Top 12 Machine Operator Skills to Put on Your Resume
In today's competitive job market, standing out as a machine operator requires more than just basic knowledge of machinery. Highlighting a mix of technical proficiency, safety awareness, and soft skills on your resume can significantly enhance your attractiveness to potential employers, showcasing your comprehensive capability in operating complex machinery efficiently and safely.
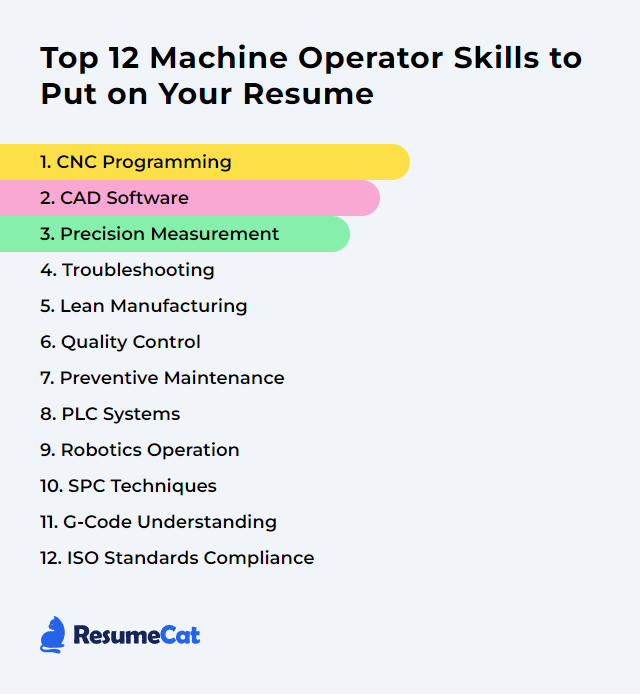
Machine Operator Skills
- CNC Programming
- CAD Software
- Precision Measurement
- Troubleshooting
- Lean Manufacturing
- Quality Control
- Preventive Maintenance
- PLC Systems
- Robotics Operation
- SPC Techniques
- G-Code Understanding
- ISO Standards Compliance
1. CNC Programming
CNC programming involves creating coded instructions that CNC machines follow to perform tasks like cutting, drilling, or shaping materials. For a machine operator, it means inputting and managing these codes to ensure the machine executes the desired operations accurately and efficiently.
Why It's Important
CNC programming is essential for a Machine Operator as it enables precise control over machinery to produce complex parts accurately, efficiently, and safely, optimizing production quality and speed.
How to Improve CNC Programming Skills
Improving CNC programming involves enhancing efficiency, accuracy, and the quality of the machining process. Here are concise tips for machine operators seeking to improve their CNC programming skills:
Understand the Basics: Solidify your understanding of CNC fundamentals, including machine operation, G-code, and M-code. CNC Cookbook offers tutorials and guides.
Master CAD/CAM Software: Familiarize yourself with CAD/CAM software to streamline the design to production process. Tutorials on Fusion 360 can be particularly helpful.
Optimize Toolpaths: Learn about different toolpath strategies to increase efficiency and surface finish. Mastercam's Blog provides insights and tips.
Simulate and Validate Programs: Use simulation software to test and validate your programs, reducing errors and machine crashes. Check out CAMplete for advanced simulation options.
Stay Updated with Technology: Continuously learn about new technologies and machining techniques. Websites like Modern Machine Shop offer news and articles on the latest trends.
Practice Lean Manufacturing: Adopt lean manufacturing principles to minimize waste and improve workflow efficiency. The Lean Enterprise Institute has resources and case studies.
Join Forums and Communities: Engage with other CNC professionals in forums and communities to exchange knowledge and solve problems. Practical Machinist is a great platform to start with.
By focusing on continuous learning and leveraging available resources, machine operators can significantly improve their CNC programming skills and contribute to more efficient, accurate, and productive machining processes.
