Top 12 Director of Logistics Skills to Put on Your Resume
In today's highly competitive job market, standing out as a Director of Logistics requires showcasing a blend of strategic vision and practical expertise on your resume. Mastering a set of key skills can not only elevate your profile but also significantly enhance your ability to manage complex supply chains and logistics operations efficiently.
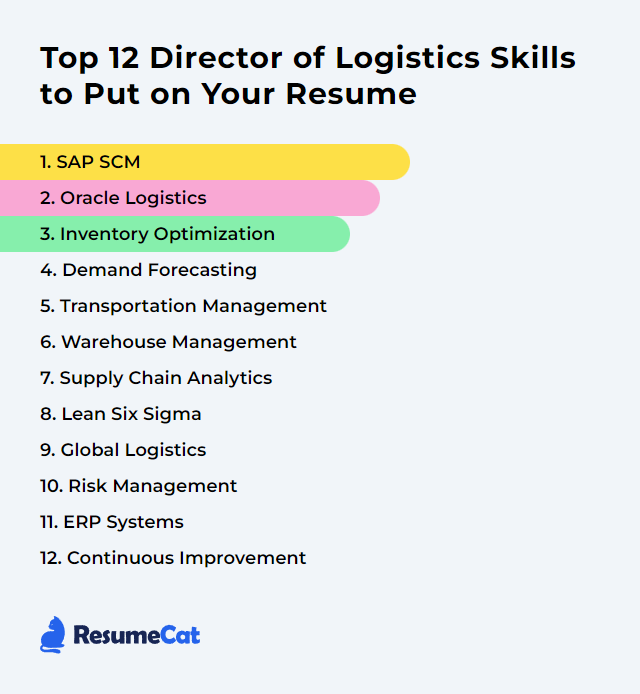
Director of Logistics Skills
- SAP SCM
- Oracle Logistics
- Inventory Optimization
- Demand Forecasting
- Transportation Management
- Warehouse Management
- Supply Chain Analytics
- Lean Six Sigma
- Global Logistics
- Risk Management
- ERP Systems
- Continuous Improvement
1. SAP SCM
SAP SCM (Supply Chain Management) is an integrated software solution that facilitates the management of supply chain processes, including planning, execution, and coordination of materials, information, and financial flows, aimed at improving efficiency, reducing costs, and enhancing customer satisfaction in logistics operations.
Why It's Important
SAP SCM (Supply Chain Management) is crucial as it optimizes and streamlines the entire supply chain process, from planning and procurement to logistics and execution. This enables a Director of Logistics to enhance operational efficiency, reduce costs, and ensure timely delivery, thus improving customer satisfaction and competitive advantage.
How to Improve SAP SCM Skills
To improve SAP SCM effectively, a Director of Logistics should focus on the following concise strategies:
Integrate Advanced Analytics: Utilize SAP's advanced analytics to gain insights into supply chain performance and identify areas for improvement. SAP Analytics Cloud can enhance decision-making and forecasting.
Leverage IoT for Real-Time Tracking: Implement IoT solutions within SAP SCM to monitor and manage the logistics network in real time, improving visibility and responsiveness. SAP Internet of Things provides tools for this.
Upgrade to SAP S/4HANA: Transition to SAP S/4HANA for a more robust, flexible, and efficient SCM system that supports real-time data processing and improved user experience.
Enhance Collaboration with SAP Ariba Network: Use SAP Ariba for better collaboration with suppliers and partners, streamlining procurement and supply chain processes.
Implement SAP Integrated Business Planning (IBP): Adopt SAP IBP for real-time, integrated supply chain planning, improving responsiveness to market changes.
Continuous Training and Support: Ensure your team receives ongoing training on the latest SAP SCM features and best practices. SAP offers training and certification programs.
Automation and AI: Incorporate automation and AI technologies to optimize supply chain operations, from predictive analytics for demand forecasting to automated warehouse management. SAP's AI and Machine Learning solutions can be found here.
By focusing on these areas, a Director of Logistics can significantly enhance the efficiency and effectiveness of their SAP SCM implementation.
