Top 12 Failure Analysis Engineer Skills to Put on Your Resume
A standout resume for a Failure Analysis Engineer requires a strategic showcase of core competencies and technical skills that highlight your ability to identify and solve complex problems. This introduction will guide you through the top 12 skills essential for demonstrating your expertise and value in this critical engineering role, ensuring your application stands out to prospective employers.
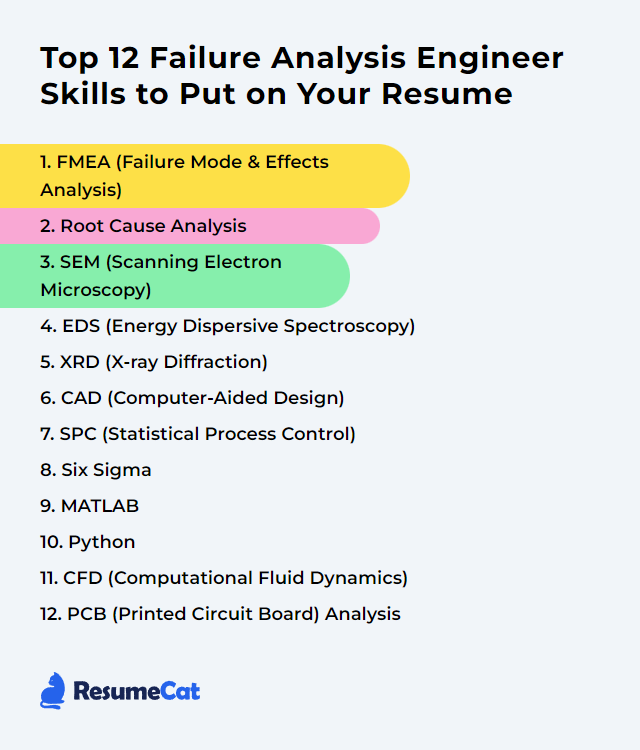
Failure Analysis Engineer Skills
- FMEA (Failure Mode and Effects Analysis)
- Root Cause Analysis
- SEM (Scanning Electron Microscopy)
- EDS (Energy Dispersive Spectroscopy)
- XRD (X-ray Diffraction)
- CAD (Computer-Aided Design)
- SPC (Statistical Process Control)
- Six Sigma
- MATLAB
- Python
- CFD (Computational Fluid Dynamics)
- PCB (Printed Circuit Board) Analysis
1. FMEA (Failure Mode and Effects Analysis)
FMEA (Failure Mode and Effects Analysis) is a systematic, step-by-step approach for identifying all possible failures in a design, manufacturing or assembly process, a product, or a service. It aims to determine the impact of different types of failures in order to prioritize which failure modes need correction or prevention. This analysis helps Failure Analysis Engineers to anticipate potential problems in the early development phase and implement solutions to mitigate risks, thus enhancing reliability and safety.
Why It's Important
FMEA is crucial for a Failure Analysis Engineer as it systematically identifies potential failure modes, assesses their impact on system performance, and prioritizes actions to mitigate risks, ensuring product reliability and safety.
How to Improve FMEA (Failure Mode and Effects Analysis) Skills
Improving FMEA involves several key steps to enhance its effectiveness and efficiency in identifying potential failures in processes or products. Here's a concise guide for a Failure Analysis Engineer:
Team Composition: Ensure the team includes members with diverse expertise relevant to the product or process being analyzed. Cross-functional collaboration is crucial for a comprehensive assessment.
Thoroughness in Failure Mode Identification: Utilize historical data, industry standards, and brainstorming sessions to exhaustively identify potential failure modes. Tools like Ishikawa diagrams can facilitate systematic exploration of root causes.
Risk Priority Number (RPN) Optimization: Accurately calculate the RPN by considering the severity, occurrence, and detectability of each failure mode. Focus on high-RPN items for prioritization but don't ignore low-RPN risks with severe consequences. The AIAG & VDA FMEA Handbook provides guidelines for effective risk assessment.
Action Plan Development and Implementation: Develop specific, actionable plans to mitigate identified risks. Assign clear responsibilities and deadlines. Utilize project management tools to track progress and ensure accountability.
Dynamic Review and Update Process: Treat FMEA as a living document. Regularly review and update the analysis to reflect changes in processes, materials, or the operational environment. Continuous improvement tools like Plan-Do-Check-Act (PDCA) can guide this iterative process.
Leverage Software Tools: Utilize FMEA software tools for efficient data management, analysis, and documentation. This enhances collaboration and provides a centralized repository for historical FMEA data. Examples include ReliaSoft XFMEA and APIS IQ-Software.
Training and Competency Development: Invest in ongoing training for team members on FMEA methodology, tools, and best practices. ASQ FMEA training offers resources for skill enhancement.