How to Display CNC Programming Skills on Your Resume
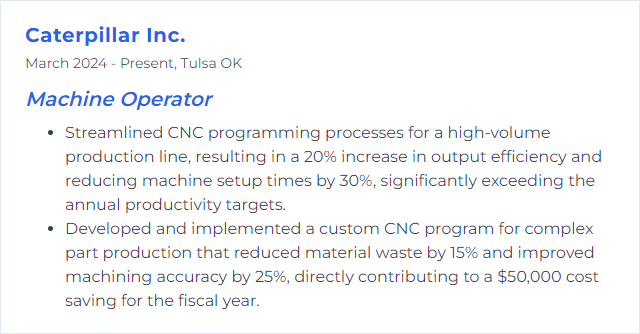
2. CAD Software
CAD software, or Computer-Aided Design software, is a tool used to create, modify, and optimize designs and technical drawings for parts and assemblies in manufacturing processes.
Why It's Important
CAD software is crucial for a Machine Operator as it enables precise design and modeling of parts or products, ensuring accurate and efficient manufacturing processes.
How to Improve CAD Software Skills
Improving CAD software, particularly for machine operators, involves enhancing user experience, compatibility, and functionality. Here are concise tips:
User-Friendly Interface: Simplify the user interface for intuitive navigation and operation. Incorporate customizable toolbars and shortcuts for common tasks. Autodesk often updates its software with these considerations.
Better Compatibility and Integration: Ensure the software can seamlessly integrate with a wide range of machines and CAM (Computer-Aided Manufacturing) systems. Compatibility with popular formats like STEP, IGES, and DXF is crucial. SolidWorks offers good examples of integration capabilities.
Enhanced Simulation Capabilities: Implement advanced simulation features that allow operators to test and modify designs under real-world conditions before sending them to production. ANSYS provides comprehensive simulation tools.
Real-Time Collaboration Tools: Facilitate easier collaboration among team members with cloud-based sharing and real-time feedback mechanisms. Onshape is a leader in cloud-based CAD, enabling real-time collaboration.
Comprehensive Training Resources: Provide access to tutorials, guides, and customer support to help machine operators maximize the software’s capabilities. Mastercam offers extensive training materials for users.
Regular Updates and Feedback Loops: Regularly update the software to address bugs, add new features, and improve user experience. Maintain open channels for user feedback to guide these updates. Fusion 360 employs a continuous update approach guided by user feedback.
Improving CAD software in these areas can significantly enhance productivity and efficiency for machine operators.
How to Display CAD Software Skills on Your Resume
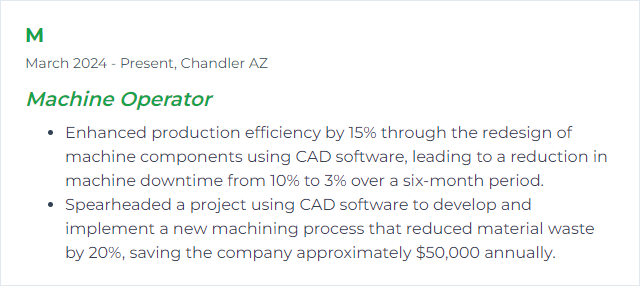
3. Precision Measurement
Precision measurement in the context of a Machine Operator refers to the use of tools and techniques to obtain highly accurate and consistent measurements of materials or components, ensuring they meet specified dimensions and tolerances for quality and performance.
Why It's Important
Precision measurement is crucial for a machine operator because it ensures the accuracy and quality of the manufactured parts, minimizes waste and rework, and helps maintain consistency in production, leading to increased efficiency and customer satisfaction.
How to Improve Precision Measurement Skills
To improve precision measurement as a Machine Operator, follow these concise steps:
Calibrate Equipment Regularly: Ensure all measuring tools and machines are calibrated according to the manufacturer's recommendations. NIST Guidelines provide a standard reference.
Use Appropriate Tools: Select the right measurement tools (micrometers, calipers, gauges) for the specific task. Mitutoyo offers a wide range of precision instruments.
Maintain Environmental Conditions: Control temperature, humidity, and vibration levels in the measurement area. Fluke provides insights into managing these factors.
Train and Educate: Continuously train on measurement techniques and tool handling. Tooling U-SME offers courses tailored for machine operators.
Implement Quality Control Procedures: Use statistical process control (SPC) to monitor and control measurement quality. ASQ’s resources can guide on SPC implementation.
