Top 12 Electronic Assembler Skills to Put on Your Resume
Crafting a standout resume as an Electronic Assembler requires showcasing a unique blend of technical prowess and precision skills. Highlighting your top skills not only demonstrates your expertise in electronic assembly but also positions you as a prime candidate in a competitive job market.
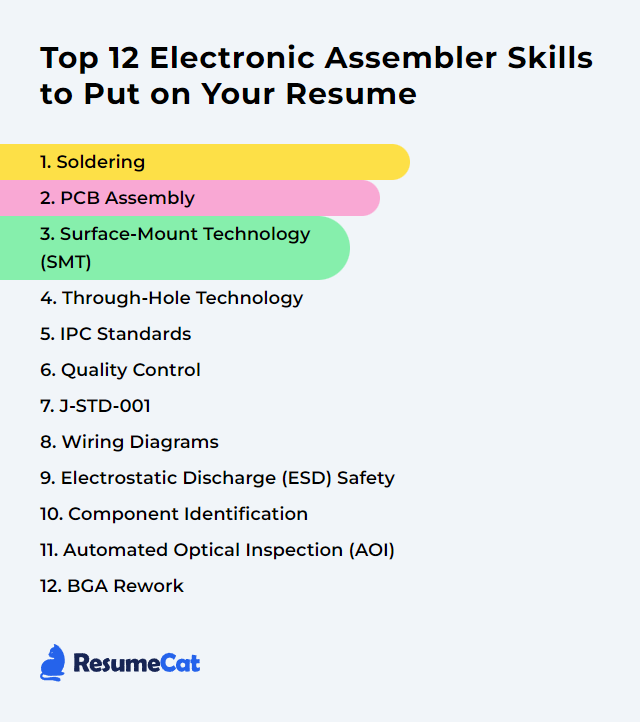
Electronic Assembler Skills
- Soldering
- PCB Assembly
- Surface-Mount Technology (SMT)
- Through-Hole Technology
- IPC Standards
- Quality Control
- J-STD-001
- Wiring Diagrams
- Electrostatic Discharge (ESD) Safety
- Component Identification
- Automated Optical Inspection (AOI)
- BGA Rework
1. Soldering
Soldering is a process used by electronic assemblers to join electronic components to a circuit board by melting and flowing a filler metal (solder) into the joint, creating a secure and conductive connection.
Why It's Important
Soldering is crucial for an Electronic Assembler as it provides a reliable and conductive connection between components, ensuring the stability and functionality of electronic circuits.
How to Improve Soldering Skills
Improving soldering skills, especially for an electronic assembler, involves practice and understanding key techniques. Here's a concise guide:
Use the Right Tools: Invest in a quality soldering iron and genuine solder. A soldering station with temperature control is ideal.
Proper Soldering Iron Care: Regularly clean and tin the tip of your soldering iron to ensure efficient heat transfer and prevent oxidation.
Correct Temperature Setting: Use the appropriate temperature for the solder and components you're working with to avoid damage.
Use Flux: Flux helps in cleaning metal surfaces and improving the flow of solder, ensuring a strong bond.
Proper Solder Placement: Apply solder to the joint, not the iron tip, allowing the component's heat to melt the solder and flow into the joint.
Practice Good Technique: Heat both the component lead and the pad simultaneously for a few seconds, then apply solder until it flows smoothly around the connection.
Inspect Your Work: Look for shiny, volcano-shaped solder joints to confirm a good connection. Avoid cold solder joints which appear dull and cracked.
Safety First: Work in a well-ventilated area or use a fume extractor to avoid inhaling fumes. Wear safety glasses to protect your eyes from splashes.
For further learning and techniques, here are some helpful resources:
- SparkFun Soldering Basics
- EEVblog Soldering Tutorial
- NASA Soldering Standards
Regular practice, along with these resources, will significantly improve your soldering skills.
