Top 12 Furnace Operator Skills to Put on Your Resume
In the competitive field of furnace operation, having a well-crafted resume that highlights your key skills is crucial for standing out to potential employers. This article will guide you through the top 12 skills essential for furnace operators, ensuring your resume showcases your capabilities effectively and sets you apart in the job market.
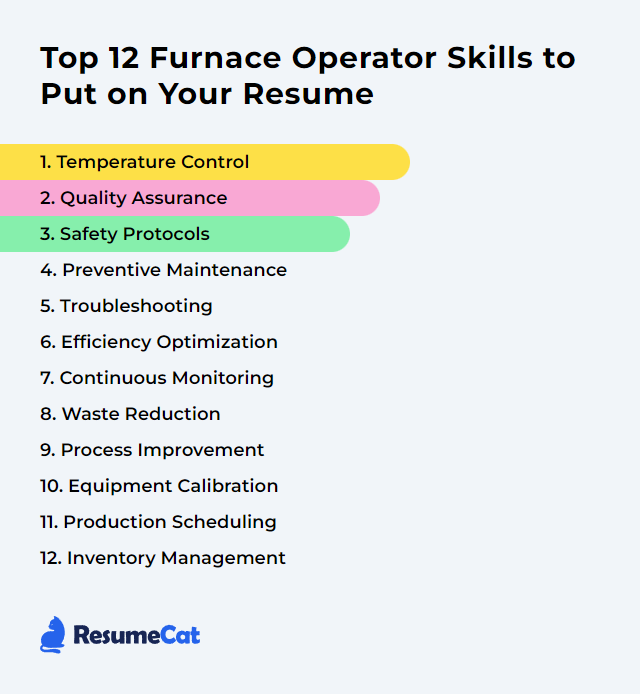
Furnace Operator Skills
- Temperature Control
- Quality Assurance
- Safety Protocols
- Preventive Maintenance
- Troubleshooting
- Efficiency Optimization
- Continuous Monitoring
- Waste Reduction
- Process Improvement
- Equipment Calibration
- Production Scheduling
- Inventory Management
1. Temperature Control
Temperature control, in the context of a furnace operator, refers to the process of monitoring and adjusting the heat levels within a furnace to ensure materials are processed at the correct temperature for optimal quality and efficiency.
Why It's Important
Temperature control is crucial for a furnace operator to ensure consistent quality, prevent material damage, and optimize energy use, leading to safe, efficient, and cost-effective operations.
How to Improve Temperature Control Skills
Improving temperature control in furnace operations involves several key strategies:
Calibration: Regularly calibrate temperature sensors and controllers to ensure accurate readings. Calibration Guide.
Upgrade Controls: Invest in advanced control systems that offer better precision, such as PID controllers. PID Control.
Insulation Maintenance: Inspect and maintain furnace insulation to reduce heat loss and improve efficiency. Insulation Tips.
Preventive Maintenance: Implement a routine maintenance schedule to check for leaks, sensor malfunctions, and other issues that could affect temperature accuracy. Maintenance Best Practices.
Use of Data Loggers: Utilize data loggers to monitor temperature fluctuations over time and adjust operations accordingly. Data Logger Use.
Operator Training: Ensure furnace operators are well-trained on the specific equipment and understand how to manage temperature controls effectively. Training Resources.
By focusing on these areas, furnace operators can achieve more precise temperature control, leading to improved product quality and energy efficiency.
How to Display Temperature Control Skills on Your Resume
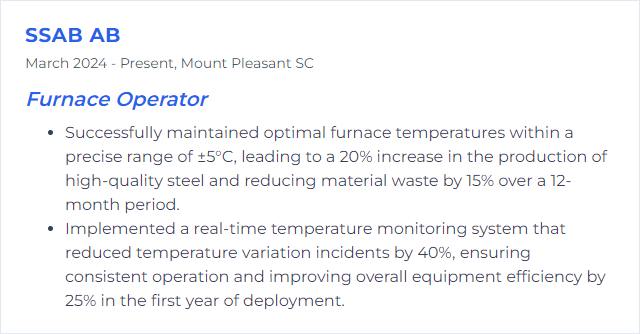
2. Quality Assurance
Quality Assurance (QA) for a Furnace Operator involves ensuring that the furnace operation meets established standards of quality, including temperature accuracy, material handling, and product specifications, to guarantee the integrity and safety of the final output.
