Top 12 Instrument Engineer Skills to Put on Your Resume
In the competitive field of instrumentation engineering, standing out to potential employers requires showcasing a unique set of skills that demonstrates your expertise and adaptability. This article delves into the top 12 skills that instrument engineers should highlight on their resumes, ensuring they capture the attention of recruiters and pave the way for successful career advancements.
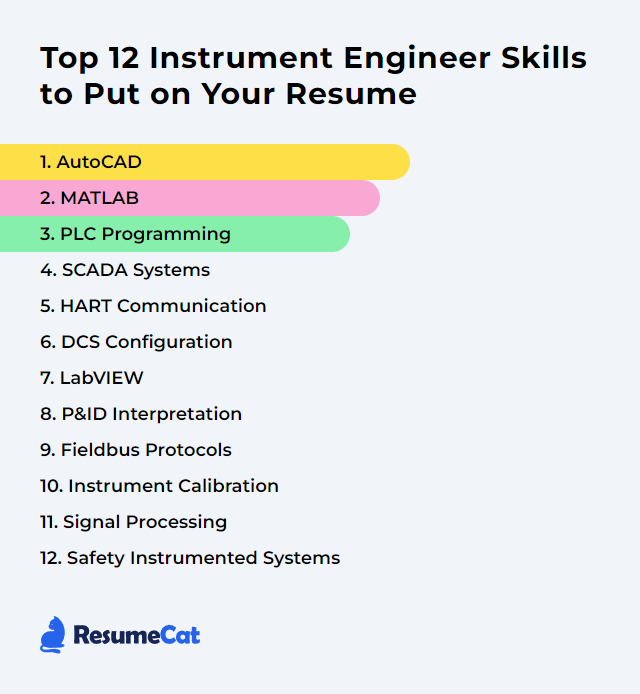
Instrument Engineer Skills
- AutoCAD
- MATLAB
- PLC Programming
- SCADA Systems
- HART Communication
- DCS Configuration
- LabVIEW
- P&ID Interpretation
- Fieldbus Protocols
- Instrument Calibration
- Signal Processing
- Safety Instrumented Systems
1. AutoCAD
AutoCAD is a computer-aided design (CAD) software used by engineers, including instrument engineers, for creating precise 2D and 3D technical drawings and models of instruments, systems, and components.
Why It's Important
AutoCAD is crucial for an Instrument Engineer as it facilitates precise design and drafting of complex instrumentation systems, enabling accurate planning, implementation, and modification of industrial processes and equipment layouts.
How to Improve AutoCAD Skills
Improving your AutoCAD skills as an Instrument Engineer involves focusing on efficiency, accuracy, and staying up-to-date with software enhancements. Here are concise tips:
Master Keyboard Shortcuts: Learning and using AutoCAD's keyboard shortcuts can significantly speed up your work. Autodesk provides a comprehensive list.
Use Data Extraction: Automate data generation for instrument lists or schedules using the Data Extraction tool, saving time and reducing errors. Autodesk offers a helpful guide.
Customize Tool Palettes: Tailor tool palettes for instrumentation engineering tasks to streamline your workflow. This tutorial from Autodesk explains how.
Utilize Dynamic Blocks: Create dynamic blocks for frequently used symbols to save time. This guide explains how to create and use them effectively.
Stay Updated: Keep your AutoCAD software up-to-date to take advantage of the latest features and improvements. Visit Autodesk’s official site for the latest updates.
Participate in Online Forums: Engage with the AutoCAD community in forums such as the Autodesk forums for tips, tricks, and troubleshooting.
Undergo Training: Consider taking advanced AutoCAD courses focused on instrumentation engineering. Websites like LinkedIn Learning offer specialized courses.
By integrating these practices into your workflow, you'll improve both your efficiency and proficiency with AutoCAD as an Instrument Engineer.
How to Display AutoCAD Skills on Your Resume
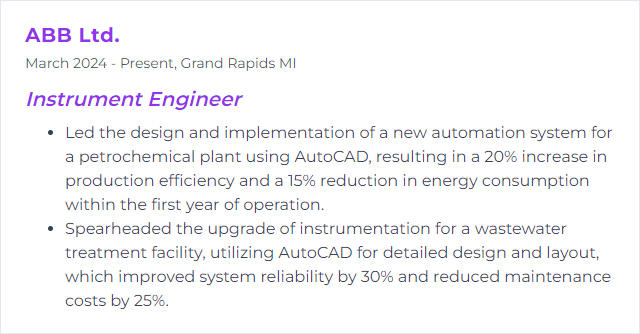
2. MATLAB
MATLAB is a high-performance programming language and environment used for technical computing, data analysis, and visualization, particularly useful for instrument engineers in designing, simulating, and testing instrumentation systems and analyzing measurement data.