How to Display SAP SCM Skills on Your Resume
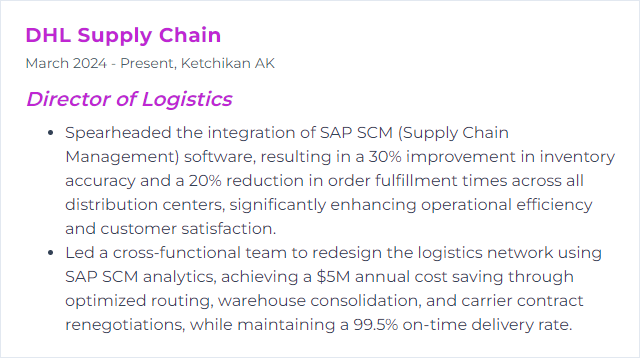
2. Oracle Logistics
Oracle Logistics provides an integrated suite of cloud-based applications designed to manage and optimize the end-to-end logistics process, encompassing transportation management, global trade management, and warehouse management. It offers tools for planning, execution, and visibility across the entire supply chain, enabling a Director of Logistics to reduce costs, improve efficiency, and ensure compliance with global trade regulations.
Why It's Important
Oracle Logistics offers an integrated suite of applications designed to streamline and optimize logistics operations. For a Director of Logistics, it is important because it provides comprehensive tools for managing transportation, global trade compliance, and warehouse operations efficiently, enabling significant cost savings, enhancing visibility across the supply chain, and improving service levels.
How to Improve Oracle Logistics Skills
Improving Oracle Logistics involves a strategic approach focusing on system integration, process optimization, and leveraging advanced analytics for better decision-making. Here’s a concise guide:
System Integration: Ensure seamless integration with existing ERP systems and supply chain modules for real-time data sharing. Oracle provides extensive documentation on integrating Oracle Logistics.
Process Optimization: Regularly review and optimize logistics processes. Utilize Oracle’s Process Automation tools to streamline operations and reduce manual intervention.
Data Analytics: Leverage Oracle’s Advanced Analytics to gain insights into logistics operations, identifying bottlenecks and areas for improvement.
Training and Support: Invest in training for your team to ensure they are up-to-date with the latest Oracle Logistics features and best practices. Oracle University offers specific training for logistics modules.
Collaborate with Oracle Partners: Work with Oracle partners who can provide specialized expertise in logistics to tailor the Oracle Logistics platform to your business needs. Explore Oracle’s partner network.
By focusing on these areas, you can enhance the efficiency and responsiveness of your logistics operations.
How to Display Oracle Logistics Skills on Your Resume

3. Inventory Optimization
Inventory Optimization is a strategic process used to maintain the right balance of stock to meet customer demand while minimizing holding costs and maximizing efficiency in procurement and distribution. It involves using analytics and forecasting tools to achieve optimal stock levels, reduce overstocks and stockouts, and improve overall supply chain performance.
Why It's Important
Inventory optimization is crucial for efficiently balancing stock levels to meet customer demand while minimizing carrying costs and avoiding stockouts, thereby ensuring operational excellence and maximizing profitability.
How to Improve Inventory Optimization Skills
To improve inventory optimization, focus on the following strategies tailored for a Director of Logistics:
Implement Demand Forecasting: Use historical data and predictive analytics to accurately forecast customer demand. Tools like Forecast Pro can enhance your forecasting accuracy.
Adopt an ABC Analysis: Classify inventory into A, B, and C categories based on importance and sales volume. This prioritization helps in focusing on the most critical items. The APICS provides resources and training for inventory management best practices.
Leverage Inventory Management Software: Utilize advanced inventory management systems that offer real-time tracking and automated reordering points. Software like NetSuite can streamline inventory optimization.
Enhance Supplier Relationships: Build strong relationships with suppliers for better terms and reliability in restocking. Collaborating closely can lead to more flexible inventory management.
Regularly Review Inventory Performance: Continuously analyze inventory performance against set KPIs to identify areas for improvement. Resources from The Chartered Institute of Logistics and Transport (CILT) can provide valuable insights and benchmarks.
Optimize Warehouse Layout: Ensure that your warehouse layout is designed for optimal inventory accessibility and turnover. Techniques such as slotting optimization can significantly reduce picking time. Consider insights from The Warehousing Education and Research Council (WERC) for industry standards.
