Top 12 Director Of Manufacturing Skills to Put on Your Resume
In the competitive field of manufacturing, standing out as a Director of Manufacturing requires a unique set of skills that blend technical expertise with leadership prowess. Highlighting these top skills on your resume can significantly enhance your visibility to potential employers, showcasing your ability to drive operational success and lead high-performing teams in a dynamic industry.
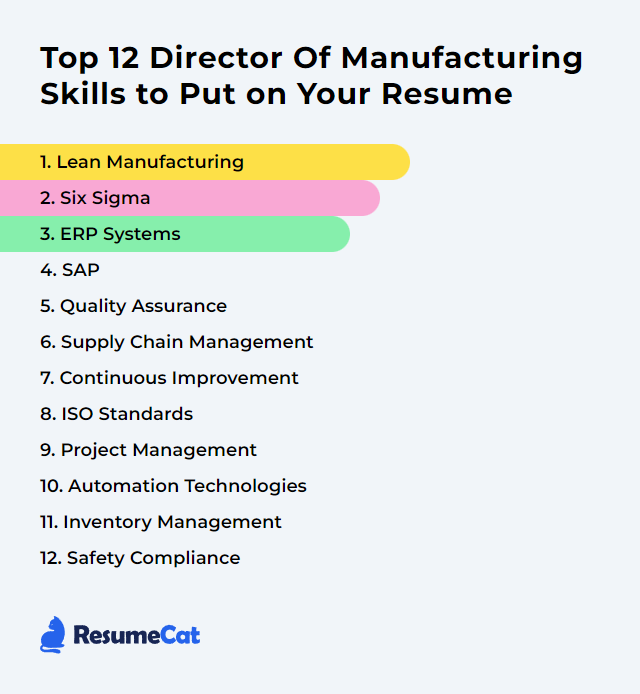
Director Of Manufacturing Skills
- Lean Manufacturing
- Six Sigma
- ERP Systems
- SAP
- Quality Assurance
- Supply Chain Management
- Continuous Improvement
- ISO Standards
- Project Management
- Automation Technologies
- Inventory Management
- Safety Compliance
1. Lean Manufacturing
Lean Manufacturing is a systematic approach aimed at minimizing waste within manufacturing systems while simultaneously maximizing productivity, designed to enhance efficiency and flexibility on the production floor, ensuring value creation for the customer at the least cost.
Why It's Important
Lean Manufacturing is crucial as it streamlines production processes, reduces waste, and increases efficiency, directly leading to higher product quality, lower costs, and improved customer satisfaction, thereby enhancing overall competitiveness and profitability for the manufacturing operation.
How to Improve Lean Manufacturing Skills
Improving Lean Manufacturing involves a strategic approach focused on eliminating waste, optimizing processes, and empowering employees. As a Director of Manufacturing, you can enhance Lean Manufacturing by:
Conducting Value Stream Mapping: Analyze and visualize your entire production process to identify waste and areas for improvement. Value Stream Mapping Guide.
Implementing 5S Methodology: Organize and maintain a clean, efficient, and safe workplace using the 5S framework (Sort, Set in order, Shine, Standardize, Sustain). This foundational step creates an environment conducive to Lean practices. 5S Guide.
Fostering a Continuous Improvement Culture: Encourage and train your team to constantly seek ways to improve processes. Lean is not a one-time project but a continuous journey towards efficiency. Kaizen Guide.
Adopting Pull Systems: Implement pull systems like Kanban to align production with demand, thereby reducing inventory and improving flow. Kanban Guide.
Utilizing Lean Tools and Techniques: Tools such as PDCA (Plan-Do-Check-Act), Root Cause Analysis, and SMED (Single-Minute Exchange of Dies) can drive process improvements. Tailor the use of these tools to your specific manufacturing environment. Lean Tools Guide.
Leveraging Technology and Automation: Smart use of technology can support Lean principles. Consider implementing IoT (Internet of Things), AI (Artificial Intelligence), and other digital tools to gather real-time data, optimize operations, and reduce errors. Industry 4.0 Guide.
Training and Empowering Employees: Invest in Lean training for your team and empower them to take ownership of improvements. Engaged and knowledgeable employees are critical for sustaining Lean initiatives. Employee Empowerment Guide.