How to Display Soldering Skills on Your Resume
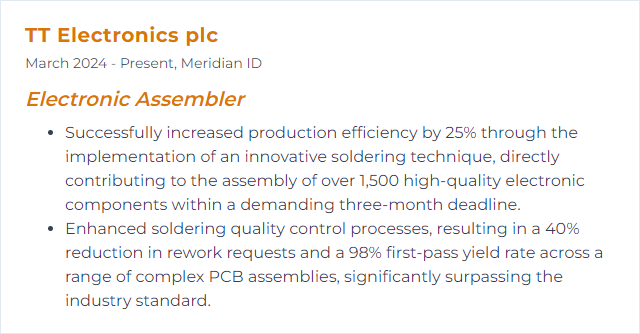
2. PCB Assembly
PCB assembly is the process of soldering or attaching electronic components to a printed circuit board (PCB) to create a functional electronic circuit.
Why It's Important
PCB Assembly is crucial as it integrates all electronic components onto the PCB, forming the backbone of all electronic devices, ensuring functionality and reliability in operation, essential for an Electronic Assembler’s work in building and maintaining modern electronic systems.
How to Improve PCB Assembly Skills
Improving PCB assembly involves enhancing both the efficiency and quality of the assembly process. Here are concise strategies for an Electronic Assembler:
Optimize Design for Manufacturability (DFM): Ensure your PCB design is optimized for assembly. Use DFM guidelines to minimize issues like complex soldering or hard-to-place components. DFM Guidelines.
Use Quality Components: Source high-quality components to reduce failures and rework. Verify suppliers and use components that meet industry standards. Component Sourcing Best Practices.
Implement Automated Solder Paste Inspection (SPI): Use SPI systems to check solder paste deposits before component placement, reducing soldering defects. SPI Importance.
Adopt Automated Optical Inspection (AOI): Integrate AOI after soldering to catch errors like misalignments or missing components, ensuring quality control. AOI Systems.
Regular Equipment Maintenance: Keep assembly equipment in optimal condition through regular maintenance to prevent downtime and ensure precision. Maintenance Tips.
Continuous Training for Assemblers: Provide ongoing training for assemblers on the latest assembly techniques and technologies to improve efficiency and reduce errors. IPC Training and Certification.
Implement Lean Manufacturing Principles: Apply lean manufacturing techniques such as just-in-time (JIT) inventory and continuous improvement processes to reduce waste and improve productivity. Lean Manufacturing in Electronics.
By focusing on these areas, an Electronic Assembler can significantly improve the efficiency, quality, and reliability of PCB assembly processes.
How to Display PCB Assembly Skills on Your Resume
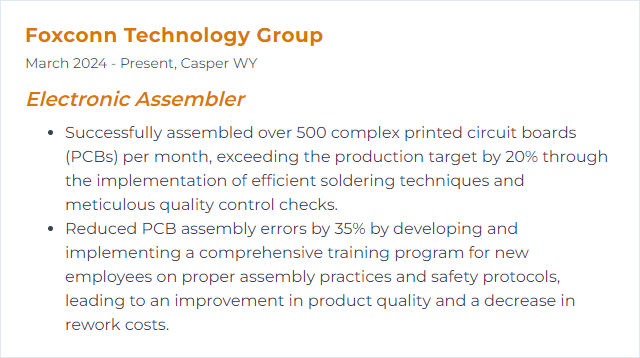
3. Surface-Mount Technology (SMT)
Surface-Mount Technology (SMT) is a method for producing electronic circuits where components are mounted directly onto the surface of printed circuit boards (PCBs), allowing for more compact, efficient assemblies compared to traditional through-hole technology.
Why It's Important
Surface-Mount Technology (SMT) is crucial for Electronic Assemblers as it allows for the efficient, automated assembly of electronic circuits with improved performance and reliability, enabling the production of smaller, more complex devices at a lower cost.
How to Improve Surface-Mount Technology (SMT) Skills
Improving Surface-Mount Technology (SMT) involves optimizing various stages of the assembly process to enhance efficiency, accuracy, and product quality. Here are concise strategies for an Electronic Assembler:
Optimize PCB Design: Use software tools for efficient PCB layout and ensure pads are correctly sized and spaced. Mentor Graphics and Altium Designer offer advanced design capabilities.
Enhance Stencil Quality: Use high-quality stencils with appropriate thickness and aperture size to improve solder paste application. ASM Assembly Systems provides stencil printing solutions.