Invest in Training: Equip your team with the latest skills in inventory management through workshops and certifications. The Institute for Supply Management (ISM) offers courses and resources for professionals.
By focusing on these areas, you can significantly improve your inventory optimization efforts, ensuring that your operation runs smoothly and efficiently.
How to Display Inventory Optimization Skills on Your Resume
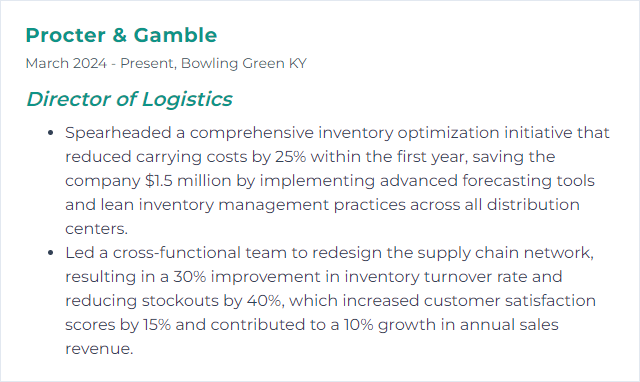
4. Demand Forecasting
Demand forecasting is the process of predicting future customer demand for a company's products or services, enabling the logistics director to optimize inventory levels, manage supply chain operations efficiently, and ensure timely product delivery to meet customer needs.
Why It's Important
Demand forecasting is critical for optimizing inventory levels, ensuring timely delivery, and minimizing costs, enabling informed decision-making and strategic planning for efficient supply chain management.
How to Improve Demand Forecasting Skills
Improving demand forecasting involves a blend of strategic planning, technology implementation, and data analysis. For a Director of Logistics aiming for efficiency, consider the following concise steps:
Leverage Advanced Analytics: Utilize predictive analytics and machine learning algorithms to analyze historical data and identify patterns. Tools like IBM Demand Forecasting can enhance accuracy.
Integrate Real-Time Data: Incorporate real-time market and weather data to adjust forecasts dynamically. Platforms like SAP Integrated Business Planning facilitate this.
Improve Data Quality: Ensure the data used for forecasting is accurate, complete, and timely. Techniques and best practices for data quality management can be found on Gartner’s insights.
Collaborate Across Departments: Foster communication between sales, marketing, and supply chain departments to align forecasts with market trends and promotional activities.
Implement Scenario Planning: Use scenario planning to prepare for various demand outcomes, thereby reducing the risk of stockouts or excess inventory. Tools like Anaplan help in building adaptable forecasting models.
Continuous Improvement: Regularly review and adjust forecasting models based on performance metrics and feedback loops. This iterative process is key to refining accuracy over time.
Educate and Train Your Team: Ensure your team has the necessary skills and knowledge in data analysis and forecasting methods. Consider specialized training resources like APICS for supply chain professionals.
By focusing on these strategies, a Director of Logistics can significantly enhance demand forecasting accuracy, leading to improved supply chain efficiency and cost reduction.
How to Display Demand Forecasting Skills on Your Resume
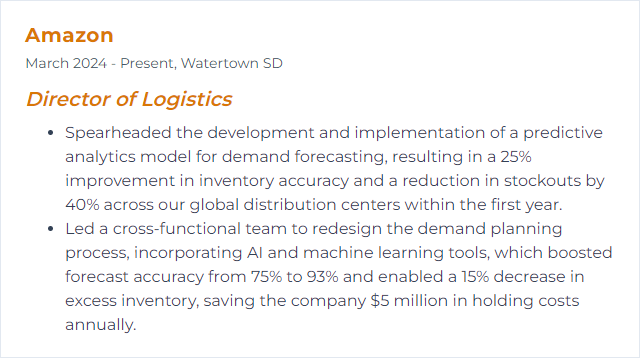
5. Transportation Management
Transportation Management involves planning, executing, and optimizing the movement of goods and materials. It encompasses selecting the most efficient routes, modes of transport, and carriers to minimize costs and maximize delivery performance, ensuring that products are delivered on time and in good condition. This is critical for a Director of Logistics to streamline operations, improve customer satisfaction, and reduce transportation expenses.
Why It's Important
Transportation Management is crucial for optimizing the movement of goods, ensuring timely delivery, reducing costs, and improving customer satisfaction, thereby enhancing overall supply chain efficiency and competitiveness.
