Air Conditioning, are crucial in controlling the indoor climate of a building. They ensure comfortable temperatures, adequate ventilation, and maintain air quality. For a Maintenance Mechanic, it involves the upkeep, troubleshooting, and repair of these systems to ensure their efficient and safe operation.
Why It's Important
HVAC systems are crucial for maintaining comfortable indoor temperatures, ensuring good air quality, and reducing humidity levels, which are essential for the well-being of occupants and the longevity of building structures and equipment. For a Maintenance Mechanic, they are vital to ensure energy efficiency, system reliability, and to prevent costly breakdowns and repairs.
How to Improve HVAC Systems Skills
Improving HVAC systems involves a combination of regular maintenance, efficiency upgrades, and smart management practices. Here's a concise guide for a Maintenance Mechanic:
Regular Maintenance: Ensure routine checks and cleaning of filters, coils, and ducts to improve airflow and system efficiency. Filter Maintenance Guide.
Sealing and Insulation: Improve duct sealing and insulation to prevent air leaks, enhancing system efficiency. Duct Sealing Tips.
Thermostat Management: Install programmable thermostats to better control temperatures and reduce energy consumption. Thermostat Guide.
Upgrade Equipment: Consider upgrading to ENERGY STAR-rated HVAC equipment to increase energy efficiency and reduce costs. Energy Star Products.
System Tuning: Regularly tune the HVAC system to ensure it operates at peak performance, including checking refrigerant levels and electrical connections. System Maintenance Checklist.
Ventilation Improvements: Enhance ventilation to improve indoor air quality and system efficiency. Ventilation Strategies.
By focusing on these areas, a Maintenance Mechanic can significantly improve the performance and efficiency of HVAC systems.
How to Display HVAC Systems Skills on Your Resume
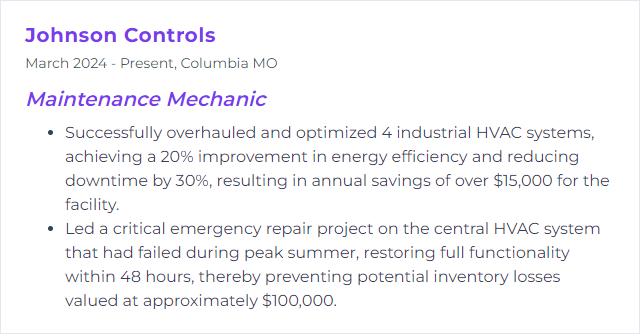
3. Welding Techniques
Welding techniques for a Maintenance Mechanic involve methods for joining metal parts using heat, pressure, or both. Key techniques include:
- Arc Welding (e.g., SMAW): Using an electric arc between an electrode and base metal to melt metals at the welding point.
- MIG Welding (GMAW): Utilizing a wire feeding gun to melt wire electrode and join materials.
- TIG Welding (GTAW): Employing a non-consumable tungsten electrode to produce the weld, offering high precision.
- Oxy-Acetylene Welding: Combining oxygen and acetylene to create a flame for welding, cutting, or brazing.
Each technique has its unique applications, tools, and safety requirements, vital for a Maintenance Mechanic to perform repairs and fabricate parts across various industries.
Why It's Important
Welding techniques are crucial for a Maintenance Mechanic because they enable precise, strong repairs and fabrications, ensuring machinery and structural integrity, reducing downtime, and extending equipment lifespan.
How to Improve Welding Techniques Skills
Improving welding techniques as a Maintenance Mechanic involves practice, understanding welding fundamentals, and staying updated with advancements in welding technologies. Below are concise tips with relevant resources:
Understand Welding Basics: Start with a strong foundation in welding principles, including types of welding processes, materials compatibility, and safety practices. Miller Welds offers comprehensive guides and tips.
Practice Consistently: Hands-on practice is crucial. Try varying materials and welding positions. Record your settings and results to refine your technique. Welding Tips and Tricks provides practical advice for improvement.
Learn from Others: Join forums or communities like WeldingWeb to exchange knowledge, tips, and experiences with fellow welders.
