Top 12 Composite Technician Skills to Put on Your Resume
In today's competitive job market, standing out as a composite technician requires showcasing a unique set of skills on your resume. This article outlines the top 12 composite technician skills that employers value, helping you to highlight your expertise and secure your next job opportunity.
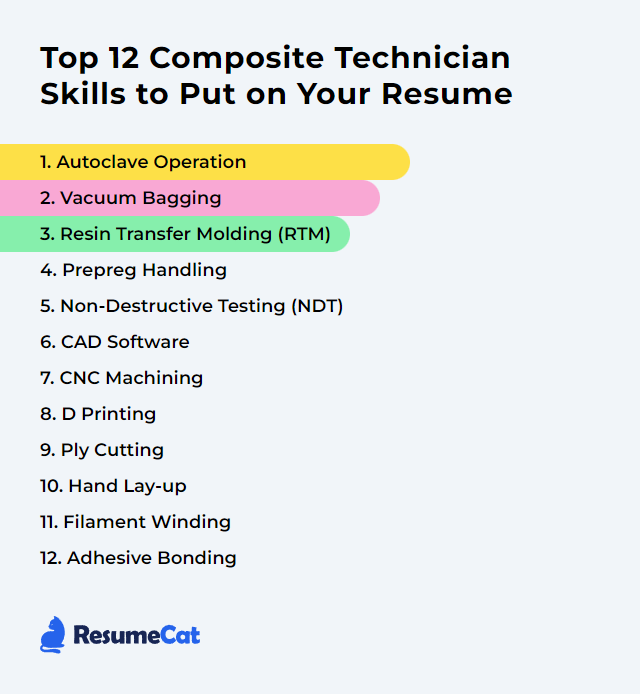
Composite Technician Skills
- Autoclave Operation
- Vacuum Bagging
- Resin Transfer Molding (RTM)
- Prepreg Handling
- Non-Destructive Testing (NDT)
- CAD Software
- CNC Machining
- D Printing
- Ply Cutting
- Hand Lay-up
- Filament Winding
- Adhesive Bonding
1. Autoclave Operation
Autoclave operation for a Composite Technician involves using a pressurized, heated chamber to cure and consolidate composite materials, ensuring they achieve desired strength, durability, and structural integrity through controlled temperature and pressure cycles.
Why It's Important
Autoclave operation is crucial for a Composite Technician because it ensures the proper curing and consolidation of composite materials under controlled temperature and pressure, resulting in high-strength, defect-free components essential for their intended applications.
How to Improve Autoclave Operation Skills
Improving autoclave operation for a Composite Technician involves optimizing the process for efficiency, safety, and quality outcomes. Here are concise strategies:
Preventive Maintenance: Regularly check and maintain autoclave components to prevent breakdowns. Centurion Scientific offers a guide on maintaining an autoclave.
Proper Loading: Ensure even spacing and proper placement of materials for uniform heat distribution. Tuttnauer provides tips on loading and unloading your autoclave.
Optimize Cycle Parameters: Adjust temperature, pressure, and time settings based on material requirements for optimal curing. The CompositesWorld website gives insights into autoclave processing for composites.
Training: Enhance skills and knowledge through continuous training on autoclave operation and safety. ASC Process Systems offers training programs focused on autoclave operation for composites.
Quality Control: Implement strict quality control measures to detect and rectify issues promptly. ASTM standards provide guidelines for safety and quality in autoclave operations.
Energy Efficiency: Consider energy-saving practices to reduce operational costs and environmental impact. Energy Star has resources on making autoclave operations more energy efficient.
By focusing on these areas, a Composite Technician can achieve improvements in the effectiveness and efficiency of autoclave operations.