Why It's Important
MATLAB is crucial for an Instrument Engineer because it provides powerful tools for system analysis, design, and simulation, enabling efficient development and testing of complex instrumentation and control systems.
How to Improve MATLAB Skills
To improve your MATLAB skills as an Instrument Engineer, focus on mastering the following areas:
Learn the Basics: Start with the fundamentals of MATLAB. MATLAB's own documentation is an excellent place to begin.
Data Visualization: Enhance your ability to visualize data, crucial for instrument engineers for analysis and reporting. MATLAB's graphics documentation provides a good starting point.
Signal Processing: As an Instrument Engineer, being proficient in signal processing in MATLAB is invaluable. Refer to the Signal Processing Toolbox for a deeper understanding.
Automate Your Tasks: Learn to automate repetitive tasks using scripts and functions. Check out this guide on scripting.
Instrument Control Toolbox: Get familiar with the Instrument Control Toolbox for connecting and controlling your instruments directly from MATLAB.
Simulink for System-Level Design: Explore Simulink for model-based design, which is particularly useful for complex system analysis and multi-domain simulation.
Stay Updated and Network: MATLAB Central is a great place to stay updated with the latest trends, find answers, and network with other professionals.
Practice Regularly: Practical application of knowledge will enhance your skills. Work on real-life projects or participate in online challenges.
Online Courses and Certifications: Consider taking online courses from platforms like Coursera, edX, or LinkedIn Learning that offer specific MATLAB courses tailored for engineers.
By focusing on these areas and consistently applying your knowledge to practical problems, you'll significantly improve your MATLAB skills relevant to the field of Instrument Engineering.
How to Display MATLAB Skills on Your Resume
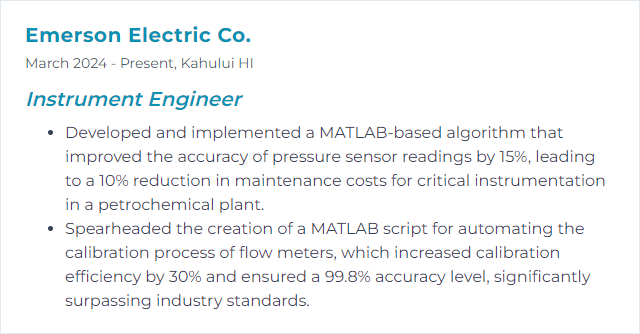
3. PLC Programming
PLC programming involves creating and implementing software instructions for Programmable Logic Controllers (PLCs) to automate industrial processes and machinery, focusing on control, monitoring, and safety functions within an engineering context.
Why It's Important
PLC programming is crucial for Instrument Engineers as it enables the automation and control of industrial processes, ensuring precision, efficiency, and safety in operations.
How to Improve PLC Programming Skills
Improving PLC (Programmable Logic Controller) programming skills involves a combination of understanding fundamental principles, practicing coding, learning from real-world applications, and staying updated with the latest technologies. For an Instrument Engineer, here are concise steps to enhance PLC programming:
Understand the Basics: Solidify your foundation in PLC principles, including logic controls, ladder diagrams, and I/O modules. The PLC Academy offers a good starting point.
Learn from Tutorials: Access online tutorials that cater to various skill levels. PLCdev has resources and guides for both beginners and advanced learners.
Practice Coding: Apply your knowledge by working on real-world projects or simulations. Tools like RSLogix 5000 provide a platform for practicing programming.
Analyze Case Studies: Study how PLCs are applied in different industries to understand diverse programming approaches. Websites like AutomationDirect often showcase project examples.
Join Forums: Engage in communities such as PLCTalk where you can ask questions, share knowledge, and learn from experienced professionals.
Stay Updated: Follow industry news and trends through portals like Control Engineering to keep abreast of the latest in PLC technology.
Attend Workshops and Webinars: Participate in events organized by PLC manufacturers and educational institutions. Sites like ISA offer courses and webinars tailored for Instrument Engineers.