Why It's Important
Quality Assurance (QA) is crucial for a Furnace Operator to ensure that the materials processed meet the required standards and specifications, thereby reducing waste, ensuring safety, and maintaining customer satisfaction through the delivery of defect-free products.
How to Improve Quality Assurance Skills
Improving Quality Assurance for a Furnace Operator involves several targeted strategies:
- Training: Ensure all operators undergo continuous training on furnace operation, safety standards, and quality control techniques.
- Standardization: Implement and adhere to industry standards for furnace operation to ensure consistency and quality in processes.
- Maintenance: Regularly schedule maintenance for the furnace to prevent defects and ensure it operates at peak efficiency.
- Monitoring: Utilize real-time monitoring tools to track furnace performance and product quality, allowing for immediate adjustments.
- Feedback Loop: Establish a feedback mechanism within the quality assurance process to continuously improve based on issues and suggestions from both customers and the production team.
By focusing on these areas, a Furnace Operator can significantly enhance the quality assurance process, ensuring a consistent and high-quality product output.
How to Display Quality Assurance Skills on Your Resume
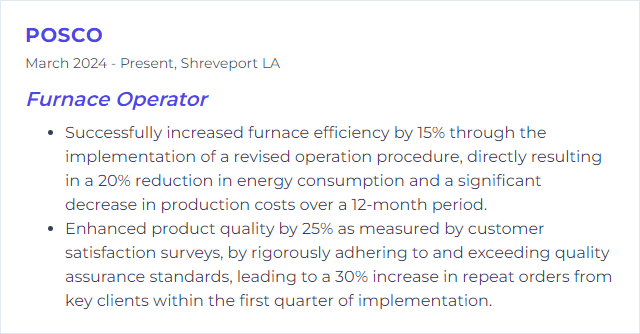
3. Safety Protocols
Safety protocols for a furnace operator are a set of guidelines and procedures designed to ensure the operator's safety when working with industrial furnaces. These include wearing appropriate personal protective equipment (PPE), following proper operating procedures, conducting regular maintenance checks, and being trained in emergency response actions.
Why It's Important
Safety protocols are essential for furnace operators to prevent accidents, ensure safe handling of high-temperature equipment, and protect against hazards like burns, explosions, and toxic gas exposure, ultimately safeguarding the operator's health and maintaining a secure working environment.
How to Improve Safety Protocols Skills
Improving safety protocols for a Furnace Operator involves several key strategies, aimed at minimizing risks and enhancing workplace safety. Here’s a concise guide:
Regular Training: Ensure all operators undergo regular safety training sessions, focusing on the operation of furnaces, emergency procedures, and the proper use of personal protective equipment (PPE).
Maintenance and Inspections: Implement a strict schedule for regular maintenance and inspections of the furnace and related equipment to identify and fix potential hazards promptly.
PPE Compliance: Enforce strict adherence to using appropriate personal protective equipment including heat-resistant gloves, face shields, and safety glasses.
Emergency Preparedness: Develop and regularly update an emergency action plan, ensuring all employees know how to respond in case of an incident, including fires or chemical exposures.
Safety Signage: Place clear and visible safety signs around the furnace area to warn of potential hazards and remind workers of safety practices.
Risk Assessment: Conduct periodic risk assessments to identify new hazards or reassess the potential risks associated with the furnace operation, adjusting safety protocols as necessary.
By focusing on these areas, you can significantly improve safety protocols for furnace operators, creating a safer working environment.
How to Display Safety Protocols Skills on Your Resume
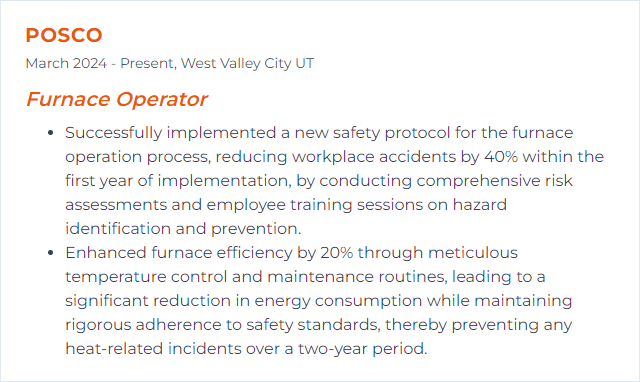
4. Preventive Maintenance
Preventive maintenance for a furnace operator involves regularly scheduled inspections, cleaning, and servicing of the furnace system to ensure it operates efficiently, prevent unexpected breakdowns, and extend its lifespan.