Regular Maintenance: Perform preventive maintenance on machines to avoid inaccuracies due to wear and tear. Machinery Lubrication offers tips on maintenance practices.
Following these steps diligently will significantly improve precision measurement in machining operations.
How to Display Precision Measurement Skills on Your Resume
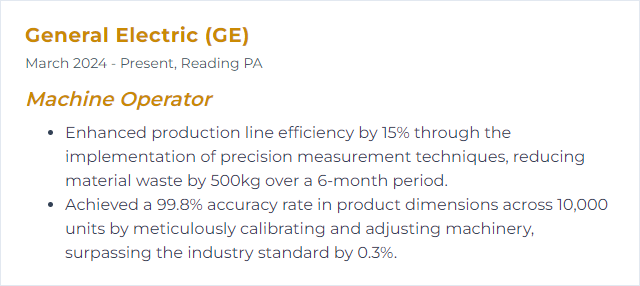
4. Troubleshooting
Troubleshooting, for a Machine Operator, involves identifying, diagnosing, and resolving issues or malfunctions within machinery or equipment to ensure optimal performance and minimal downtime.
Why It's Important
Troubleshooting is essential for a Machine Operator as it enables quick identification and resolution of problems, ensuring minimal downtime and maintaining optimal machine performance and productivity.
How to Improve Troubleshooting Skills
Improving troubleshooting skills as a Machine Operator involves a few key steps focused on understanding the machinery, developing a systematic approach, and continuously learning. Here's a concise guide:
Understand Your Machinery: Familiarize yourself with the machine manuals and specifications. Machine Manufacturers’ Websites often have detailed guides.
Learn from Experience: Document and review past troubleshooting scenarios. Websites like Reliable Plant offer case studies and real-life examples.
Develop a Systematic Approach: Adopt a methodical process for diagnosing issues, such as the 5-Why Technique.
Use the Right Tools: Ensure you have and know how to use the necessary diagnostic tools. Online forums like Practical Machinist can offer advice on tool selection and use.
Continuous Learning: Stay updated with new technologies and troubleshooting methods through online courses and resources. Coursera and LinkedIn Learning have relevant courses.
Safety First: Always prioritize safety by understanding and following proper procedures. OSHA’s Training resources can be invaluable.
By focusing on these areas, you can enhance your troubleshooting skills effectively.
How to Display Troubleshooting Skills on Your Resume
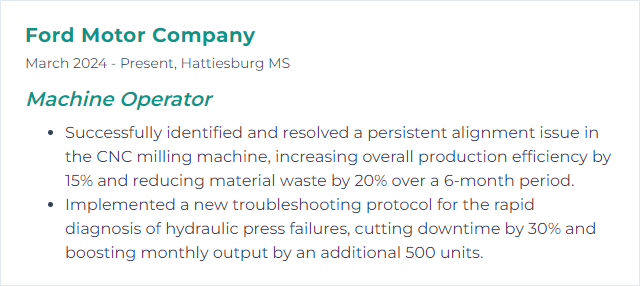
5. Lean Manufacturing
Lean Manufacturing is a production approach focused on minimizing waste and maximizing efficiency, aiming to enhance product quality and production speed while reducing costs. For a Machine Operator, it means consistently working to improve processes, reduce unnecessary movements or materials, and ensure machines are optimally utilized for the most efficient production.
Why It's Important
Lean Manufacturing is important because it aims to reduce waste and improve efficiency in production processes, directly impacting a Machine Operator by streamlining their work, minimizing errors, and increasing productivity, leading to a safer and more rewarding work environment.
How to Improve Lean Manufacturing Skills
Improving Lean Manufacturing, particularly from a Machine Operator's perspective, involves focusing on waste reduction, continuous improvement, and optimizing processes. Here are concise strategies:
Embrace Kaizen: Actively engage in Kaizen, or continuous improvement, by regularly assessing and enhancing your work processes and efficiency.
Implement 5S: Follow the 5S methodology (Sort, Set in order, Shine, Standardize, Sustain) to organize your workspace for maximum efficiency and reduced waste.