Refine Solder Paste Printing: Optimize printer settings, including squeegee speed, pressure, and angle, to ensure consistent solder paste volume. DEK Printing Machines offers advanced printing options.
Improve Component Placement: Utilize high-precision placement machines and regularly calibrate them. Juki Automation Systems has a range of placement equipment.
Optimize Reflow Soldering: Fine-tune the reflow oven profile for even heating and cooling to reduce soldering defects. Heller Industries provides reflow soldering ovens.
Implement Automated Optical Inspection (AOI): Use AOI machines after soldering to detect and correct defects early. Koh Young Technology specializes in 3D inspection technology.
Regular Maintenance and Calibration: Ensure all equipment is regularly maintained and calibrated for optimal performance.
Continuous Training: Provide ongoing training for staff on the latest SMT techniques and technologies. IPC offers certification and training programs.
Embrace Lean Manufacturing Principles: Implement lean manufacturing techniques to minimize waste and improve workflow efficiency. Lean Enterprise Institute is a valuable resource.
Adopt Quality Management Systems (QMS): Implement a QMS, like ISO 9001, to systematically manage quality and continuous improvement. ISO provides guidelines for quality management systems.
By focusing on these areas, an Electronic Assembler can significantly improve the efficiency and quality of their SMT process.
How to Display Surface-Mount Technology (SMT) Skills on Your Resume
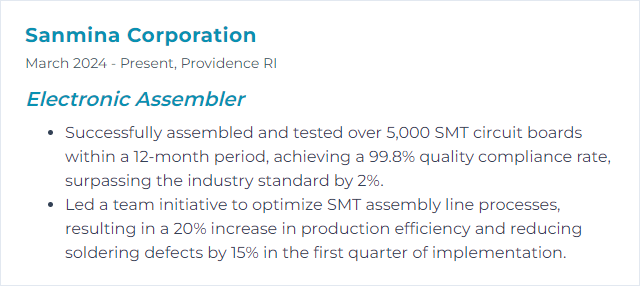
4. Through-Hole Technology
Through-Hole Technology (THT) involves mounting electronic components by inserting their leads through holes drilled in a printed circuit board (PCB) and then soldering them in place on the opposite side. This method is commonly used for components that require strong mechanical bonds or are too large for surface-mount technology.
Why It's Important
Through-Hole Technology (THT) is important for Electronic Assemblers because it allows for strong mechanical bonds between components and the PCB, making it ideal for applications requiring durability and reliability, especially in environments subject to physical stress or where manual adjustments and replacements are necessary.
How to Improve Through-Hole Technology Skills
Improving Through-Hole Technology (THT) in electronic assembly involves enhancing the efficiency and reliability of the soldering process, component placement, and inspection. Here are concise strategies:
Preparation and Planning: Ensure that PCB designs are optimized for THT with clear, accessible component locations and solder pads. Use PCB design guidelines to enhance assembly quality.
Skill Enhancement: Invest in training for assemblers to improve manual soldering techniques and understand the intricacies of THT component handling. Online courses and tutorials like those found on Coursera can be beneficial.
Equipment Upgrade: Utilize advanced soldering stations and tools that offer better temperature control and precision. Consider the equipment options at Hakko.
Quality Solder and Flux: Use high-quality solder and flux to ensure strong, reliable connections. Information on solder selection can be found on Indium Corporation’s resource page.
Automated Assistance: Where possible, incorporate semi-automated machines for component placement and soldering to reduce human error. Check Panasonic's SMT & PTH solutions for advanced options.
Inspection and Testing: Implement rigorous inspection techniques such as visual inspection, Automated Optical Inspection (AOI), and electrical testing to catch and rectify errors early. Keysight offers a range of testing equipment suitable for THT components.
Feedback Loop: Establish a feedback mechanism to learn from defects and continuously improve the THT process. This involves data collection, analysis, and adjustment of practices based on findings.
By focusing on these areas, electronic assemblers can significantly improve the quality and efficiency of Through-Hole Technology assembly processes.