By focusing on these areas, a Failure Analysis Engineer can significantly improve the effectiveness of FMEA, leading to more reliable and safe products and processes.
How to Display FMEA (Failure Mode and Effects Analysis) Skills on Your Resume
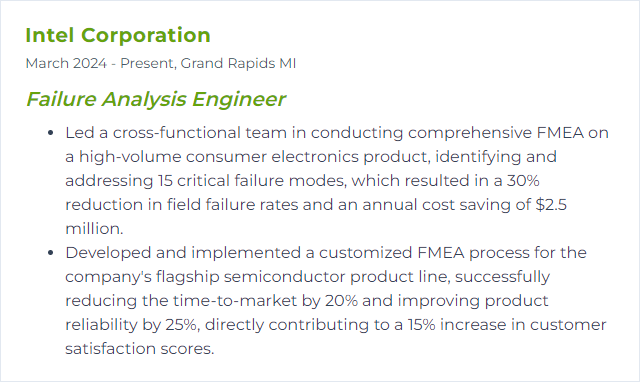
2. Root Cause Analysis
Root Cause Analysis (RCA) is a systematic process used by Failure Analysis Engineers to identify the underlying reasons for a fault or problem in order to implement effective solutions that prevent recurrence.
Why It's Important
Root Cause Analysis (RCA) is crucial for a Failure Analysis Engineer because it systematically identifies the underlying reasons for failures, enabling the implementation of effective solutions to prevent recurrence, enhance reliability, and improve product quality.
How to Improve Root Cause Analysis Skills
Improving Root Cause Analysis (RCA) involves a systematic approach to identify the underlying causes of failures, rather than just addressing the symptomatic issues. Here's a concise guide for a Failure Analysis Engineer:
Define the Problem Clearly: Start with a precise definition of the problem, including when and where it occurred. Use the 5 Whys technique to drill down to the root cause.
Collect Data: Gather all relevant data about the failure, including operational, maintenance, and historical records. This step is crucial for a thorough analysis.
Identify Possible Causal Factors: List all factors that could have contributed to the problem. Tools like Fishbone Diagrams (Ishikawa) can help in organizing and identifying potential causes.
Determine the Root Cause: Analyze the causal factors and use tools like Fault Tree Analysis (FTA) to identify the root cause(s).
Implement Corrective Actions: Develop a plan to address the root cause(s) and prevent recurrence. Ensure actions are specific, measurable, and time-bound.
Monitor Effectiveness: After implementing corrective actions, monitor the situation to ensure the problem is resolved and to prevent recurrence.
Document and Share Findings: Document the findings, actions taken, and outcomes. Sharing these insights can help prevent similar issues across the organization.
Continuous improvement in RCA skills requires practice, training, and the use of analytical tools. Consider further reading and professional development opportunities in areas like Six Sigma and Root Cause Analysis Training to enhance your expertise.
How to Display Root Cause Analysis Skills on Your Resume
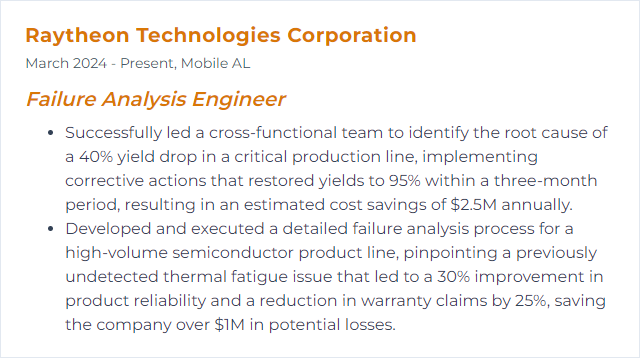
3. SEM (Scanning Electron Microscopy)
Scanning Electron Microscopy (SEM) is a powerful imaging technique used by Failure Analysis Engineers to closely examine materials for surface defects, fractures, or failures at a microscale by scanning the sample with a focused beam of electrons, producing high-resolution, three-dimensional images.
Why It's Important
SEM (Scanning Electron Microscopy) is crucial for a Failure Analysis Engineer because it provides high-resolution images of materials, enabling the detailed examination of microstructural defects, fractures, and failure points at the nanometer scale, thereby facilitating the identification of the root causes of failure and guiding the development of solutions to prevent future occurrences.
How to Improve SEM (Scanning Electron Microscopy) Skills
Improving Scanning Electron Microscopy (SEM) for Failure Analysis involves enhancing image resolution, contrast, and sample preparation techniques to better identify the root causes of material or component failure. Here are concise strategies:
Optimize Accelerating Voltage: Adjust the electron beam's accelerating voltage for the best balance between resolution and depth of field. Lower voltages improve surface details, while higher voltages offer deeper penetration. Microscopy Today provides insights on optimization.
