Top 12 Facility Technician Skills to Put on Your Resume
In the competitive field of facility maintenance, showcasing the right blend of technical prowess and soft skills on your resume can significantly elevate your job prospects. Highlighting a diverse set of top facility technician skills demonstrates to potential employers your comprehensive capability to manage, maintain, and ensure the smooth operation of their physical assets.
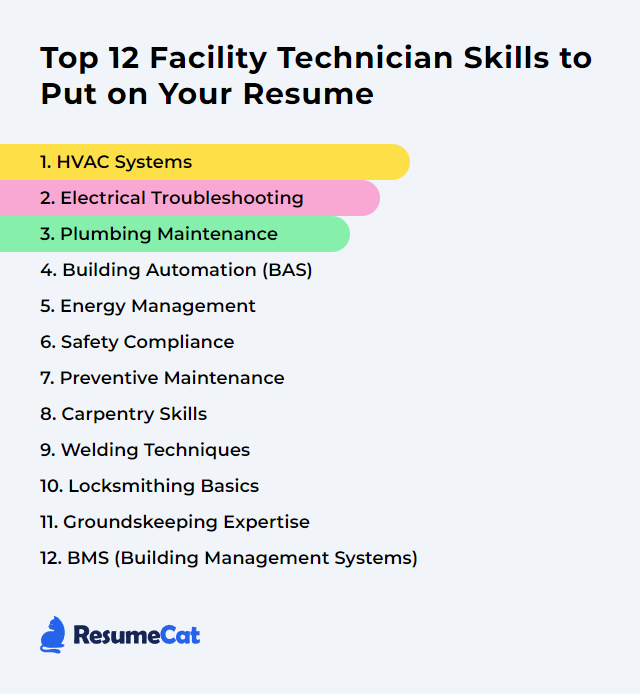
Facility Technician Skills
- HVAC Systems
- Electrical Troubleshooting
- Plumbing Maintenance
- Building Automation (BAS)
- Energy Management
- Safety Compliance
- Preventive Maintenance
- Carpentry Skills
- Welding Techniques
- Locksmithing Basics
- Groundskeeping Expertise
- BMS (Building Management Systems)
1. HVAC Systems
HVAC systems, short for Heating, Ventilation, and Air Conditioning systems, are essential in controlling the indoor climate of a building, providing comfortable temperatures, ensuring air quality, and managing humidity levels. For a Facility Technician, they involve installation, maintenance, and repair of these systems to ensure optimal operation and energy efficiency.
Why It's Important
HVAC systems are crucial for maintaining indoor air quality, ensuring comfort, and preserving the integrity of equipment and building structures by regulating temperature and humidity levels. For a Facility Technician, they are essential for ensuring operational efficiency, safety, and compliance with health standards.
How to Improve HVAC Systems Skills
Improving HVAC systems involves enhancing efficiency, reliability, and comfort while minimizing energy consumption and operational costs. Here are concise strategies for a Facility Technician:
Regular Maintenance: Perform routine inspections and maintenance to ensure the system operates at peak efficiency. This includes cleaning filters, coils, and ducts, and checking for leaks or damage. ASHRAE provides guidelines on maintenance practices.
Upgrade Systems: Replace outdated components with energy-efficient models. Consider implementing smart thermostats for better control and energy savings. Energy Star offers a list of certified products.
Improve Insulation and Air Sealing: Enhance building insulation and seal leaks to reduce heating and cooling demands. This includes windows, doors, and ductwork. The U.S. Department of Energy provides insights on effective insulation techniques.
Use HVAC Zoning: Implement zoning systems to provide independent temperature control in different areas, reducing energy waste in unoccupied spaces. ACCA (Air Conditioning Contractors of America) offers resources on zoning solutions.
Install Energy Recovery Ventilators (ERVs): ERVs improve air quality while conserving energy by recovering heat or coolness from exhaust air. The U.S. Environmental Protection Agency has resources on improving indoor air quality with ERVs.
Implement a Building Management System (BMS): A BMS can optimize HVAC operation based on real-time data, significantly reducing energy use and costs. The Building Controls Industry Association provides insights into the benefits of building automation.
Continual Education and Training: Stay updated with the latest HVAC technologies and practices through continuous learning. HVAC Excellence and RSES (Refrigeration Service Engineers Society) offer certification and training programs.