How to Improve Transportation Management Skills
Improving Transportation Management, especially from the perspective of a Director of Logistics, involves a multifaceted approach focusing on efficiency, cost reduction, and enhancing service quality. Here are key strategies:
Leverage Technology: Implement advanced Transportation Management Systems (TMS) for route optimization, freight audit, payment systems, and real-time tracking. Tools like Oracle Transportation Management and SAP Transportation Management can drive significant improvements.
Data Analytics: Use data analytics to understand trends, forecast demand, and make informed decisions. Platforms like Tableau and Power BI can analyze transportation metrics for better decision-making.
Carrier Relationship Management: Develop strong relationships with carriers. Leverage platforms like C.H. Robinson’s Navisphere to enhance carrier collaboration and secure competitive rates.
Sustainability Practices: Implement eco-friendly transportation practices. The SmartWay Transport Partnership by the EPA offers tools and frameworks to reduce environmental impact.
Continuous Improvement: Adopt a culture of continuous improvement (Lean Six Sigma) to identify inefficiencies and implement best practices. Resources like ASQ’s Lean Six Sigma Training can provide methodologies for process improvement.
Compliance and Risk Management: Ensure strict adherence to regulations and manage risks effectively. Tools like Descartes can help in managing compliance and reducing risks.
Employee Training and Development: Invest in training programs for your team to stay updated with the latest trends and technologies in logistics. LinkedIn Learning offers courses on various aspects of logistics and supply chain management.
By focusing on these areas, a Director of Logistics can significantly improve transportation management, enhancing efficiency, reducing costs, and improving service delivery.
How to Display Transportation Management Skills on Your Resume
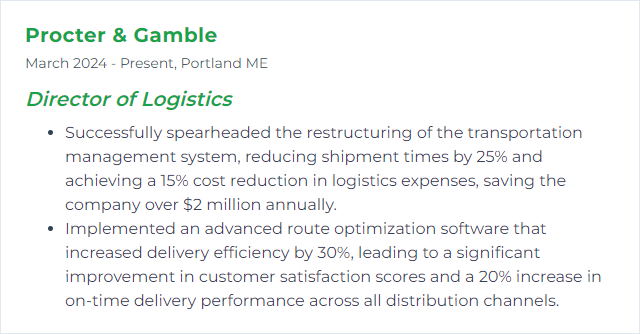
6. Warehouse Management
Warehouse Management involves overseeing the operations of a warehouse, including inventory management, order fulfillment, and the efficient storage and movement of goods, to ensure optimal functionality and productivity in support of an organization's logistics and supply chain strategy.
Why It's Important
Warehouse Management is crucial for optimizing inventory accuracy, enhancing order fulfillment efficiency, and reducing operational costs, enabling the Director of Logistics to ensure timely delivery, customer satisfaction, and profitability.
How to Improve Warehouse Management Skills
Improving warehouse management involves optimizing operations for efficiency, accuracy, and safety. As a Director of Logistics, consider these concise strategies:
Implement a Warehouse Management System (WMS): A WMS can enhance inventory accuracy and streamline processes. Review options here.
Adopt Lean Inventory Practices: Minimize waste by implementing just-in-time inventory to reduce excess stock. Learn about lean practices here.
Improve Layout and Organization: Design your warehouse layout for optimal flow and accessibility. Guidelines on effective layout design can be found here.
Invest in Training: Regularly train staff on best practices and safety. The Occupational Safety and Health Administration (OSHA) offers resources here.
Leverage Automation and Robotics: Incorporate technology to increase efficiency and reduce manual errors. Insights on warehouse automation can be accessed here.
Regularly Review and Optimize Processes: Use data analytics to monitor performance and identify improvement areas. Find analytics tools recommendations here.
By focusing on these areas, you can significantly enhance warehouse operations and overall logistics performance.