Stay Updated: Welding technology evolves. Keep up with the latest equipment and techniques by following industry leaders and manufacturers. Lincoln Electric frequently updates its how-to section with innovative methods and tools.
Safety First: Always prioritize safety to prevent accidents and ensure the longevity of your welding career. Familiarize yourself with the latest safety standards and personal protective equipment (PPE). OSHA’s Welding, Cutting, and Brazing guide is an essential resource.
Seek Feedback: Have a more experienced welder review your work and provide constructive feedback. This can pinpoint areas for improvement you might have missed.
Certification and Training: Consider obtaining certifications or attending workshops for advanced techniques. This not only hones your skills but also validates your expertise. The American Welding Society offers various certification programs.
Dedicating time to learn and apply these tips, coupled with a commitment to continuous improvement, will significantly enhance your welding techniques as a Maintenance Mechanic.
How to Display Welding Techniques Skills on Your Resume
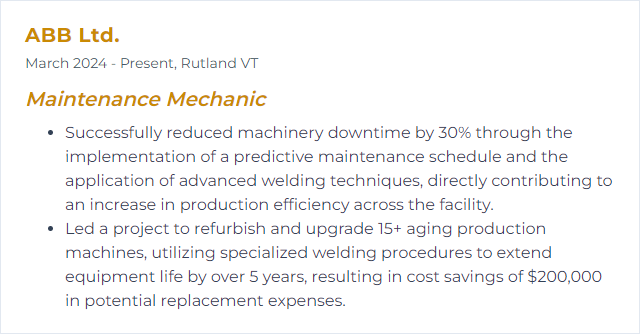
4. Hydraulic Systems
Hydraulic systems use pressurized fluid to generate, control, and transmit power. They're utilized in machinery for lifting, turning, and moving heavy loads, essential for a Maintenance Mechanic to maintain and troubleshoot for efficient operation.
Why It's Important
Hydraulic systems are crucial for a maintenance mechanic because they enable the efficient transmission of power to operate machinery, achieve precise control and movement, and maintain heavy loads with reliability and ease, thus ensuring smooth and effective maintenance processes.
How to Improve Hydraulic Systems Skills
Improving hydraulic systems for a maintenance mechanic involves several key steps aimed at enhancing efficiency, reliability, and longevity. Here’s a concise guide:
Regular Maintenance: Adhere to a scheduled maintenance plan that includes checking hoses, fittings, fluid levels, and filters. Preventive maintenance helps identify issues before they escalate. Hydraulic Maintenance Tips.
Fluid Quality: Use the correct hydraulic fluid and maintain its cleanliness. Contaminated fluid is a common cause of hydraulic system failure. Regularly check and replace the fluid if necessary. Hydraulic Fluid Management.
System Monitoring: Implement condition monitoring tools to track system performance and predict failures before they occur. Techniques include temperature, pressure, and flow rate monitoring. Condition Monitoring.
Upgrade Components: Replace older components with modern, more efficient versions. Upgrades can improve system performance and reduce energy consumption. Upgrading Hydraulic Systems.
Training: Ensure ongoing training for maintenance personnel on the latest hydraulic technologies and maintenance techniques. Knowledge is crucial for efficient troubleshooting and repairs. Hydraulic Training.
By focusing on these areas, a maintenance mechanic can significantly improve the performance and reliability of hydraulic systems.
How to Display Hydraulic Systems Skills on Your Resume
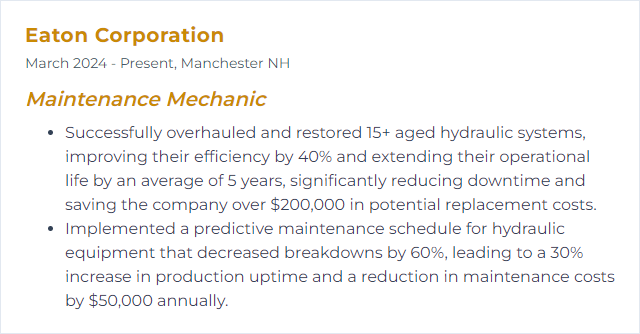
5. Pneumatic Systems
Pneumatic systems use compressed air to transmit and control energy, operating various machinery and equipment in industrial settings. Maintenance mechanics ensure these systems are properly installed, maintained, and repaired for optimal performance.