How to Display Through-Hole Technology Skills on Your Resume
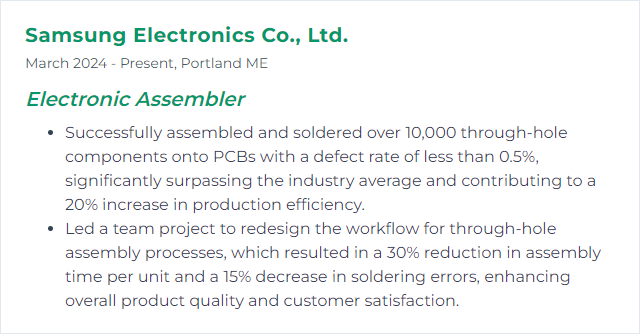
5. IPC Standards
IPC Standards for an Electronic Assembler refer to a series of globally recognized guidelines and requirements designed to ensure the reliability, quality, and consistency of electronic assemblies. They cover various aspects including soldering, assembly, and electronic component placement.
Why It's Important
IPC Standards are essential for Electronic Assemblers because they provide universally accepted guidelines on electronics manufacturing and assembly processes, ensuring quality, reliability, and consistency across products.
How to Improve IPC Standards Skills
Improving IPC Standards for an Electronic Assembler involves several key steps focusing on training, implementation, and continuous improvement. Here's a concise guide on how to enhance IPC compliance and application:
Get Certified: Enroll in IPC certification programs for electronic assemblers, such as the IPC-A-610 (Acceptability of Electronic Assemblies), to ensure a thorough understanding of standards.
Continuous Training: Regularly update your skills and knowledge through IPC's training and certification programs, to stay abreast of the latest standards and techniques.
Implement Quality Control: Establish a robust quality control process that includes regular inspections and audits based on IPC Standards. IPC's Quality Resources provide tools and guidance for maintaining high standards.
Engage in IPC Membership: Join the IPC to gain access to the latest developments, technical research, and industry networking opportunities that can help improve compliance and implementation of standards.
Feedback and Continuous Improvement: Actively participate in IPC committees or forums to provide feedback on standards. Utilize the IPC EDGE platform for continuous learning and improvement in standards application.
Use IPC Materials and Tools: Implement IPC recommended materials, tools, and software from the IPC Online Store to ensure processes and products meet IPC standards.
By following these steps and utilizing the resources provided, an Electronic Assembler can significantly improve the application and adherence to IPC Standards, leading to higher quality electronic assemblies and enhanced industry reputation.
How to Display IPC Standards Skills on Your Resume
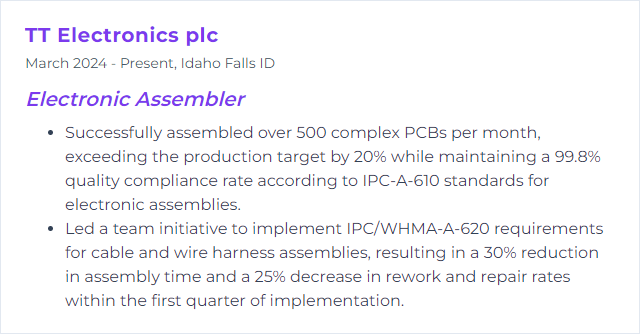
6. Quality Control
Quality Control in the context of an Electronic Assembler involves systematically inspecting and testing electronic components and assemblies to ensure they meet predefined standards of quality, functionality, and reliability before they are shipped to customers.
Why It's Important
Quality Control is essential for an Electronic Assembler to ensure the reliability and safety of electronic products, minimize defects and failures, and uphold customer satisfaction and compliance with industry standards.
How to Improve Quality Control Skills
Improving Quality Control (QC) in electronic assembly involves several targeted strategies. Here's a concise guide:
Standardize Processes: Establish and adhere to standardized processes for assembly and testing. IPC Standards provide guidelines for electronic assemblies, ensuring consistent quality.
Training: Continuously train assemblers and QC staff on the latest techniques and standards. IPC Certification programs can enhance skills and knowledge.
Automated Inspection: Implement automated inspection systems, such as Automated Optical Inspection (AOI) and X-ray inspection, to identify defects not visible to the naked eye.
Quality Management System (QMS): Adopt a QMS such as ISO 9001, which provides a framework for consistent quality in manufacturing.
Preventive Maintenance: Regular maintenance of equipment can prevent defects. This includes calibration, cleaning, and replacement of worn-out parts.