Enhance Detector Configuration: Utilize secondary electron detectors for surface topography and backscattered electron detectors for compositional contrast. Customizing detector setup can improve material contrast. JEOL discusses advanced detector options.
Improve Sample Preparation: Proper sample preparation is crucial. For non-conductive materials, apply a conductive coating (e.g., gold or carbon) to prevent charging. For biological samples, consider cryo-SEM methods for natural state observation. ScienceDirect offers detailed sample preparation techniques.
Use Image Processing Tools: Enhance SEM images post-acquisition with software tools for better clarity and contrast. This can help in identifying microstructural features or defects more clearly. Adobe Photoshop and GIMP are popular choices for image enhancement.
Employ Advanced SEM Techniques: Explore techniques like Focused Ion Beam (FIB) for site-specific cross-sectioning or Electron Backscatter Diffraction (EBSD) for crystallographic analysis. These methods provide deeper insights into failure mechanisms. Oxford Instruments offers comprehensive guides on EBSD.
Continuous Learning: SEM technology and techniques are constantly evolving. Engage with the wider scientific community through forums, webinars, and publications to stay updated on the latest advancements. ResearchGate is a valuable platform for connecting with peers and accessing relevant research.
By focusing on these areas, a Failure Analysis Engineer can significantly enhance the capabilities and applications of SEM in identifying and understanding material failures.
How to Display SEM (Scanning Electron Microscopy) Skills on Your Resume
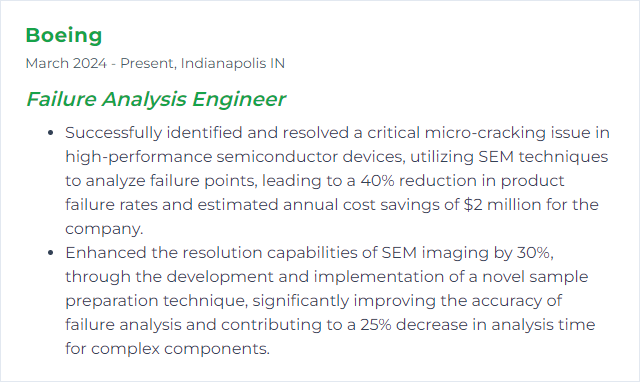
4. EDS (Energy Dispersive Spectroscopy)
Energy Dispersive Spectroscopy (EDS) is an analytical technique used for elemental analysis or chemical characterization of a sample. It relies on the interaction of electron beams with a material to induce the emission of characteristic X-rays from the sample, allowing for the identification and quantification of the elements present. In failure analysis, EDS is crucial for identifying material compositions, contaminations, or discrepancies that may contribute to the failure of a component or system.
Why It's Important
EDS is crucial for a Failure Analysis Engineer as it enables the rapid identification of elemental composition and distribution within materials, helping to uncover the root causes of failures by analyzing chemical or material discrepancies.
How to Improve EDS (Energy Dispersive Spectroscopy) Skills
Improving Energy Dispersive Spectroscopy (EDS) for Failure Analysis involves optimizing sample preparation, instrumentation settings, and data analysis techniques. Here’s how you can achieve better results:
Sample Preparation: Ensure samples are clean and properly mounted. Minimize contamination and surface irregularities to improve signal quality. Consider using ion milling for surface preparation for more accurate results (Microscopy Society of America).
Instrumentation Optimization: Utilize the latest EDS detectors with higher count rates and better energy resolution. Adjust the accelerating voltage and working distance to suit your sample for optimal spatial resolution and X-ray generation (Oxford Instruments).
Data Analysis Software: Use advanced software for spectrum processing and quantification. Software capable of artifact correction and advanced peak deconvolution improves accuracy (Bruker).
Standards and Calibration: Regularly calibrate your EDS system using known standards to ensure accuracy over time. This is critical for quantitative analysis (National Institute of Standards and Technology (NIST)).
Temperature Control: For temperature-sensitive samples, consider using cryo-techniques to preserve the sample state and reduce beam damage during analysis (Gatan).
Training and Continuous Learning: Stay updated with the latest EDS techniques and software improvements. Take advantage of webinars, workshops, and courses offered by instrument manufacturers and professional societies (Microscopy Society of America Education).
By focusing on these areas, a Failure Analysis Engineer can significantly enhance the performance of EDS for more accurate and reliable results.