Improving Lean Manufacturing is a strategic and continuous effort that requires commitment from all levels of the organization. By focusing on these areas, a Director of Manufacturing can significantly enhance operational efficiency and productivity.
How to Display Lean Manufacturing Skills on Your Resume
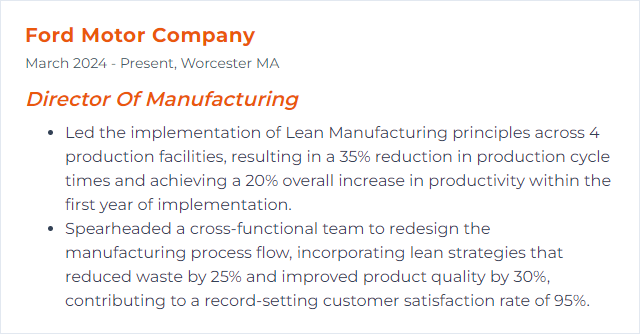
2. Six Sigma
Six Sigma is a data-driven methodology aimed at improving manufacturing processes, reducing defects, and enhancing quality and efficiency, thereby increasing customer satisfaction and organizational profitability.
Why It's Important
Six Sigma is crucial for a Director of Manufacturing as it dramatically enhances process efficiency, reduces defects to near zero, optimizes resource use, and significantly boosts product quality and customer satisfaction, leading to increased profitability and competitive advantage.
How to Improve Six Sigma Skills
Improving Six Sigma within a manufacturing environment, especially from a Director of Manufacturing perspective, involves a strategic approach focused on continuous improvement, employee empowerment, and leveraging technology. Here are concise steps:
Leadership Commitment: As a Director, demonstrate unwavering commitment to Six Sigma methodologies. Promote a culture that values quality improvement and data-driven decision-making. ASQ Leadership in Six Sigma.
Employee Training: Invest in comprehensive Six Sigma training for your team, focusing on both Yellow and Green Belt certifications, to ensure they have the necessary skills. IASSC Six Sigma Training.
Project Selection: Carefully select Six Sigma projects that align with your manufacturing goals, focusing on areas with the highest potential for improvement and impact on customer satisfaction. Choosing Six Sigma Projects.
Technology Utilization: Leverage the latest in manufacturing and statistical analysis software to enhance your Six Sigma efforts, from process simulation to data analysis tools. Minitab for Six Sigma.
Continuous Improvement Culture: Foster a culture that encourages continuous improvement and open communication. Encourage employees to identify inefficiencies and suggest improvements. Creating a Culture of Continuous Improvement.
Measure and Adjust: Regularly review the progress and impact of Six Sigma projects. Use KPIs to measure success and be willing to adjust strategies based on data-driven insights. Measuring Six Sigma Success.
By focusing on these areas, a Director of Manufacturing can significantly improve Six Sigma initiatives, driving efficiency, reducing waste, and enhancing product quality.
How to Display Six Sigma Skills on Your Resume
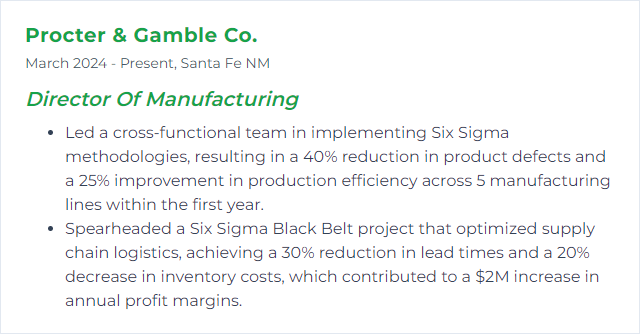
3. ERP Systems
ERP (Enterprise Resource Planning) systems are integrated software platforms that manage and synchronize a company's core business processes, such as production, supply chain, inventory, and operations, to enhance efficiency, data accuracy, and decision-making for manufacturing directors and other executives.
Why It's Important
ERP systems are crucial for a Director of Manufacturing as they integrate all facets of operations, including supply chain, production, quality control, and distribution, enabling efficient resource management, real-time data-driven decision-making, and streamlined processes, ultimately improving productivity and profitability.
How to Improve ERP Systems Skills
Improving ERP (Enterprise Resource Planning) systems, especially from the perspective of a Director of Manufacturing, involves enhancing efficiency, flexibility, and data accuracy. Here are concise strategies:
Integration and Automation: Ensure seamless integration with other systems (CRM, SCM) for real-time data sharing and automate routine tasks to reduce errors and save time. ERP Integration Guide.