Supplier Quality Management: Ensure components sourced meet your quality standards. AS9100 certification can be a benchmark for suppliers in the aerospace sector.
Root Cause Analysis: When defects occur, use tools like 5 Whys and Fishbone Diagrams to identify and address the underlying causes.
Continuous Improvement: Embrace a culture of continuous improvement with methodologies like Six Sigma and Lean Manufacturing.
By implementing these strategies, electronic assemblers can significantly enhance their QC efforts, leading to higher product quality and customer satisfaction.
How to Display Quality Control Skills on Your Resume
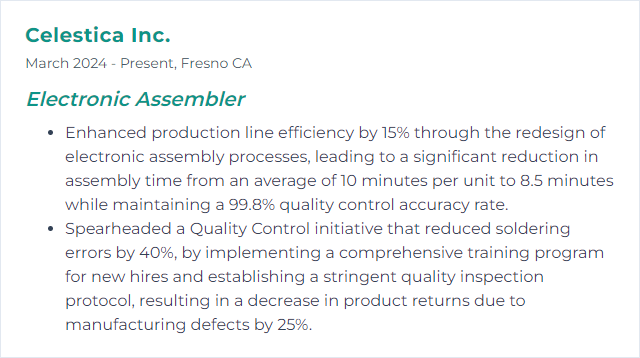
7. J-STD-001
J-STD-001, also known as the "Requirements for Soldered Electrical and Electronic Assemblies," is a widely recognized standard providing guidelines for high-quality soldering of electronic assemblies. It covers various aspects including materials, methods, and verification criteria critical for the assembly process, ensuring reliable and durable electronic products. For an Electronic Assembler, it serves as a key reference for best practices in soldering techniques and quality control.
Why It's Important
J-STD-001, known as the Requirements for Soldered Electrical and Electronic Assemblies, is crucial for Electronic Assemblers as it sets the industry standards for high-quality soldering. This ensures reliable, durable, and safe electronic assemblies by defining the best practices, materials, methods, and verification criteria across the electronics manufacturing sector.
How to Improve J-STD-001 Skills
Improving your skills and understanding of J-STD-001, which sets the standard for electronics assemblies, involves a multifaceted approach focusing on education, practice, and staying updated with industry trends. Here are concise steps to enhance your proficiency:
Education and Certification: Enroll in IPC J-STD-001 training and certification programs. These courses offer both theoretical knowledge and practical skills in electronic assemblies. IPC Certification Portal.
Practice: Apply the J-STD-001 standards in hands-on projects to reinforce learning. Regular practice helps in understanding the nuances of the standard.
Stay Updated: The standards evolve, so subscribe to IPC updates or join forums to stay informed about the latest changes. IPC Store for Latest Standards.
Use Quality Tools and Materials: Ensure you're using the right tools and materials that meet or exceed the standards set by J-STD-001.
Peer Review and Feedback: Engage in peer reviews of soldered components and assemblies to gain feedback and learn from the expertise of others.
Continual Learning: Electronics technology and standards are always advancing. Participate in webinars, workshops, and conferences to keep your knowledge current. IPC Events.
Incorporating these steps into your professional development will enhance your skills in aligning with J-STD-001 requirements.
How to Display J-STD-001 Skills on Your Resume
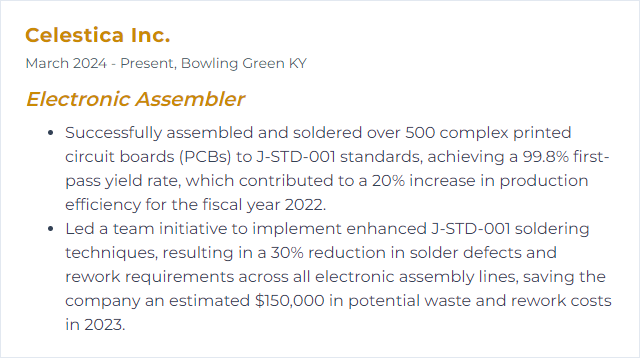
8. Wiring Diagrams
Wiring diagrams are schematic representations showing the connections and pathways for electrical or electronic components and systems, used by electronic assemblers to correctly wire and assemble electronic devices and circuitry.