By integrating these steps, you'll progressively enhance your PLC programming skills, contributing significantly to your capabilities as an Instrument Engineer.
How to Display PLC Programming Skills on Your Resume
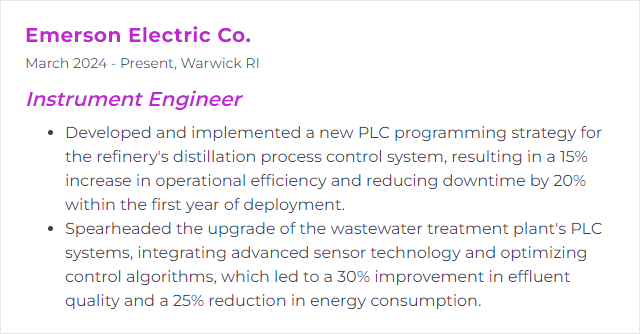
4. SCADA Systems
SCADA (Supervisory Control and Data Acquisition) systems are computer-based systems used by instrument engineers to monitor and control industrial processes and infrastructures in real-time. They gather data from sensors and instruments located at various sites, allowing for centralized control, operational efficiency, and enhanced decision-making.
Why It's Important
SCADA systems are crucial for Instrument Engineers as they enable the monitoring, control, and automation of industrial processes and equipment, ensuring efficiency, reliability, and safety in operations.
How to Improve SCADA Systems Skills
Improving SCADA (Supervisory Control and Data Acquisition) systems, particularly from an Instrument Engineer's perspective, involves enhancing reliability, security, data management, and integration capabilities. Here's a very short and concise guide:
Enhance Security: Implement strong cybersecurity measures to protect against threats. Utilize resources from the Industrial Control Systems Cyber Emergency Response Team (ICS-CERT) for best practices and updates.
Improve Data Management: Optimize data collection and analysis by integrating advanced data analytics tools. Explore OSIsoft PI System for efficient data management solutions.
Upgrade Hardware: Regularly assess and upgrade sensors, actuators, and controllers to improve accuracy and reliability. Honeywell and Siemens offer state-of-the-art industrial automation hardware.
Implement Redundancy: Design systems with redundancy in critical components to enhance reliability and minimize downtime. Schneider Electric provides solutions for high-availability SCADA systems.
Ensure Compatibility and Scalability: Ensure that new devices and software are compatible with existing systems and can scale as needs grow. Rockwell Automation offers scalable automation solutions that integrate seamlessly with legacy systems.
Regular Training and Updates: Ensure staff are regularly trained on the latest technologies and system updates. ISA (International Society of Automation) offers specialized training courses for automation professionals.
System Integration: Integrate SCADA with enterprise systems (ERP, CRM) for better decision-making. SAP and Oracle provide solutions for integrating business processes with SCADA systems.
Improving SCADA systems is an ongoing process that involves keeping up with the latest technological advancements and best practices in the field of industrial automation and control systems.
How to Display SCADA Systems Skills on Your Resume
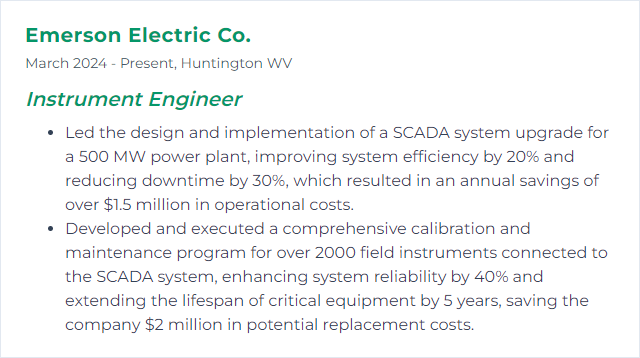
5. HART Communication
HART (Highway Addressable Remote Transducer) Communication is a digital communication protocol used in industrial instrumentation to enable smart field devices to communicate data (such as device status, diagnostic information, and measurement values) over traditional 4-20 mA analog signal lines. For an Instrument Engineer, HART provides a means for two-way field communication, facilitating device configuration, calibration, and troubleshooting without interrupting the analog signal.
Why It's Important
HART (Highway Addressable Remote Transducer) Communication is essential for Instrument Engineers as it enables the seamless integration of digital communication with traditional 4-20 mA analog signaling. This dual functionality allows for real-time access to device diagnostics, configuration, and monitoring without interrupting the analog control signal, enhancing process control, system efficiency, and maintenance capabilities.