Customization and Scalability: Tailor the ERP to fit specific manufacturing needs and ensure it can scale with business growth. Custom ERP Solutions.
Training and Support: Provide comprehensive training for users and continuous support to maximize system utilization. ERP Training Best Practices.
Data Analysis and Reporting: Utilize advanced data analytics for actionable insights and decision-making. Improved reporting tools for real-time monitoring of KPIs. ERP Analytics.
Mobile Accessibility: Ensure the ERP system is accessible via mobile devices for on-the-go management and decision-making. Mobile ERP Strategy.
Continuous Improvement: Regularly review and update the ERP system to adapt to new technologies and business practices. Continuous Improvement in ERP.
Implementing these strategies can significantly enhance the performance and value of ERP systems in manufacturing settings.
How to Display ERP Systems Skills on Your Resume
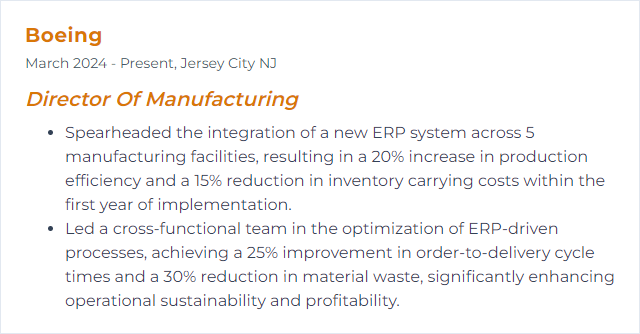
4. SAP
SAP is an enterprise resource planning (ERP) software used to manage business operations and customer relations, including manufacturing processes, supply chain, finance, and HR, to improve efficiency and decision-making.
Why It's Important
SAP streamlines and integrates core manufacturing processes, enhancing operational efficiency, providing real-time data for informed decision-making, and improving supply chain management, crucial for a Director of Manufacturing to achieve optimal production performance and profitability.
How to Improve SAP Skills
Improving your SAP (Systems, Applications, and Products in Data Processing) system involves optimizing processes, leveraging new technologies, and enhancing user experience. Here are concise steps tailored for a Director of Manufacturing:
Process Optimization: Streamline manufacturing processes by utilizing SAP's Digital Manufacturing Insights to gain real-time visibility and analytics, enabling smarter decision-making.
Technology Integration: Integrate Internet of Things (IoT) solutions to automate data collection from manufacturing equipment, improving efficiency and predictive maintenance.
User Training and Support: Invest in SAP training for your team to ensure they can fully leverage SAP capabilities, enhancing overall productivity and system adoption.
Customization and Flexibility: Work with SAP Custom Development to tailor the SAP suite to your specific manufacturing needs, ensuring the system is as relevant and beneficial as possible.
Leverage SAP S/4HANA: Transition to SAP S/4HANA for a more powerful, streamlined ERP system that supports real-time analytics and transactions, significantly improving processing times and insights.
Continuous Improvement: Regularly review and adapt your SAP system in collaboration with SAP SuccessFactors to align with evolving manufacturing goals, workforce management, and industry advancements.
By focusing on these areas, you can significantly improve your SAP system's efficiency, effectiveness, and adaptability, ensuring it supports your manufacturing operations' current and future needs.
How to Display SAP Skills on Your Resume
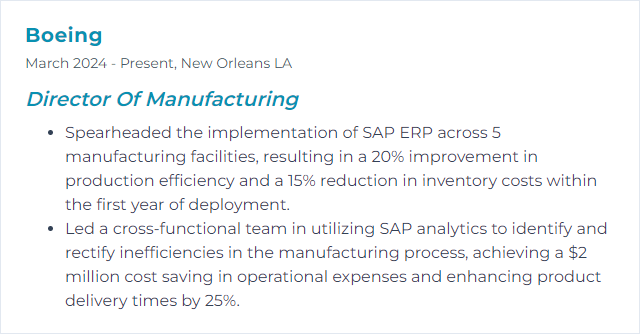
5. Quality Assurance
Quality Assurance (QA) is a systematic process designed to ensure that manufactured products meet specified quality standards and requirements, aiming to enhance customer satisfaction and comply with regulatory standards.
