Top 12 Logistics Supervisor Skills to Put on Your Resume
In today's fast-paced and dynamic supply chain environment, having a resume that stands out is crucial for logistics supervisors. Highlighting a mix of technical expertise and soft skills relevant to the role can significantly enhance your chances of securing your next opportunity in the logistics sector.
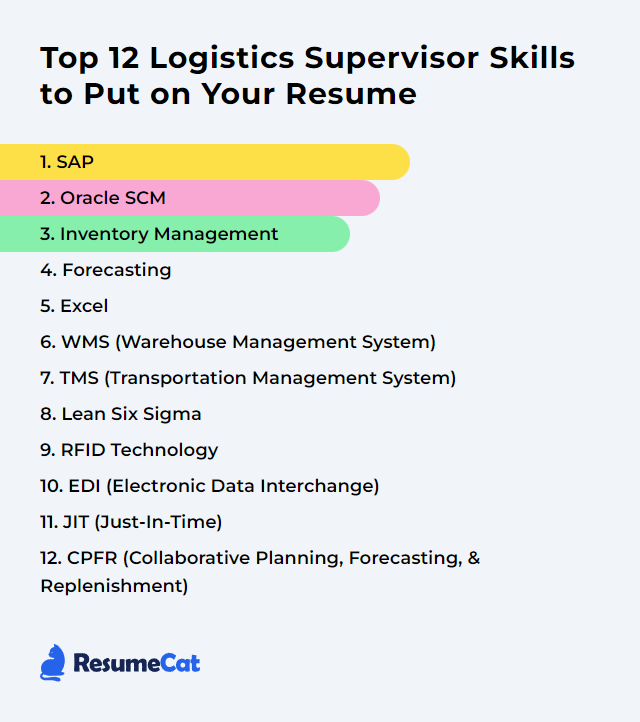
Logistics Supervisor Skills
- SAP
- Oracle SCM
- Inventory Management
- Forecasting
- Excel
- WMS (Warehouse Management System)
- TMS (Transportation Management System)
- Lean Six Sigma
- RFID Technology
- EDI (Electronic Data Interchange)
- JIT (Just-In-Time)
- CPFR (Collaborative Planning, Forecasting, and Replenishment)
1. SAP
SAP is a comprehensive enterprise resource planning (ERP) software that integrates all aspects of business operations, including logistics, to streamline processes, manage inventory, and facilitate efficient supply chain management.
Why It's Important
SAP is important for a Logistics Supervisor because it provides integrated and real-time tools to manage supply chain processes, inventory, and distribution efficiently, ensuring timely delivery and optimal resource utilization.
How to Improve SAP Skills
Improving your SAP experience as a Logistics Supervisor involves focusing on optimization, training, and integration. Here's a concise guide:
Optimization: Streamline processes by customizing SAP to fit your logistics operations. Utilize SAP's Advanced Planning and Optimization (APO) module for better forecasting and planning.
Training: Enhance your team's SAP skills through targeted SAP training courses. Focus on logistics-specific modules like Materials Management (MM) and Sales and Distribution (SD).
Integration: Ensure seamless data flow by integrating SAP with other systems (e.g., CRM, SCM) using SAP Integration Suite. This enhances visibility and decision-making.
Automation: Leverage SAP Intelligent Robotic Process Automation to automate repetitive tasks, reducing errors and freeing up time for strategic work.
Data Analysis: Utilize SAP BusinessObjects for advanced analytics. Making data-driven decisions improves efficiency and service levels.
Focusing on these areas will lead to significant improvements in your logistics operations within SAP.
How to Display SAP Skills on Your Resume

2. Oracle SCM
Oracle SCM (Supply Chain Management) is a comprehensive suite of cloud-based applications designed to manage and optimize supply chain operations, including procurement, product lifecycle, order fulfillment, and logistics, providing real-time visibility and insights for efficient decision-making and improved coordination across the supply chain. For a Logistics Supervisor, it facilitates efficient management of logistics processes, inventory, and transportation, ensuring timely delivery and cost reduction.