How to Display EDS (Energy Dispersive Spectroscopy) Skills on Your Resume
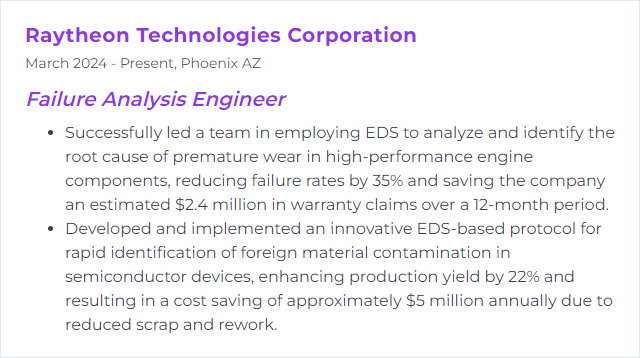
5. XRD (X-ray Diffraction)
XRD (X-ray Diffraction) is a non-destructive analytical technique used by Failure Analysis Engineers to identify the crystalline structure of materials, detect phase compositions, and analyze stress/strain in materials, helping to understand the root causes of failures in components or structures.
Why It's Important
XRD (X-ray Diffraction) is crucial for a Failure Analysis Engineer because it enables the precise identification of crystalline phases and materials' structural properties, aiding in understanding the root causes of failures by analyzing phase compositions, grain size, and residual stresses in materials.
How to Improve XRD (X-ray Diffraction) Skills
Improving X-ray Diffraction (XRD) analysis, particularly for a Failure Analysis Engineer, involves enhancing sample preparation, optimizing measurement conditions, and applying advanced data analysis techniques. Follow these concise steps to achieve more accurate and insightful XRD results:
Sample Preparation: Ensure samples are properly prepared to minimize surface irregularities and achieve representative phase composition. Meticulous preparation involves grinding, polishing, and possibly mounting the sample to obtain a flat, representative surface.
Optimization of Measurement Conditions: Adjust the XRD machine settings for optimal resolution and intensity. This includes optimizing the step size, scan speed, and incident angle. Choosing the right parameters is crucial for enhancing the quality of the diffraction pattern.
Advanced Data Analysis: Utilize sophisticated software and analytical techniques for data interpretation. Peak deconvolution, phase identification, and quantitative analysis can be improved with software like TOPAS or Jade. Implementing Rietveld refinement can also significantly enhance the accuracy of quantitative phase analysis.
Instrument Calibration and Maintenance: Regular calibration and maintenance of the XRD equipment ensure consistent and accurate results. Follow the manufacturer's guidelines and best practices for instrument care.
Continuous Learning and Training: Stay updated with the latest advancements in XRD techniques and software. Participating in workshops and training sessions can provide insights into novel methodologies and improvements in XRD analysis.
By focusing on these areas, a Failure Analysis Engineer can significantly improve the reliability and accuracy of XRD analysis, leading to better-informed decisions in failure investigation and material characterization.
How to Display XRD (X-ray Diffraction) Skills on Your Resume
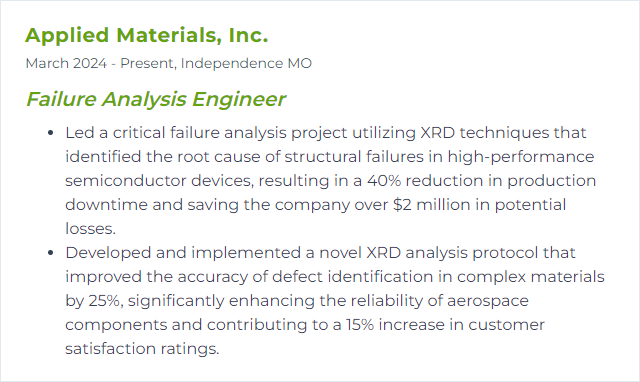
6. CAD (Computer-Aided Design)
CAD, or Computer-Aided Design, is a technology that enables Failure Analysis Engineers to create, modify, analyze, and optimize designs digitally, facilitating precision and efficiency in identifying and addressing design-related failures.
Why It's Important
CAD is crucial for a Failure Analysis Engineer as it enables precise design and simulation of components, allowing for the identification and rectification of potential failures before they occur, thereby enhancing reliability and safety.
How to Improve CAD (Computer-Aided Design) Skills
Improving your CAD skills as a Failure Analysis Engineer involves mastering software functionalities, understanding engineering principles, and integrating feedback effectively. Here are concise steps to enhance your CAD proficiency:
Learn the Fundamentals: Start with understanding the basics of your CAD software. Utilize official tutorials from your software's website (e.g., AutoCAD, SolidWorks) to grasp core functionalities.
Practice Regularly: Consistent practice is key. Engage in daily or weekly design challenges on platforms like GrabCAD to refine your skills.
Understand Material Properties: As a Failure Analysis Engineer, knowledge of material science is crucial. Apply this understanding to your designs by consulting resources from MatWeb for material properties.
Use Simulation Tools: Leverage simulation features within your CAD software to predict failure modes. Check out ANSYS for advanced simulation techniques.