How to Display Autoclave Operation Skills on Your Resume
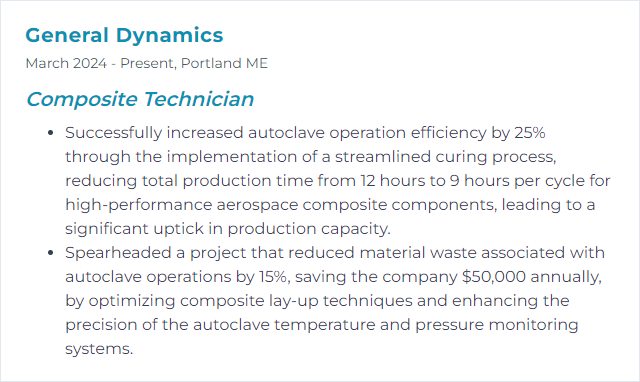
2. Vacuum Bagging
Vacuum bagging is a process used in composite fabrication where materials are placed in a vacuum bag and subjected to vacuum pressure to compress layers, remove air voids, and ensure even resin distribution, resulting in higher-quality, stronger, and more lightweight composite structures.
Why It's Important
Vacuum bagging is crucial for composite technicians as it compacts the composite layers, eliminates air voids, and ensures a uniform resin distribution, resulting in stronger, lighter, and more precise composite structures.
How to Improve Vacuum Bagging Skills
Improving vacuum bagging in composite fabrication involves optimizing materials, technique, and equipment to enhance the quality and efficiency of the process. Here are concise steps for a Composite Technician:
Material Selection: Choose the right bagging film, breather, and release film suitable for the specific resin system and curing temperature. Airtech offers a wide range of materials suitable for different applications.
Leak Prevention: Ensure all seals are airtight by applying sealant tape properly and inspecting for leaks. Use a leak detection spray to identify and address any issues.
Equipment Check: Regularly check and maintain vacuum pumps, gauges, and hoses. Opt for high-quality vacuum equipment to maintain consistent vacuum pressure.
Optimal Bagging Technique: Implement techniques like pleating to accommodate complex shapes and ensure the bag conforms well to the mold without bridging or wrinkles.
Consistent Work Environment: Maintain a clean, controlled environment to prevent contamination and ensure the materials function as expected.
Proper Training: Continuously update skills and knowledge on vacuum bagging processes. Composites One offers training and resources for composite technicians.
Trial and Error: Document and learn from each process to refine techniques and material choices.
By focusing on these key aspects, a Composite Technician can significantly improve the vacuum bagging process, leading to better quality composites and more efficient production.
How to Display Vacuum Bagging Skills on Your Resume
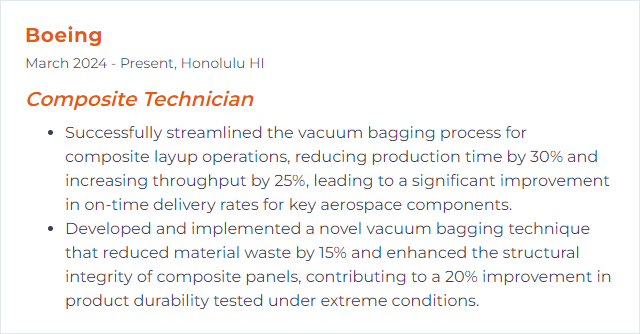
3. Resin Transfer Molding (RTM)
Resin Transfer Molding (RTM) is a manufacturing process where dry fiber reinforcements are placed into a closed mold, and then resin is injected under pressure to impregnate the fibers, forming a composite material. This method is used to produce high-strength, complex-shaped parts with good surface finishes.
Why It's Important
Resin Transfer Molding (RTM) is crucial for a Composite Technician because it allows for the precise control of resin content and fiber placement, ensuring high-quality, consistent composite parts with superior mechanical properties and surface finish. This process is also versatile and efficient for producing complex shapes and can be automated, leading to increased productivity and reduced manufacturing costs.
How to Improve Resin Transfer Molding (RTM) Skills
Improving Resin Transfer Molding (RTM) can be achieved by focusing on key areas such as mold design, resin selection, and process optimization. Here's a concise guide aimed at Composite Technicians:
Mold Design: Enhance the mold design for uniform flow and minimal resin waste. Utilize computational fluid dynamics (CFD) to simulate resin flow and identify optimal gate and vent locations.