Why It's Important
Pneumatic systems are important for a Maintenance Mechanic because they provide a reliable, efficient, and cost-effective means of powering and controlling machinery and tools, utilizing compressed air to perform various tasks with precision and speed, enhancing productivity and reducing downtime.
How to Improve Pneumatic Systems Skills
To improve pneumatic systems as a Maintenance Mechanic, focus on fundamental aspects like system inspection, leak detection, and component maintenance. Implementing these practices ensures efficient operation and longevity of pneumatic systems.
Regular Inspection: Schedule and conduct regular inspections of the entire pneumatic system, including compressors, valves, hoses, and fittings. This helps in identifying wear and tear or potential issues before they escalate. Pneumatic System Inspection Guide.
Leak Detection and Repair: Use ultrasonic leak detectors or soap water solution to find and fix leaks in the system. Even small leaks can significantly reduce system efficiency. Leak Detection Techniques.
Proper Lubrication: Ensure all moving parts are adequately lubricated to reduce friction and wear. Use the correct type of lubricant as recommended by the equipment manufacturer. Lubrication Best Practices.
Clean Air Supply: Install air filters and regularly replace or clean them to prevent dust, oil, and moisture from entering the system. Clean air extends the life of pneumatic components. Air Quality in Pneumatic Systems.
Update and Upgrade: Consider upgrading older components with newer, more efficient models. Modern pneumatic components often offer better performance and energy efficiency. Advancements in Pneumatic Technology.
By focusing on these areas, Maintenance Mechanics can significantly improve the performance and reliability of pneumatic systems.
How to Display Pneumatic Systems Skills on Your Resume
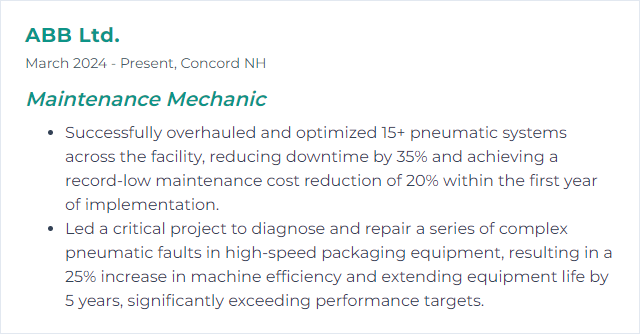
6. Electrical Troubleshooting
Electrical troubleshooting for a Maintenance Mechanic involves systematically diagnosing and fixing issues with electrical circuits or systems to ensure they operate correctly and safely.
Why It's Important
Electrical troubleshooting is crucial for a Maintenance Mechanic as it ensures the safe, efficient operation of machinery and equipment, reducing downtime, preventing costly repairs, and enhancing workplace safety by identifying and fixing electrical faults promptly.
How to Improve Electrical Troubleshooting Skills
Improving electrical troubleshooting skills, especially for a Maintenance Mechanic, involves a blend of theoretical knowledge, practical experience, and continuous learning. Here are concise steps with inline linking for further exploration:
Understand Basic Electrical Concepts: Grasp the fundamentals of electricity, including Ohm's Law, AC/DC currents, and circuit components. Khan Academy offers comprehensive resources.
Learn to Read Schematics and Wiring Diagrams: This skill is crucial for identifying issues and understanding how systems are interconnected. SparkFun provides a good starting point.
Use the Right Tools: Familiarize yourself with multimeters, clamp meters, and insulation resistance testers. Understand their applications through guides like Fluke's resources.
Practice Safety: Always prioritize safety by understanding and applying guidelines from OSHA's Electrical Safety.
Troubleshooting Techniques: Learn systematic approaches to troubleshooting, such as dividing the system, checking for power and ground, and following signal paths. The Balance Careers provides insights into developing troubleshooting techniques.