Seek Feedback and Collaborate: Use platforms like Reddit’s CAD community to share your work, receive constructive criticism, and learn from peers.
Stay Updated: Follow CAD blogs and publications to stay informed about the latest trends and technologies in CAD design.
Take Advanced Courses: Enroll in specialized courses on platforms like Coursera or LinkedIn Learning to deepen your expertise in CAD and failure analysis.
By systematically applying these steps, you'll improve your CAD skills and enhance your effectiveness as a Failure Analysis Engineer.
How to Display CAD (Computer-Aided Design) Skills on Your Resume
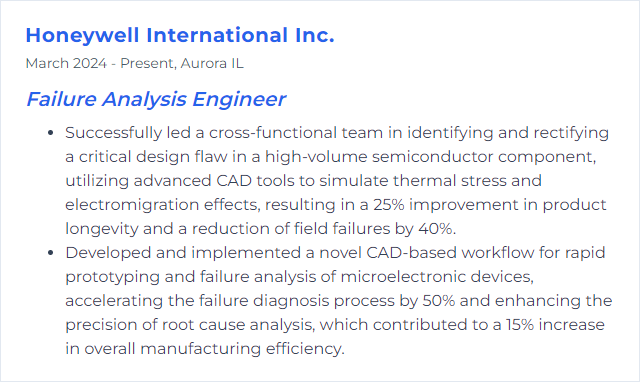
7. SPC (Statistical Process Control)
Statistical Process Control (SPC) is a method used in manufacturing to monitor, control, and improve processes through statistical analysis. For a Failure Analysis Engineer, SPC involves using statistical tools to identify and understand process variability, detect failures or defects early, and implement corrective actions to prevent recurrence, thereby enhancing product quality and reliability.
Why It's Important
SPC is crucial for a Failure Analysis Engineer because it allows for the early detection of process deviations, enabling proactive measures to prevent defects, reduce variability, and ensure product reliability and quality.
How to Improve SPC (Statistical Process Control) Skills
Improving Statistical Process Control (SPC) involves several key strategies, especially for a Failure Analysis Engineer focusing on identifying and mitigating process failures. Here's a concise guide:
Educate and Train: Ensure all team members understand SPC principles and tools. Continuous education on SPC basics and advanced techniques can enhance the team's ability to identify and respond to process variations.
Implement Real-Time Monitoring: Use real-time SPC software tools that provide immediate feedback on process performance, enabling quick reactions to potential issues.
Regularly Review Process Capability: Evaluate processes using CPK and PPK metrics to ensure they meet desired specifications and identify areas for improvement.
Utilize Root Cause Analysis (RCA): When failures occur, apply RCA techniques to systematically identify and address the underlying causes. Tools like the 5 Whys and Fishbone Diagrams can be effective.
Adopt Continuous Improvement Practices: Employ methodologies like Six Sigma and Lean to continuously seek ways to improve processes and reduce variability.
Engage in Benchmarking: Compare your processes and performance metrics with industry standards or leaders to identify areas for improvement. The American Society for Quality (ASQ) provides resources and case studies for benchmarking.
Ensure Data Quality: The foundation of effective SPC is high-quality data. Implement data governance practices to ensure data integrity.
Collaborate Across Departments: Foster communication and collaboration between departments (e.g., production, quality, engineering) to ensure a comprehensive approach to process control and improvement.
By focusing on these strategies and utilizing relevant resources, a Failure Analysis Engineer can significantly enhance the effectiveness of Statistical Process Control efforts within their organization.
How to Display SPC (Statistical Process Control) Skills on Your Resume
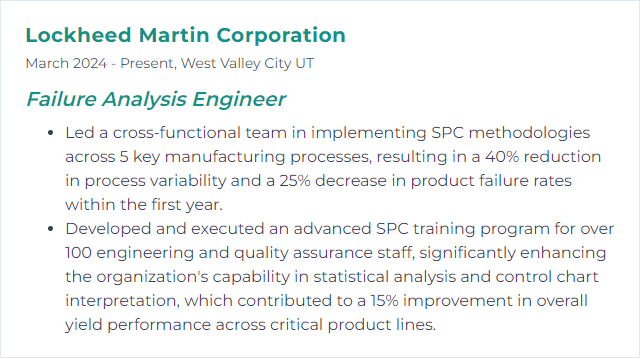
8. Six Sigma
Six Sigma is a data-driven methodology and set of techniques for process improvement, aiming to identify and eliminate defects in manufacturing and business processes, thereby improving quality, efficiency, and customer satisfaction. For a Failure Analysis Engineer, it provides a structured approach to identifying root causes of failures, optimizing processes, and reducing variability to enhance product reliability and performance.