Why It's Important
Oracle SCM (Supply Chain Management) is important for a Logistics Supervisor because it streamlines and optimizes the end-to-end logistics process, from inventory management to order fulfillment, ensuring efficient operations, cost reduction, and enhanced customer satisfaction.
How to Improve Oracle SCM Skills
Improving Oracle SCM (Supply Chain Management) for a Logistics Supervisor involves several key strategies aimed at enhancing efficiency, visibility, and collaboration across the supply chain. Below are concise steps to achieve this:
Leverage Analytics: Utilize Oracle SCM Cloud's advanced analytics to gain insights into supply chain performance, identifying areas for improvement. Oracle Analytics can help in making informed decisions quickly.
Integration: Ensure seamless integration of Oracle SCM with other systems (ERP, CRM, etc.) for real-time data exchange and visibility. The Oracle Integration service simplifies this process.
Training and Support: Invest in ongoing training for staff to fully leverage Oracle SCM capabilities. Oracle provides a comprehensive learning platform, Oracle University, which offers courses specifically for SCM solutions.
Automation: Automate routine tasks within the supply chain to increase efficiency and reduce errors. Oracle SCM Cloud's automation capabilities can significantly streamline operations.
Collaboration Tools: Utilize collaboration tools within Oracle SCM for better coordination with suppliers, partners, and customers. This enhances transparency and speeds up decision-making processes.
Customization and Flexibility: Tailor Oracle SCM to fit specific business needs, ensuring flexibility to adapt to market changes. Oracle SCM Cloud's configuration options are designed to accommodate unique requirements.
Performance Monitoring: Regularly monitor and review supply chain performance against KPIs. Adjust strategies as needed to continually optimize operations.
By focusing on these areas, a Logistics Supervisor can significantly improve the efficiency and responsiveness of their supply chain operations using Oracle SCM.
How to Display Oracle SCM Skills on Your Resume
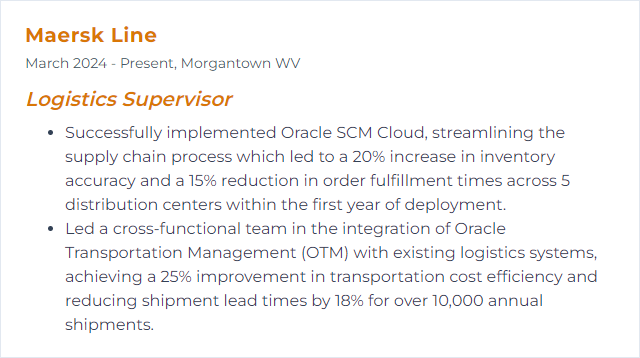
3. Inventory Management
Inventory management is the process of ordering, storing, using, and selling a company's inventory. For a Logistics Supervisor, it involves overseeing the balance of stock levels, managing the flow of goods, and ensuring the right products are available at the right time to meet demand without overstocking or stockouts.
Why It's Important
Inventory management is crucial for a Logistics Supervisor as it ensures the optimal balance of stock availability and the minimization of costs, avoiding both overstocking and stockouts. This balance is essential for meeting customer demands efficiently, maintaining cash flow, and enhancing overall operational effectiveness.
How to Improve Inventory Management Skills
Improving inventory management involves optimizing stock levels, enhancing order accuracy, and streamlining processes to reduce costs and improve customer satisfaction. Here are concise strategies for a Logistics Supervisor:
Implement an Inventory Management System: Use technology to track inventory in real-time. Shopify's guide offers insights into choosing the right system.
Adopt Just-In-Time (JIT) Inventory: Reduce inventory costs by keeping stock levels low and ordering goods only as needed. The Lean Enterprise Institute explains JIT principles in detail.
Regular Audits: Schedule regular physical counts to verify inventory accuracy. Square outlines steps for conducting an inventory audit.
Improve Forecasting: Use historical sales data to better predict future demand. IBM discusses advanced forecasting methods.
Supplier Relationship Management: Work closely with suppliers to ensure timely deliveries and quality products. SCMDOJO offers best practices for managing supplier relationships.