Resin Selection: Choose resins with suitable viscosity and curing characteristics for your application. Consult resin suppliers' data sheets for properties and processing parameters.
Temperature Control: Precisely control mold temperature to manage resin viscosity and curing rate, ensuring complete wet-out and minimizing defects. Thermal management systems can help maintain consistent temperatures.
Pressure Management: Apply optimal injection pressure to ensure complete mold filling without inducing excessive fiber displacement or resin bleeding. Techniques and guidelines can be found in RTM process optimization studies.
Fiber Preform Optimization: Tailor the fiber architecture for uniform resin flow and mechanical properties. Use textile preforming techniques to design preforms that facilitate resin infusion.
Process Monitoring: Implement in-process monitoring with sensors to track resin flow, temperature, and pressure in real-time, allowing for adjustments as needed. Explore advanced RTM monitoring technologies for insights.
Training and Skills Development: Continually update skills and knowledge on RTM process advancements through workshops and certification programs offered by composites training institutions.
By focusing on these aspects, Composite Technicians can significantly improve the RTM process, leading to higher quality components, reduced waste, and increased efficiency.
How to Display Resin Transfer Molding (RTM) Skills on Your Resume

4. Prepreg Handling
Prepreg handling involves the careful manipulation and preparation of pre-impregnated composite fibers (materials already infused with a resin matrix) for lay-up processes, ensuring correct alignment, placement, and environmental conditions (temperature and humidity control) before curing to form composite structures.
Why It's Important
Prepreg handling is crucial for a Composite Technician because it ensures the integrity and performance of the composite material by maintaining its ideal resin content, fiber alignment, and avoiding contamination or damage, which directly affects the quality and strength of the final product.
How to Improve Prepreg Handling Skills
Improving prepreg handling involves a few key practices to ensure the material's integrity and performance in composite applications. Here are concise tips for a Composite Technician:
Storage: Store prepregs at recommended temperatures, typically in a freezer, to prevent premature curing. Thaw them gradually to room temperature before use to avoid condensation. CompositesWorld offers insights on proper storage practices.
Handling: Use clean gloves to handle prepregs, avoiding contamination with oils or dirt. Work on clean, smooth surfaces to prevent damage or incorporation of foreign particles.
Cutting: Use sharp, clean cutting tools specifically designated for prepreg materials to ensure clean edges and reduce fraying. Techniques for cutting can be found through resources like Performance Composites.
Lay-up: Follow the lay-up sequence and orientation precisely as specified in the manufacturing instructions. This ensures the composite part performs as designed. CompositesLab provides an overview of the lay-up process.
Curing: Cure the prepreg under the correct temperature and pressure settings as per the material specifications. This is critical for achieving optimal material properties. The SAMPE Journal often has articles on best practices for curing.
Safety: Always adhere to safety guidelines for handling chemicals and materials, including wearing appropriate personal protective equipment (PPE). The Occupational Safety and Health Administration (OSHA) provides guidelines on workplace safety.
By following these guidelines, Composite Technicians can ensure the quality and performance of prepreg materials in their projects.
How to Display Prepreg Handling Skills on Your Resume
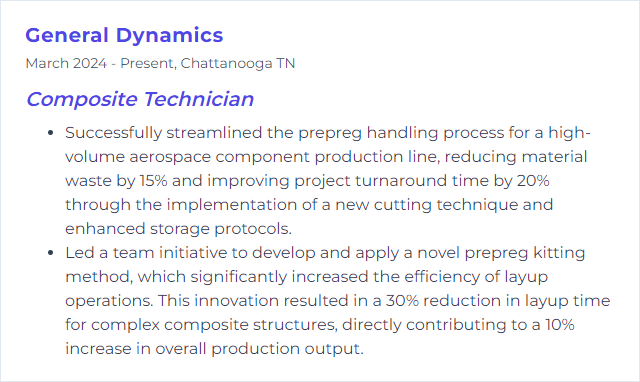
5. Non-Destructive Testing (NDT)
Non-Destructive Testing (NDT) is a set of analysis techniques used by Composite Technicians to evaluate the properties or integrity of composite materials or structures without causing damage.