Why It's Important
Six Sigma is important for a Failure Analysis Engineer because it provides a systematic, data-driven approach to identify, analyze, and reduce defects and variability in processes, leading to improved product quality, reliability, and customer satisfaction.
How to Improve Six Sigma Skills
Improving Six Sigma, particularly for a Failure Analysis Engineer, involves focusing on enhancing the efficiency and effectiveness of processes to minimize defects and failures. Here are concise strategies:
Enhance Data Analysis Skills: Improve your ability to analyze and interpret data to identify root causes of failures. Utilize statistical software like Minitab or JMP for deeper insights.
Engage in Continuous Learning: Keep updated with the latest Six Sigma techniques and tools. Online platforms like ASQ offer courses and certifications in Six Sigma.
Implement Automated Solutions: Use technology to automate data collection and analysis. Explore tools like MATLAB for advanced analysis and modeling.
Strengthen Root Cause Analysis: Perfect your root cause analysis techniques. Techniques like the 5 Whys or Fishbone Diagram can be crucial. More on these can be found on MindTools.
Enhance Communication Skills: Improve how you communicate findings and recommendations to stakeholders. This includes both written reports and presentations. Resources like Toastmasters International can improve public speaking and presentation skills.
Collaborate Across Departments: Work closely with other departments (e.g., manufacturing, quality assurance) to implement solutions. This ensures that improvements are practical and sustainable.
Adopt a Proactive Approach: Shift from a reactive to a proactive mindset. Focus on predicting and preventing failures before they occur, using predictive analysis tools.
Leverage Lean Six Sigma: Combine Lean principles with Six Sigma for more efficient processes. Lean Six Sigma resources are available at iSixSigma.
By focusing on these areas, a Failure Analysis Engineer can significantly improve their Six Sigma processes, leading to reduced defects, enhanced efficiency, and better overall performance.
How to Display Six Sigma Skills on Your Resume
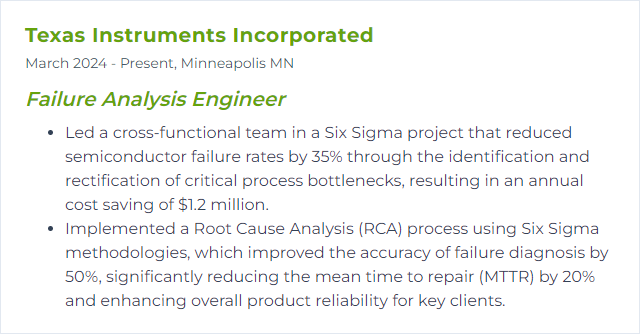
9. MATLAB
MATLAB is a high-level programming and numeric computing environment used by engineers and scientists for data analysis, algorithm development, and modeling and simulating complex systems, essential for conducting failure analysis by processing and interpreting large datasets to identify the root causes of failures.
Why It's Important
MATLAB is important for a Failure Analysis Engineer because it provides powerful data analysis and visualization tools, enabling the identification and diagnostics of failure patterns and root causes in systems and components efficiently.
How to Improve MATLAB Skills
To improve MATLAB skills for a Failure Analysis Engineer, consider the following concise steps:
Master the Basics: Start with MATLAB Onramp, a free tutorial for beginners provided by MathWorks. It covers essential MATLAB operations and functions. MATLAB Onramp
Learn MATLAB for Engineering Applications: Dive into topics specific to engineering such as signal processing, data analysis, and numerical methods through the MATLAB and Simulink Training courses. Training Courses
Practice with Real Data: Apply your skills on datasets related to failure analysis, such as equipment performance logs or material failure datasets. There are various sources for datasets, but practicing with your own data is highly beneficial.
Use MATLAB Toolboxes: Utilize specialized toolboxes for in-depth analysis. For Failure Analysis, the Statistics and Machine Learning Toolbox and the Signal Processing Toolbox are particularly useful. Statistics and Machine Learning Toolbox, Signal Processing Toolbox
Join MATLAB Central: Engage with the community on MATLAB Central. Here, you can ask questions, share code, and learn from the experiences of others in failure analysis and other fields. MATLAB Central
Stay Updated: MATLAB constantly evolves, so subscribe to the MATLAB Blog for the latest features, tips, and tricks. This will help you stay at the forefront of MATLAB’s capabilities. MATLAB Blog
By following these steps and regularly applying MATLAB to your failure analysis projects, you will enhance your proficiency and effectiveness in using MATLAB as a tool for engineering analysis.