Optimize Warehouse Layout: Design the warehouse to streamline operations and reduce handling time. Camcode provides tips on improving warehouse efficiency.
Train Staff: Ensure all team members are trained on inventory management best practices. APICS offers certification and training in supply chain and inventory management.
By leveraging technology, optimizing processes, and focusing on continuous improvement, a Logistics Supervisor can significantly enhance inventory management.
How to Display Inventory Management Skills on Your Resume
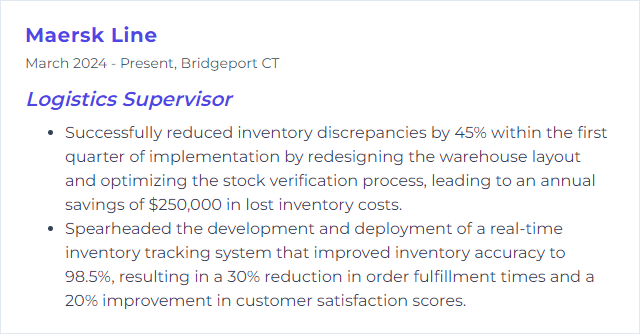
4. Forecasting
Forecasting, in the context of a Logistics Supervisor, involves predicting future demand, inventory levels, and supply chain requirements to ensure efficient, cost-effective operations and timely delivery of goods.
Why It's Important
Forecasting is crucial for a Logistics Supervisor as it enables effective planning of inventory, manpower, and transportation, ensuring timely delivery of goods while optimizing costs and resources.
How to Improve Forecasting Skills
Improving forecasting, especially for a Logistics Supervisor, involves integrating accurate data analysis, technology, and continuous improvement strategies. Here are concise ways to enhance forecasting:
Leverage Historical Data: Use past performance and trend analysis to predict future demands accurately. Tools like Excel or more sophisticated ERP systems can help organize and analyze historical data.
Implement Technology Solutions: Adopt specialized forecasting software like Demand Planning software to utilize advanced algorithms and artificial intelligence for more accurate predictions.
Collaborate and Communicate: Enhance coordination with sales, marketing, and production teams to understand demand drivers. Platforms like Slack can facilitate better communication.
Continuous Training: Stay updated with forecasting methodologies and tools. Online courses on platforms like Coursera or Udemy can be valuable.
Monitor External Factors: Keep an eye on industry trends, economic factors, and seasonality. Resources like Bloomberg offer insights and data for informed predictions.
Regular Reviews and Adjustments: Establish a routine for reviewing forecasts versus actual outcomes to refine your methods continuously. Tools like Tableau can help visualize and analyze these comparisons for better adjustments.
By focusing on these aspects, a Logistics Supervisor can significantly improve forecasting accuracy, leading to more efficient operations and reduced costs.
How to Display Forecasting Skills on Your Resume
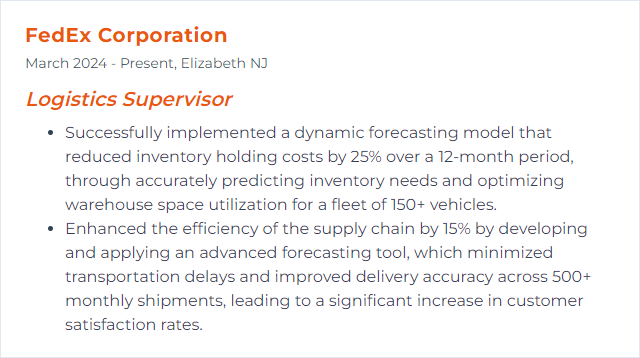
5. Excel
Excel is a spreadsheet program used for organizing, analyzing, and managing data, crucial for tracking inventory, scheduling shipments, and analyzing supply chain efficiency for a Logistics Supervisor.
Why It's Important
Excel is crucial for a Logistics Supervisor as it enables efficient data management, facilitates complex calculations for inventory tracking, scheduling, and forecasting, and allows for the creation of detailed reports and analysis to optimize logistics operations.