Why It's Important
Preventive maintenance is crucial for a furnace operator as it ensures the furnace runs efficiently, reduces the likelihood of unexpected breakdowns, extends the equipment's lifespan, and ensures a safe operating environment by preventing hazardous situations.
How to Improve Preventive Maintenance Skills
To improve preventive maintenance, especially for a Furnace Operator, focus on these key strategies:
Regular Inspections: Schedule and perform regular inspections to identify wear and potential issues before they escalate. Detailed checklists tailored to specific furnace components can guide these inspections.
Predictive Maintenance Tools: Invest in predictive maintenance technologies such as thermal imaging and vibration analysis to detect anomalies early.
Maintenance Training: Ensure operators and maintenance staff receive ongoing training in both the operation of the furnace and the latest maintenance techniques.
Cleaning Protocols: Implement thorough cleaning schedules to prevent buildup that can affect furnace efficiency and longevity. Regular cleaning of critical components can prevent unexpected failures.
Spare Parts Inventory: Maintain a well-organized inventory of essential spare parts to minimize downtime during repairs. Effective inventory management ensures parts are available when needed.
Maintenance Software: Utilize CMMS (Computerized Maintenance Management System) software to schedule, track, and analyze maintenance activities efficiently.
By integrating these strategies into your preventive maintenance plan, you can enhance furnace reliability, safety, and operational efficiency.
How to Display Preventive Maintenance Skills on Your Resume
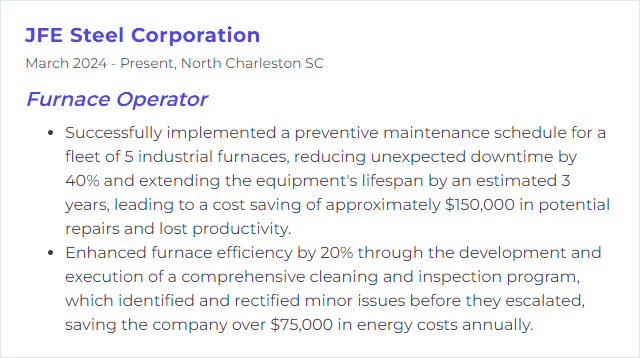
5. Troubleshooting
Troubleshooting, in the context of a Furnace Operator, involves systematically diagnosing and resolving operational problems with the furnace to ensure it runs efficiently and safely.
Why It's Important
Troubleshooting is crucial for a Furnace Operator because it enables quick identification and resolution of issues, ensuring efficient, safe operation and minimizing downtime and production losses.
How to Improve Troubleshooting Skills
Improving troubleshooting skills as a Furnace Operator involves a systematic approach to diagnosing and resolving issues effectively. Here's a concise guide:
Understand Your Equipment: Familiarize yourself with the furnace's operating manual and specifications. This guide offers insights into furnace basics and repairs.
Identify Common Issues: Recognize common problems specific to furnaces, such as ignition failure or thermostat issues. This resource outlines common furnace problems and solutions.
Use Diagnostic Tools: Employ diagnostic tools and techniques to pinpoint issues. Thermometers, multimeters, and inspection cameras can be invaluable. Learn more about diagnostic tools here.
Follow a Logical Process: Approach troubleshooting methodically, starting from the most likely and simplest issues to more complex ones. The 5-Step Troubleshooting Approach by Fluke outlines a systematic process.
Consult Resources: Utilize manufacturer's resources, online forums, and troubleshooting guides for specific issues. Websites like HVAC-Talk can provide community support and advice.
Continuous Learning: Stay updated on new technologies, tools, and troubleshooting techniques through online courses and industry publications. Coursera and edX offer relevant courses in equipment maintenance and repair.
By following these steps and continually seeking knowledge, you can enhance your troubleshooting skills as a Furnace Operator.