Why It's Important
Non-Destructive Testing (NDT) is crucial for a Composite Technician because it allows for the detection of internal and surface defects in composite materials without causing damage, ensuring structural integrity, safety, and reliability of composite components while maintaining their operational lifespan.
How to Improve Non-Destructive Testing (NDT) Skills
Improving Non-Destructive Testing (NDT) for a Composite Technician involves enhancing skills, adopting advanced technologies, and ensuring adherence to best practices. Here’s a concise guide:
Continuous Learning: Stay updated with the latest NDT techniques and composite material characteristics through online courses and certifications. Websites like ASNT offer resources and training opportunities.
Advanced Technologies: Embrace advanced NDT technologies such as Phased Array Ultrasonic Testing (PAUT) and Digital Radiography (DR) for more detailed inspections. Explore technology resources at Olympus-IMS.
Practice and Experience: Gain hands-on experience with various composite materials and NDT methods. Engage in practical training sessions and workshops.
Quality Assurance Standards: Familiarize yourself with and adhere to international standards such as those from ASTM regarding NDT for composite materials to ensure consistency and reliability in testing.
Collaboration and Networking: Join professional networks and forums such as NDT.net to exchange knowledge and experiences with other professionals in the field.
By focusing on these areas, a Composite Technician can significantly improve their proficiency in NDT, leading to more accurate and reliable testing outcomes.
How to Display Non-Destructive Testing (NDT) Skills on Your Resume
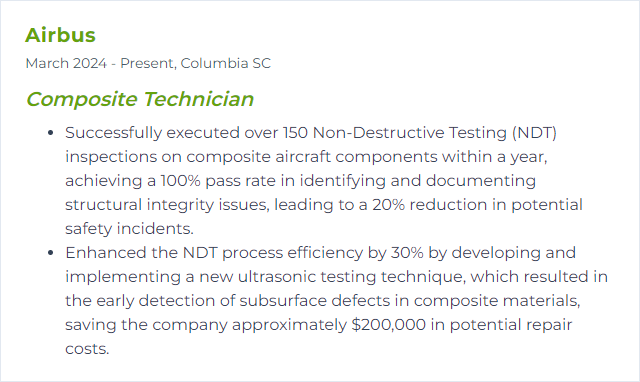
6. CAD Software
CAD software, short for Computer-Aided Design software, is a tool used by composite technicians to create precise drawings and models of composite materials and structures, facilitating the design, simulation, and manufacturing processes.
Why It's Important
CAD software is crucial for a Composite Technician as it enables precise design and modeling of composite materials and structures, facilitating the creation of complex shapes, optimizing material usage, and improving product quality and performance.
How to Improve CAD Software Skills
Improving CAD software for a Composite Technician involves enhancing features that are critical for designing, analyzing, and manufacturing composite materials and structures. Here are concise strategies:
User Interface (UI) Optimization: Streamline the UI for intuitive navigation and operation, focusing on tools specific to composite design and analysis. Autodesk provides an example of a user-friendly interface that can inspire improvements.
Material Database Expansion: Incorporate an extensive, updatable database of composite materials, including properties and applications, to aid in selection and simulation. Granta Design offers a comprehensive material database that could be integrated.
Simulation and Analysis Tools: Enhance simulation tools for stress, strain, and failure analysis specific to composite materials, incorporating various loading conditions and environmental factors. ANSYS Composite PrepPost is a leading tool that can provide inspiration for advanced simulation capabilities.
Manufacturing Process Integration: Integrate modules for various composite manufacturing processes (e.g., layup, molding) to allow for design for manufacturability (DFM) analysis, optimizing both the product and its manufacturing process. Siemens Digital Industries Software offers solutions that can be looked into for inspiration.
Collaboration and Cloud Integration: Facilitate seamless collaboration among team members and with external partners through cloud-based sharing and version control. Onshape is a cloud-native platform that exemplifies modern collaboration features.