How to Improve Excel Skills
Improving Excel skills, particularly for a Logistics Supervisor role, involves focusing on data management, analysis, and visualization techniques to enhance decision-making and operational efficiency. Here's a very short and concise guide to get started:
Master Excel Basics: Ensure you're comfortable with basic functions, formulas, and shortcuts. GCFGlobal offers comprehensive tutorials.
Learn Advanced Formulas: Focus on formulas critical for logistics such as
VLOOKUP
,INDEX MATCH
, andSUMIFS
. Exceljet provides clear examples.Utilize PivotTables: PivotTables are essential for summarizing, analyzing, and presenting large datasets. Microsoft Support has official guides.
Understand Data Visualization: Develop skills in creating charts and graphs to represent logistics data visually. Chandoo offers excellent tutorials for making better charts.
Automate Repetitive Tasks with Macros: Learn to record and write simple VBA codes to automate your regular Excel tasks. Excel Easy introduces VBA in an accessible manner.
Explore Power Query and Power Pivot: These Excel add-ins are powerful tools for data analysis and business intelligence. Microsoft Excel Tech Community is a good resource for learning these tools.
Keep Learning and Practicing: Excel is vast, and continuous learning is crucial for staying proficient and discovering new features or techniques.
By focusing on these areas, a Logistics Supervisor can significantly enhance their Excel skills, leading to improved efficiency, accuracy, and decision-making in their role.
How to Display Excel Skills on Your Resume
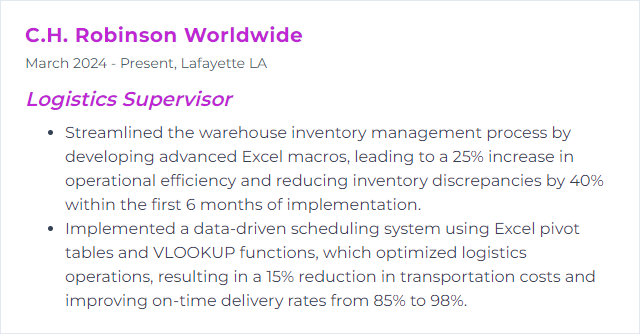
6. WMS (Warehouse Management System)
A Warehouse Management System (WMS) is a software solution that optimizes and controls warehouse operations, from inventory management to order fulfillment, aiming to enhance efficiency, accuracy, and productivity within a warehouse environment.
Why It's Important
A Warehouse Management System (WMS) is crucial for a Logistics Supervisor as it optimizes warehouse operations, ensuring efficient inventory management, accurate order fulfillment, and timely deliveries, ultimately improving customer satisfaction and reducing operational costs.
How to Improve WMS (Warehouse Management System) Skills
Improving a Warehouse Management System (WMS) involves several key steps focused on optimizing efficiency, accuracy, and productivity in warehouse operations. Here's a concise guide for a Logistics Supervisor:
Evaluate Current System Performance: Start by assessing the existing WMS for any shortcomings or inefficiencies. Tools like WMS scorecards can help benchmark performance.
Integrate Technologies: Incorporate advanced technologies like RFID, IoT, and automation to enhance data accuracy and operational efficiency.
Optimize Inventory Management: Implement inventory optimization tools within your WMS to reduce carrying costs and improve order fulfillment rates.
Enhance User Training: Ensure all users are fully trained on WMS features and updates. Regular training sessions can significantly improve system utilization.
Regularly Update Software: Keep your WMS up-to-date with the latest software versions to leverage new features and security patches. Consult your vendor's support and updates page for guidance.
Implement Analytics and Reporting: Use the WMS's analytics and reporting tools to gain insights into operations and identify areas for improvement.
Seek User Feedback: Regularly collect feedback from system users to identify pain points and areas for enhancement. User feedback is crucial for continual improvement.
Collaborate with Vendors for Customization: Work closely with your WMS vendor to customize the system according to your specific warehouse operations. Custom features can significantly boost productivity.
By following these steps and focusing on continuous improvement, a Logistics Supervisor can significantly enhance the efficiency and efficacy of their Warehouse Management System.