How to Improve HART Communication Skills
Improving HART Communication involves ensuring both hardware and software components are properly optimized for effective signal transmission and interpretation. Here are concise steps an Instrument Engineer can follow:
Cable Quality and Layout: Use high-quality, shielded twisted pair cables and maintain proper grounding to minimize noise. Avoid running HART cables parallel to high-voltage or high-current wires.
Device Compatibility: Ensure all devices in the loop (transmitters, controllers, etc.) are HART compatible and properly configured. Check the FieldComm Group for compatibility information.
Loop Impedance: Maintain an appropriate loop impedance within 250 to 600 ohms for optimal signal strength.
Use of Repeaters: For long cable runs or in cases of weak signals, consider using HART repeaters to boost signal integrity.
Software Tools: Utilize diagnostic software tools for network health checking and troubleshooting. Manufacturer tools or third-party applications like PACTware can be invaluable.
Proper Termination: Ensure correct termination of communication lines to prevent reflections and signal degradation.
Regular Maintenance and Updates: Keep all firmware and software within the HART devices updated to the latest versions. Perform regular system checks and calibrations.
Training and Resources: Continuously educate yourself and your team on HART communication advancements and troubleshooting techniques. The International Society of Automation (ISA) offers resources and training.
By focusing on these areas, an Instrument Engineer can significantly improve HART communication effectiveness in their applications.
How to Display HART Communication Skills on Your Resume
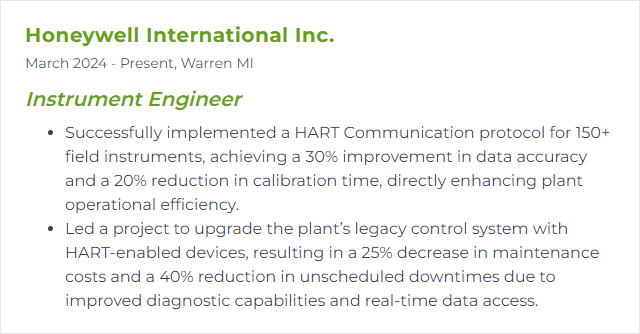
6. DCS Configuration
DCS Configuration, in the context of an Instrument Engineer, involves setting up and customizing a Distributed Control System (DCS) to monitor and control engineering processes and machinery. This includes defining control logic, input/output assignments, process parameters, and user interfaces to ensure optimal performance and safety of industrial operations.
Why It's Important
DCS (Distributed Control System) configuration is crucial for an Instrument Engineer because it ensures optimal control, monitoring, and safety of process operations by accurately defining process parameters, control logic, and interlocks, leading to efficient, reliable, and safe plant operation.
How to Improve DCS Configuration Skills
Improving a Distributed Control System (DCS) configuration requires a strategic approach focusing on system integration, optimization, and automation. Here’s a concise guide for an Instrument Engineer:
Assess Current System: Begin with a comprehensive assessment of your current DCS configuration. Identify inefficiencies, redundancies, and areas for improvement. Emerson's guide on DCS evaluation can provide insights.
Standardize Processes: Implement standardized configurations for processes and operations to enhance consistency and reliability. Yokogawa's approach to standardization offers useful methodologies.
Upgrade Hardware/Software: Ensure your DCS hardware and software are up to date. Upgrading can significantly improve performance, compatibility, and security. Siemens offers modernization tips for DCS systems.
Enhance Cybersecurity: Protect your DCS from cyber threats by implementing robust security measures. Honeywell's cybersecurity solutions can help fortify your defenses.
Integrate Advanced Analytics: Leverage advanced analytics and machine learning to predict maintenance needs, optimize performance, and reduce downtime. Rockwell Automation discusses the integration of analytics into control systems.
Implement Redundancy: Ensure system reliability by implementing redundancy in critical components of your DCS. This can prevent significant downtime. ABB's redundancy features offer insights into creating a more reliable DCS.
Continuous Training: Keep your team updated with the latest DCS technologies and best practices through continuous training and development. ISA offers various training courses for control systems.
Feedback Loops: Establish feedback mechanisms to continuously monitor, assess, and tweak the DCS configuration based on operational data and user feedback.
By focusing on these areas, an Instrument Engineer can significantly improve the efficiency, reliability, and security of a DCS configuration.