Practice JIT: Adopt Just-In-Time (JIT) manufacturing to minimize inventory costs and reduce waste by receiving goods only as they are needed in the production process.
Use Standard Work: Apply Standard Work principles to establish efficient, repeatable processes that ensure quality and reduce variability.
Engage in Problem-Solving: Participate in problem-solving teams to identify root causes of waste and inefficiencies using tools like PDCA (Plan-Do-Check-Act) and A3 Problem Solving.
Utilize Visual Management: Implement Visual Management techniques to make the state and flow of work apparent, facilitating quicker decision-making and adjustments.
By actively engaging in these practices, machine operators can significantly contribute to the improvement of Lean Manufacturing processes within their organizations.
How to Display Lean Manufacturing Skills on Your Resume
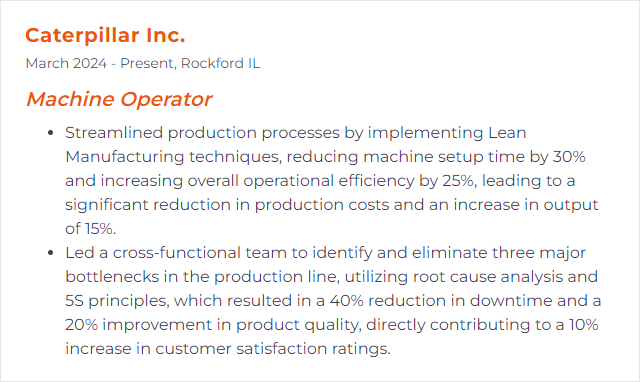
6. Quality Control
Quality Control (QC) for a Machine Operator involves monitoring and adjusting machinery to ensure that the manufactured products meet specified standards of quality and safety before they are distributed or sold.
Why It's Important
Quality Control is crucial for a Machine Operator as it ensures the production of defect-free products, maintains high customer satisfaction, and reduces waste and rework costs, ultimately contributing to the efficiency and profitability of the manufacturing process.
How to Improve Quality Control Skills
Improving Quality Control for a Machine Operator involves several key steps focused on precision, consistency, and continuous improvement. Here's a concise guide:
Understand Specifications: Ensure you're thoroughly familiar with the product specifications and quality standards. ASQ's quality resources can be a starting point.
Regular Maintenance: Keep machinery in optimal condition through regular maintenance checks. The U.S. Department of Labor's maintenance tips may help.
Use of Technology: Incorporate technology like sensors and automation for real-time quality monitoring. NIST's advanced manufacturing site has further insights.
Continuous Training: Engage in continuous learning and training on quality control best practices and equipment handling. MIT's free online courses offer a range of relevant subjects.
Feedback Loop: Establish a feedback loop for identifying and correcting defects promptly. Lean on resources like ISO's quality management standards for structured approaches.
By focusing on these areas, a Machine Operator can significantly contribute to improving Quality Control in their operations.
How to Display Quality Control Skills on Your Resume
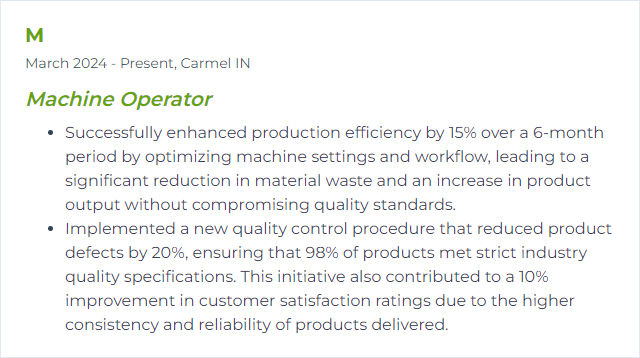
7. Preventive Maintenance
Preventive maintenance is a routine maintenance process carried out on machinery to prevent unexpected breakdowns and ensure optimal performance.
Why It's Important
Preventive maintenance is crucial for a machine operator because it ensures machines operate efficiently, minimizes unexpected breakdowns, reduces costly repairs, and extends the lifespan of the equipment.