How to Display WMS (Warehouse Management System) Skills on Your Resume
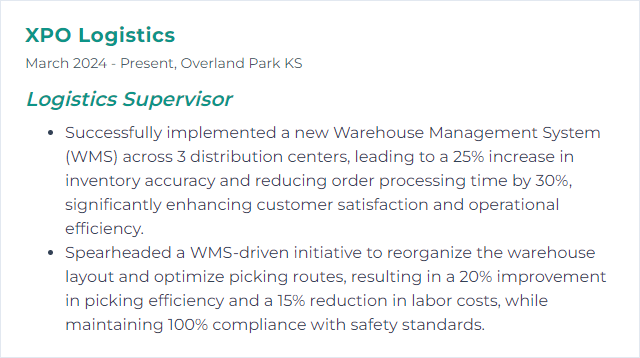
7. TMS (Transportation Management System)
A Transportation Management System (TMS) is a logistics platform that allows users to manage and optimize the daily operations of their transportation fleets. It provides tools for route planning, freight audit and payment, carrier management, load optimization, and tracking of shipments, enhancing efficiency and reducing costs in the supply chain.
Why It's Important
A Transportation Management System (TMS) is crucial for a Logistics Supervisor as it streamlines operations by optimizing route planning and freight consolidation, reducing costs, improving shipment efficiency, and enhancing customer satisfaction through better delivery performance.
How to Improve TMS (Transportation Management System) Skills
Improving a Transportation Management System (TMS) as a Logistics Supervisor involves several key strategies focused on enhancing efficiency, reducing costs, and improving service levels. Here are concise steps with relevant resources:
Integration and Automation: Streamline operations by integrating your TMS with other systems such as ERP, WMS, and carrier systems for real-time data exchange. Automation of repetitive tasks reduces errors and saves time. Guide to TMS Integration.
Data Analytics and Reporting: Leverage the TMS’s analytics tools to monitor performance metrics, identify trends, and make data-driven decisions. This helps in optimizing routes, carrier performance, and cost savings. Benefits of TMS Analytics.
Carrier Relationship Management: Evaluate and negotiate with carriers regularly to ensure competitive rates and service quality. An updated carrier database within your TMS aids in selecting the best options for each shipment. Carrier Management Best Practices.
Continuous Training and Development: Ensure your team is well-versed in the TMS features and updates through regular training sessions. This enhances system utilization and efficiency. Importance of TMS Training.
Advanced Features Utilization: Explore and utilize advanced TMS features like AI and machine learning for predictive analytics, IoT for real-time tracking, and blockchain for security and transparency. Emerging TMS Technologies.
Feedback and Adaptation: Collect feedback from users and stakeholders to identify areas for improvement. Be adaptable to changing logistics trends and technologies to keep your TMS relevant and efficient. Implementing Feedback in TMS.
Sustainability Focus: Opt for eco-friendly routes and carriers within your TMS to contribute to sustainability goals. This can also lead to cost savings and improved brand image. Sustainable Logistics Practices.
Implementing these steps requires a strategic approach and continuous improvement mindset. By focusing on integration, data-driven decision-making, carrier management, staff training, utilization of advanced features, adapting based on feedback, and sustainability, a Logistics Supervisor can significantly enhance the performance and value of their TMS.
How to Display TMS (Transportation Management System) Skills on Your Resume
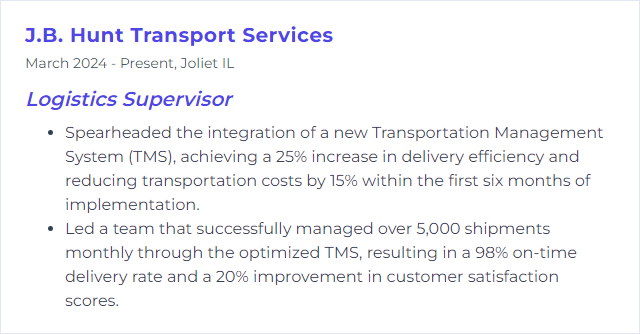
8. Lean Six Sigma
Lean Six Sigma is a methodology that combines the waste reduction principles of Lean manufacturing with the process improvement tools of Six Sigma to enhance efficiency, eliminate defects, and reduce costs in logistical operations.
