Top 12 Inventory Coordinator Skills to Put on Your Resume
An effective inventory coordinator is crucial for maintaining the operational efficiency of any organization, ensuring that supply aligns with demand. Highlighting the top skills for this role on your resume can significantly enhance your job prospects, showcasing your capability to manage and optimize inventory with precision and strategic insight.
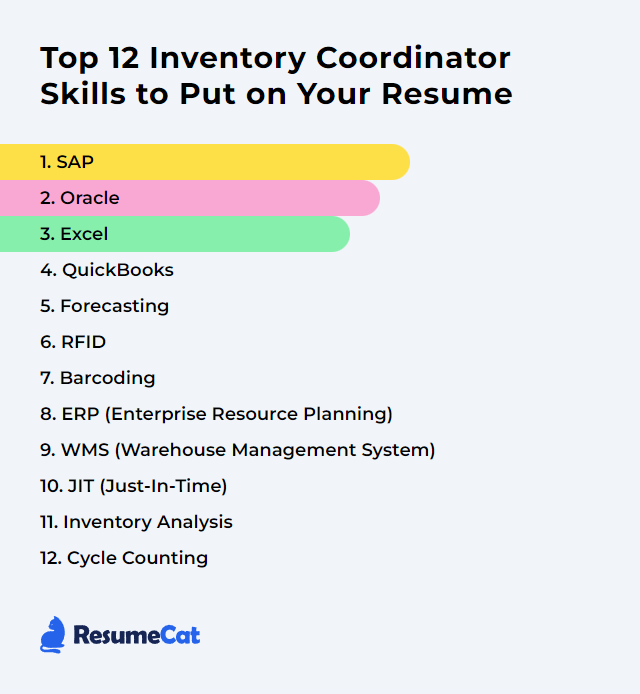
Inventory Coordinator Skills
- SAP
- Oracle
- Excel
- QuickBooks
- Forecasting
- RFID
- Barcoding
- ERP (Enterprise Resource Planning)
- WMS (Warehouse Management System)
- JIT (Just-In-Time)
- Inventory Analysis
- Cycle Counting
1. SAP
SAP is an enterprise resource planning (ERP) software used to manage business operations and customer relations, including inventory management. For an Inventory Coordinator, it streamlines tracking, ordering, and analyzing stock levels, ensuring efficient inventory control and optimization.
Why It's Important
SAP is crucial for an Inventory Coordinator because it streamlines inventory management, enhances data accuracy, and facilitates real-time tracking of stock levels, orders, and deliveries, leading to improved efficiency and decision-making in inventory control.
How to Improve SAP Skills
Improving your SAP experience as an Inventory Coordinator involves streamlining processes, enhancing data accuracy, and leveraging SAP's functionalities to optimize inventory management. Here are concise steps and resources to help you get started:
Understand SAP Inventory Management Fundamentals: Ensure you have a solid grasp of SAP's inventory management modules. This knowledge will help you navigate the system efficiently and make the most of its functionalities.
Utilize SAP Training Resources: Take advantage of SAP's official training and certification programs to enhance your skills. SAP Learning Hub (SAP Learning Hub) offers a wide range of resources tailored to various roles and skill levels.
Implement Best Practices for Data Accuracy: Consistently maintain accurate data within SAP by regularly updating inventory records, conducting physical inventory checks, and reconciling discrepancies. Accurate data is crucial for effective inventory management.
Automate Inventory Processes: Leverage SAP's automation capabilities to streamline inventory processes, such as reorder point planning and inventory forecasting. This can reduce manual errors and save time.
Customize Reports for Better Insight: Customize SAP inventory reports to meet your specific needs. This enables better decision-making by providing insights into inventory levels, turnover rates, and demand forecasting. SAP's official documentation (SAP Help Portal) offers guidance on report customization.
Engage with the SAP Community: Join SAP forums and communities (SAP Community) to exchange knowledge, tips, and best practices with other professionals. Learning from peers can provide new perspectives and solutions to common challenges.
Remember, continuous learning and adapting to new functionalities within SAP are key to improving its usage for inventory management.