How to Display Troubleshooting Skills on Your Resume
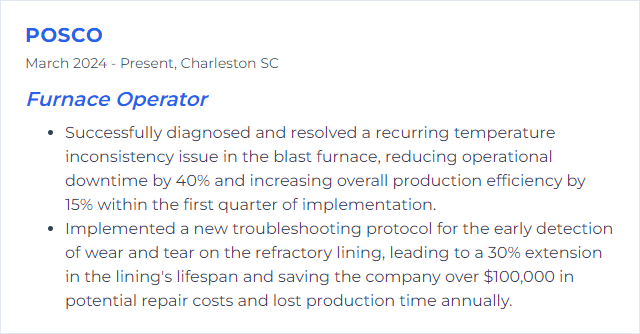
6. Efficiency Optimization
Efficiency Optimization, in the context of a Furnace Operator, involves adjusting operating conditions and processes to maximize output quality and quantity while minimizing energy consumption and waste, ensuring the furnace operates at its highest possible efficiency.
Why It's Important
Efficiency optimization is crucial for a Furnace Operator because it ensures the maximum output with minimal energy consumption and waste, reducing operating costs and increasing productivity while also minimizing environmental impact.
How to Improve Efficiency Optimization Skills
To improve efficiency optimization for a furnace operator, focus on the following steps:
Monitor and Control Heat Loss: Minimize heat loss by ensuring proper insulation and sealing leaks. Use thermal imaging to identify problem areas. Energy.gov on Heat Loss
Optimize Load Management: Ensure the furnace is loaded to its optimal capacity to maximize efficiency. Proper load distribution can significantly reduce energy consumption. Industrial Heating on Load Management
Regular Maintenance: Conduct routine maintenance to keep the furnace running efficiently. Clean components, check for wear, and replace parts as necessary. The Fabricator on Furnace Maintenance
Upgrade Equipment: Invest in modern, more efficient furnace models or retrofit existing furnaces with energy-efficient features. Plant Engineering on Furnace Efficiency
Train Operators: Ensure furnace operators are trained in best practices for energy efficiency. Knowledgeable operators can make adjustments to improve performance. HarbisonWalker International on Training
By focusing on these areas, furnace operators can significantly improve efficiency and reduce operational costs.
How to Display Efficiency Optimization Skills on Your Resume
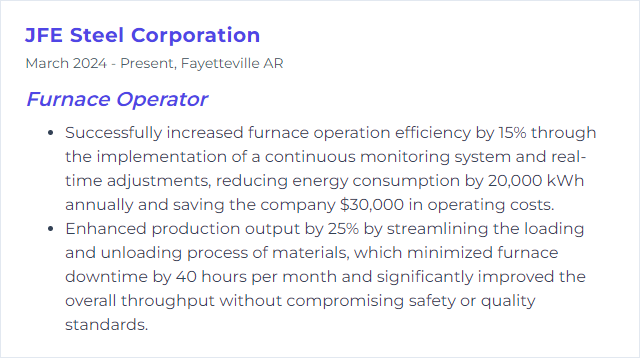
7. Continuous Monitoring
Continuous Monitoring, in the context of a Furnace Operator, refers to the ongoing process of collecting and analyzing data related to furnace performance, temperature, emissions, and other operational metrics in real-time to ensure optimal functioning, safety, and compliance with regulations.
Why It's Important
Continuous monitoring is crucial for a Furnace Operator to ensure the furnace operates within safe and optimal parameters, preventing equipment failure, enhancing efficiency, and ensuring product quality while also safeguarding worker safety.
How to Improve Continuous Monitoring Skills
To improve Continuous Monitoring for a Furnace Operator, focus on the following key strategies:
Implement Advanced Sensors: Equip the furnace with high-quality sensors for real-time monitoring of temperature, pressure, and other critical parameters. Honeywell offers a range of sensors suitable for various industrial applications.
Adopt IoT Solutions: Utilize Internet of Things (IoT) technology to remotely monitor and control furnace operations. Siemens provides comprehensive IoT solutions for industrial applications.
Use Predictive Maintenance Software: Leverage software that can predict equipment failures before they happen, based on data analytics. IBM Maximo offers predictive maintenance capabilities.
Regular Training for Operators: Ensure furnace operators are regularly trained on the latest monitoring techniques and technologies. Lincoln Electric offers training and education for operators.