Why It's Important
Quality Assurance (QA) is crucial in manufacturing as it ensures product reliability, meets regulatory standards, and maintains customer satisfaction, directly impacting the company's reputation and bottom line.
How to Improve Quality Assurance Skills
Improving Quality Assurance (QA) as a Director of Manufacturing involves a strategic mix of leadership, process optimization, and leveraging technology. Here's a concise roadmap:
Leadership and Culture: Foster a culture of quality by leading by example. Encourage open communication and continuous improvement. Engage your team in quality objectives and recognize their efforts in achieving them. ASQ's guide on quality culture can offer insights.
Process Optimization: Implement Lean manufacturing and Six Sigma methodologies to streamline processes, reduce waste, and improve efficiency. Standardizing processes ensures consistency in product quality. Lean Enterprise Institute and iSixSigma provide valuable resources.
Training and Development: Invest in regular training and certification programs for your team to keep them updated with the latest QA methodologies and tools. ASQ's training programs are a good place to start.
Technology and Automation: Utilize advanced QA technologies and automation tools for more accurate and efficient quality checks. This includes AI for predictive quality and IoT for real-time monitoring. MIT Sloan Review discusses AI's impact, and IoT For All explores IoT applications in manufacturing.
Supplier Quality Management: Ensure the quality of materials and components by closely collaborating with suppliers. Implement supplier quality management systems and conduct regular audits. APQC offers best practices on supplier quality management.
Customer Feedback: Actively seek and incorporate customer feedback into your QA processes. This helps in identifying areas needing improvement and aligning product quality with customer expectations. Harvard Business Review highlights the importance of customer feedback.
Implementing these strategies requires a holistic approach, integrating people, processes, and technology towards a common goal of quality excellence.
How to Display Quality Assurance Skills on Your Resume
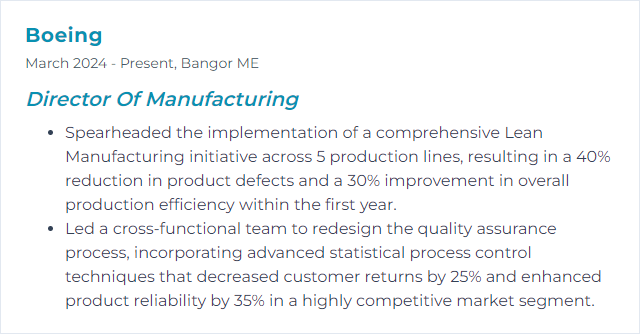
6. Supply Chain Management
Supply Chain Management (SCM) is the strategic coordination and integration of procurement, production, inventory management, and delivery processes to efficiently produce and distribute products and services, minimizing costs while meeting customer demands. For a Director of Manufacturing, it involves overseeing the end-to-end operations from raw material sourcing to final product delivery, ensuring smooth, cost-effective, and timely production and distribution.
Why It's Important
Supply Chain Management is crucial for a Director of Manufacturing because it ensures the efficient and cost-effective procurement of materials, timely production, and delivery of products, directly impacting product quality, customer satisfaction, and profitability.
How to Improve Supply Chain Management Skills
Improving Supply Chain Management (SCM) requires a strategic approach focused on enhancing efficiency, visibility, and collaboration across all supply chain components. As a Director of Manufacturing, you can achieve this by:
Leveraging Technology: Implement advanced SCM software (Oracle SCM, SAP SCM) to improve forecasting, planning, and execution.
Enhancing Visibility: Use tools like IBM Supply Chain Insights to gain real-time visibility into supply chain operations, enabling better decision-making.
Optimizing Inventory: Adopt lean inventory management practices to minimize waste and ensure optimal stock levels. Techniques such as Just-In-Time (JIT) can be effective (APICS).
Fostering Collaboration: Encourage collaboration both internally and with external partners (suppliers, logistics providers) to improve information flow and align goals (Supply Chain Collaboration).
Continuous Improvement: Embrace a culture of continuous improvement (Kaizen) to constantly seek ways to enhance SCM processes. Engage teams in regular review and improvement cycles (ASQ).
Sustainability Focus: Integrate sustainability into your SCM to meet consumer demand and regulatory requirements, reducing environmental impact and improving social responsibility (Sustainable Supply Chain Foundation).