Attend Workshops and Training: Continuous education through courses and workshops can enhance your skills. Platforms like Coursera and Udemy offer relevant courses.
Hands-on Practice: There's no substitute for experience. Work on real-world problems, start with small projects, and gradually take on more complex tasks.
Join Online Forums and Communities: Engage with platforms like All About Circuits to learn from experienced professionals and enthusiasts.
By following these steps and utilizing the resources provided, you can significantly improve your electrical troubleshooting skills.
How to Display Electrical Troubleshooting Skills on Your Resume
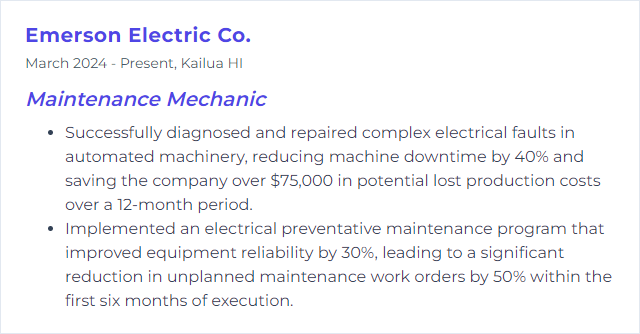
7. Preventive Maintenance
Preventive maintenance is a routine and scheduled maintenance practice aimed at preventing equipment breakdowns and ensuring optimal operational efficiency, involving tasks such as inspections, adjustments, cleaning, lubrication, and parts replacements.
Why It's Important
Preventive maintenance is important for a Maintenance Mechanic as it ensures machinery and equipment operate efficiently, reduces the likelihood of unexpected breakdowns, minimizes downtime, extends the lifespan of assets, and ultimately saves on repair costs and lost production time.
How to Improve Preventive Maintenance Skills
Improving preventive maintenance involves adopting strategies that optimize inspection, servicing, and repair activities to prevent equipment failures. For a Maintenance Mechanic, focusing on the following areas can enhance the effectiveness of preventive maintenance:
Maintenance Planning: Develop a comprehensive maintenance schedule based on manufacturer recommendations and historical data. Utilize maintenance management software to organize and track tasks efficiently.
Condition Monitoring: Implement condition-based monitoring tools to detect early signs of equipment deterioration. Techniques like vibration analysis, thermal imaging, and oil analysis can provide valuable insights (Predictive Maintenance Technologies).
Training and Skills Development: Continuously improve the skills and knowledge of maintenance staff through training sessions and workshops. This ensures they are up-to-date with the latest maintenance techniques and technologies (Maintenance Training).
Utilize Technology: Leverage technology such as Computerized Maintenance Management Systems (CMMS) to automate maintenance tasks, track equipment history, and analyze data for informed decision-making (CMMS Benefits).
Quality Spare Parts: Ensure the use of high-quality spare parts and materials for repairs and replacements to prolong equipment life and reduce the frequency of breakdowns.
Review and Optimize: Regularly review the preventive maintenance program to identify areas of improvement. Analyze maintenance records to adjust the frequency of inspections and services based on actual equipment condition and performance.
For a Maintenance Mechanic, focusing on these strategies can significantly improve the effectiveness of preventive maintenance activities, leading to increased equipment reliability and reduced downtime.
How to Display Preventive Maintenance Skills on Your Resume
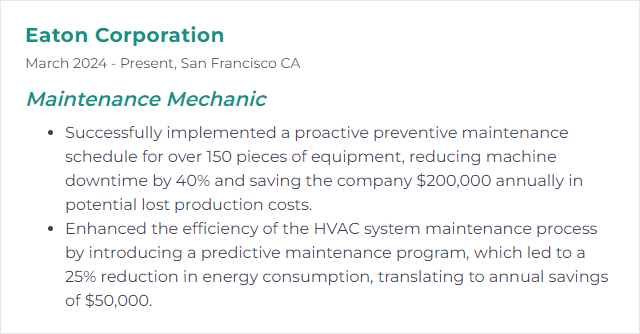
8. CNC Machinery
CNC machinery refers to computer numerical control machines, which are automated machining tools controlled by a computer program. These machines precisely cut, shape, or form materials based on pre-programmed instructions. For a Maintenance Mechanic, it involves ensuring these machines operate efficiently, performing regular maintenance, troubleshooting errors, and repairing any mechanical faults.