How to Display SAP Skills on Your Resume
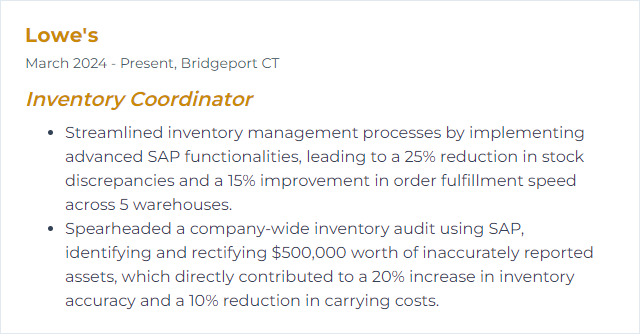
2. Oracle
Oracle is a comprehensive software system that provides various applications and tools for database management, cloud solutions, and enterprise resource planning (ERP), including inventory management. For an Inventory Coordinator, Oracle can help in tracking inventory levels, orders, sales, and deliveries to optimize stock levels and improve supply chain efficiency.
Why It's Important
Oracle is important for an Inventory Coordinator because it provides a comprehensive and integrated database system for efficiently managing inventory levels, tracking stock movements, and forecasting demand, thereby optimizing inventory control and reducing costs.
How to Improve Oracle Skills
To improve Oracle usage as an Inventory Coordinator, focus on the following concise steps:
Enhance Data Accuracy: Regularly update and validate inventory data to ensure accurate forecasting and reporting. Oracle Inventory Management.
Leverage Oracle Training: Utilize Oracle University's training courses to improve skills and understanding of Oracle's inventory system. Oracle University Training.
Implement Automated Processes: Use Oracle's automation features for replenishment, ordering, and inventory tracking to increase efficiency. Oracle Process Automation.
Utilize Reporting Tools: Exploit Oracle's advanced reporting tools for inventory analysis to make informed decisions. Oracle Analytics.
Customize Oracle for Your Needs: Tailor Oracle applications through customization to fit your specific inventory requirements. Oracle Application Customization.
Engage with Oracle Community: Join Oracle forums and communities for tips, advice, and best practices sharing. Oracle Community.
By focusing on these areas, you can significantly improve your proficiency and efficiency in managing inventory using Oracle.
How to Display Oracle Skills on Your Resume
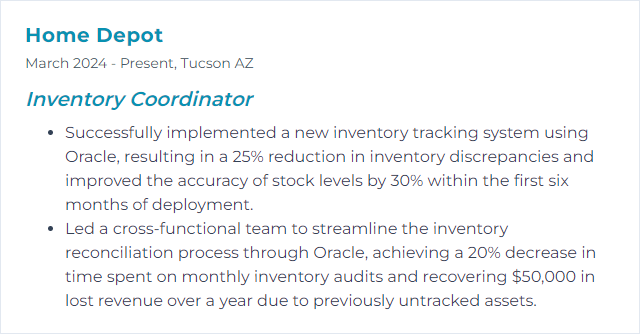
3. Excel
Excel is a spreadsheet program used for organizing, analyzing, and storing data, essential for inventory coordinators to track, manage, and forecast inventory levels efficiently.
Why It's Important
Excel is important for an Inventory Coordinator because it enables efficient tracking, analysis, and reporting of inventory levels, facilitating accurate stock management and decision-making.
How to Improve Excel Skills
To improve Excel skills as an Inventory Coordinator, focus on mastering the following areas:
Data Management: Learn to organize and manage inventory data efficiently. Use tables and named ranges for easier data manipulation.
Formulas and Functions: Get proficient in essential functions like
VLOOKUP
,INDEX+MATCH
, andSUMIFS
for data analysis and calculations. ExcelJet offers clear guides.PivotTables: Master PivotTables to summarize, analyze, and present large amounts of inventory data. The Excel PivotTable Tutorial is a great place to start.
Data Validation: Use data validation to ensure accurate data entry. Learn how to set dropdown lists for inventory categories. Excel Easy provides a straightforward tutorial.
Conditional Formatting: Implement conditional formatting to highlight important information, like low stock levels. Ablebits offers examples of useful formulas.
Macros and VBA: Automate repetitive tasks and customize Excel functions with basic VBA and macros. The Excel VBA Tutorial is an excellent resource for beginners.
Excel Shortcuts: Increase efficiency by mastering keyboard shortcuts. ExcelJet's Shortcut List is a comprehensive resource.