Why It's Important
Lean Six Sigma is important for a Logistics Supervisor because it combines waste reduction (Lean) and process variation and defect reduction (Six Sigma), leading to more efficient, reliable, and high-quality logistics operations. This results in cost savings, improved customer satisfaction, and a competitive advantage in the marketplace.
How to Improve Lean Six Sigma Skills
To enhance Lean Six Sigma as a Logistics Supervisor, focus on these concise strategies:
- Continuous Learning: Enroll in Lean Six Sigma certification courses to deepen your understanding and stay updated with the latest methodologies.
- Process Mapping: Utilize process mapping tools to visualize and streamline logistics processes, reducing waste and inefficiencies.
- Data Analysis: Leverage statistical software for data-driven decision-making, identifying areas for improvement in your logistics operations.
- Kaizen Events: Organize regular Kaizen events with your team to foster a culture of continuous improvement and collaborative problem-solving.
- Benchmarking: Conduct benchmarking studies to compare your logistics processes against industry standards and identify best practices.
- Voice of the Customer (VOC): Collect and analyze customer feedback to ensure logistics services meet or exceed customer expectations, enhancing satisfaction and loyalty.
- Cross-Functional Teams: Build cross-functional teams to encourage collaboration and innovation, leveraging diverse perspectives to solve logistics challenges.
By implementing these strategies, you can significantly improve Lean Six Sigma practices within your logistics operations, driving efficiency, reducing costs, and enhancing customer satisfaction.
How to Display Lean Six Sigma Skills on Your Resume
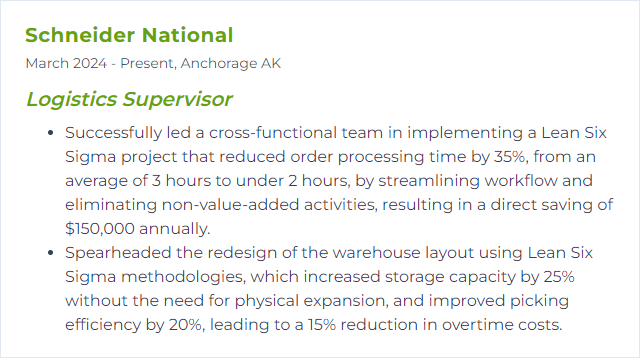
9. RFID Technology
RFID (Radio Frequency Identification) technology allows the wireless use of electromagnetic fields to transfer data, for the purposes of automatically identifying and tracking tags attached to objects. In logistics, it enables real-time tracking of inventory and assets, significantly improving efficiency and accuracy in supply chain management.
Why It's Important
RFID technology is crucial for a Logistics Supervisor as it enables efficient tracking and management of inventory in real-time, significantly reducing errors, improving supply chain visibility, and enhancing overall operational efficiency.
How to Improve RFID Technology Skills
Improving RFID technology, particularly from a Logistics Supervisor's perspective, involves enhancing accuracy, range, and data integration capabilities. Here are concise points for improvement:
Enhance Accuracy: Utilize advanced data filtering algorithms to reduce false reads and improve tag discrimination. Consider dual-frequency RFID tags for environments with high metal or liquid presence. RFID Journal provides insights on latest advancements.
Extend Range: Invest in ultra-high frequency (UHF) RFID systems for longer read ranges, suitable for tracking assets over larger areas. Active RFID tags, though more expensive, offer even greater range and are discussed in resources like ScienceDirect.
Improve Data Integration: Ensure seamless integration of RFID data with your existing Warehouse Management System (WMS) or Transportation Management System (TMS) for real-time visibility. GS1 US has standards and guidelines for efficient data exchange.
Strengthen Security: Implement advanced encryption and authentication protocols to safeguard data transmission from tags to readers. IEEE Xplore offers research papers on the latest security technologies in RFID.
Adopt Multi-Tagging: Use multiple tags per item for redundancy and ensure consistent readability regardless of orientation or environmental conditions. Explore RFID & Wireless IoT Global for case studies on multi-tagging applications.
Regular Updates and Maintenance: Keep your RFID system's firmware and software updated to leverage the latest features and security patches. Engage with vendors for routine system checks and maintenance.