How to Display MATLAB Skills on Your Resume
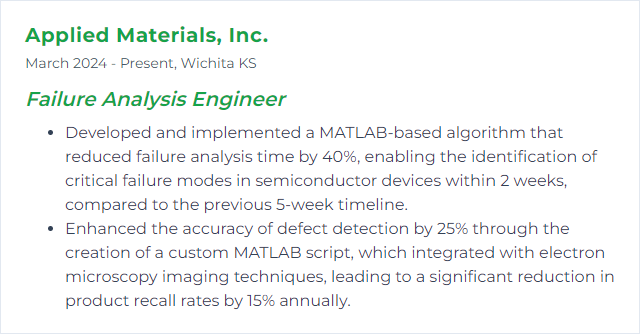
10. Python
Python is a high-level, versatile programming language known for its easy-to-read syntax, widely used in data analysis, automation, and scripting tasks, including failure analysis and engineering applications.
Why It's Important
Python is important for a Failure Analysis Engineer because it provides powerful data analysis tools and libraries (like pandas and NumPy), enabling efficient handling of large datasets, automation of failure analysis processes, and complex data visualization, which are crucial for identifying root causes and improving system reliability.
How to Improve Python Skills
Improving your Python skills, especially as a Failure Analysis Engineer, involves focusing on areas that enhance your ability to analyze, model, and solve complex problems effectively. Here are concise strategies:
Master Core Concepts: Ensure you have a solid understanding of Python basics. Python.org is an excellent place to start.
Learn Data Analysis Libraries: Focus on libraries like NumPy, pandas, and Matplotlib. They are crucial for data manipulation and visualization. Tutorials from Real Python can be quite helpful.
Understand Scientific Computing: Libraries such as SciPy (for advanced computing) and scikit-learn (for machine learning) are essential. Their respective documentation (SciPy, scikit-learn) is an excellent resource.
Practice Coding Regularly: Sites like LeetCode and HackerRank offer Python challenges that improve your coding and problem-solving skills.
Work on Real Projects: Applying your skills to real-world problems is invaluable. GitHub is a great place to find projects or contribute to open source. Explore projects on GitHub.
Stay Updated and Connect: Following Python-related blogs, attending webinars, and joining communities like Stack Overflow can provide new insights and help solve challenges you encounter.
By focusing your learning and practice on these areas, you can significantly improve your Python skills, making you more effective in your role as a Failure Analysis Engineer.
How to Display Python Skills on Your Resume
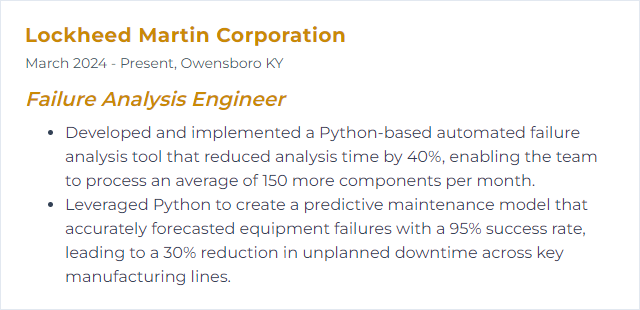
11. CFD (Computational Fluid Dynamics)
CFD (Computational Fluid Dynamics) is a branch of fluid mechanics that uses numerical analysis and algorithms to solve and analyze problems involving fluid flows. For a Failure Analysis Engineer, CFD provides a tool to simulate and understand the behavior of fluids in various conditions, helping to predict failures in systems or components due to fluid-related issues.
Why It's Important
CFD (Computational Fluid Dynamics) is crucial for a Failure Analysis Engineer as it enables precise simulation and analysis of fluid flows around or within a system, helping to predict and diagnose potential failures, optimize designs for performance and safety, and reduce the need for costly physical prototypes and experiments.
How to Improve CFD (Computational Fluid Dynamics) Skills
Improving Computational Fluid Dynamics (CFD) performance and accuracy, especially for Failure Analysis Engineers, involves several key strategies. Here’s a concise guide:
Mesh Refinement: Optimize mesh with adaptive refinement to balance accuracy and computational resources. ANSYS provides insights on choosing a meshing strategy.
Solver Selection: Choose the appropriate solver based on the flow regime and physics involved. OpenFOAM offers a variety of solvers tailored for different applications.
Validation and Verification (V&V): Regularly perform V&V against experimental or benchmark data to ensure model fidelity. The American Institute of Aeronautics and Astronautics (AIAA) outlines standards for V&V.
High-Performance Computing (HPC): Utilize HPC resources to manage large-scale simulations efficiently. Rescale offers cloud-based HPC solutions tailored for CFD.
Advanced Turbulence Models: Employ advanced turbulence models (e.g., Large Eddy Simulation (LES) or Detached Eddy Simulation (DES)) for more accurate flow predictions. CFD Online provides a comprehensive overview of turbulence modeling options.
Optimization Techniques: Implement design optimization techniques like Genetic Algorithms or Machine Learning for iterative improvement. SciPy offers optimization libraries in Python.