Customization and Extensibility: Enable users to create custom plugins or scripts to automate repetitive tasks or to add specialized functionality that caters to the unique needs of composite technicians. SolidWorks allows for extensive customization, serving as a model for this feature.
Training and Support Resources: Offer comprehensive, easily accessible training materials and support resources, focusing on the specific needs of composite technicians. Providing tutorials, webinars, and a robust online community can enhance user competency and productivity. Autodesk University is an excellent resource for learning and community support.
By focusing on these areas, CAD software can be significantly improved to meet the specialized needs of Composite Technicians, enhancing their efficiency, accuracy, and innovation in composite material design and manufacturing.
How to Display CAD Software Skills on Your Resume
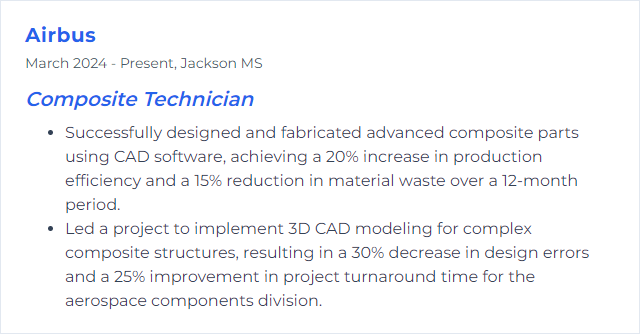
7. CNC Machining
CNC machining is a computer-controlled process used to precisely cut, shape, and drill materials, including composites, based on digital designs, essential for creating accurate and repeatable parts or molds in composite fabrication.
Why It's Important
CNC machining is crucial for a Composite Technician as it allows for precise, repeatable, and efficient cutting, shaping, and drilling of composite materials, ensuring high-quality components with tight tolerances essential for advanced applications.
How to Improve CNC Machining Skills
Improving CNC machining, especially from a Composite Technician's perspective, involves optimizing tool paths, selecting appropriate cutting tools, and ensuring proper machine maintenance. Here are concise strategies:
Optimize Tool Paths: Utilize software like Mastercam to simulate and optimize tool paths, reducing machining time and tool wear.
Select Appropriate Cutting Tools: Choose tools designed for composite materials, such as diamond-coated end mills, to enhance cutting efficiency and surface finish.
Ensure Proper Machine Maintenance: Regular maintenance, as detailed in Haas Automation's guidelines, is crucial to prevent machine inaccuracies and extend its lifespan.
Use CNC-specific Composite Strategies: Implement strategies like low helix drills and compression cutters, tailored for composites, to minimize delamination and improve hole quality. Sandvik Coromant offers tools and tips specifically for these materials.
Temperature and Humidity Control: Maintain a controlled environment, as composite materials can be sensitive to temperature and humidity changes, affecting machining precision. Control Techniques provides solutions for environmental control in industrial settings.
By focusing on these areas, Composite Technicians can significantly enhance CNC machining performance and output quality.
How to Display CNC Machining Skills on Your Resume
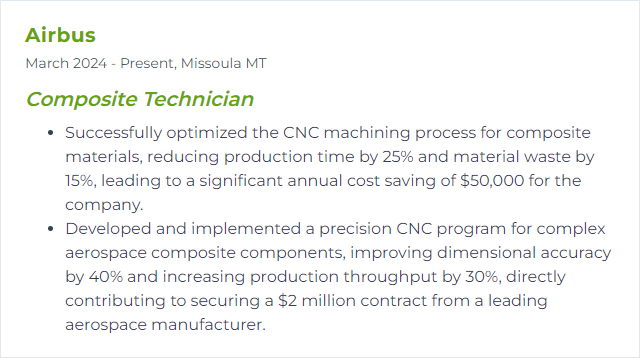
8. D Printing
3D printing, in the context of a Composite Technician, is a manufacturing process that creates three-dimensional objects layer by layer from materials such as polymers, metals, or composites, directly from digital models. It enables the production of complex shapes and composite structures with precise control over material placement and properties.