How to Display DCS Configuration Skills on Your Resume
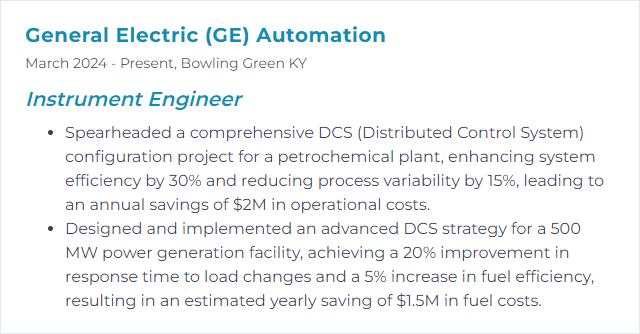
7. LabVIEW
LabVIEW (Laboratory Virtual Instrument Engineering Workbench) is a graphical programming platform used by instrument engineers for developing automated test, measurement, and control systems, enabling quick data acquisition, instrument control, and industrial automation.
Why It's Important
LabVIEW is crucial for Instrument Engineers because it provides a powerful and intuitive graphical programming environment for designing, prototyping, and deploying applications for test, measurement, and control systems, enhancing efficiency and reducing development time.
How to Improve LabVIEW Skills
Improving your LabVIEW skills as an Instrument Engineer involves a mix of learning, practice, and leveraging community resources. Here are concise strategies:
Engage in Continuous Learning: Enroll in NI's LabVIEW training courses to understand fundamentals and advanced techniques.
Practice Regularly: Apply your knowledge by working on real-world projects or simulations to solidify your skills.
Use Templates and Sample Projects: Explore NI's example programs to learn from existing solutions and best practices.
Join the LabVIEW Community: Participate in forums and user groups to share insights, get help, and stay updated on new features or techniques.
Implement Best Practices: Familiarize yourself with LabVIEW style guidelines and design patterns to write efficient, maintainable, and scalable code.
Explore External Resources: Books like "LabVIEW for Everyone" and websites like LabVIEW MakerHub can offer new perspectives and tips.
By following these steps and continuously exploring new features and tools within the LabVIEW environment, you can enhance your proficiency and efficiency as an Instrument Engineer working with LabVIEW.
How to Display LabVIEW Skills on Your Resume
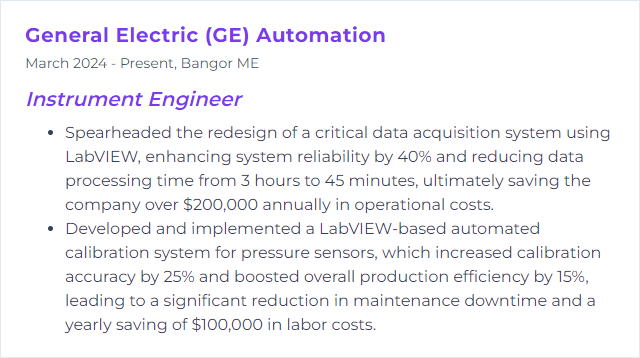
8. P&ID Interpretation
P&ID Interpretation for an Instrument Engineer involves understanding and analyzing Piping and Instrumentation Diagrams (P&IDs) to identify and specify all instruments, valves, and controls necessary for the operation, control, and safety of a process system. It includes interpreting symbols, tags, and lines that represent physical equipment, piping, and instrumentation connections.
Why It's Important
P&ID interpretation is crucial for an Instrument Engineer as it enables the understanding of the process flow, control logic, and instrumentation requirements of a system, ensuring the design, installation, and maintenance of instruments align with operational needs and safety standards.
How to Improve P&ID Interpretation Skills
Improving P&ID (Piping and Instrumentation Diagram) interpretation skills involves a combination of theoretical knowledge, practical experience, and continuous learning. For an Instrument Engineer, here are concise steps to enhance P&ID interpretation capabilities:
Understand Symbols and Notations: Familiarize yourself with common symbols and notations used in P&IDs, including instruments, valves, pumps, and flow directions. The ISA (International Society of Automation) provides guidelines and standards (e.g., ISA-5.1) for symbols and notations.
Learn the Process Flow: Comprehend the overall process flow depicted in the P&ID, including how different equipment and systems are interconnected. This understanding is crucial for troubleshooting and optimizing processes.
Focus on Control Loops and Instrumentation: Pay special attention to control loops and instrumentation details. Understanding how instruments are configured in loops and their function within the control system is key. Resources such as Control Global offer insights into control systems and instrumentation.