Software Proficiency: Stay updated with the latest CFD software enhancements and training. COMSOL and Siemens regularly offer training and updates.
Collaboration: Collaborate with cross-disciplinary teams for comprehensive analysis. Platforms like GrabCAD facilitate collaboration and sharing of CAD models.
Professional Development: Continuously update your skills through webinars, workshops, and courses. Coursera and edX offer online courses in CFD and fluid dynamics.
Regulatory Standards Compliance: Ensure compliance with industry-specific regulatory standards for model validation. ISO standards for example, provide guidelines for verification and validation in CFD.
By focusing on these areas, Failure Analysis Engineers can significantly enhance the performance, accuracy, and applicability of their CFD analyses for more reliable failure analysis and predictive maintenance strategies.
How to Display CFD (Computational Fluid Dynamics) Skills on Your Resume
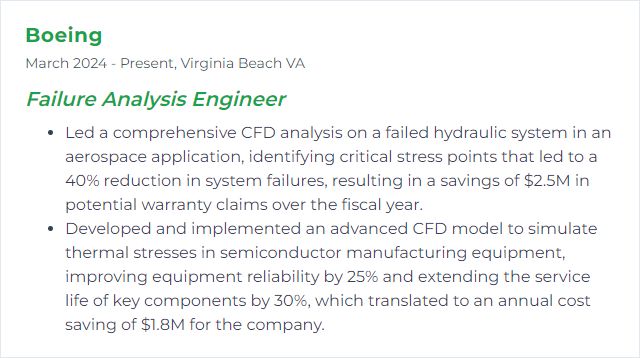
12. PCB (Printed Circuit Board) Analysis
PCB Analysis, in the context of Failure Analysis Engineering, refers to the systematic examination of a Printed Circuit Board to identify, diagnose, and understand the root causes of failures or malfunctions in electronic components or circuitry, aiming to enhance reliability and performance.
Why It's Important
PCB analysis is crucial for a Failure Analysis Engineer to identify defects or failures, understand their root causes, and implement corrective actions to enhance product reliability, safety, and performance.
How to Improve PCB (Printed Circuit Board) Analysis Skills
Improving PCB analysis involves a combination of advanced techniques, thorough knowledge, and the right tools. Here are concise steps and resources for a Failure Analysis Engineer:
Enhance Visual Inspection: Use high-quality magnification tools or Automated Optical Inspection (AOI) systems for identifying surface defects. Microscope and AOI systems offer advanced solutions.
Apply Non-Destructive Testing (NDT): Techniques like X-ray inspection provide insight into layer alignments, solder quality, and hidden components without damaging the PCB. Explore X-ray inspection technology.
Utilize Advanced Analytical Techniques: Techniques such as Scanning Electron Microscopy (SEM) with Energy Dispersive X-ray Spectroscopy (EDS) can identify material composition and detect microscopic defects. SEM-EDS Analysis can be critical.
Conduct Electrical Testing: Use in-circuit testing (ICT) and Flying Probe tests to check for electrical performance and detect shorts, opens, and wrong component values. Flying Probe Testing offers flexible and detailed analysis.
Perform Functional Testing: Simulating the operating environment of the PCB can reveal functional issues not evident in other tests. Functional Test Solutions provide a framework.
Implement Failure Mode and Effect Analysis (FMEA): Systematically evaluate potential failure modes within the design and manufacturing process to enhance reliability. FMEA Guidelines can guide the process.
Leverage Simulation Software: Early in the design process, use PCB simulation software to predict potential issues related to circuit behavior and thermal performance. Altium Designer and ANSYS Electronics are notable examples.
Engage with Continuous Education and Training: Stay updated on new technologies, materials, and processes in PCB design and analysis. IPC offers training and certification programs relevant to PCB manufacturing and analysis.
By integrating these strategies, a Failure Analysis Engineer can significantly enhance the accuracy and efficiency of PCB analysis, leading to reduced failure rates and improved product reliability.
How to Display PCB (Printed Circuit Board) Analysis Skills on Your Resume
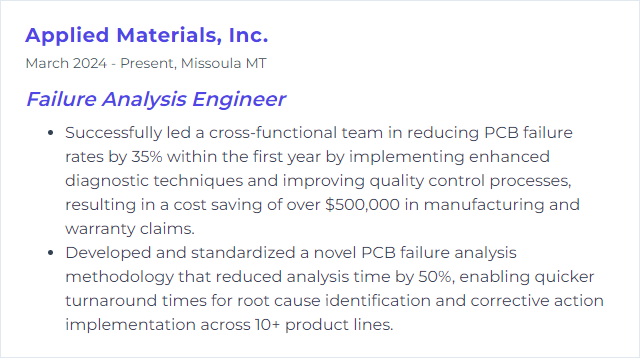