Why It's Important
Wiring diagrams are essential for Electronic Assemblers as they provide a clear blueprint for accurately constructing and connecting electronic components and systems, ensuring functionality and safety.
How to Improve Wiring Diagrams Skills
To improve wiring diagrams, follow these concise steps:
Clarity: Use clear and distinct symbols for different components. Ensure each symbol is standardized across the industry (IEEE standards).
Color Coding: Apply consistent color coding for wires to indicate their purpose, making it easier to follow the circuit (Color Coding Standards).
Labeling: Clearly label all components and wires with descriptive names or numbers, linking to a detailed legend if necessary.
Signal Flow: Arrange diagrams so that the signal flow is from left to right and top to bottom for intuitive understanding.
Connections: Clearly indicate connections, junctions, and terminals, distinguishing between different types of connections (IPC Association).
Software Tools: Utilize software tools for drawing and simulating wiring diagrams to ensure accuracy and ease of editing (KiCad EDA, Autodesk Eagle).
Revision Control: Maintain a revision history for the diagram to track changes and updates over time.
By focusing on these areas, you can create more effective and user-friendly wiring diagrams.
How to Display Wiring Diagrams Skills on Your Resume
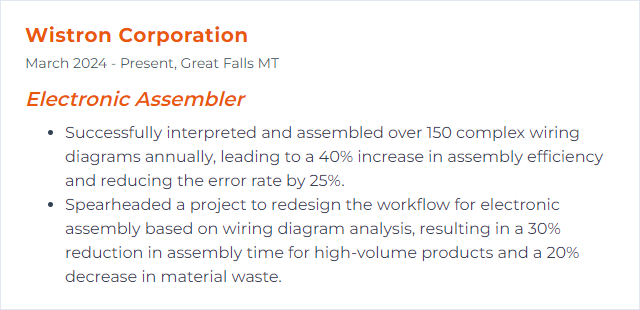
9. Electrostatic Discharge (ESD) Safety
Electrostatic Discharge (ESD) Safety in the context of an Electronic Assembler involves implementing practices and using equipment designed to prevent damage to sensitive electronic components caused by the sudden flow of electricity between two electrically charged objects. This includes grounding mats, wrist straps, and ESD-safe tools to mitigate the risk of damaging components during assembly.
Why It's Important
ESD safety is crucial for an Electronic Assembler to prevent damage to sensitive electronic components and ensure the reliability and functionality of the assembled products.
How to Improve Electrostatic Discharge (ESD) Safety Skills
Improving Electrostatic Discharge (ESD) safety for an Electronic Assembler involves several key practices:
Use of ESD-safe tools and equipment: Ensure that all tools and equipment are ESD-safe to prevent static discharge. This includes using ESD-safe soldering irons, cutters, and tweezers. ESD Association
Wear ESD protective clothing: Wear ESD-safe garments, wrist straps, and footwear to reduce the risk of static electricity generation. Desco Industries, Inc.
ESD-safe work surface: Use anti-static mats or ESD workbenches that are grounded. This provides a safe surface to work on sensitive electronic components. RS Components
Proper component handling: Always handle electronic components by their edges and avoid touching the pins or circuits directly. Use conductive bins and containers for storage. Uline
Regular auditing and testing: Conduct regular audits of your ESD control program and test your ESD equipment and work area to ensure they meet the required standards. ESD Journal
Education and training: Regularly train and educate all personnel on ESD safety protocols and the importance of following them. IPC
By implementing these strategies, an Electronic Assembler can significantly reduce the risk of ESD damage to electronic components.