Study Safety and Emergency Systems: Identify safety and emergency features in P&IDs, such as relief valves, shutdown systems, and alarms. Knowledge of these systems is vital for ensuring process safety.
Engage in Practical Training and Simulation: Use simulation software or training modules that allow you to interact with virtual P&IDs. Hands-on experience is invaluable for improving interpretation skills.
Participate in Peer Review and Collaboration: Engage with peers and experienced professionals to review P&IDs together. This collaborative approach can provide new insights and a deeper understanding of complex diagrams.
Continuous Learning: Stay updated with industry best practices, standards, and new technologies. Websites like Engineering Institute of Technology offer courses and webinars that can keep your skills sharp.
By following these steps and leveraging the resources provided, an Instrument Engineer can significantly improve their P&ID interpretation skills, leading to better decision-making and system optimization.
How to Display P&ID Interpretation Skills on Your Resume
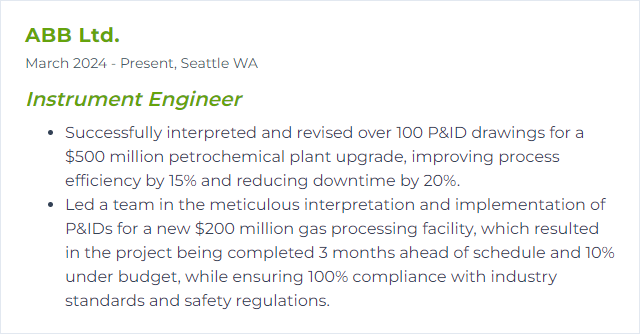
9. Fieldbus Protocols
Fieldbus protocols are a set of digital communication standards used by field instruments and control systems to exchange real-time data. They enable integration, automation, and interoperability among devices from various manufacturers, facilitating efficient process control and monitoring in industrial environments.
Why It's Important
Fieldbus protocols are crucial for Instrument Engineers as they standardize communication among field devices and control systems, enabling efficient data exchange, simplified system integration, and real-time process control. This enhances system diagnostics, reduces wiring costs, and improves overall process efficiency and reliability.
How to Improve Fieldbus Protocols Skills
Improving Fieldbus protocols, such as Foundation Fieldbus, PROFIBUS, and Modbus, involves enhancing communication efficiency, reliability, interoperability, and security. As an Instrument Engineer, focusing on the following areas can lead to significant improvements:
Standardization and Interoperability: Ensure all devices and systems are compliant with the latest Fieldbus standards to improve interoperability. Engage with organizations like the FieldComm Group for Foundation Fieldbus and the PROFIBUS & PROFINET International (PI) for PROFIBUS to stay updated.
Network Design and Topology: Optimize network design for redundancy and reliability. Implement ring, star, or hybrid topologies as appropriate. Resources such as the Belden Guide to Designing Industrial Networks provide valuable insights.
Device Configuration and Management: Utilize advanced device management tools for efficient configuration, diagnostics, and maintenance. Explore tools like the Field Device Tool (FDT) and Electronic Device Description Language (EDDL).
Security Measures: Implement robust security protocols and practices to protect against cyber threats. Refer to guidelines from the ISA/IEC 62443 series for industrial network security.
Data Management and Integration: Leverage advanced data analytics and integration techniques for smarter decision-making. Tools like OPC UA can be useful for seamless data integration; more information is available at the OPC Foundation website.
Training and Education: Continuously educate and train personnel on the latest technologies and best practices. Resources such as ISA offer specialized training courses.
Regular Maintenance and Monitoring: Establish routine checks and balances for the network to preempt failures and ensure optimal performance.
By concentrating on these areas, an Instrument Engineer can significantly improve the performance and reliability of Fieldbus protocols within their organization.
How to Display Fieldbus Protocols Skills on Your Resume
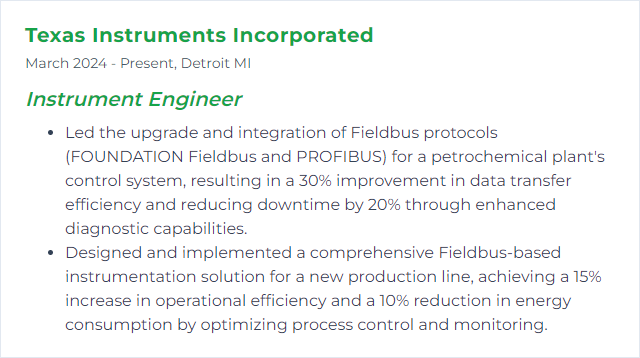
10. Instrument Calibration
Instrument calibration is the process of configuring an instrument to provide accurate and precise measurements, by comparing and adjusting its output to match a known standard or reference value.