How to Display Warehouse Management Skills on Your Resume
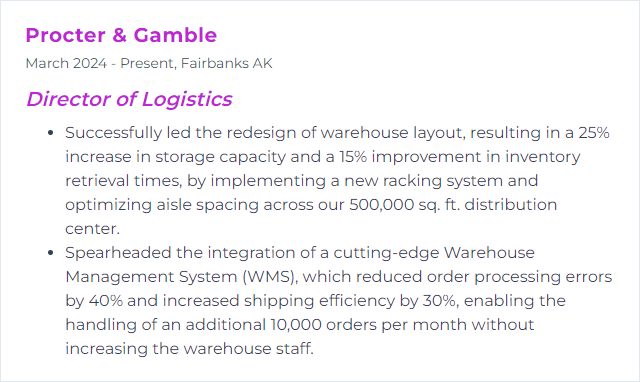
7. Supply Chain Analytics
Supply Chain Analytics involves leveraging data analysis tools and methodologies to optimize logistics, inventory management, and operational efficiency within the supply chain, aiming to enhance decision-making, reduce costs, and improve service delivery.
Why It's Important
Supply Chain Analytics is crucial for a Director of Logistics as it enables data-driven decision-making, optimizing operations, reducing costs, improving efficiency, and enhancing customer satisfaction through more reliable and responsive supply chain processes.
How to Improve Supply Chain Analytics Skills
Improving Supply Chain Analytics involves strategic steps to enhance data accuracy, visibility, and decision-making processes. Here’s a concise guide tailored for a Director of Logistics:
Implement Advanced Analytics Tools: Adopt advanced analytics platforms that offer real-time insights and predictive analytics to anticipate supply chain disruptions.
Integrate Data Sources: Ensure seamless data integration from various points in your supply chain for a unified view, enhancing accuracy and decision-making.
Enhance Data Quality: Invest in data cleaning and validation processes to ensure analytics are based on accurate and up-to-date information.
Leverage IoT and AI: Utilize IoT and AI technologies to gather and analyze data in real-time, facilitating proactive adjustments and optimizations.
Upskill Your Team: Provide training and resources for your team to understand and leverage analytics tools effectively.
Collaborate with Partners: Foster collaboration with supply chain partners to share data and insights, improving end-to-end visibility and efficiency.
Monitor and Adapt: Regularly review analytics processes and outcomes, staying adaptable to new technologies and methodologies to continuously refine and improve your supply chain analytics capabilities.
By focusing on these strategies, Directors of Logistics can significantly enhance the effectiveness of their supply chain analytics, leading to improved operational efficiencies, reduced costs, and better decision-making.
How to Display Supply Chain Analytics Skills on Your Resume
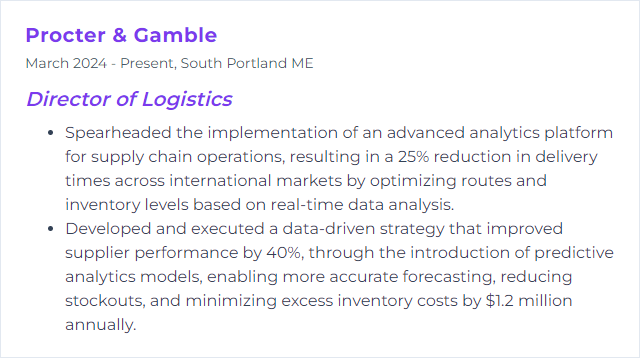
8. Lean Six Sigma
Lean Six Sigma is a methodology that combines the Lean manufacturing principles of reducing waste with Six Sigma's focus on reducing variation and defects. For a Director of Logistics, it offers a structured approach to improving operational efficiency, enhancing quality, and optimizing supply chain processes, ultimately leading to increased customer satisfaction and reduced costs.
Why It's Important
Lean Six Sigma is important for a Director of Logistics as it streamlines operations, reduces waste, and improves efficiency, leading to faster delivery times, lower costs, and enhanced customer satisfaction.
How to Improve Lean Six Sigma Skills
Improving Lean Six Sigma within a logistics context, especially for a Director of Logistics, involves a focus on continuous improvement, data-driven decision making, and cross-functional collaboration. Here's a concise guide:
Enhance Data Analytics: Invest in advanced data analytics tools to accurately measure performance, identify inefficiencies, and spot improvement opportunities. Lean Six Sigma Tools from ASQ are a great starting point.
Strengthen Team Training: Ensure your team is well-versed in Lean Six Sigma methodologies. Offer regular training sessions and consider certifications. ASQ Certifications can elevate team expertise.