By focusing on these areas, logistics operations can achieve higher efficiency, accuracy, and security in tracking and managing assets.
How to Display RFID Technology Skills on Your Resume
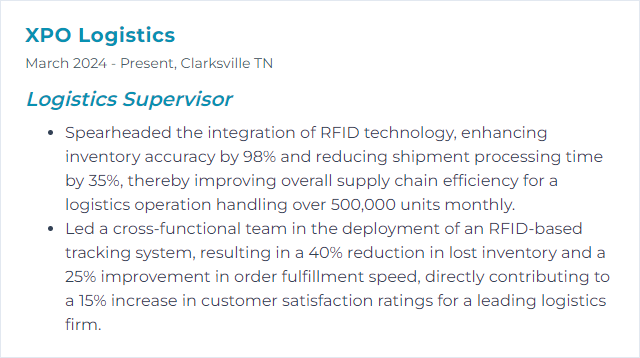
10. EDI (Electronic Data Interchange)
EDI (Electronic Data Interchange) is a standardized method for exchanging business documents, such as purchase orders and invoices, electronically between companies, streamlining logistics and supply chain operations.
Why It's Important
EDI (Electronic Data Interchange) is crucial for a Logistics Supervisor as it streamlines the exchange of critical documents (like purchase orders, invoices, and shipping notices) between companies, significantly improving operational efficiency, reducing errors, and enhancing communication with partners, leading to faster, more accurate, and cost-effective logistics processes.
How to Improve EDI (Electronic Data Interchange) Skills
Improving EDI for a Logistics Supervisor involves enhancing data accuracy, streamlining processes, and ensuring robust security. Here are concise steps:
Assess and Update EDI Standards: Regularly review and update your EDI standards to ensure they meet current industry practices. EDI Standards.
Automate EDI Processes: Implement automation tools to reduce manual data entry and minimize errors. Tools like SPS Commerce can automate transactions between you and your trading partners.
Integrate EDI with ERP Systems: Ensure seamless data flow between EDI and your Enterprise Resource Planning (ERP) systems for real-time information access. ERP Integration.
Enhance Security Measures: Adopt advanced security protocols to protect sensitive data transmitted via EDI. EDI Security Best Practices.
Train Staff on EDI Usage: Provide regular training for your team on new features and best practices in EDI management. EDI Training.
Monitor and Analyze EDI Transactions: Use analytics tools to monitor EDI transactions for insights into improving efficiency and identifying issues early. EDI Analytics.
By focusing on these areas, a Logistics Supervisor can significantly improve the efficiency and reliability of their organization's EDI processes.
How to Display EDI (Electronic Data Interchange) Skills on Your Resume
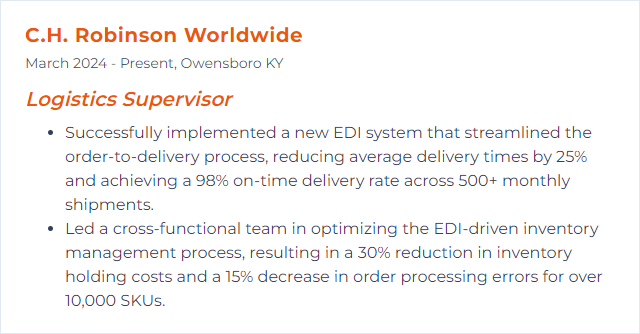
11. JIT (Just-In-Time)
JIT (Just-In-Time) is a logistics and inventory management strategy aimed at reducing inventory costs and enhancing efficiency by receiving goods only as they are needed for the production process, minimizing warehouse storage needs.
Why It's Important
JIT minimizes inventory costs, enhances efficiency, and ensures timely delivery of goods, crucial for a Logistics Supervisor to optimize supply chain operations and meet customer demands efficiently.
How to Improve JIT (Just-In-Time) Skills
To improve Just-In-Time (JIT) systems as a Logistics Supervisor, consider the following concise steps:
Supplier Relationships: Strengthen relationships with suppliers for reliable, timely deliveries. Harvard Business Review discusses building deep supplier relationships.