How to Display Electrostatic Discharge (ESD) Safety Skills on Your Resume
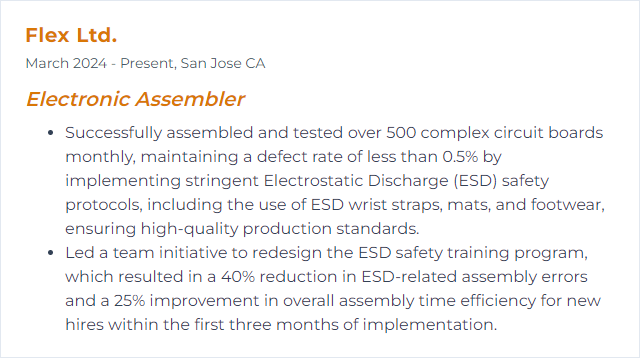
10. Component Identification
Component Identification in the context of an Electronic Assembler involves the process of recognizing and distinguishing various electronic components, such as resistors, capacitors, diodes, and integrated circuits, based on their physical characteristics, markings, and symbols, to accurately assemble and solder them onto printed circuit boards (PCBs) according to schematic diagrams.
Why It's Important
Component identification is crucial for an Electronic Assembler because it ensures the correct parts are correctly placed and soldered onto the circuit board, preventing malfunctions, increasing device reliability, and enhancing overall production quality and efficiency.
How to Improve Component Identification Skills
Improving component identification for an Electronic Assembler involves enhancing skills in recognizing various electronic components and understanding their specifications. This skill is crucial for assembling electronic devices accurately and efficiently. Here are concise tips and resources:
Learn the Basics: Understand the fundamentals of electronic components, such as resistors, capacitors, and integrated circuits. Electronics Club is a great starting point for beginners.
Use Datasheets: Datasheets provide detailed information about components. Learn how to read and interpret them. Digi-Key offers a vast repository.
Visual Recognition: Improve your ability to recognize components on sight. Electronics Hub provides images and descriptions for a variety of components.
Practice Identification: Regularly practice identifying components and their specifications. Use practice boards or kits available from suppliers like SparkFun.
Stay Updated: Electronic components evolve rapidly. Stay informed about new components and technologies by following tech news on EE Times.
Use Identification Tools: Familiarize yourself with tools like multimeters and component testers to verify components. Adafruit offers tools and guides for beginners.
By consistently applying these strategies and utilizing the provided resources, an Electronic Assembler can significantly improve their component identification skills.
How to Display Component Identification Skills on Your Resume
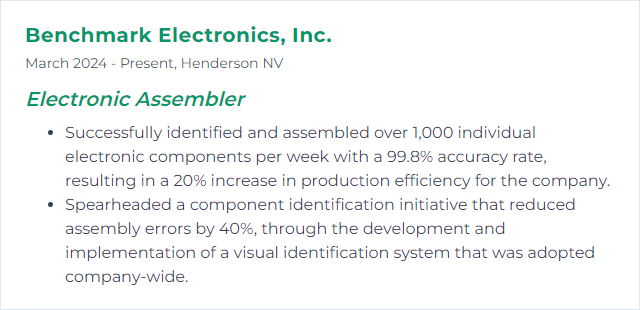
11. Automated Optical Inspection (AOI)
Automated Optical Inspection (AOI) is a visual inspection technique used in electronics manufacturing where a camera automatically scans the device under test for both catastrophic failure and quality defects. It is a crucial tool for electronic assemblers to ensure that PCBs (Printed Circuit Boards) are produced without manufacturing defects, helping to maintain high quality and reliability in electronic products.
Why It's Important
Automated Optical Inspection (AOI) is crucial for Electronic Assemblers as it enables fast and accurate inspection of electronic assemblies to detect defects like solder errors, missing components, or incorrect parts, ensuring high-quality production and reducing the likelihood of faulty products reaching customers.
How to Improve Automated Optical Inspection (AOI) Skills
Improving Automated Optical Inspection (AOI) in the context of electronic assembly involves enhancing accuracy, reducing false positives, and ensuring the system remains adaptable to various PCB designs. Here are concise strategies:
Optimize Lighting and Cameras: Adjust the lighting and camera settings to ensure clear, high-resolution images. Different PCB materials and colors may require specific lighting conditions for optimal inspection. AOI Lighting Techniques.
Regular Calibration: Regularly calibrate the AOI system to maintain precision. This involves checking the system’s ability to identify known defects and adjusting as necessary. Calibration Importance.
Update Inspection Algorithms: Continually update and refine the software algorithms to improve defect detection rates and reduce false positives. Advanced algorithms can adapt to new PCB designs more efficiently. Algorithm Improvement.