Implement Cross-Functional Collaboration: Promote collaboration between departments to ensure the seamless application of Lean Six Sigma principles. This Harvard Business Review article provides insights into breaking down silos.
Adopt Agile Project Management: Integrate Lean Six Sigma with agile project management to enhance flexibility and responsiveness to changes. Agile Project Management by PMI offers a comprehensive guide.
Focus on Customer Value: Always align improvement projects with customer needs and expectations to enhance value delivery. The Value Stream Mapping guide from the Lean Enterprise Institute can help visualize and improve the flow of value to customers.
Drive a Culture of Continuous Improvement: Foster an organizational culture that embraces change and continuous improvement. Encourage feedback, recognize achievements, and learn from failures. Creating a Culture of Continuous Improvement from MIT Sloan offers strategies to build this culture.
By focusing on these areas, a Director of Logistics can significantly enhance the impact of Lean Six Sigma initiatives within their organization.
How to Display Lean Six Sigma Skills on Your Resume
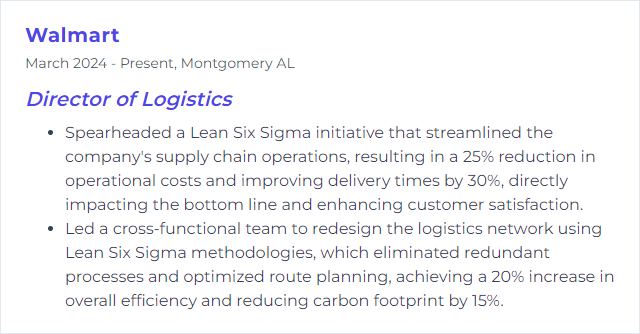
9. Global Logistics
Global logistics refers to the comprehensive process of managing the movement and storage of goods, services, and information across international borders, from the point of origin to the point of consumption, to meet customer requirements. This involves coordinating transportation, inventory, warehousing, material handling, packaging, fulfillment, and security tasks on a global scale. For a Director of Logistics, it encompasses strategic planning and execution to optimize the supply chain, reduce costs, and ensure efficient delivery in a global marketplace.
Why It's Important
Global logistics is crucial as it ensures the efficient and timely movement of goods across borders, optimizing supply chains, reducing costs, and enhancing customer satisfaction, thereby driving competitive advantage and business growth for companies in the global market.
How to Improve Global Logistics Skills
Improving global logistics requires a strategic approach focused on efficiency, technology integration, and collaboration. Here's a concise plan for a Director of Logistics:
Leverage Technology: Implement advanced logistics technology like IoT, AI, and blockchain for real-time tracking, demand forecasting, and secure, transparent transactions.
Optimize Route Planning: Use dynamic routing software to adapt to real-time changes, reducing fuel costs and improving delivery times.
Enhance Supplier Relationships: Develop strategic partnerships with suppliers and use collaborative platforms to ensure communication and efficiency in the supply chain.
Focus on Sustainability: Implement sustainable logistics practices like using eco-friendly packaging and optimizing load capacity to reduce carbon footprint and costs.
Invest in Training and Development: Foster a culture of continuous improvement by investing in employee training focusing on new technologies and best practices in logistics.
Adopt a Customer-Centric Approach: Utilize data analytics to understand customer preferences and tailor logistics strategies to enhance customer satisfaction.
Regularly Review and Adapt: Conduct regular audits of your logistics operations to identify inefficiencies and adapt to changing market demands and challenges.
By focusing on these areas, a Director of Logistics can significantly improve the efficiency, resilience, and sustainability of global logistics operations.
How to Display Global Logistics Skills on Your Resume
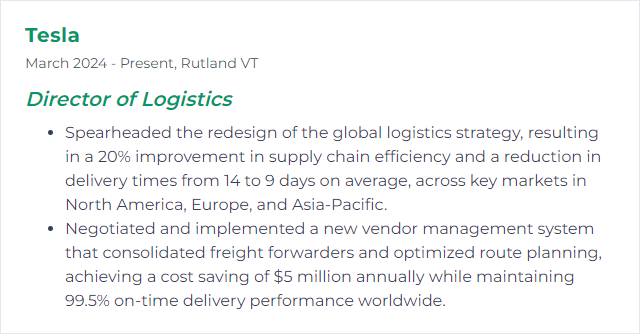
10. Risk Management
Risk Management, in the context of a Director of Logistics, involves identifying, assessing, and prioritizing risks to supply chain operations and implementing strategies to minimize, monitor, and control the probability or impact of unfortunate events or to maximize the realization of opportunities.