How to Improve Preventive Maintenance Skills
To improve Preventive Maintenance as a Machine Operator, focus on the following short and concise strategies:
Schedule Regular Inspections: Consistently inspect and monitor equipment performance. Use a preventive maintenance schedule that aligns with the manufacturer's recommendations.
Implement a CMMS: Use a Computerized Maintenance Management System (CMMS) to streamline maintenance tasks, track performance, and predict failures. Fiix offers solutions tailored to various needs.
Train Operators: Ensure all operators are trained on the basics of machine maintenance and the importance of reporting issues. Tooling U-SME provides online courses focused on maintenance practices.
Standardize Maintenance Procedures: Develop and adhere to standard operating procedures (SOPs) for maintenance. This guide from Reliable Plant can help in creating effective SOPs.
Utilize Predictive Maintenance Technologies: Incorporate technologies like vibration analysis, thermography, and ultrasonic detection to predict equipment failures before they occur. The PdM Guide by Fluke details various predictive maintenance technologies.
Maintain a Clean Work Environment: Keep the machine and its surroundings clean to prevent the build-up of contaminants that can cause wear and tear. Cleanliness guidelines from Machinery Lubrication offer practical tips.
Regularly Review and Adjust the Maintenance Plan: As machines age or production conditions change, adjust your maintenance plan accordingly. Continuous improvement practices are outlined in this article by Plant Services.
By adopting these strategies, machine operators can significantly contribute to the overall efficiency and longevity of the equipment they manage.
How to Display Preventive Maintenance Skills on Your Resume
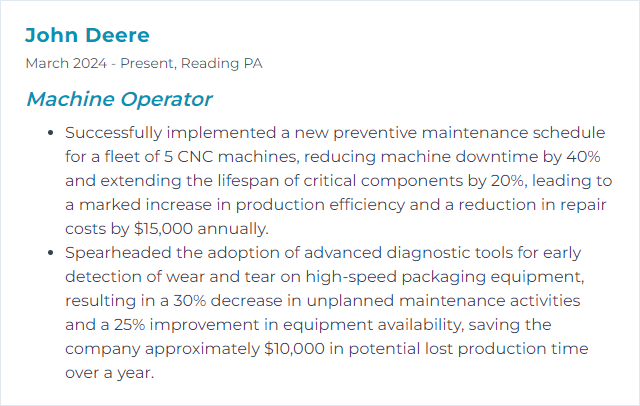
8. PLC Systems
A PLC (Programmable Logic Controller) system is a digital computer used in industrial settings, like manufacturing lines, to automate machinery operations. It controls the machinery based on programmed instructions, ensuring precise and efficient operation. For a Machine Operator, it's a critical tool for managing and monitoring the performance of machines under their control.
Why It's Important
PLC (Programmable Logic Controller) systems are crucial for Machine Operators because they automate machine processes, ensuring precise, consistent, and safe operations, significantly enhancing productivity and minimizing human error.
How to Improve PLC Systems Skills
To enhance PLC (Programmable Logic Controller) systems in the context of machine operation, focus on the following areas:
Training: Equip operators with comprehensive PLC training to understand system capabilities and troubleshooting techniques.
Regular Maintenance: Implement a routine maintenance schedule to prevent unexpected downtimes and ensure system reliability.
Software Updates: Keep the PLC software up-to-date with the latest versions for enhanced performance and security features.
Network Security: Enhance network security to protect against unauthorized access and potential cyber threats.
System Integration: Integrate PLC systems with IoT (Internet of Things) technology for real-time monitoring and data analysis, leading to improved decision-making and efficiency.
By focusing on these key areas, machine operators can significantly improve the performance and reliability of PLC systems.
How to Display PLC Systems Skills on Your Resume
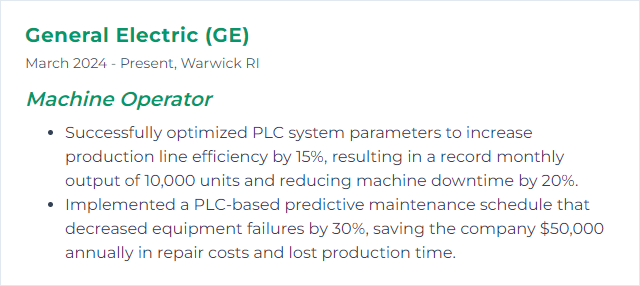
9. Robotics Operation
Robotics operation involves the setup, monitoring, and control of automated machines or robot systems by a machine operator to perform tasks efficiently and accurately, often in manufacturing or production environments.