Why It's Important
CNC machinery is important because it ensures precision, consistency, and efficiency in manufacturing processes, significantly reducing errors and waste. For a Maintenance Mechanic, it means maintaining these advanced machines is crucial for minimizing downtime and ensuring continuous, high-quality production.
How to Improve CNC Machinery Skills
Improving CNC machinery involves a combination of regular maintenance, software updates, and hardware upgrades. Here’s a concise guide:
Regular Maintenance: Schedule and perform regular maintenance checks to ensure all parts are in good working condition. Focus on cleaning, lubricating, and checking for wear and tear. Machinery Lubrication provides insights on proper lubrication practices.
Software Updates: Keep the CNC operating system and software updated. Manufacturers often release updates that improve performance and add features. Check the CNC Software page for the latest software solutions.
Hardware Upgrades: Upgrade components such as spindle motors, tool holders, and control systems to improve efficiency and precision. Haas Automation offers a range of hardware upgrade options.
Training: Ensure maintenance staff are trained on the latest CNC technologies and troubleshooting techniques. Tooling U-SME offers specialized training courses.
Preventive Measures: Implement a predictive maintenance program using IoT sensors to monitor machine health in real-time, allowing for preemptive repairs. Predictronics specializes in predictive maintenance solutions.
By focusing on these areas, a Maintenance Mechanic can significantly improve the performance and longevity of CNC machinery.
How to Display CNC Machinery Skills on Your Resume
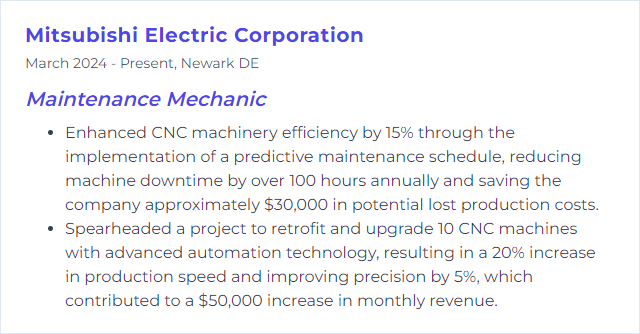
9. Blueprint Reading
Blueprint reading for a Maintenance Mechanic involves interpreting and understanding the technical drawings and diagrams of machinery, equipment, and buildings to perform repairs, maintenance, and installations accurately and efficiently. It includes recognizing symbols, dimensions, and specifications essential for safe and effective maintenance operations.
Why It's Important
Blueprint reading is crucial for a Maintenance Mechanic because it enables accurate understanding and interpretation of machine and system layouts, facilitating effective repair, maintenance, and troubleshooting of equipment.
How to Improve Blueprint Reading Skills
Improving blueprint reading as a Maintenance Mechanic involves developing the ability to understand and interpret various symbols, lines, and notations used in mechanical drawings. Here’s a concise guide to enhance your skills:
Familiarize with Basic Symbols and Notations: Start with learning the standard symbols and notations used in mechanical blueprints. This guide is a good starting point.
Understand Scales and Dimensions: Practice reading and converting scales. Understand how dimensions are represented. Engineering.com has resources and articles that can help.
Practice Orthographic and Isometric Drawings: Learn to visualize 2D drawings in 3D. This tutorial on technical drawing can be beneficial.
Study Assembly Drawings: Assembly drawings show how parts fit together. Practice by disassembling a machine part and sketching it. GrabCAD offers a wide range of CAD models for practice.
Use Online Courses and Tutorials: Platforms like Coursera and Udemy offer courses on blueprint reading and technical drawing.
Hands-On Practice: Apply what you’ve learned by interpreting blueprints in your daily work. Start with simple projects and gradually move to more complex ones.