By focusing on these areas, Facility Technicians can significantly improve the performance and efficiency of HVAC systems.
How to Display HVAC Systems Skills on Your Resume
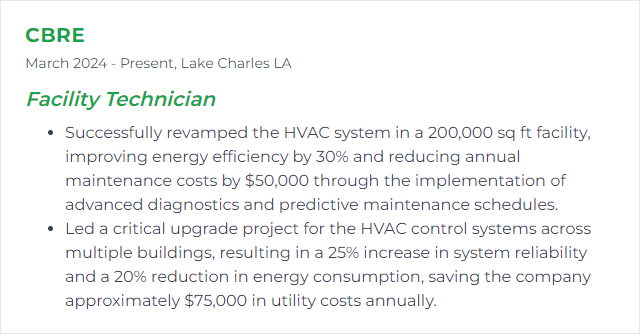
2. Electrical Troubleshooting
Electrical troubleshooting for a Facility Technician involves systematically examining and diagnosing problems within electrical systems and equipment to identify and correct faults, ensuring the safe and efficient operation of the facility.
Why It's Important
Electrical troubleshooting is crucial for a Facility Technician because it ensures the safe, efficient, and uninterrupted operation of electrical systems within the facility, preventing hazards, reducing downtime, and saving on repair costs.
How to Improve Electrical Troubleshooting Skills
Improving electrical troubleshooting skills, especially for a Facility Technician, involves a combination of theoretical knowledge and practical experience. Here’s a concise guide:
Understand Basics: Solidify your understanding of electrical fundamentals such as voltage, current, resistance, and how circuits work. Khan Academy’s Electrical Engineering courses are a great place to start.
Learn Schematics: Being able to read and interpret wiring diagrams and schematics is crucial. SparkFun’s How to Read a Schematic offers a good primer.
Use the Right Tools: Familiarize yourself with multimeters, clamp meters, and circuit finders. Understanding how and when to use them is key. Fluke’s Electrical Measurement Safety provides insights on safely using these tools.
Hands-On Practice: Nothing beats hands-on experience. Set up practice circuits or use simulators like EveryCircuit or Falstad’s Circuit Simulator to build and troubleshoot virtual circuits.
Safety First: Always prioritize safety by understanding and adhering to safety standards and practices. OSHA’s Electrical section has essential safety tips and regulations.
Keep Learning: Technology and best practices evolve. Stay updated through webinars, workshops, and courses from reputable sources like IEEE and NFPA.
Improving electrical troubleshooting skills is an ongoing process that combines learning, practice, and staying updated on the latest in electrical safety and technology.
How to Display Electrical Troubleshooting Skills on Your Resume
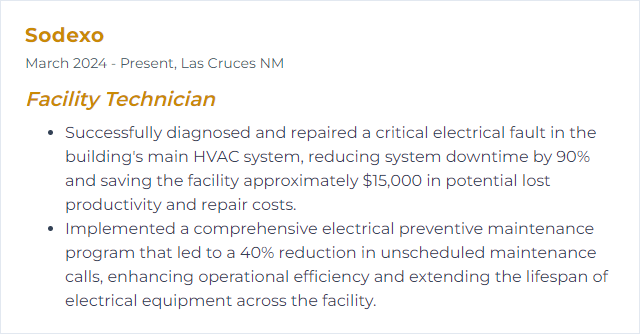
3. Plumbing Maintenance
Plumbing maintenance involves the regular inspection, cleaning, and repair of a facility's plumbing systems and fixtures to ensure their optimal operation, prevent leaks or blockages, and extend their lifespan. This includes tasks like checking pipes, drains, faucets, and water heaters for potential issues.
Why It's Important
Plumbing maintenance is crucial for a Facility Technician as it ensures the efficient operation and longevity of the plumbing system, prevents costly and disruptive leaks or blockages, and safeguards the health and safety of the building's occupants by preventing water contamination and damage.
How to Improve Plumbing Maintenance Skills
To enhance plumbing maintenance as a Facility Technician, consider these concise strategies:
Regular Inspections: Conduct routine checks to identify leaks, corrosion, or blockages early. EPA's guide on leak detection provides useful tips.
Drain Care: Use strainers and advise against disposing of grease or non-biodegradable substances down drains. This Old House offers practical drain maintenance advice.
Water Pressure Monitoring: Too high or too low water pressure can indicate issues. Home Depot's water pressure guide explains how to adjust and monitor water pressure.