Risk Management: Develop robust risk management strategies to anticipate and mitigate supply chain disruptions (Risk Management in Supply Chain).
By focusing on these key areas, you can significantly improve the efficiency, resilience, and competitiveness of your supply chain.
How to Display Supply Chain Management Skills on Your Resume
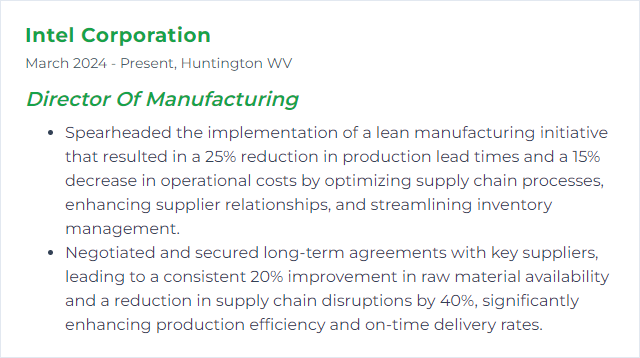
7. Continuous Improvement
Continuous Improvement in the context of a Director of Manufacturing refers to the ongoing effort to enhance products, services, or processes through incremental improvements or breakthrough innovations, aiming to boost efficiency, quality, and productivity in manufacturing operations.
Why It's Important
Continuous Improvement is crucial for a Director of Manufacturing as it drives operational efficiency, reduces waste, enhances product quality, and increases competitiveness, ensuring sustainable growth and customer satisfaction in a rapidly evolving market.
How to Improve Continuous Improvement Skills
To enhance Continuous Improvement in a manufacturing setting, a Director of Manufacturing should focus on the following strategies:
Leadership and Culture: Lead by example to foster a culture of continuous improvement. Encourage open communication and collaboration across all levels of the organization.
Training and Education: Invest in regular training programs to equip your team with the latest methodologies and tools in continuous improvement, such as Lean and Six Sigma.
Process Evaluation: Regularly review and assess manufacturing processes to identify inefficiencies and areas for improvement. Use tools like Value Stream Mapping for effective analysis.
Employee Involvement: Actively involve employees in the improvement process through suggestion schemes and involvement teams. Their hands-on experience is invaluable for identifying practical improvements.
Technology and Innovation: Stay abreast of technological advancements and integrate relevant innovations into your manufacturing processes to enhance efficiency and quality.
Performance Metrics: Implement key performance indicators (KPIs) to measure progress and success in continuous improvement efforts. Ensure these metrics are aligned with your overall business goals.
Feedback Loop: Establish a feedback loop to review the outcomes of improvement initiatives and refine strategies accordingly.
For further reading and detailed strategies, explore these resources:
How to Display Continuous Improvement Skills on Your Resume
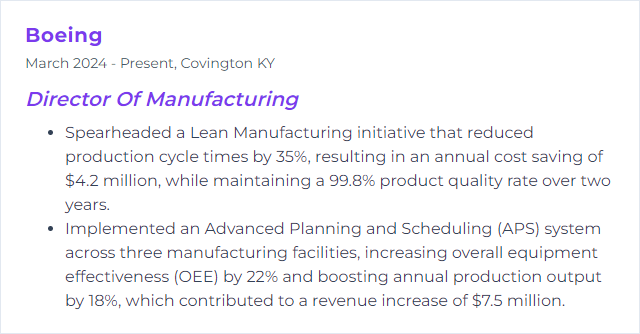
8. ISO Standards
ISO standards are internationally recognized guidelines that ensure products, services, and systems are safe, reliable, and of good quality. They help streamline manufacturing processes, enhance productivity, and facilitate access to new markets.
Why It's Important
ISO Standards ensure consistent quality, efficiency, and safety across manufacturing processes, enabling global market access, regulatory compliance, and consumer trust, essential for competitive advantage and operational excellence.
How to Improve ISO Standards Skills
Improving ISO standards within a manufacturing environment involves a strategic approach centered on continuous improvement, employee engagement, and process optimization. Here are concise steps tailored for a Director of Manufacturing:
Conduct a Gap Analysis: Assess current processes against specific ISO standards to identify areas of non-conformance. Tools like ISO's self-assessment checklist can be invaluable.