Seek Feedback: Share your interpretations with experienced mechanics or engineers and ask for feedback.
By consistently practicing and seeking new learning resources, you can significantly improve your blueprint reading skills tailored to maintenance mechanics.
How to Display Blueprint Reading Skills on Your Resume
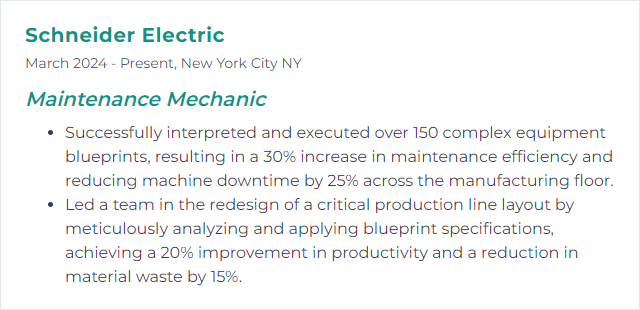
10. Equipment Calibration
Equipment calibration is the process of adjusting and verifying the accuracy and performance of tools and machines against known standards to ensure they operate as intended and produce reliable results. This is crucial for maintenance mechanics to maintain operational efficiency and safety.
Why It's Important
Equipment calibration is crucial for ensuring accuracy, reliability, and safety in machinery operations, thereby minimizing downtime, reducing maintenance costs, and ensuring compliance with industry standards.
How to Improve Equipment Calibration Skills
Improving equipment calibration involves several key steps to ensure accuracy and reliability in measurements. Here's a concise guide tailored for a Maintenance Mechanic:
Regular Schedule: Establish and adhere to a regular calibration schedule based on manufacturer recommendations and usage frequency. Calibration Frequency Guide
Training: Ensure you have proper training on calibration procedures and understand the equipment's operational principles. Calibration Training
Use Certified Standards: Utilize calibration standards that are traceable to national or international standards. NIST Traceability
Documentation: Keep detailed records of all calibrations, adjustments, and maintenance performed. Good Documentation Practices
Correct Environmental Conditions: Perform calibrations under suitable environmental conditions that mimic normal operating conditions. Environmental Conditions Impact
Regular Inspections: Frequently inspect equipment for signs of wear or damage that could impact accuracy. Maintenance Inspections
Professional Calibration Services: For critical or complex equipment, consider using professional calibration services to ensure the highest degree of accuracy. Choosing a Calibration Service
By following these steps, a Maintenance Mechanic can significantly improve the reliability and accuracy of equipment calibration.
How to Display Equipment Calibration Skills on Your Resume
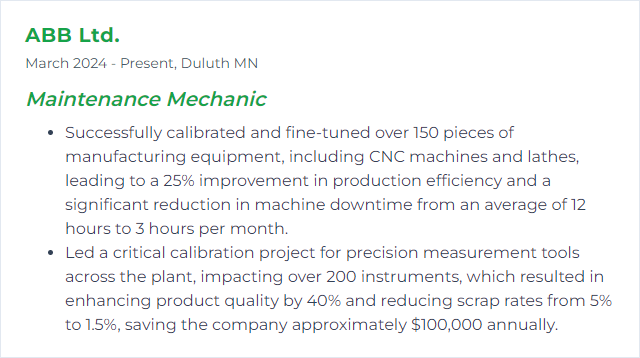
11. Vibration Analysis
Vibration analysis is a technique used in maintenance to detect abnormalities in machinery by analyzing vibration patterns. It helps identify problems like misalignment, imbalance, or wear before they lead to failure, allowing for timely repairs and preventing downtime.
Why It's Important
Vibration analysis is crucial for a Maintenance Mechanic because it helps identify early signs of machine wear and faults, allowing for timely maintenance and preventing costly breakdowns and unplanned downtime.
How to Improve Vibration Analysis Skills
Improving vibration analysis, essential for maintenance mechanics, involves a mix of enhancing skills, using advanced tools, and understanding machine dynamics. Here's a concise guide:
Enhance Your Skills: Increase your understanding of vibration analysis principles. Online courses and tutorials can be very helpful. Consider platforms like Coursera and Udemy for courses on vibration analysis and machinery diagnostics.