By focusing on these areas and practicing regularly, you'll significantly improve your Excel skills, making inventory management more efficient and accurate.
How to Display Excel Skills on Your Resume
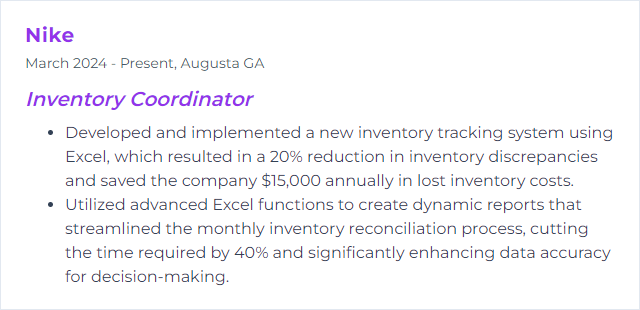
4. QuickBooks
QuickBooks is an accounting software designed to manage financial operations such as sales, expenses, and inventory, enabling an Inventory Coordinator to track stock levels, orders, and sales efficiently.
Why It's Important
QuickBooks is important for an Inventory Coordinator as it efficiently tracks and manages inventory levels, costs, and sales data, ensuring accurate financial reporting and optimal inventory control.
How to Improve QuickBooks Skills
Improving QuickBooks for an Inventory Coordinator can be achieved through a few key steps:
Use Advanced Inventory Features: Ensure QuickBooks is upgraded to include Advanced Inventory for real-time tracking and management. QuickBooks Advanced Inventory
Integrate with External Inventory Management Tools: Integrate QuickBooks with specialized inventory management tools for enhanced functionalities. Fishbowl Inventory is a popular option.
Automate Data Entry: Utilize barcode scanning to reduce manual data entry errors. QuickBooks Desktop Enterprise supports this feature. Barcode Scanning
Regularly Update Inventory: Schedule regular inventory updates to ensure accuracy, aiding in better forecasting and replenishment strategies.
Utilize Custom Fields and Reports: Customize fields and reports in QuickBooks for specific inventory tracking needs, helping in better analysis and decision-making. Custom Fields
Educate and Train Staff: Invest in training for staff on QuickBooks’ latest inventory management features to maximize efficiency. QuickBooks offers training resources. QuickBooks Training
Implementing these strategies can significantly improve inventory management within QuickBooks, making the process more efficient for an Inventory Coordinator.
How to Display QuickBooks Skills on Your Resume
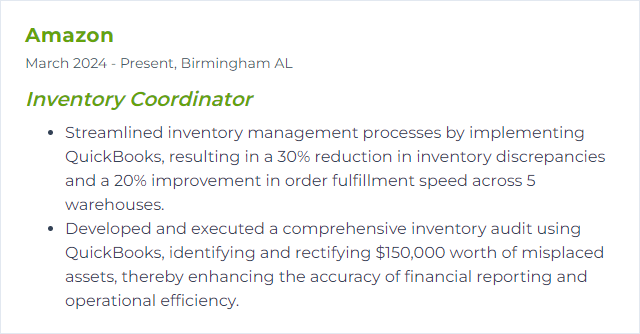
5. Forecasting
Forecasting, in the context of an Inventory Coordinator, involves predicting future inventory requirements based on historical sales data, trends, and market analysis to ensure optimal stock levels, minimize costs, and meet customer demand efficiently.
Why It's Important
Forecasting is crucial for an Inventory Coordinator as it helps in predicting demand, ensuring optimal stock levels, avoiding overstock or stockouts, and improving customer satisfaction by guaranteeing product availability. This leads to efficient inventory management, cost reduction, and enhanced profitability.
How to Improve Forecasting Skills
To improve forecasting as an Inventory Coordinator, focus on the following concise strategies:
Leverage Historical Data: Analyze past sales trends to predict future demand accurately. Tools like Excel can be helpful for basic forecasting models.
Implement Forecasting Software: Utilize specialized forecasting software that employs algorithms and AI to enhance accuracy.
Consider External Factors: Stay informed about market trends, seasons, and events that could impact demand. Resources like IBISWorld provide industry-specific insights.
Collaborate with Stakeholders: Regular communication with sales, marketing, and suppliers can offer valuable insights. Tools like Slack facilitate cross-functional collaboration.