Why It's Important
3D printing is important for a Composite Technician because it enables the rapid prototyping and production of complex composite parts with precise geometries, reducing costs and manufacturing time while increasing design flexibility and material efficiency.
How to Improve D Printing Skills
Improving 3D printing, especially from a Composite Technician's perspective, involves focusing on material selection, print settings optimization, and post-processing techniques. Here are concise strategies:
Material Selection: Use advanced composite materials that offer enhanced strength and durability. Research and select materials that best fit the specific requirements of your project.
Optimize Print Settings: Fine-tune printer settings such as layer height, print speed, and temperature for optimal strength and accuracy. Simplify3D's guide offers a comprehensive troubleshooting tool.
Post-Processing Techniques: Implement post-processing methods like annealing for thermoplastics to improve mechanical properties or use techniques like infiltration (with epoxy, for instance) to enhance part strength and surface finish.
Incorporate Software for Simulation: Use software tools like Autodesk Fusion 360 to simulate the printing process and identify potential issues before printing.
Continuous Learning and Experimentation: Stay updated with the latest advancements in 3D printing technologies and materials. Experiment with new techniques and materials to discover what works best for your specific applications.
By focusing on these areas, you can significantly improve the quality and performance of 3D printed components in composite applications.
How to Display D Printing Skills on Your Resume
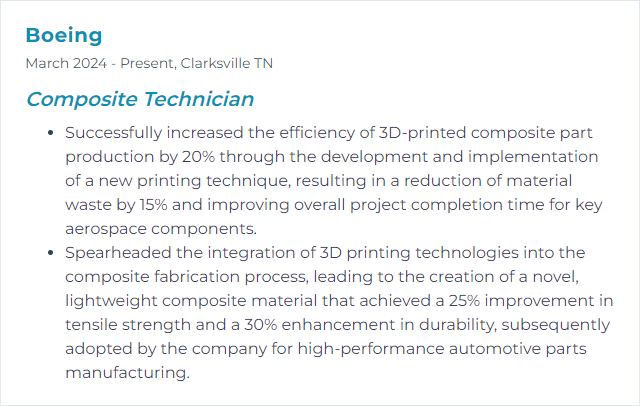
9. Ply Cutting
Ply cutting involves precisely trimming individual layers of composite material (plies) to specific shapes and sizes according to design specifications, essential for creating complex composite structures with desired mechanical properties and dimensions.
Why It's Important
Ply cutting is crucial for a Composite Technician because it ensures the precise shaping and layering of composite materials, optimizing structural integrity and performance in the final product.
How to Improve Ply Cutting Skills
Improving ply cutting, especially for a Composite Technician, involves focusing on precision, efficiency, and minimizing waste. Here are concise steps with relevant resources:
Understand Material Properties: Knowing the specific type of composite ply you're working with is crucial. Different materials may require different cutting techniques. CompositesWorld provides insights into various composite materials.
Use the Right Tools: Invest in high-quality cutting tools suitable for composite materials. Tools should be kept sharp and well-maintained. For recommendations, check out JEC Group.
Optimize Cutting Patterns: Use software like NestingWorks for SolidWorks to optimize your cutting layout, reducing waste and saving material.
Maintain a Clean Work Area: Ensure your cutting surface is clean and free from obstructions. This minimizes the risk of inaccuracies or damage to the material.
Follow Safety Procedures: Always wear appropriate safety gear and follow best practices to prevent accidents. The Occupational Safety and Health Administration (OSHA) provides guidelines on workplace safety.
Continuous Learning: Stay updated with the latest techniques and tools in ply cutting by subscribing to industry publications like Advanced Composites Magazine.
Practice Precision: Make use of precision tools like digital calipers and laser cutters for accurate cuts. Precision is key in reducing waste and ensuring the quality of the final product.
By incorporating these strategies, Composite Technicians can enhance their ply cutting process, leading to improved efficiency and material utilization.