Water Heater Maintenance: Annually drain and remove sediment from water heaters. Energy.gov provides a comprehensive water heater maintenance guide.
Winterization: Prevent freezing and bursting of pipes with insulation and specialized heating techniques. Here’s a useful winterization guide from Family Handyman.
Educate Users: Inform building occupants about what shouldn't go down drains and the importance of reporting leaks. The Balance Small Business outlines how to educate tenants.
By adopting these steps, Facility Technicians can significantly reduce the likelihood of plumbing issues, ensuring smoother operations and extended system lifespan.
How to Display Plumbing Maintenance Skills on Your Resume
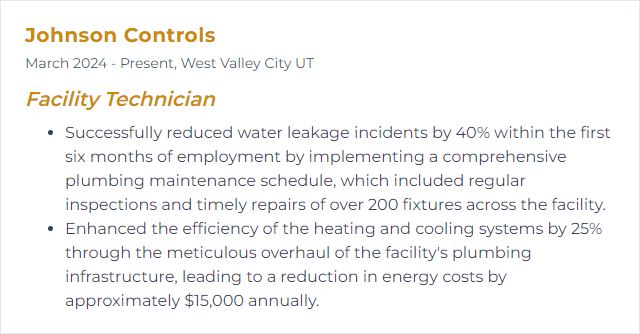
4. Building Automation (BAS)
Building Automation Systems (BAS) are centralized networks of software and hardware that control and monitor the environment, mechanical, and electrical equipment in buildings to improve efficiency, enhance occupant comfort, and reduce energy consumption. For a Facility Technician, BAS simplifies the management of HVAC, lighting, fire safety, and security systems, allowing for automated adjustments and real-time problem diagnosis to ensure optimal building performance.
Why It's Important
Building Automation Systems (BAS) are crucial for Facility Technicians as they streamline the monitoring and management of a building's mechanical and electrical systems, such as HVAC, lighting, and security. This ensures optimal operational efficiency, enhances occupants' comfort, reduces energy consumption, and simplifies maintenance tasks, allowing for quicker response to issues and preventative maintenance, thereby saving time and costs.
How to Improve Building Automation (BAS) Skills
Improving Building Automation Systems (BAS) involves enhancing efficiency, reliability, and user-friendliness. This concise guide offers actionable steps for Facility Technicians:
Upgrade Software and Firmware: Regularly update your BAS software and firmware to ensure you're utilizing the latest features and security patches. Manufacturers often provide guidance and updates, so check their official websites.
Implement Predictive Maintenance: Utilize the BAS for predictive maintenance by monitoring system performance and predicting failures before they happen. Tools like Schneider Electric’s EcoStruxure can help in predictive analysis.
Integrate IoT Devices: Enhance system capabilities by integrating IoT devices. This can improve data collection and enable more sophisticated control strategies. Learn more about IoT integration from Honeywell Building Technologies.
Improve User Training: Ensure that all users, especially facility technicians, receive thorough training on the BAS. This can significantly improve the system's efficiency and effectiveness. Many vendors offer training, such as Johnson Controls’ Training Institute.
Enhance Cybersecurity: Strengthen the cybersecurity of your BAS to protect against threats. This includes regular password updates, secure networking practices, and staying informed about potential vulnerabilities. The Cybersecurity and Infrastructure Security Agency (CISA) provides valuable resources.
Optimize Energy Management: Use BAS for energy management by monitoring energy usage and identifying areas for improvement. Software like Trane’s Energy Optics can provide insights into energy consumption.
Regular System Audits: Conduct regular audits of the BAS to ensure it is functioning as intended and to identify areas for improvement. This can involve checking for updates, evaluating system performance, and reassessing user needs.
By focusing on these areas, Facility Technicians can significantly improve the performance and utility of Building Automation Systems.
How to Display Building Automation (BAS) Skills on Your Resume
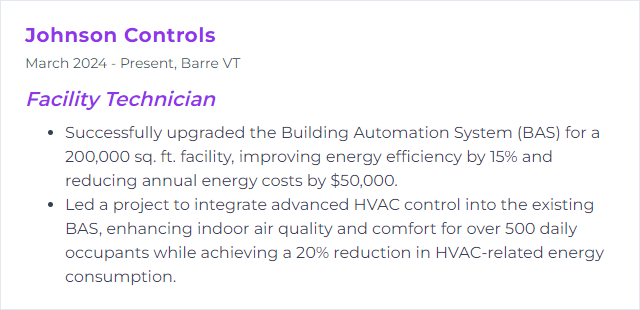
5. Energy Management
Energy management for a Facility Technician involves monitoring, controlling, and conserving energy within a building or organization to optimize usage, reduce costs, and enhance sustainability.