Why It's Important
Robotics operation is crucial for a Machine Operator as it enhances efficiency, precision, and safety in manufacturing processes, while also reducing human error and physical strain.
How to Improve Robotics Operation Skills
Improving robotics operation for a Machine Operator involves enhancing efficiency, safety, and productivity through the following steps:
Continuous Training: Invest in ongoing training programs to keep operators updated on the latest technology and safety protocols.
Regular Maintenance: Implement a preventive maintenance schedule to avoid unexpected downtime and extend the life of robotic systems.
Optimization of Workflows: Analyze and optimize workflows to ensure robots are used efficiently, reducing bottlenecks and improving throughput.
Safety Measures: Enhance safety by adhering to industry standards and using safety barriers and sensors, minimizing the risk of accidents.
Software Updates: Regularly update the robotic system’s software to leverage new features and improvements, enhancing performance and capabilities.
Collaborative Robots (Cobots): Explore the use of cobots that are designed to work alongside human operators, improving flexibility and efficiency.
By focusing on these key areas, Machine Operators can significantly improve the operation of robotics systems in their workflow.
How to Display Robotics Operation Skills on Your Resume
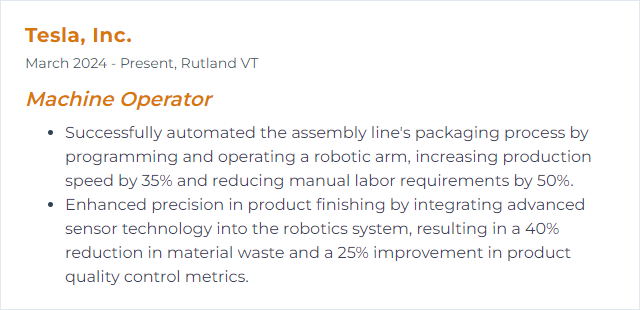
10. SPC Techniques
SPC (Statistical Process Control) Techniques are methods used by machine operators to monitor and control a manufacturing process to ensure it operates at its maximum potential. By collecting and analyzing data on variables that affect the process, operators can identify trends, make adjustments, and maintain product quality within desired specifications, minimizing variability and defects.
Why It's Important
SPC (Statistical Process Control) techniques are important for a Machine Operator as they enable real-time monitoring and control of manufacturing processes to ensure consistent quality, reduce waste, and improve efficiency by identifying and addressing variations before they become defects.
How to Improve SPC Techniques Skills
To improve Statistical Process Control (SPC) techniques as a Machine Operator, consider the following:
- Understand SPC Fundamentals: Master the basics of SPC, including control charts, process capability, and variation. ASQ's SPC guide is a great place to start.
- Regular Training: Engage in ongoing training sessions to stay updated with the latest SPC tools and techniques. Online courses from platforms like Coursera can be beneficial.
- Use Appropriate Tools: Employ SPC software specifically designed for manufacturing environments. Minitab offers comprehensive SPC analysis tools.
- Maintain Equipment: Ensure machines are regularly calibrated and maintained to reduce variability in the manufacturing process. NIST's guidelines on calibration can provide valuable insights.
- Collaborate with Quality Control: Work closely with the quality control department to understand SPC data and implement corrective actions promptly.
By comprehensively understanding SPC, staying educated on new methods, utilizing the right tools, maintaining equipment, and collaborating effectively, machine operators can significantly enhance SPC techniques in their operations.