Engage Your Team: Foster a culture of quality and continuous improvement. Training and engaging your team in ISO requirements is crucial. Consider resources from ASQ (American Society for Quality) for training materials.
Implement Process Improvements: Based on the gap analysis, streamline processes, eliminate inefficiencies, and ensure consistent documentation. Lean manufacturing principles can help in this regard.
Utilize Quality Management Systems (QMS): A robust QMS like ISO 9001 can help in standardizing processes and achieving continuous improvement.
Regular Audits and Reviews: Conduct internal audits and management reviews regularly to ensure compliance and identify areas for improvement. The ISO Auditing Practices Group offers guidance on effective auditing.
Leverage Technology: Implement technology solutions for process monitoring, data analysis, and document control to enhance compliance and efficiency. Solutions like ERP systems can be effective.
Continuous Improvement: Adopt the Plan-Do-Check-Act (PDCA) cycle for continuous improvement in your ISO standards compliance efforts.
By following these steps and leveraging the provided resources, a Director of Manufacturing can significantly improve their organization's adherence to ISO standards, ultimately leading to higher quality, efficiency, and customer satisfaction.
How to Display ISO Standards Skills on Your Resume
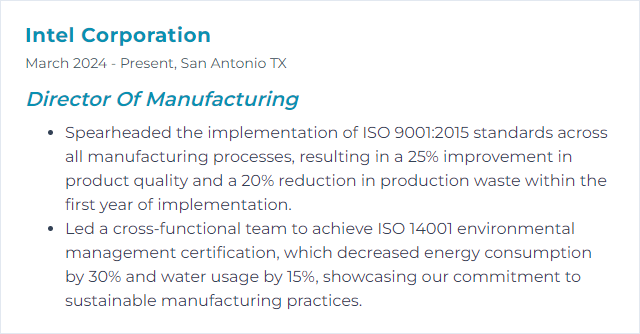
9. Project Management
Project management, in the context of a Director of Manufacturing, involves planning, executing, and overseeing manufacturing projects from inception to completion, ensuring they meet quality, time, and budget requirements while coordinating resources, team members, and processes to achieve the desired production outcomes.
Why It's Important
Project management is crucial for a Director of Manufacturing as it ensures efficient coordination of resources, timelines, and tasks, leading to the successful execution of manufacturing projects. This optimizes production, minimizes costs, and enhances product quality, directly impacting the company's bottom line and competitive edge.
How to Improve Project Management Skills
Improving project management, especially from the perspective of a Director of Manufacturing, involves a strategic approach focused on efficiency, communication, and continuous improvement. Here are key points to consider:
Adopt Agile Methodologies: Implement Agile practices to enhance flexibility and responsiveness. Agile's iterative approach allows for better handling of changes and uncertainties in manufacturing projects. Agile Alliance provides resources and principles that can guide this implementation.
Leverage Technology: Utilize project management software tools tailored for manufacturing projects to streamline project planning, execution, and monitoring. Tools like Monday.com and Smartsheet offer customizable solutions for managing resources, timelines, and communication.
Enhance Communication: Establish clear and effective communication channels among all stakeholders. Effective communication ensures alignment and prompt resolution of issues. Tools like Slack can facilitate instant messaging and collaboration.
Focus on Continuous Improvement: Adopt a Kaizen or continuous improvement philosophy to identify inefficiencies and implement solutions. Regular review meetings and Kaizen principles can guide these efforts.
Develop Skills and Team: Invest in training and development programs to enhance the skills of your team. Project Management Institute (PMI) offers certifications and resources that can elevate the capabilities of your project management team.
Implement Risk Management: Develop a proactive risk management plan to identify potential issues and have mitigation strategies in place. The Risk Management Guide by CIO outlines steps to anticipate and manage risks effectively.
Measure Performance and Outcomes: Use Key Performance Indicators (KPIs) to track and measure the success of your projects. This data-driven approach aids in making informed decisions. The Balanced Scorecard Institute offers a framework for setting and tracking goals.
By focusing on these areas, a Director of Manufacturing can significantly improve the efficiency and outcome of project management efforts.