Why It's Important
Energy management is crucial for a Facility Technician to ensure efficient use of energy, reduce operational costs, and minimize environmental impact, thereby maintaining optimal building performance and sustainability.
How to Improve Energy Management Skills
Improving energy management as a Facility Technician involves a few key steps focused on optimizing usage, enhancing efficiency, and reducing waste. Here's a concise guide:
Audit and Monitor: Start by conducting energy audits to identify inefficiencies and areas of improvement. Use energy management systems (EMS) to continuously monitor consumption. Energy Star provides guidelines and tools for effective energy monitoring.
Implement Efficient Lighting: Transition to LED lighting and install occupancy sensors to reduce energy consumption in less-used areas. The U.S. Department of Energy offers insights on LED benefits.
HVAC Optimization: Regular maintenance of HVAC systems ensures they operate efficiently. Consider upgrading to energy-efficient models and utilize programmable thermostats. ASHRAE provides standards for energy-efficient building operations.
Renewable Energy Sources: Explore the feasibility of integrating renewable energy sources, such as solar panels, to reduce dependence on traditional power sources. The Database of State Incentives for Renewables & Efficiency® is a comprehensive resource for incentives and policies that support renewables.
Employee Engagement: Educate and engage facility occupants in energy-saving practices, such as turning off unused equipment and efficient space utilization. The ENERGY STAR Buildings and Plants tools and resources can help in planning and executing awareness campaigns.
Maintenance and Upgrades: Regularly maintain equipment to ensure it operates at peak efficiency and upgrade to energy-efficient models when possible. The U.S. Department of Energy’s Office of Energy Efficiency & Renewable Energy offers guidance on energy-efficient technologies.
Energy-Efficient Procurement: When purchasing new equipment or materials, opt for energy-efficient products. Consider products certified by ENERGY STAR or those that meet the Federal Energy Management Program standards.
Implementing these strategies will not only improve energy management within your facility but also contribute to significant cost savings and environmental benefits over time.
How to Display Energy Management Skills on Your Resume
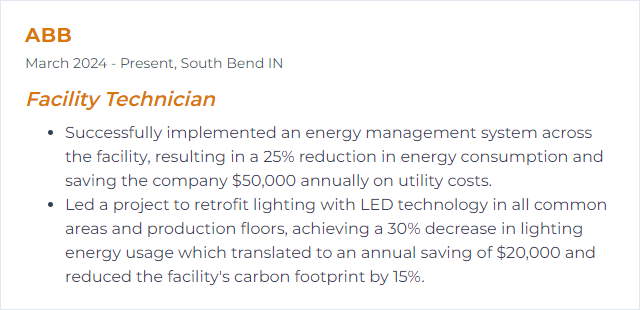
6. Safety Compliance
Safety compliance, in the context of a Facility Technician, refers to adhering to established health, safety, and environmental regulations and policies to ensure a safe and hazard-free workplace.
Why It's Important
Safety compliance is crucial for a Facility Technician as it ensures the workplace is secure, minimizes risks of accidents and injuries, and adheres to legal regulations, thereby protecting both employees and the organization from potential hazards and legal consequences.
How to Improve Safety Compliance Skills
Improving safety compliance for a Facility Technician involves a multifaceted approach focusing on training, equipment maintenance, and adherence to safety protocols.
Regular Training: Ensure all staff, especially Facility Technicians, undergo regular safety training to stay updated on the latest safety protocols and emergency response techniques.
Routine Equipment Checks: Implement a strict schedule for routine maintenance and safety checks of all equipment to prevent accidents caused by malfunctioning machinery.
Adherence to Protocols: Encourage strict adherence to safety protocols established by organizations such as OSHA or the CDC, ensuring all activities are performed within regulatory guidelines.
Safety Gear: Ensure that all Facility Technicians have access to and use the necessary personal protective equipment (PPE) appropriate for their tasks.