Why It's Important
Instrument calibration is crucial for ensuring accurate and reliable measurements, essential for maintaining process safety, compliance with standards, and optimizing performance in industrial operations.
How to Improve Instrument Calibration Skills
Improving instrument calibration involves several key steps to ensure accuracy, reliability, and consistency of measurements. As an Instrument Engineer, focus on:
Regular Calibration Schedule: Establish and adhere to a consistent calibration schedule based on manufacturer recommendations and usage intensity. International Society of Automation (ISA) provides guidelines on calibration frequencies.
Use of Certified Standards: Employ calibration standards that are traceable to national or international standards. For reference standards, NIST (National Institute of Standards and Technology) offers traceable calibration services.
Proper Calibration Techniques: Follow best practices and methodologies for calibration. Techniques should be chosen based on the specific instrument and its application. The ISA provides resources and training on proper calibration techniques.
Environmental Control: Ensure calibration is performed under suitable environmental conditions to minimize external influences. Guidelines on environmental conditions can be found through ASTM International.
Documentation and Records: Maintain comprehensive records of all calibrations, including date, technician, methods, and results. This ensures traceability and aids in identifying trends or recurring issues. ISO 9001 outlines requirements for quality management systems, including documentation.
Continuous Training: Invest in ongoing training for personnel involved in calibration to keep up with best practices and new technologies. ISA offers specialized training courses.
Calibration Software: Utilize calibration management software for scheduling, data management, and trend analysis. Software options can be explored at Fluke Calibration which provides a variety of tools and resources.
Preventive Maintenance: Implement a preventive maintenance program for instruments to ensure they remain in good working condition, reducing calibration issues. IEEE publishes standards and best practices for instrument maintenance.
Validation and Verification: Regularly perform validation and verification of calibration procedures to ensure they are effective. ISO/IEC 17025 provides the general requirements for the competence of testing and calibration laboratories.
Feedback and Continuous Improvement: Encourage feedback from users and technicians to identify areas for improvement. Adopt a continuous improvement approach to calibration processes.
By focusing on these key areas, Instrument Engineers can significantly improve the accuracy, efficiency, and reliability of instrument calibration.
How to Display Instrument Calibration Skills on Your Resume
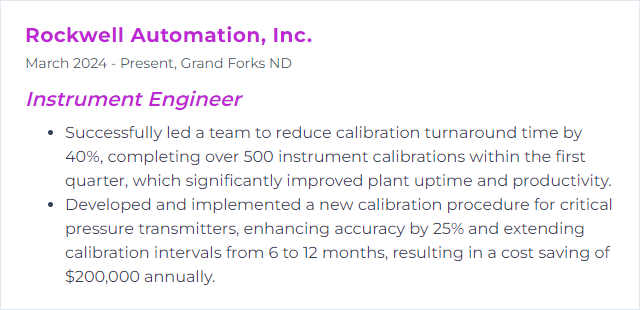
11. Signal Processing
Signal processing involves analyzing, modifying, and synthesizing signals such as sound, images, and biological measurements. For an Instrument Engineer, it entails the techniques and methods used to improve the accuracy, reliability, and efficiency of measuring systems and instruments by filtering noise, extracting relevant features, and converting signals to more useful forms.
Why It's Important
Signal Processing is crucial for Instrument Engineers because it enables the extraction, interpretation, and enhancement of information from various sensor outputs, ensuring accurate and reliable measurements for control, monitoring, and diagnostics in industrial systems.
How to Improve Signal Processing Skills
To improve signal processing as an Instrument Engineer, focus on these concise steps:
Understand the Basics: Ensure a solid understanding of fundamental signal processing concepts. MIT's OpenCourseWare on Signal Processing is a great starting point.
Leverage Software Tools: Utilize software like MATLAB or Python (with libraries such as NumPy and SciPy) for analysis and simulation. MathWorks provides a comprehensive MATLAB tutorial for signal processing.
Filter Design and Application: Learn to design and apply filters effectively to remove noise or extract signals. The Interactive Digital Filter Design tool can be quite handy for understanding and designing filters.