Inventory Management: Utilize inventory management software for real-time tracking and demand forecasting. Shopify offers insights on inventory management systems.
Process Optimization: Streamline logistics processes through lean management techniques to reduce waste and improve efficiency. The Lean Enterprise Institute provides resources on lean principles.
Technology Integration: Adopt advanced technologies like IoT and AI for better supply chain visibility and predictive analytics. IBM explores the importance of supply chain visibility.
Continuous Improvement: Implement a culture of continuous improvement (Kaizen) to regularly assess and enhance JIT systems. ASQ offers resources on Kaizen for continuous improvement.
By focusing on these areas, you can significantly enhance JIT operations, ensuring products are produced and delivered only as needed, minimizing inventory costs, and improving overall efficiency.
How to Display JIT (Just-In-Time) Skills on Your Resume
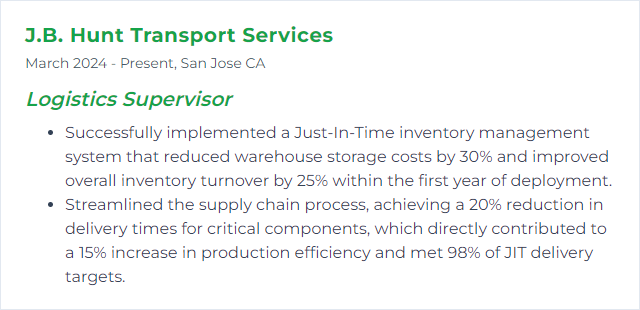
12. CPFR (Collaborative Planning, Forecasting, and Replenishment)
CPFR (Collaborative Planning, Forecasting, and Replenishment) is a business practice where supply chain partners collaborate on planning, forecasting, and inventory management to optimize the supply chain process, reduce costs, and improve service delivery.
Why It's Important
CPFR is important because it enhances supply chain coordination, improves inventory management, and reduces costs by aligning forecasting and replenishment plans between suppliers and retailers, leading to increased efficiency and customer satisfaction.
How to Improve CPFR (Collaborative Planning, Forecasting, and Replenishment) Skills
Improving CPFR involves enhancing collaboration, data sharing, and technology utilization between partners. Here are concise steps for a Logistics Supervisor:
Strengthen Partnerships: Foster open communication and trust among all partners. Establish clear roles and responsibilities. Collaborative Partnerships.
Standardize Processes: Adopt industry standards for data exchange and process management to ensure consistency and efficiency. GS1 Standards.
Enhance Data Quality: Ensure the accuracy, timeliness, and relevance of shared data. Implement tools for real-time data sharing. Data Quality Management.
Leverage Technology: Utilize advanced forecasting and replenishment software. Consider cloud-based solutions for better scalability and collaboration. Cloud Solutions.
Continuous Improvement: Regularly review performance metrics and adjust strategies as needed. Implement feedback loops for ongoing optimization. Continuous Improvement in Supply Chain.
Training and Development: Invest in training for all stakeholders to ensure they understand CPFR processes and tools. Supply Chain Training.
By focusing on these areas, a Logistics Supervisor can significantly enhance CPFR efforts, leading to improved supply chain efficiency and performance.
How to Display CPFR (Collaborative Planning, Forecasting, and Replenishment) Skills on Your Resume
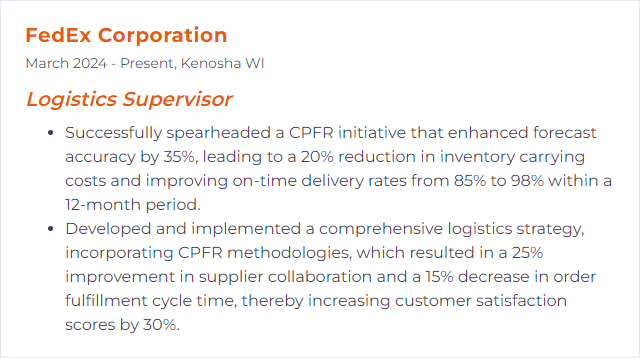