Continuously Monitor and Adjust: Use a KPI dashboard to track forecast accuracy and adjust your methods in real-time.
Educate Yourself: Enhance your skills with courses from platforms like Coursera that offer specialized training in inventory management and forecasting.
Remember, forecasting is an iterative process that improves with ongoing refinement and adaptation to new information.
How to Display Forecasting Skills on Your Resume
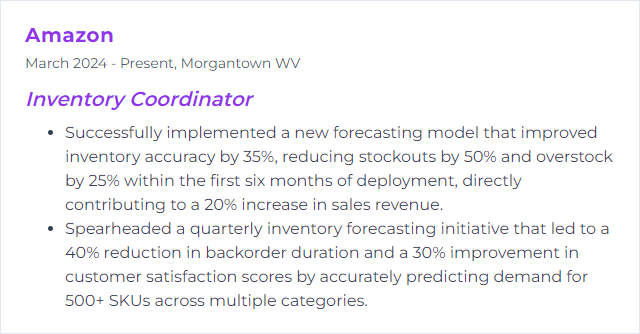
6. RFID
RFID (Radio-Frequency Identification) is a technology used for tracking and managing inventory by using tags that emit radio signals to identify and track items wirelessly.
Why It's Important
RFID is important for an Inventory Coordinator as it enables automatic, real-time tracking of inventory, significantly improving accuracy, efficiency, and the management of stock levels, reducing manual labor and errors.
How to Improve RFID Skills
To improve RFID for inventory management:
- Update Hardware: Invest in the latest RFID readers and tags with better range and sensitivity for accurate tracking.
- Enhance Software: Use advanced inventory management software that integrates seamlessly with RFID technology for real-time updates and analytics.
- Optimize Placement: Implement strategic placement of RFID tags and readers to ensure maximum coverage and minimize dead zones.
- Regular Training: Conduct regular training sessions for staff on the latest RFID practices and technologies to improve efficiency.
- Maintain Equipment: Schedule regular maintenance checks for RFID equipment to prevent downtime.
- Security Measures: Enhance security protocols to protect RFID data from unauthorized access and ensure data integrity.
By focusing on these areas, an Inventory Coordinator can significantly improve RFID efficiency and reliability for better inventory management.
How to Display RFID Skills on Your Resume
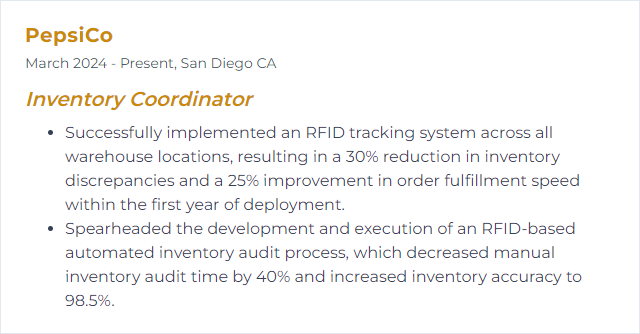
7. Barcoding
Barcoding is a method of representing data in a visual, machine-readable form, which involves attaching unique codes to items in inventory to efficiently track, manage, and update stock levels, facilitating accurate and rapid data collection and inventory control for an Inventory Coordinator.
Why It's Important
Barcoding is crucial for an Inventory Coordinator as it streamlines inventory tracking, enhances accuracy, speeds up data entry, and reduces errors, ensuring efficient inventory management and optimal stock levels.
How to Improve Barcoding Skills
To improve barcoding as an Inventory Coordinator, focus on the following steps:
Standardize Labels: Ensure consistency in barcode labels across all inventory items. Use universally recognized formats like UPC or EAN for broader compatibility (GS1 Standards).
Update Scanning Equipment: Invest in modern, efficient scanners that can read barcodes quickly and accurately, reducing manual input errors (Barcode Scanner Guide).
Implement Quality Control: Regularly check and maintain the integrity of barcodes to prevent scanning issues. This can involve physical checks and using software to detect errors (Quality Control Tips).
Training: Provide comprehensive training to staff on proper scanning techniques and the importance of accurate barcoding to minimize human errors (Effective Training Strategies).
Use Barcode Software: Adopt advanced inventory management software that supports barcode scanning, enabling real-time tracking and updates (Software Advice).