Incident Reporting: Establish a clear and easy-to-follow incident reporting system to quickly address and rectify any safety issues that arise.
By focusing on these key areas, a Facility Technician can significantly improve safety compliance, creating a safer working environment for everyone involved.
How to Display Safety Compliance Skills on Your Resume
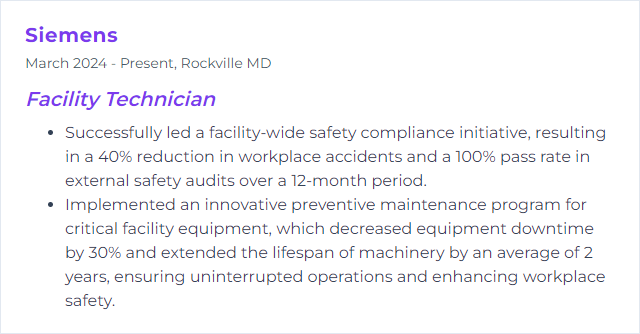
7. Preventive Maintenance
Preventive maintenance is a scheduled, routine maintenance performed on equipment, systems, or facilities by a Facility Technician to prevent potential problems, reduce the likelihood of equipment failure, and ensure optimal operational efficiency.
Why It's Important
Preventive maintenance is crucial for a Facility Technician as it ensures equipment runs efficiently, reduces unexpected breakdowns, minimizes repair costs, and prolongs asset life, ultimately supporting a safe and operational facility.
How to Improve Preventive Maintenance Skills
Improving preventive maintenance involves a strategic approach focused on efficiency, technology integration, and continuous improvement. Here’s a concise guide for a Facility Technician:
Assess and Plan: Evaluate current maintenance practices to identify areas for improvement. Develop a detailed plan that prioritizes tasks based on equipment criticality and failure impact.
Implement a CMMS: Use a Computerized Maintenance Management System (CMMS) to automate scheduling, track work orders, and store equipment history. This enhances task organization and data analysis.
Adopt Predictive Maintenance: Integrate predictive maintenance techniques using IoT sensors and analytics to monitor equipment condition in real-time. This approach helps in identifying issues before they lead to failure. Predictive Maintenance Guide provides further insights.
Standardize Procedures: Develop and implement standard operating procedures (SOPs) for maintenance tasks. This ensures consistency and efficiency in carrying out preventive measures.
Training and Skills Development: Continuously train facility technicians on the latest maintenance technologies and best practices. Facilities Net offers insights on the importance of training.
Review and Optimize: Regularly review maintenance data and feedback to identify trends, recurring issues, and areas for improvement. Adjust the preventive maintenance plan accordingly to optimize performance and reduce downtime.
By focusing on these areas, a Facility Technician can significantly improve the effectiveness of preventive maintenance within their organization.
How to Display Preventive Maintenance Skills on Your Resume
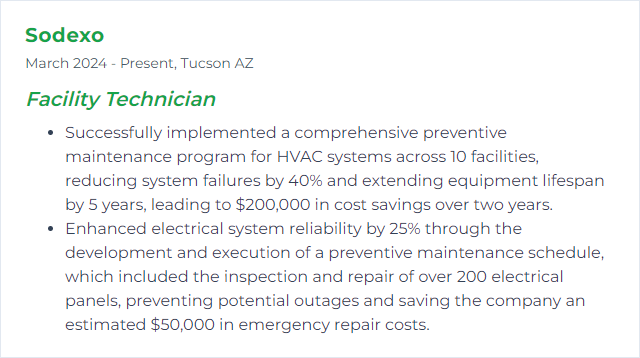
8. Carpentry Skills
Carpentry skills for a Facility Technician involve the ability to measure, cut, shape, assemble, and install building materials. This encompasses maintaining and repairing structures, fixtures, and fittings within a facility.
Why It's Important
Carpentry skills are crucial for a Facility Technician as they enable the efficient execution of repairs, maintenance, and improvements within structures, ensuring the safety, functionality, and aesthetics of facilities. These skills facilitate cost-effective, timely problem-solving and the customization of solutions to meet specific facility needs.
How to Improve Carpentry Skills Skills
Improving carpentry skills as a Facility Technician involves a mix of practice, continuous learning, and leveraging online resources. Here are concise steps to enhance your abilities:
Practice Regularly: Hands-on experience is crucial. Tackle a variety of projects to challenge and refine your skill set.