Why It's Important
Risk management is crucial for a Director of Logistics as it ensures the efficient and uninterrupted flow of goods by identifying, analyzing, and mitigating potential risks. This proactive approach minimizes disruptions, reduces costs, enhances safety, and ensures compliance, thereby safeguarding the company's reputation and profitability.
How to Improve Risk Management Skills
Improving risk management, especially for a Director of Logistics, involves a strategic approach designed to identify, assess, and mitigate potential risks that could impact operations. Here's a concise guide:
Risk Identification: Continuously identify and list potential risks that could affect logistics operations, including supply chain disruptions, geopolitical changes, and technology failures.
Risk Assessment: Evaluate the identified risks to determine their potential impact and likelihood. Tools like SWOT (Strengths, Weaknesses, Opportunities, and Threats) analysis can be useful. Guide to SWOT Analysis
Mitigation Strategies: Develop and implement strategies to reduce the probability of risk occurrence or minimize its impact. This could involve diversifying suppliers, investing in technology for better tracking and management, or developing contingency plans. Risk Mitigation Strategies
Continuous Monitoring: Set up a system for ongoing monitoring of the risk landscape, as it can change rapidly. Utilize risk management software for real-time data analysis and reporting. Risk Management Software Solutions
Communication: Maintain clear and consistent communication channels within your organization and with external stakeholders (suppliers, logistics partners) to ensure quick response to any risk event. Effective Communication in Risk Management
Training and Awareness: Regularly train your team on risk management practices and keep them informed about potential risks and the procedures to follow in case of an event. Logistics Training Programs
Review and Improvement: Regularly review and update your risk management strategies based on new threats, past incidents, and lessons learned to improve resilience. Continuous Improvement in Risk Management
By incorporating these strategies, a Director of Logistics can significantly improve risk management within their organization, ensuring smoother operations and the ability to quickly adapt to challenges.
How to Display Risk Management Skills on Your Resume
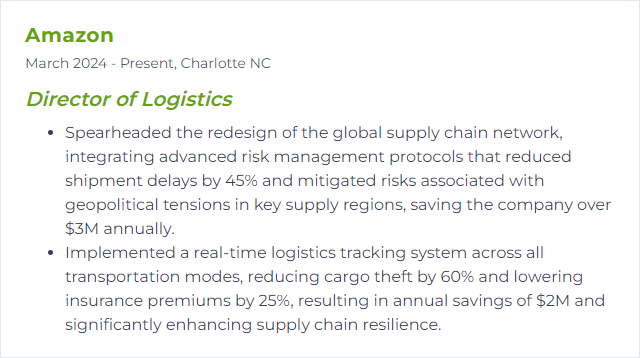
11. ERP Systems
ERP (Enterprise Resource Planning) systems are integrated software platforms that manage and automate core business processes, including logistics, by consolidating information from various departments into a unified database, facilitating improved decision-making, efficiency, and coordination across the organization.
Why It's Important
ERP systems are crucial for a Director of Logistics as they streamline and integrate core business processes—such as inventory management, order processing, and shipping—into a single system. This integration enhances operational efficiency, improves data accuracy and decision-making, and ultimately boosts customer satisfaction by ensuring timely delivery of goods and services.
How to Improve ERP Systems Skills
Improving ERP systems, especially from a logistics perspective, involves enhancing data accuracy, integration capabilities, and real-time tracking. Here are concise steps for a Director of Logistics:
Integration and Automation: Ensure the ERP system integrates seamlessly with internal and external systems (e.g., CRM, SCM) and automates routine tasks to reduce errors and save time. ERP Integration Best Practices
Data Accuracy and Quality: Implement data governance practices to maintain high-quality, accurate data for better decision-making. Data Quality Management
Real-Time Tracking: Upgrade to real-time tracking for inventory and shipments to enhance visibility and control. Real-Time Tracking in Supply Chain
Customization and Scalability: Customize the ERP system to fit specific logistics needs and ensure it can scale with your business growth. ERP Customization Guide
Training and Support: Invest in comprehensive training for users and establish a support structure for addressing system issues promptly. ERP Training Strategies
Continuous Improvement: Regularly review and update the ERP system based on new logistics trends, technologies, and business needs. Continuous Improvement in ERP
Focusing on these areas can significantly enhance the effectiveness of ERP systems in logistics, driving efficiencies and supporting strategic business goals.