Continuous Improvement: Regularly review and optimize your barcoding system based on feedback and technological advancements to ensure efficiency and accuracy (Continuous Improvement Guide).
How to Display Barcoding Skills on Your Resume
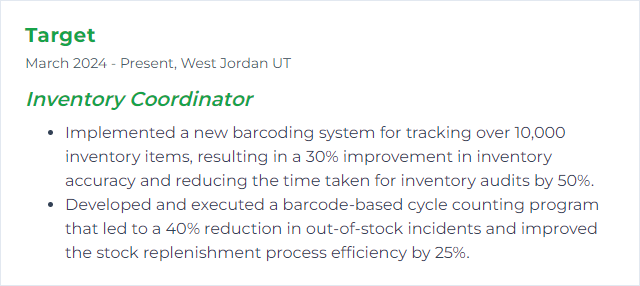
8. ERP (Enterprise Resource Planning)
ERP (Enterprise Resource Planning) is a software system that integrates and manages all the core processes of a business, including inventory management, in a unified system, allowing for streamlined operations, real-time data access, and improved decision-making for inventory coordinators.
Why It's Important
ERP is crucial for an Inventory Coordinator as it integrates all facets of inventory management—tracking stock levels, orders, and deliveries—ensuring accurate, real-time visibility and control over inventory, optimizing stock levels, and reducing operational costs.
How to Improve ERP (Enterprise Resource Planning) Skills
To improve ERP for an Inventory Coordinator, focus on:
Data Accuracy: Ensure all inventory data is accurate and up-to-date. This involves regular audits and reconciliations. Here's a guide on data accuracy in ERP.
Integration: Integrate ERP with other systems (e.g., CRM, SCM) for seamless information flow. Explore integration strategies.
Training & Support: Provide comprehensive training and ongoing support to users to maximize ERP utilization. Training tips.
Customization: Customize ERP functions to fit inventory management needs without overcomplicating the system. Understanding ERP customization.
Process Optimization: Continuously review and optimize inventory processes within the ERP to enhance efficiency. Learn about process optimization.
Forecasting and Planning: Utilize ERP's forecasting tools to better predict stock requirements and minimize overstock or stockouts. Forecasting insights.
Feedback Loop: Establish a feedback loop with users to identify pain points and areas for improvement in the ERP system. Feedback importance.
By focusing on these areas, an Inventory Coordinator can significantly improve the efficiency and effectiveness of their ERP system.
How to Display ERP (Enterprise Resource Planning) Skills on Your Resume
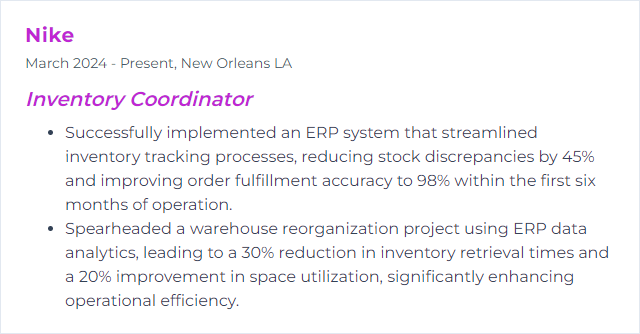
9. WMS (Warehouse Management System)
A Warehouse Management System (WMS) is a software solution that optimizes and controls warehouse operations, from inventory management to order fulfillment, aimed at improving efficiency and accuracy in tasks relevant to an Inventory Coordinator.
Why It's Important
A Warehouse Management System (WMS) is crucial for an Inventory Coordinator as it optimizes warehouse operations by automating inventory tracking, enhancing accuracy, and improving the efficiency of picking, packing, and shipping processes, leading to timely order fulfillment and inventory control.
How to Improve WMS (Warehouse Management System) Skills
Improving a Warehouse Management System (WMS) involves several strategic steps to enhance its efficiency and effectiveness. Here's a concise guide tailored for an Inventory Coordinator:
Data Accuracy: Ensure all inventory data is accurately recorded and updated in real-time. Utilize barcode scanning and RFID technology for precise tracking.
Process Optimization: Regularly review and streamline warehouse processes. Implement Lean principles to eliminate waste and increase efficiency.
Software Updates: Keep the WMS software updated with the latest features and security patches. Collaborate with vendors for custom enhancements specific to your needs.