How to Display SPC Techniques Skills on Your Resume
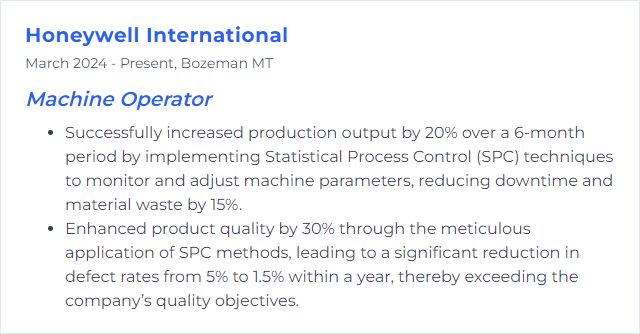
11. G-Code Understanding
G-Code is a programming language used to instruct and control automated machine operations, such as CNC machining, guiding the machine on how to move, shape, or cut materials according to specified dimensions and paths.
Why It's Important
Understanding G-code is crucial for a machine operator as it enables precise control over CNC machines, ensuring accurate production, troubleshooting errors, and optimizing machining processes for efficiency and quality.
How to Improve G-Code Understanding Skills
To improve your understanding of G-Code as a machine operator, focus on these concise steps:
Start with Basics: Grasp the fundamental concepts and commands of G-Code. TITANS of CNC Academy offers free resources that are well-structured for beginners.
Practice Regularly: Hands-on experience is key. Use simulation software like NC Viewer to practice and visualize G-Code without the risk of damaging machinery.
Learn from Examples: Analyze and break down existing G-Code files. GitHub is a great place to find community-shared G-Code projects.
Use Reference Guides: Keep a G-Code reference guide handy for quick help on specific commands and syntax.
Join Forums: Engage with communities such as Reddit’s r/CNC or CNCZone to ask questions, share experiences, and get advice from experienced operators.
Take Online Courses: Websites like Coursera and Udemy offer courses on CNC programming that can deepen your understanding of G-Code.
By following these steps and utilizing these resources, you can significantly improve your G-Code skills.
How to Display G-Code Understanding Skills on Your Resume
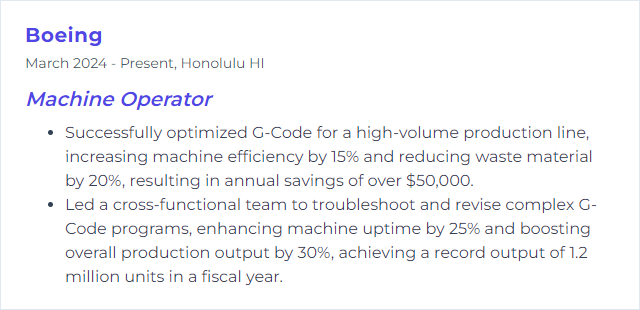
12. ISO Standards Compliance
ISO Standards Compliance for a Machine Operator involves adhering to internationally recognized guidelines and procedures to ensure safety, quality, and efficiency in operating machinery. This includes following specific operational protocols, maintenance routines, and safety measures outlined in relevant ISO standards to maintain consistent performance and minimize risks.
Why It's Important
ISO Standards Compliance ensures a machine operator works with machines that are safe, reliable, and meet international quality standards, enhancing productivity, reducing accidents, and ensuring consistent product quality.
How to Improve ISO Standards Compliance Skills
Improving ISO Standards Compliance for a Machine Operator involves several key steps. Ensure adherence to these guidelines for enhanced compliance:
Understand ISO Requirements: Familiarize yourself with the specific ISO standards relevant to your machinery and operations. ISO's official website is a comprehensive resource.
Training and Awareness: Undergo regular training sessions to stay updated on the best practices and operational procedures as per ISO standards. ASQ offers various training opportunities.
Maintenance and Calibration: Regularly maintain and calibrate machinery to ensure it operates within the required ISO standards. NIST provides guidelines on calibration standards.
Document Management: Keep accurate records of operations, maintenance, and training as evidence of compliance. ISO offers standards for document management systems.
Continuous Improvement: Adopt a culture of continuous improvement through regular audits and reviews. Utilize the Plan-Do-Check-Act (PDCA) cycle for ongoing compliance enhancement.
Engage with Quality Management Systems (QMS): Implement and actively participate in a QMS that complies with ISO standards, like ISO 9001. ISO 9001 details quality management system requirements.
By following these steps and leveraging the resources provided, a Machine Operator can significantly improve their compliance with ISO standards.
How to Display ISO Standards Compliance Skills on Your Resume