Learn from Professionals: Use platforms like YouTube for free tutorials or consider paid courses on Udemy to learn from experienced carpenters.
Understand Tools and Materials: Familiarize yourself with different tools and their maintenance. Websites like Fine Woodworking offer insights into tools and techniques.
Safety First: Always prioritize safety by following guidelines and wearing appropriate gear. Resources like OSHA provide safety standards and practices.
Join a Community: Participate in forums such as Reddit’s r/carpentry to exchange knowledge, tips, and get feedback on your work.
Read Books and Magazines: Invest in carpentry books and magazines. Libraries or online stores are good sources for publications like "The Complete Manual of Woodworking".
By integrating these steps into your routine, you'll progressively enhance your carpentry skills, contributing significantly to your effectiveness as a Facility Technician.
How to Display Carpentry Skills Skills on Your Resume
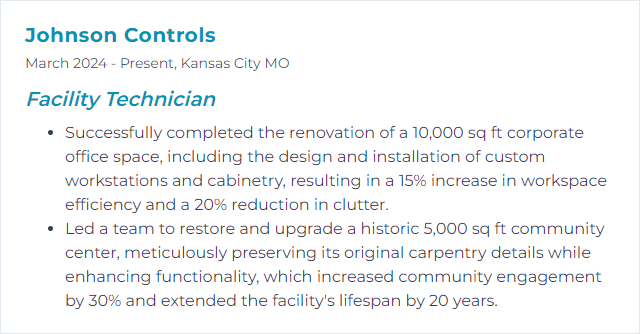
9. Welding Techniques
Welding techniques for a Facility Technician involve using specific methods to join metal parts together. Key techniques include:
MIG Welding (Metal Inert Gas): Utilizes a wire feeding gun to fuse metal pieces together. It's versatile and easy to learn, suitable for various repair and maintenance tasks.
TIG Welding (Tungsten Inert Gas): Involves using a tungsten electrode to produce the weld. It allows for greater control and precision, ideal for delicate or intricate welding jobs.
Stick Welding (Shielded Metal Arc Welding): Uses an electrode stick that melts to create the weld. It's effective for outdoor use and on dirty or rusty metals, common in many facility maintenance scenarios.
Flux-Cored Arc Welding: Similar to MIG but uses a special tubular wire filled with flux. It can be preferable for thicker materials and outdoor work due to its resistance to wind.
Each technique requires understanding of equipment setup, material preparation, and safety protocols, tailored to the specific needs of maintaining and repairing facility infrastructure.
Why It's Important
Welding techniques are crucial for a Facility Technician because they ensure the structural integrity and safety of equipment and infrastructure. Mastery of these techniques enables efficient repairs, maintenance, and fabrication, reducing downtime and extending the life of facility components.
How to Improve Welding Techniques Skills
Improving welding techniques as a Facility Technician involves both theoretical knowledge and hands-on practice. Here are concise steps with inline linking for further exploration:
Understand Welding Basics: Familiarize yourself with different welding processes, materials, and safety protocols. Miller Electric provides a comprehensive guide.
Proper Equipment Handling: Ensure you're using the right welding equipment for the job and maintaining it properly. Lincoln Electric offers insights on equipment selection and maintenance.
Practice Consistently: Regular practice helps develop steadiness, speed, and precision. Consider setting up a practice schedule.
Seek Feedback and Mentorship: Learn from experienced welders. They can provide valuable insights and tips. Join forums like WeldingWeb for community advice and mentorship opportunities.
Stay Updated with Technology: Welding technologies evolve. Familiarize yourself with the latest techniques and equipment. The Fabricator is a good resource for staying updated.
Attend Workshops and Training: Participate in workshops and further training to refine your skills and learn new techniques. Websites like American Welding Society (AWS) offer information on courses and certifications.
By focusing on these areas and leveraging the resources provided, a Facility Technician can significantly improve their welding techniques.