How to Display Project Management Skills on Your Resume
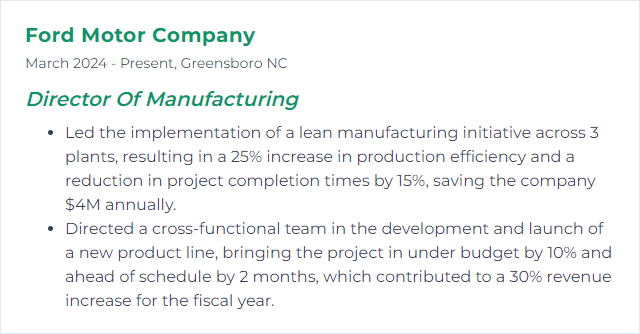
10. Automation Technologies
Automation technologies encompass systems, software, and machinery designed to streamline and enhance manufacturing processes. They reduce human intervention, increase efficiency, and improve quality and productivity in production lines.
Why It's Important
Automation technologies enhance efficiency, reduce costs, and improve product quality by streamlining production processes, minimizing human error, and enabling 24/7 operation. This leads to increased competitiveness and profitability for the manufacturing operation.
How to Improve Automation Technologies Skills
To improve Automation Technologies as a Director of Manufacturing, focus on the following key strategies:
Continuous Learning: Stay updated with the latest trends and technologies in automation by subscribing to leading journals and platforms like Automation World and IEEE Robotics and Automation Society.
Invest in R&D: Allocate resources to research and development to innovate and refine automation processes. Collaborate with institutions like MIT's Industrial Liaison Program for cutting-edge insights.
Employee Training: Upskill your workforce to handle advanced automation technologies through platforms like Udemy or Coursera.
Adopt Flexible Automation: Implement flexible automation systems that can be easily reconfigured for different tasks. Learn more from the Robotics Industries Association.
Monitor and Optimize: Use analytics tools to monitor the performance of your automation systems. Platforms like Tableau can help analyze data for optimization.
Collaborate with Vendors: Establish strong relationships with technology vendors for support and to stay informed about upgrades and innovations. Events by The Association for Manufacturing Technology are great for networking.
Sustainability Focus: Incorporate sustainable practices into your automation strategies. Resources from The Sustainable Manufacturing Innovation Alliance can guide you.
By focusing on these strategies, you can enhance your manufacturing operations' efficiency, productivity, and sustainability through improved automation technologies.
How to Display Automation Technologies Skills on Your Resume
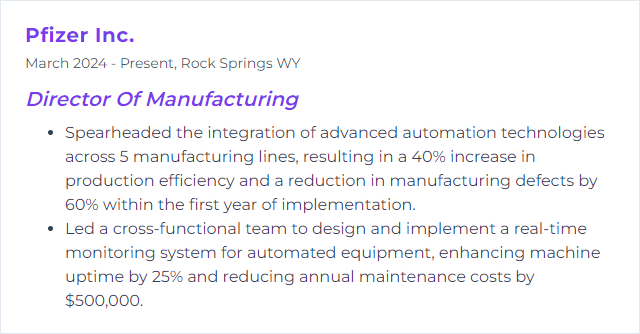
11. Inventory Management
Inventory Management is the process of overseeing and controlling the ordering, storage, and use of components that a company uses in the production of the items it sells, as well as the management of finished products that are ready for sale. This includes tracking inventory levels, orders, sales, and deliveries to ensure that the right amount of materials and products are available at the right time, optimizing both production efficiency and customer satisfaction.
Why It's Important
Inventory management is crucial for ensuring optimal stock levels, minimizing waste and costs, and meeting production schedules efficiently, thereby maximizing profitability and customer satisfaction.
How to Improve Inventory Management Skills
Improving inventory management involves strategic planning and the utilization of advanced tools to streamline operations, enhance accuracy, and reduce costs. Here are concise steps tailored for a Director of Manufacturing:
Implement Lean Inventory Practices: Adopt lean manufacturing principles to minimize waste and stock only what is necessary. Lean Inventory Management can significantly reduce carrying costs and improve efficiency.
Adopt Automation and Technology: Utilize Inventory Management Software to automate tracking, forecasting, and ordering processes. This technology can help in maintaining optimal inventory levels and improving accuracy.
Enhance Forecasting Methods: Improve demand forecasting by using data analytics and AI tools to predict market trends and customer needs more accurately, thus ensuring you have the right inventory when needed.
Strengthen Supplier Relationships: Develop strong relationships with suppliers for better negotiation on prices and more flexible terms. This can lead to more efficient inventory restocking processes. Supplier Relationship Management is crucial in achieving this goal.