Establish a Continuous Improvement Program: Implement a program that encourages ongoing evaluation and improvement of monitoring practices. Lean methodologies, available for study through resources like Lean Enterprise Institute, can provide a framework.
By focusing on these strategies, you can enhance the effectiveness of continuous monitoring for furnace operations, leading to increased efficiency, safety, and product quality.
How to Display Continuous Monitoring Skills on Your Resume
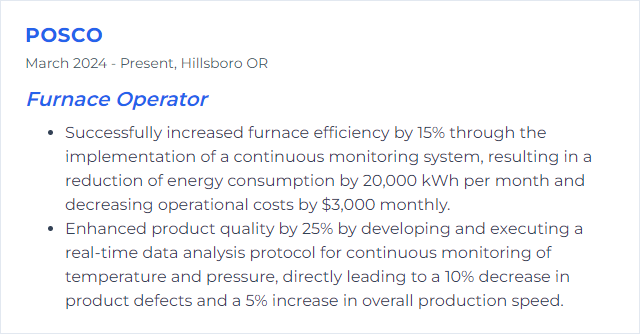
8. Waste Reduction
Waste reduction for a Furnace Operator involves minimizing the amount of waste generated during furnace operations by optimizing material usage, enhancing efficiency, and recycling or reusing materials whenever possible to minimize environmental impact.
Why It's Important
Waste reduction is critical for a Furnace Operator as it conserves resources, reduces production costs, minimizes environmental impact, and improves efficiency and sustainability of operations.
How to Improve Waste Reduction Skills
Improving waste reduction for a Furnace Operator involves several strategies focused on efficiency, recycling, and process optimization. Here's a concise guide:
Optimize Furnace Efficiency: Ensure the furnace operates at optimal conditions to reduce waste. Regular maintenance and calibration can minimize excess use of materials and energy. Energy Star Guidelines offer insights on efficiency practices.
Material Recycling: Implement a recycling program for waste materials. Metals and other materials can often be recycled to reduce waste. The EPA provides resources on recycling programs.
Process Optimization: Review and optimize the manufacturing process to minimize waste. Lean manufacturing principles can be applied to reduce excess material use and improve process efficiencies. Lean Enterprise Institute has resources on lean manufacturing.
Employee Training: Educate employees on waste reduction techniques and the importance of minimizing waste. Proper training can lead to more efficient operations and waste handling. OSHA offers training resources that can be adapted for waste reduction education.
Waste Segregation: Segregate waste materials to facilitate recycling and reduce contamination. This simplifies recycling processes and improves waste management efficiency. Waste Wise Products discusses the importance of waste segregation.
By focusing on these areas, a Furnace Operator can significantly contribute to waste reduction efforts, promoting sustainability and operational efficiency.
How to Display Waste Reduction Skills on Your Resume
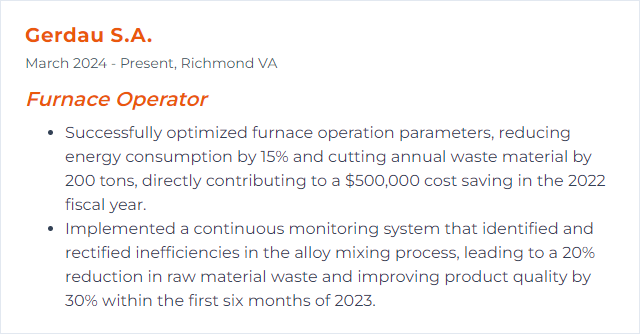
9. Process Improvement
Process improvement, in the context of a Furnace Operator, refers to the systematic approach to enhancing the efficiency and effectiveness of the furnace operation processes, aiming to reduce waste, improve product quality, and increase productivity and safety.
Why It's Important
Process improvement is essential for a Furnace Operator because it enhances efficiency, reduces waste, improves product quality, and ensures safer operations, leading to increased productivity and cost savings.
How to Improve Process Improvement Skills
To improve process improvement for a Furnace Operator, focus on these key steps:
Data Collection and Analysis: Continuously record and analyze furnace operation data to identify inefficiencies. Use tools like SPC (Statistical Process Control) to monitor and improve quality.