How to Display Welding Techniques Skills on Your Resume
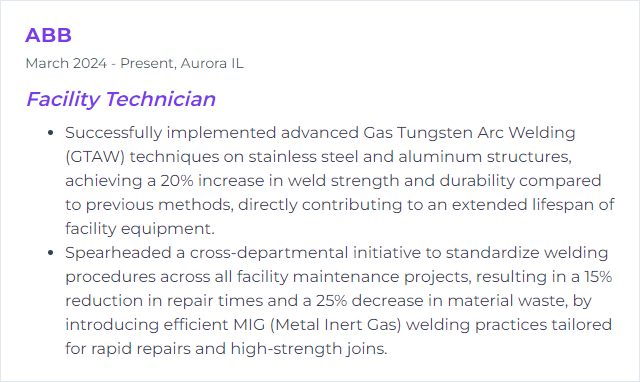
10. Locksmithing Basics
Locksmithing basics for a Facility Technician involve understanding the installation, maintenance, and repair of various types of locks and key systems. This includes mechanical and electronic locks, key duplication, rekeying, and implementing master key systems to ensure secure and efficient access control within a facility.
Why It's Important
Locksmithing basics are crucial for a Facility Technician as they ensure the ability to maintain, repair, and enhance the security of buildings. This knowledge enables the technician to address lockouts, install new locks, and manage key control systems, ultimately contributing to the safety and security of the facility and its occupants.
How to Improve Locksmithing Basics Skills
Improving your locksmithing basics as a Facility Technician involves understanding the fundamentals of locks and keys, practicing various techniques, and staying updated with the latest industry tools and technologies. Here are concise steps to enhance your locksmithing skills:
Understand Lock Mechanisms: Start by learning how different types of locks work (e.g., pin tumbler, wafer, and disc detainer locks). Master Locksmiths Association provides clear explanations of various lock mechanisms.
Practice Picking and Bypassing: Invest in a practice lock set and tools. Practice picking locks to understand their vulnerabilities. Websites like Lockpick World offer practice kits suitable for beginners to advanced users.
Key Duplication and Rekeying: Learn how to duplicate keys and rekey locks efficiently. Key Cutting Machine Guide on Locksmith Ledger offers insights into choosing and using key cutting machines.
Stay Updated with Smart Lock Technology: Familiarize yourself with the installation and troubleshooting of smart locks. ASSA ABLOY Academy provides courses on electronic access control and new lock technologies.
Join Professional Associations: Become a member of locksmithing associations such as the Associated Locksmiths of America (ALOA) to access resources, training, and certification programs.
Continuous Learning: Locksmithing technology evolves, so it's crucial to stay informed. Regularly read industry publications like The National Locksmith for the latest news and tutorials.
By following these steps and leveraging the resources provided, you can significantly improve your locksmithing basics and enhance your capabilities as a Facility Technician.
How to Display Locksmithing Basics Skills on Your Resume
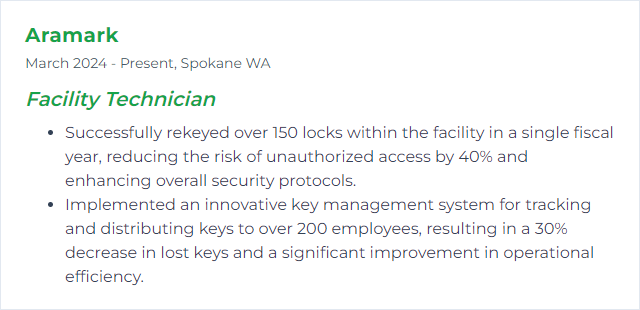
11. Groundskeeping Expertise
Groundskeeping expertise refers to the specialized knowledge and skills required for the maintenance and care of outdoor areas and landscapes at a facility. This includes tasks such as lawn care, planting, pruning, pest control, and ensuring the cleanliness and aesthetic appeal of outdoor spaces. For a Facility Technician, this expertise is crucial for maintaining a safe, functional, and visually pleasing environment.
Why It's Important
Groundskeeping expertise is crucial for a Facility Technician as it ensures the outdoor environment is safe, aesthetically pleasing, and functional. This expertise helps in maintaining the facility's value, complying with safety regulations, and enhancing the overall user experience by keeping the exterior spaces well-manicured and operational.
How to Improve Groundskeeping Expertise Skills
Improving your groundskeeping expertise as a Facility Technician involves both formal education and practical experience. Focus on the following steps:
Education: Enroll in horticulture or landscaping courses at a community college or online. Websites like Coursera and Udemy offer relevant courses that can enhance your knowledge.
Certifications: Obtain certifications like the Professional Grounds Management Society’s (PGMS) Certified Grounds Manager program for advanced knowledge and credibility.