Use Advanced Tools: Invest in high-quality vibration analysis equipment. Tools like vibration analyzers and software can significantly improve diagnosis accuracy. Check out options from leading manufacturers like Fluke and SKF.
Understand Machine Dynamics: Get familiar with the specific machinery you're working on. Manufacturer manuals and Machinery's Handbook can provide valuable insights into specific vibration patterns and potential faults.
Data Interpretation: Learn to interpret vibration data accurately. Resources like the Mobius Institute offer valuable insights into data analysis techniques.
Continuous Learning: The field of vibration analysis is always evolving. Join forums and subscribe to journals from organizations like the Vibration Institute to stay updated on the latest trends and technologies.
By focusing on these areas, maintenance mechanics can significantly improve their vibration analysis skills and contribute to better machinery maintenance and reliability.
How to Display Vibration Analysis Skills on Your Resume
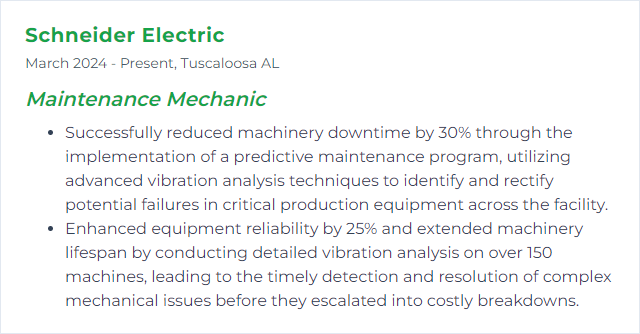
12. Motor Controls
Motor controls refer to the systems and devices used to manage the operation of electric motors, including starting, stopping, speed regulation, and direction control, ensuring efficient and safe machinery operation for maintenance mechanics.
Why It's Important
Motor controls are important for a Maintenance Mechanic because they provide the ability to start, stop, and regulate the speed and torque of motors, ensuring machinery operates efficiently, safely, and reliably, minimizing downtime and extending equipment lifespan.
How to Improve Motor Controls Skills
Improving motor controls for a Maintenance Mechanic involves enhancing efficiency, reliability, and safety. Here are concise strategies:
Regular Maintenance: Perform routine inspections and maintenance to prevent breakdowns and ensure optimal performance. Maintenance Guide
Upgrade to Variable Frequency Drives (VFDs): VFDs allow precise control of motor speed and torque, leading to energy savings and reduced mechanical stress. VFD Benefits
Implement Motor Control Centers (MCCs): Use MCCs for centralized control, simplifying maintenance and enhancing safety. MCC Overview
Use Soft Starters: Soft starters reduce mechanical and electrical stress on motors during startup, extending their lifespan. Soft Starters Explained
Adopt Predictive Maintenance Techniques: Utilize sensors and IoT devices to monitor motor conditions in real-time, predicting failures before they occur. Predictive Maintenance Insights
Training and Education: Regularly update your knowledge on the latest motor control technologies and best practices. Online Training Resource
By focusing on these areas, a Maintenance Mechanic can significantly improve the performance and reliability of motor controls.
How to Display Motor Controls Skills on Your Resume
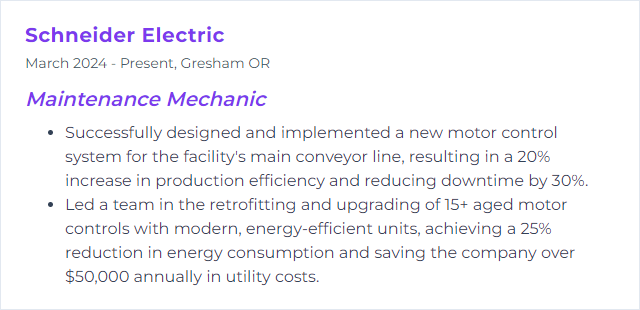