Signal Analysis Techniques: Master various signal analysis techniques, including Fourier analysis, wavelets, and time-frequency methods. The Wavelet Toolbox in MATLAB is a powerful resource for advanced analysis.
Practical Experience: Apply your skills on real-world problems or datasets. Websites like Kaggle offer datasets and competitions that can provide practical experience.
Continuous Learning: Signal processing is an evolving field. Keep updated with the latest research and methodologies through resources like the IEEE Signal Processing Society.
By focusing on these areas, you can significantly improve your signal processing skills in a practical and impactful manner.
How to Display Signal Processing Skills on Your Resume
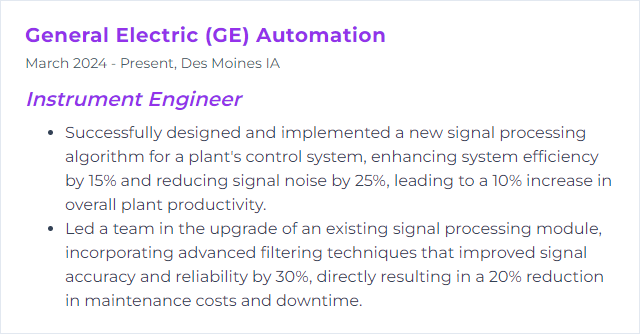
12. Safety Instrumented Systems
Safety Instrumented Systems (SIS) are engineered sets of hardware and software controls designed specifically for managing the safety of industrial processes. They aim to prevent or mitigate hazardous events by taking the process to a safe state when predetermined conditions are violated. For an Instrument Engineer, SIS involves the specification, design, implementation, and maintenance of systems that ensure the safe operation of process systems, in compliance with safety standards like IEC 61508 and IEC 61511.
Why It's Important
Safety Instrumented Systems (SIS) are crucial for an Instrument Engineer because they ensure the safe operation of process industries by automatically taking corrective action to prevent hazardous events, thus protecting people, the environment, and assets.
How to Improve Safety Instrumented Systems Skills
Improving Safety Instrumented Systems (SIS) involves ensuring their reliability, availability, and effectiveness in mitigating risks to acceptable levels. As an Instrument Engineer, focus on the following key areas:
Risk Analysis: Conduct thorough risk assessments to identify and evaluate potential hazards. Use standards like IEC 61511 for guidance.
Design and Selection: Choose appropriate Safety Integrity Level (SIL) for each SIS function based on risk analysis results. Utilize fail-safe designs and redundancy where necessary.
Verification and Validation: Implement rigorous verification and validation processes to ensure that the SIS meets the desired SIL requirements and functions correctly in all scenarios.
Maintenance and Testing: Develop a comprehensive maintenance and testing plan to ensure SIS components function correctly over time. This might include regular functional testing and periodic SIL verification.
Training and Documentation: Ensure all staff are well-trained on SIS operation, maintenance, and emergency procedures. Maintain detailed documentation for all SIS lifecycle phases, from design to decommissioning.
Performance Monitoring: Use real-time monitoring tools to track SIS performance. Analyze data to identify trends and make improvements.
Compliance and Best Practices: Stay updated with industry standards (e.g., IEC 61508, IEC 61511) and best practices. Engage in continuous learning and improvement cycles.
By focusing on these areas, you can enhance the safety, reliability, and performance of Safety Instrumented Systems within your organization.
How to Display Safety Instrumented Systems Skills on Your Resume
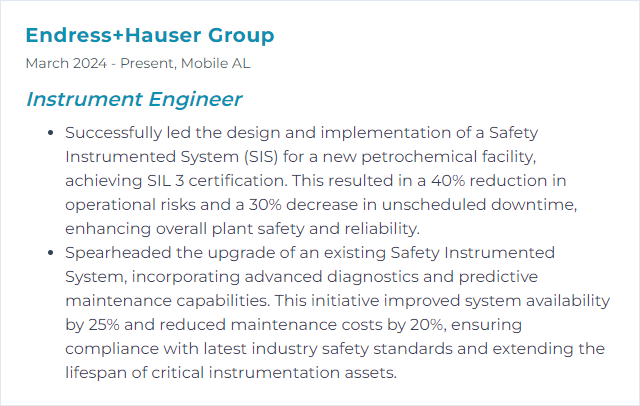