Employee Training: Enhance skills and knowledge through ongoing training programs. Well-trained operators can identify and rectify issues more efficiently.
Maintenance Optimization: Implement a predictive maintenance strategy to prevent unexpected downtime, ensuring equipment is always in optimal condition.
Lean Manufacturing: Adopt lean manufacturing principles to minimize waste and improve efficiency in the furnace operation process.
Technology Upgrade: Invest in modern technologies, such as IoT (Internet of Things) for real-time monitoring and control, to enhance furnace efficiency and product quality.
By focusing on these areas, Furnace Operators can significantly improve their process improvement efforts.
How to Display Process Improvement Skills on Your Resume
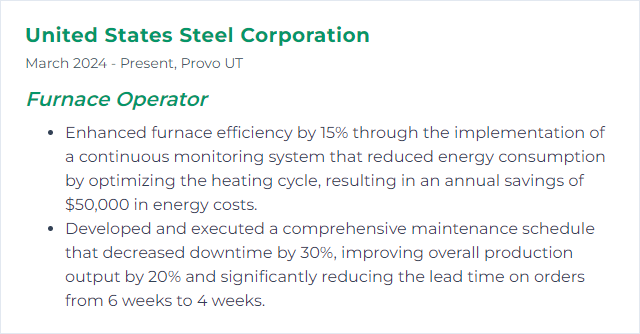
10. Equipment Calibration
Equipment calibration for a Furnace Operator involves the process of adjusting and verifying the accuracy of the furnace's temperature controls and measurement instruments to ensure they produce precise and consistent results according to specified standards.
Why It's Important
Equipment calibration ensures that a furnace operates within specified parameters, guaranteeing accurate temperature readings and uniform heat distribution. This is crucial for achieving consistent product quality, complying with safety standards, and optimizing energy use.
How to Improve Equipment Calibration Skills
Improving equipment calibration, especially for a Furnace Operator, involves a few key steps focused on accuracy, consistency, and ensuring optimal performance:
Regular Calibration Schedule: Establish a routine calibration schedule based on the manufacturer's recommendations and industry standards. This ensures the furnace operates within specified tolerances.
Use Certified Standards: Employ certified reference materials (CRMs) for calibration, ensuring the accuracy of the calibration process.
Professional Calibration Services: Engage professional calibration services for complex instruments, ensuring adherence to national and international standards.
Training: Ensure operators are trained in calibration procedures and understand the importance of maintaining equipment within specification.
Documentation and Review: Maintain detailed records of all calibrations and review them regularly to identify trends or recurring issues that may indicate a need for equipment maintenance or replacement.
Environmental Conditions: Monitor and control the environmental conditions (temperature, humidity) in the calibration area, as they can affect the accuracy of calibration.
Calibration Software: Utilize calibration management software to track schedules, manage records, and ensure timely execution of calibration tasks.
By focusing on these areas, a Furnace Operator can significantly improve the accuracy, reliability, and efficiency of equipment calibration.
How to Display Equipment Calibration Skills on Your Resume
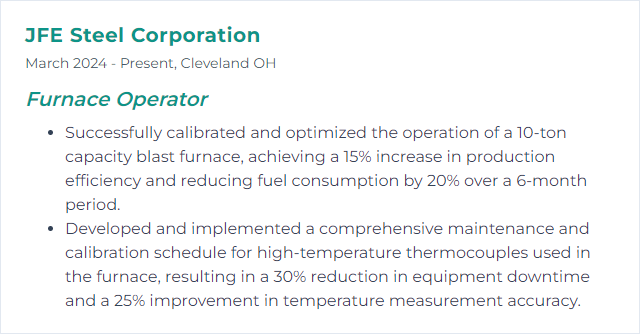
11. Production Scheduling
Production scheduling is the process of planning and organizing the sequence and timing of production tasks, specifically for a furnace operator, it involves determining the order, start times, and duration of furnace operations to optimize efficiency, meet deadlines, and ensure the timely delivery of products.
Why It's Important
Production scheduling is crucial for a Furnace Operator because it ensures the efficient and timely processing of materials, maximizes furnace utilization, minimizes downtime, and aligns production with demand, leading to cost savings and increased customer satisfaction.