Training: Conduct ongoing training sessions for staff on the latest WMS features and best practices to ensure proficient usage.
Integration: Integrate WMS with other systems such as ERP, CRM, and e-commerce platforms for seamless data flow. Explore integration tools and services like Zapier for automation between apps.
Performance Monitoring: Utilize WMS analytics and reporting tools to monitor performance metrics. Address any issues promptly to maintain optimal operations.
Feedback Loop: Establish a feedback mechanism for users to report issues and suggest improvements. This can lead to actionable insights and enhancements.
By focusing on these key areas, an Inventory Coordinator can significantly improve the effectiveness of a Warehouse Management System.
How to Display WMS (Warehouse Management System) Skills on Your Resume
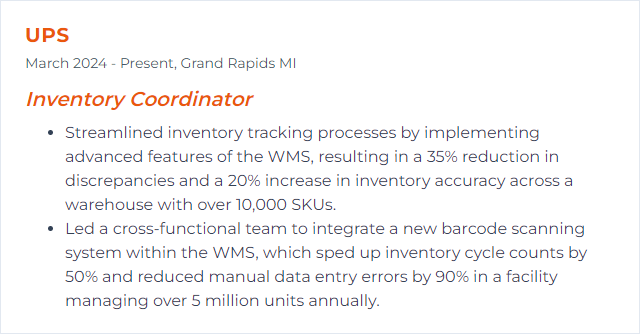
10. JIT (Just-In-Time)
JIT (Just-In-Time) is an inventory management strategy aimed at reducing inventory costs by receiving goods only as they are needed in the production process, thereby minimizing inventory levels. For an Inventory Coordinator, it involves careful planning and coordination with suppliers to ensure timely delivery of materials, avoiding both shortages and excess inventory.
Why It's Important
JIT minimizes inventory costs by ensuring materials and products are ordered and received only as needed, reducing storage space and minimizing waste, thereby improving cash flow and operational efficiency.
How to Improve JIT (Just-In-Time) Skills
Improving JIT (Just-In-Time) inventory management involves optimizing processes to ensure materials are received and products are produced only as needed, minimizing waste and storage costs. For an Inventory Coordinator, key strategies include:
Supplier Relationships: Develop strong relationships with suppliers to ensure reliable, timely deliveries. Work on communication and possibly integrate systems for seamless order processing. Supplier Management
Demand Forecasting: Use advanced analytics and historical data to accurately predict customer demand, adjusting procurement and production schedules accordingly. Forecasting Techniques
Inventory Visibility: Implement inventory management software for real-time visibility into stock levels, orders, and supplier schedules. This facilitates better decision-making and responsiveness. Inventory Management Software
Lean Inventory: Adopt lean inventory principles, eliminating unnecessary items and focusing on what adds value to meet customer demand efficiently. Lean Inventory Management
Process Optimization: Continuously review and optimize inventory management processes, including order processing, warehousing, and material handling to reduce lead times and costs. Process Improvement
Cross-Functional Teams: Foster collaboration across departments (sales, procurement, production) to ensure alignment on inventory levels and demand forecasts. Team Collaboration
Emergency Planning: Develop contingency plans for supply chain disruptions, including alternative suppliers and safety stock levels. Supply Chain Resilience
By focusing on these areas, an Inventory Coordinator can significantly improve JIT inventory management, resulting in reduced costs, increased efficiency, and higher customer satisfaction.
How to Display JIT (Just-In-Time) Skills on Your Resume

11. Inventory Analysis
Inventory analysis is the process of examining inventory levels, turnover rates, and sales trends to optimize stock levels, reduce costs, and improve customer satisfaction. For an Inventory Coordinator, it involves managing and analyzing inventory data to ensure the right products are available at the right time.
Why It's Important
Inventory Analysis is crucial for an Inventory Coordinator as it helps in optimizing stock levels, reducing carrying costs, ensuring timely replenishment, and preventing overstock or stockouts. This analysis supports informed decision-making for maintaining efficiency and meeting customer demand effectively.
How to Improve Inventory Analysis Skills
Improving inventory analysis involves streamlining processes, enhancing accuracy, and making data-driven decisions. Here are concise steps tailored for an Inventory Coordinator:
Implement Automation Tools: Use software to automate inventory tracking and management. Tools like Zoho Inventory or QuickBooks Commerce can minimize manual errors and save time.