How to Display ERP Systems Skills on Your Resume
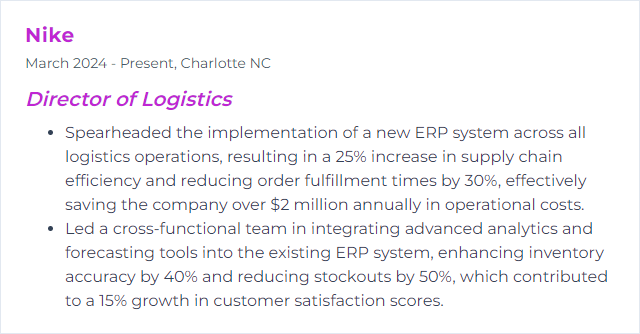
12. Continuous Improvement
Continuous Improvement, for a Director of Logistics, involves systematically and perpetually enhancing logistics processes, operations, and efficiencies to reduce costs, improve service delivery, and boost overall performance.
Why It's Important
Continuous improvement is vital for a Director of Logistics as it enhances efficiency, reduces costs, improves customer satisfaction, and ensures adaptability in a rapidly changing market, ultimately maintaining competitive advantage.
How to Improve Continuous Improvement Skills
Improving Continuous Improvement (CI) in logistics involves strategic, consistent efforts aimed at enhancing processes, increasing efficiency, and reducing waste. Here’s a brief guide tailored for a Director of Logistics:
Establish Clear Objectives: Define specific, measurable goals aligned with your organization's vision. Understanding your end target is crucial for effective improvement. SMART Goals can guide you in setting these objectives.
Engage Your Team: Involve employees at all levels in the CI process. Their insights can highlight areas for improvement and drive ownership of change. Team Engagement Strategies from Harvard Business Review provide valuable approaches.
Implement Lean Logistics: Adopt Lean principles to eliminate waste, streamline operations, and improve value delivery. This Lean Management Guide offers an overview and practical tips.
Leverage Technology: Invest in technology solutions that enhance visibility, improve communication, and automate processes. Explore Supply Chain Digitalization for insights on harnessing technology in logistics.
Monitor Performance and Feedback: Use Key Performance Indicators (KPIs) to track progress and gather feedback regularly. This ensures continuous alignment with goals and highlights areas for further improvement. The Balanced Scorecard Institute offers a framework for measuring performance.
Foster a Culture of Continuous Learning: Promote ongoing education, training, and development opportunities. Encouraging a mindset of continuous learning supports adaptability and innovation. Continuous Learning Culture by Deloitte offers strategies to build this environment.
Review and Revise Regularly: Continuous Improvement is an ongoing process. Regularly review strategies, outcomes, and practices to ensure they remain effective and aligned with organizational goals. The PDCA (Plan-Do-Check-Act) cycle is a fundamental method for this, detailed in ASQ’s PDCA Cycle.
By focusing on these areas, a Director of Logistics can significantly enhance their Continuous Improvement efforts, leading to more efficient, responsive, and competitive logistics operations.
How to Display Continuous Improvement Skills on Your Resume
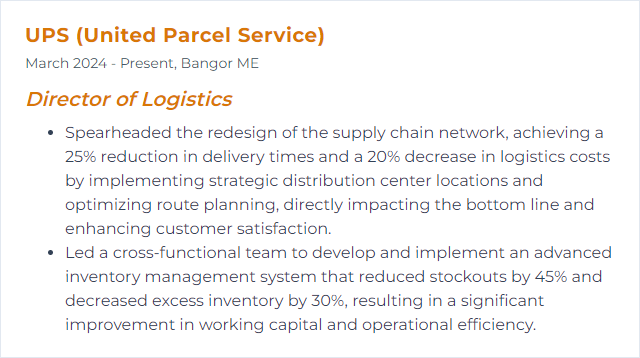