How to Improve Production Scheduling Skills
Improving production scheduling, especially for a furnace operator, involves streamlining processes, enhancing communication, and leveraging technology. Here's a concise guide:
Implement Lean Manufacturing Principles: Focus on reducing waste within the manufacturing process. Lean Manufacturing can help in identifying areas of improvement in your scheduling.
Use Advanced Scheduling Software: Adopt scheduling software that can handle complex variables and constraints specific to furnace operations. Software like JobPack Production Scheduling can optimize furnace usage and maintenance schedules.
Optimize Load Planning: Efficiently plan your furnace loads to maximize throughput and minimize downtime. This resource offers tips on effective preparation that indirectly influences scheduling efficiency.
Enhance Communication: Implement tools and processes that improve communication between different departments. Platforms like Slack can facilitate real-time updates and adjustments to the schedule.
Continuous Improvement: Regularly review and adjust schedules based on performance data. Tools like Six Sigma can be applied to systematically improve the scheduling process.
Employee Training: Ensure all staff are well-trained on the scheduling tools and philosophies you adopt. This guide on manufacturing scheduling software from NIST is a good starting point for understanding the complexities involved.
By focusing on these areas, you can make significant improvements to your production scheduling, leading to increased efficiency and productivity in furnace operations.
How to Display Production Scheduling Skills on Your Resume
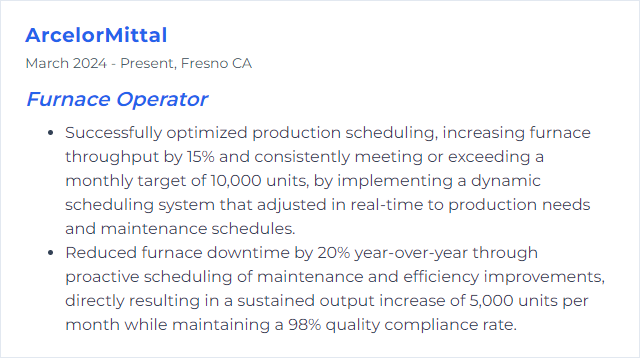
12. Inventory Management
Inventory management for a Furnace Operator involves tracking and controlling the raw materials, fuel, and replacement parts necessary for furnace operations, ensuring optimal stock levels for uninterrupted production while minimizing costs and storage space.
Why It's Important
Inventory management is crucial for a Furnace Operator to ensure the timely availability of raw materials and parts, minimize production delays, control costs, and maintain optimal stock levels for efficient operation.
How to Improve Inventory Management Skills
Improving inventory management, especially for a Furnace Operator, involves streamlining processes to enhance efficiency and accuracy. Here are concise steps:
Implement an Inventory Management System: Use software to track raw materials and finished goods in real time. QuickBooks and Fishbowl are examples that offer inventory solutions.
Regular Stock Audits: Conduct periodic checks to ensure the inventory records match the physical stock. This helps in identifying discrepancies early.
Supplier Management: Develop strong relationships with suppliers for reliable raw material sourcing. Tools like Supplier Performance Management help in evaluating and managing suppliers.
Demand Forecasting: Utilize historical data and market trends to predict future demands, thereby optimizing stock levels. Forecast Pro is a tool designed for accurate forecasting.
Lean Inventory: Adopt lean inventory principles to minimize waste and reduce excess stock without compromising on supply needs.
Continuous Improvement: Regularly review and adjust your inventory management practices based on performance analytics and changing business needs.
By integrating these steps with the specific needs of furnace operation, such as considering the shelf life of sensitive materials and the timing of supply for continuous production, you can significantly improve inventory management efficiency.
How to Display Inventory Management Skills on Your Resume
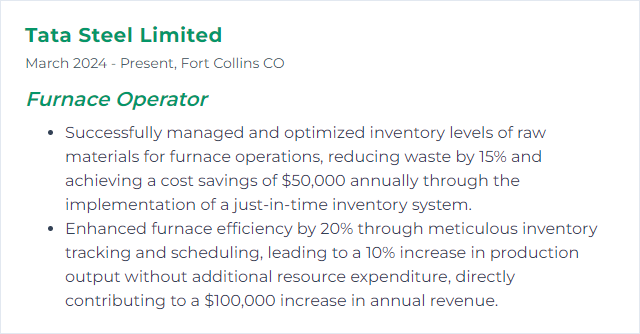