Adopt ABC Analysis: Prioritize inventory based on importance and sales performance. ABC analysis helps in focusing on high-value items. Learn more about ABC Analysis here.
Regular Audits: Conduct regular audits comparing physical inventory counts with system records to maintain accuracy. This guide to inventory auditing provides practical steps.
Analyze Demand Forecasting: Use historical sales data to predict future demand accurately. Tools like Forecast Pro can assist in making informed restocking decisions.
Optimize Inventory Layout: Organize inventory to streamline picking and restocking processes. This involves strategic placement of high-demand items. Effective Warehouse Layout tips can be a good resource.
Enhance Supplier Relationships: Build strong relationships with suppliers for better negotiation on terms and reliability. This guide on supplier relationship management is a useful resource.
Leverage KPIs and Metrics: Monitor Key Performance Indicators (KPIs) such as stock turnover rate, order accuracy, and back-order rate. This helps in identifying inefficiencies. This article lists essential inventory KPIs to track.
Continuous Improvement: Stay updated with industry trends and continuously seek ways to improve inventory management processes. Resources like Supply Chain Management Review provide valuable insights.
By following these steps, an Inventory Coordinator can significantly enhance inventory analysis, leading to better decision-making, reduced costs, and improved customer satisfaction.
How to Display Inventory Analysis Skills on Your Resume
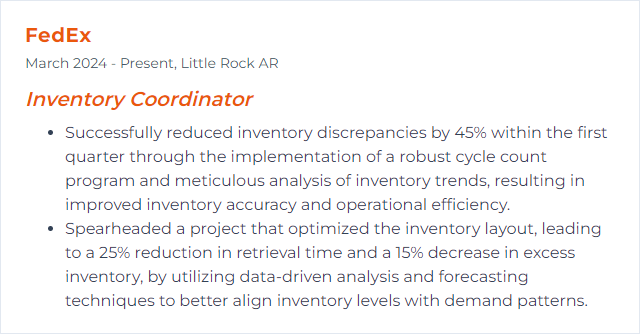
12. Cycle Counting
Cycle counting is a periodic inventory auditing procedure where an Inventory Coordinator counts a small subset of inventory items on a regular basis, ensuring accuracy without the need for a full inventory recount.
Why It's Important
Cycle counting is essential for an Inventory Coordinator as it ensures accurate inventory records, improves order fulfillment accuracy, minimizes stock discrepancies, and reduces the need for disruptive, full-scale physical inventories. This ongoing process aids in maintaining operational efficiency and customer satisfaction.
How to Improve Cycle Counting Skills
Improving cycle counting involves enhancing accuracy, efficiency, and reliability in inventory management. Here's a concise guide for an Inventory Coordinator:
Implement a robust cycle counting schedule: Prioritize items based on ABC analysis, counting high-value items (A) more frequently. ABC Analysis Guide.
Leverage technology: Use barcode scanners or RFID technology to reduce manual errors and streamline the counting process. RFID Technology Benefits.
Train your team: Ensure all team members are trained on cycle counting procedures and the importance of accuracy. Effective Training Tips.
Review and adjust regularly: Analyze cycle count data to identify trends or recurring issues, adjusting your process as needed. Inventory Accuracy.
Utilize cycle counting software: Invest in inventory management software that supports cycle counting for real-time inventory tracking. Choosing Software Tips.
Implementing these strategies will help improve the accuracy and efficiency of your cycle counting process, ensuring a more reliable inventory management system.
How to Display Cycle Counting Skills on Your Resume
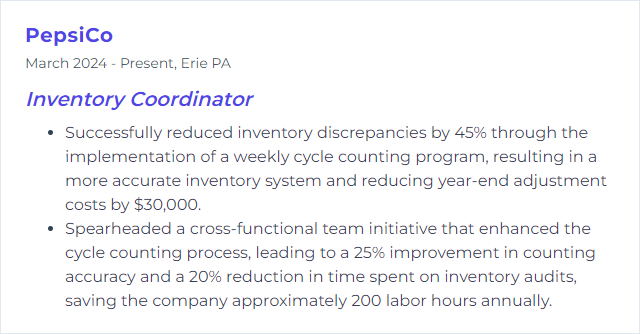