Workshops and Seminars: Participate in workshops and seminars for hands-on experience. Organizations like the PGMS and local horticultural societies often host educational events.
Networking: Join professional networks and forums (e.g., LinkedIn groups for groundskeeping professionals) to exchange knowledge and stay updated on best practices.
Practice: Apply new techniques and innovations in your daily work. Experiment with different landscaping designs, sustainable practices, and maintenance routines to find what works best.
Feedback: Seek feedback from peers and supervisors to continuously improve your skills and address any areas for development.
By following these steps and committing to lifelong learning, you can significantly improve your groundskeeping expertise as a Facility Technician.
How to Display Groundskeeping Expertise Skills on Your Resume
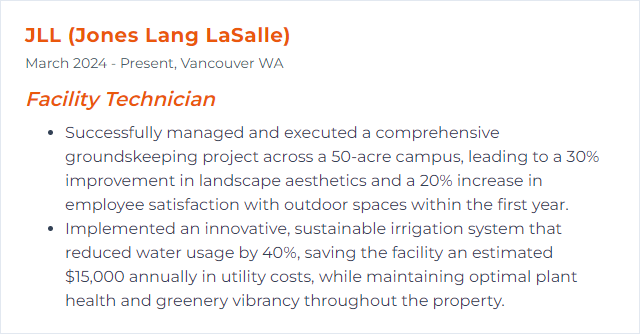
12. BMS (Building Management Systems)
BMS (Building Management Systems) is a centralized control system installed in buildings that manages and monitors the building's mechanical and electrical equipment such as ventilation, lighting, power systems, fire systems, and security systems, aiming to ensure operational efficiency, optimal performance, and comfort. For a Facility Technician, it provides a platform to supervise, adjust, and maintain the various systems within a building, enhancing the facility's overall functionality and safety.
Why It's Important
BMS is crucial for Facility Technicians as it streamlines building operations, enhances energy efficiency, ensures optimal environmental conditions, and simplifies maintenance tasks, significantly improving facility management and operational reliability.
How to Improve BMS (Building Management Systems) Skills
Improving Building Management Systems (BMS) as a Facility Technician involves focusing on optimization, integration, and continuous learning. Here are concise steps with resources for further exploration:
Optimization of System Settings: Regularly review and adjust settings for heating, ventilation, air conditioning (HVAC), lighting, and other systems for optimal performance. Energy Star's Guidelines offer a good starting point.
Integration of IoT Devices: Integrate Internet of Things (IoT) devices for smarter control and data collection. This IoT Guide for Smart Buildings by IoT Analytics provides insights.
Upgrade Software/Firmware: Ensure your BMS software and any connected device firmware are up to date. Manufacturers often release updates that improve functionality and security.
Energy Efficiency Measures: Implement energy efficiency measures such as LED lighting, energy-efficient HVAC systems, and occupancy sensors. The U.S. Department of Energy offers valuable resources.
Training and Education: Continuously educate yourself on new technologies and best practices in BMS. Websites like Building Automation Monthly offer courses and articles.
Regular System Audits and Maintenance: Perform regular audits of the BMS and connected systems to identify issues before they become problems. ASHRAE provides standards and guidance.
Leverage Analytics and AI: Use analytics and AI to predict system failures, optimize energy use, and improve occupant comfort. IBM’s insights on AI in buildings can be a helpful resource.
Implement Cybersecurity Measures: Protect your BMS from cyber threats by implementing strong cybersecurity measures. The National Cybersecurity Center of Excellence offers practical guides.
By focusing on these areas, a Facility Technician can significantly improve the efficiency, security, and functionality of a Building Management System.
How to Display BMS (Building Management Systems) Skills on Your Resume
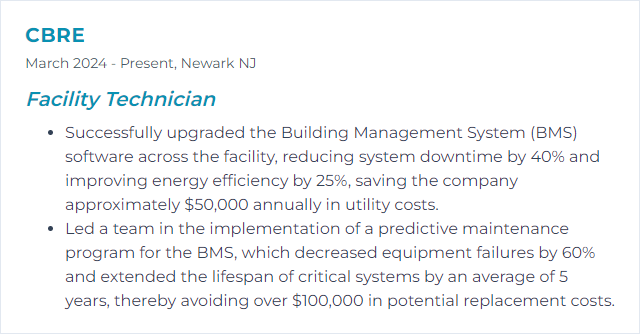