Enhance Defect Classifications: Work on better defect classification to improve the system's ability to distinguish between true defects and permissible variances. This involves training the system with a wide range of defect types. Defect Classification.
Integrate 3D Inspection: Incorporating 3D inspection alongside traditional 2D methods can improve defect detection, especially for solder quality and component placement. 3D AOI Benefits.
Operator Training: Ensure operators are well-trained in using the AOI system, interpreting its findings, and performing manual checks when necessary. Skilled operators can significantly enhance the overall efficiency of the inspection process. Operator Training Importance.
Feedback Loop: Implement a feedback loop from post-AOI processes back to the AOI settings and parameters to continuously improve detection accuracy based on real-world outcomes. Feedback Loops in Manufacturing.
By focusing on these areas, you can enhance the performance of your AOI system, leading to more reliable and efficient electronic assembly processes.
How to Display Automated Optical Inspection (AOI) Skills on Your Resume
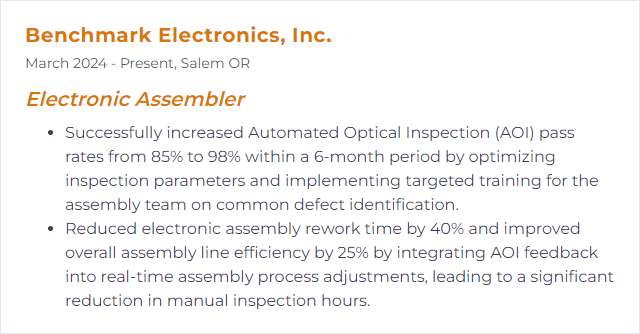
12. BGA Rework
BGA rework refers to the process of removing, reballing, and resoldering Ball Grid Array (BGA) components on a circuit board, often used by electronic assemblers to repair or replace defective chips without damaging the board or surrounding components.
Why It's Important
BGA rework is essential for electronic assemblers as it allows for the precise correction of defects in Ball Grid Array soldering, ensuring the functionality and reliability of electronic devices without the need for complete board replacement, thereby saving time and reducing costs.
How to Improve BGA Rework Skills
Improving BGA (Ball Grid Array) rework involves precision, practice, and the right tools. Here's a concise guide:
Preparation: Ensure the PCB (Printed Circuit Board) and BGA component are clean and free from any contaminants. Use isopropyl alcohol for cleaning.
Equipment Calibration: Regularly calibrate your rework station and equipment to ensure accurate temperature and airflow settings. Quick Guide on Calibration.
Proper Alignment: Use a high-quality optical system for aligning the BGA to the PCB. Precise alignment is crucial to avoid soldering faults. Alignment Techniques.
Optimized Profiles: Develop and optimize reflow profiles specific to the board and component. This includes preheat, soak, reflow, and cooling phases. Tailor the profile according to the solder paste and BGA specifications. Reflow Profiling Guidelines.
Use of Stencils: Apply solder paste with precision using a stencil designed for the specific BGA pattern. This ensures uniform solder paste volume. Stencil Printing Process.
Inspection and Testing: Post-rework inspection is critical. Use X-ray inspection to check solder joints and connections beneath the BGA. Perform functional tests to ensure the component operates correctly. X-Ray Inspection Standards.
Practice and Training: Regular practice and training are essential. Stay updated with the latest BGA rework techniques and technologies. Training and Certification Programs.
Remember, mastering BGA rework takes time and patience, but following these steps will lead to more reliable and efficient repairs and rework.
How to Display BGA Rework Skills on Your Resume
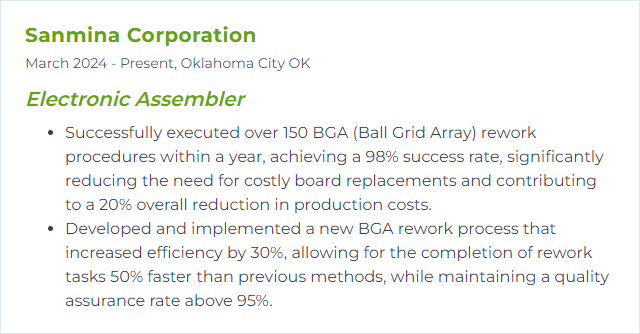