Regularly Review and Optimize Inventory: Conduct regular audits and analyze inventory turnover rates. Tools like ABC Analysis can be helpful in prioritizing inventory management efforts based on the value of different items.
Train Your Team: Ensure your team is well-trained in inventory management best practices and the use of any implemented technology. Continuous education and training can greatly improve inventory handling and decision-making processes.
Continuous Improvement: Adopt a Kaizen or continuous improvement approach to inventory management. Regularly review processes, solicit team feedback, and stay updated on new technologies or methodologies in the field.
By focusing on these areas, a Director of Manufacturing can significantly improve inventory management, leading to reduced costs, improved production efficiency, and ultimately, higher customer satisfaction.
How to Display Inventory Management Skills on Your Resume
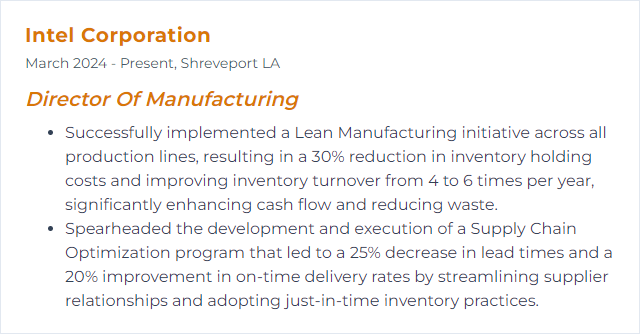
12. Safety Compliance
Safety compliance in the context of a Director of Manufacturing involves ensuring that all operational processes, equipment, and employee behaviors adhere to established health, safety, and environmental regulations and standards to prevent accidents and injuries in the manufacturing facility.
Why It's Important
Safety compliance is crucial in manufacturing to ensure the well-being of employees, prevent workplace accidents, minimize legal liabilities, and uphold productivity by reducing downtime caused by injuries or regulatory penalties.
How to Improve Safety Compliance Skills
Improving safety compliance in a manufacturing setting involves a multifaceted approach, focusing on training, culture, and continuous improvement. Here are concise steps to enhance safety compliance:
Assess and Analyze Risks: Conduct regular safety audits and risk assessments to identify potential hazards. OSHA’s Recommended Practices for Safety and Health Programs is an excellent resource for understanding how to evaluate your workplace.
Develop a Safety Plan: Create a comprehensive safety plan that addresses identified risks, includes emergency procedures, and sets clear safety goals. The National Safety Council offers guidance on various safety topics.
Training and Education: Implement ongoing safety training programs for employees. Ensure they understand the risks and the importance of compliance. OSHA's Training Services can help design your training program.
Engage Employees: Foster a safety culture by involving employees in safety discussions, decisions, and audits. This engagement can lead to better adherence to safety protocols.
Regular Communication: Keep safety in the forefront of employees’ minds through regular meetings, updates, and visible safety metrics.
Invest in Safety Tools and Equipment: Provide the necessary tools, equipment, and protective gear to ensure employees can work safely. Regularly maintain and inspect equipment.
Monitor and Enforce Compliance: Use inspections and audits to ensure adherence to safety protocols. Address violations promptly and consistently.
Review and Improve: Continuously assess the effectiveness of your safety program and make necessary adjustments. This could involve adopting new technologies or practices.
For a Director of Manufacturing, aligning safety compliance with operational goals can enhance both safety and productivity. Engaging with professional organizations such as the American Society of Safety Professionals can provide additional resources and networking opportunities to stay abreast of best practices and innovations in safety compliance.
How to Display Safety Compliance Skills on Your Resume
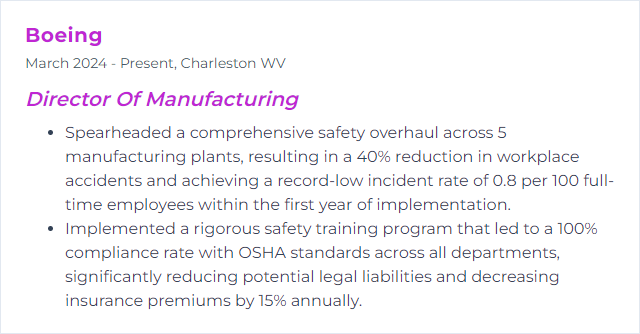