How to Display Ply Cutting Skills on Your Resume
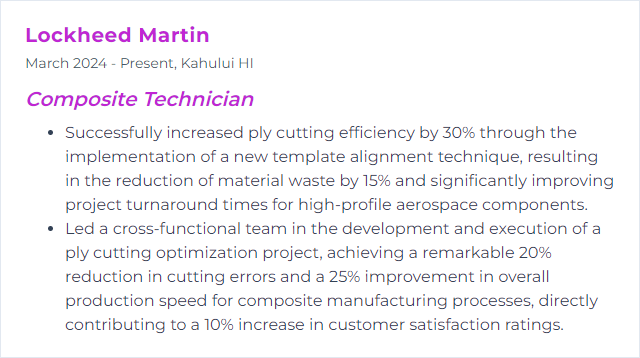
10. Hand Lay-up
Hand lay-up is a manual process used by composite technicians to create composite materials. It involves placing layers of fiber-reinforced material into a mold and then applying resin by hand to build the composite structure. This method allows for precise control over fiber orientation and material placement.
Why It's Important
Hand lay-up is important because it allows a Composite Technician to create complex shapes and custom composite parts with precise control over fiber orientation and laminate thickness, essential for optimizing the strength and weight of the component.
How to Improve Hand Lay-up Skills
Improving Hand Lay-up technique involves several key steps focused on preparation, execution, and quality control. Below are concise guidelines to enhance the process:
Material Preparation: Ensure all materials (resin, fibers, etc.) are at optimal conditions. Store materials properly to avoid contamination or degradation. CompositesWorld offers insights on material handling.
Mold Preparation: Clean and apply release agents uniformly. A well-prepared mold ensures easy part removal and surface quality. The American Composites Manufacturers Association provides guidelines on mold maintenance.
Accurate Cutting: Cut fiber materials precisely to fit the mold, reducing waste and ensuring proper reinforcement placement. Techniques for cutting can be found through resources like Composites One.
Consistent Lay-up: Apply each layer carefully, ensuring no air entrapment or wrinkles. Use tools like rollers and brushes effectively to compact the layers. The Institute for Advanced Composites Manufacturing Innovation offers training on lay-up techniques.
Curing Control: Follow the recommended curing cycle for the resin system used. Proper curing ensures optimal mechanical properties. SAMPE is a professional organization that provides information on materials and process engineering, including curing processes.
Inspection and Quality Control: Implement regular inspections throughout the lay-up and curing process. Use non-destructive testing (NDT) methods to detect voids or delamination. NDT Resource Center offers a variety of resources on NDT techniques.
Continuous Learning and Training: Stay updated with the latest techniques and materials. Attend workshops, webinars, and training sessions. CompositesLab is a comprehensive resource for learning about composites.
By focusing on these areas, a Composite Technician can significantly improve the quality and efficiency of the Hand Lay-up process.
How to Display Hand Lay-up Skills on Your Resume
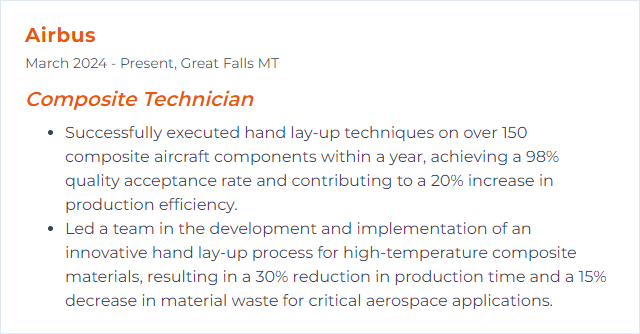
11. Filament Winding
Filament winding is a manufacturing process used to produce composite materials where continuous fiber reinforcements (e.g., glass, carbon) are precisely wound around a rotating form or mandrel in specific patterns, creating high-strength cylindrical or complex structures. The fibers are typically coated with a resin as they are wound, which then cures, solidifying the structure. This technique is essential for producing lightweight, durable components with tailored properties for aerospace, automotive, and industrial applications.
Why It's Important
Filament winding is crucial for a Composite Technician as it enables the efficient production of strong, lightweight, and durable composite structures with precise fiber placement and orientation, optimizing material use and structural performance for various applications.
How to Improve Filament Winding Skills
To improve Filament Winding as a Composite Technician, focus on the following key aspects:
Material Preparation: Ensure fibers and resin systems are properly prepared. Pre-treat fibers to enhance adhesion with the resin. Material Handling
Tension Control: Maintain consistent tension on the fibers during the winding process. This prevents defects and ensures uniform composite strength. Tension Control in Filament Winding
Winding Pattern Optimization: Utilize software for optimal winding patterns to achieve desired strength and stiffness characteristics. CADWIND – The Composite Blade Design Software
Cure Cycle Optimization: Optimize the cure cycle based on the resin system used to ensure complete cure and maximize material properties. Curing Process of Composites
Quality Control: Implement rigorous inspection and testing protocols (e.g., ultrasonic testing) to detect any defects or inconsistencies. Nondestructive Evaluation Techniques for Composites
Continuous Learning and Adaptation: Stay updated with the latest materials, technology, and techniques in filament winding through continuous education and training. SAMPE – Society for the Advancement of Material and Process Engineering
By focusing on these areas, a Composite Technician can significantly improve the quality and performance of filament-wound composite structures.
How to Display Filament Winding Skills on Your Resume
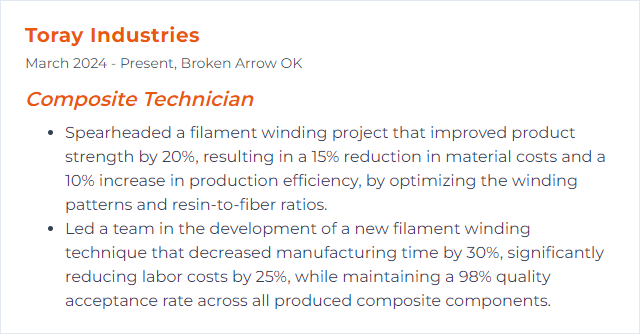
12. Adhesive Bonding
Adhesive bonding is a process used by composite technicians to join components together using a glue or resin, creating a strong and durable bond without the need for mechanical fasteners, thus maintaining the integrity and performance of composite materials.
Why It's Important
Adhesive bonding is crucial for a Composite Technician because it provides a strong, lightweight, and versatile method for joining composite materials, ensuring structural integrity and performance while minimizing damage and stress concentrations often associated with mechanical fasteners.
How to Improve Adhesive Bonding Skills
Improving adhesive bonding for a Composite Technician involves a few key steps:
Surface Preparation: Ensure surfaces are clean, dry, and free of contaminants. Use appropriate cleaning agents and techniques like abrasion or plasma treatment. Surface Preparation Guidelines.
Adhesive Selection: Choose the correct adhesive type based on materials to be bonded, environmental conditions, and load requirements. Adhesive Selection Guide.
Application Technique: Apply adhesive uniformly without introducing air bubbles. Follow manufacturer's instructions for application methods and curing times. Adhesive Application Tips.
Curing Process: Ensure the adhesive is cured under the right conditions, considering temperature, pressure (if needed), and time. Understanding Adhesive Curing.
Quality Control: Conduct tests to ensure bond integrity, such as peel, shear, and tensile strength tests. Adhesive Testing Methods.
By focusing on these areas, a Composite Technician can improve the quality and reliability of adhesive bonds in composite materials.
How to Display Adhesive Bonding Skills on Your Resume
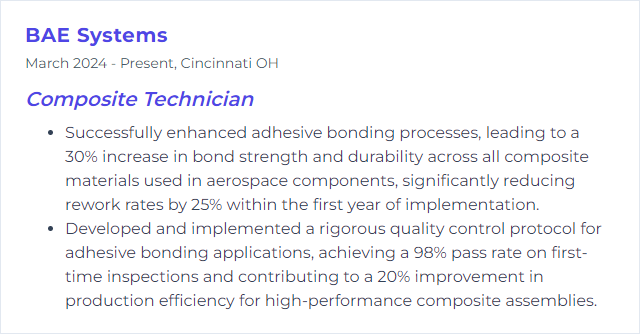