Top 12 Central Supply Technician Skills to Put on Your Resume
In the fast-paced healthcare industry, Central Supply Technicians play a critical role in ensuring the availability and sterility of medical supplies, directly impacting patient care and safety. A well-crafted resume highlighting a mix of technical expertise, meticulous organizational abilities, and strong communication skills can set candidates apart in this vital field.
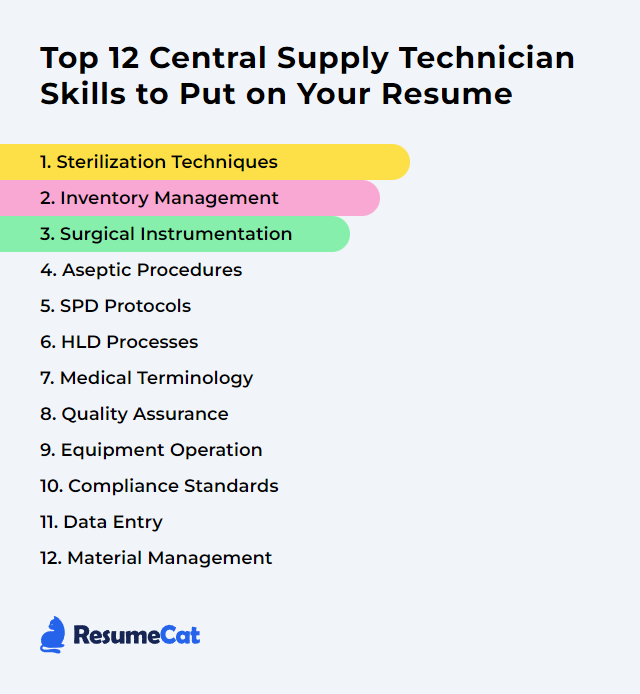
Central Supply Technician Skills
- Sterilization Techniques
- Inventory Management
- Surgical Instrumentation
- Aseptic Procedures
- SPD Protocols
- HLD Processes
- Medical Terminology
- Quality Assurance
- Equipment Operation
- Compliance Standards
- Data Entry
- Material Management
1. Sterilization Techniques
Sterilization techniques are methods used by Central Supply Technicians to eliminate all forms of microbial life, including bacteria, viruses, fungi, and spores, from medical instruments and equipment. These techniques include autoclaving (steam sterilization), ethylene oxide gas, hydrogen peroxide gas plasma, and dry heat, ensuring that surgical and medical devices are safe for patient use.
Why It's Important
Sterilization techniques are crucial for a Central Supply Technician as they ensure the elimination of all forms of microbial life, including bacteria, viruses, and spores, on medical instruments and equipment. This prevents infections and ensures patient safety during medical procedures.
How to Improve Sterilization Techniques Skills
Improving sterilization techniques as a Central Supply Technician involves continuous learning and adhering to best practices in the field. Here’s a concise guide:
Stay Updated: Regularly review and update your knowledge based on the latest CDC guidelines and AAMI standards.
Proper Training: Ensure comprehensive training on the use of all sterilization equipment and materials. IAHCSMM offers resources and certifications.
Quality Assurance Programs: Implement and participate in quality assurance programs to monitor the effectiveness of sterilization processes.
Routine Equipment Maintenance: Follow manufacturer guidelines for routine maintenance and validation of sterilization equipment to ensure optimal performance.
Best Practices for Instrument Preparation: Adhere to best practices for cleaning and preparing instruments before sterilization. WHO guidelines can offer additional insights.
Use of Indicators: Employ biological and chemical indicators to verify the effectiveness of the sterilization process as recommended by CDC.
Improving sterilization techniques is a continual process of education, practice, and adherence to evolving guidelines and standards.
How to Display Sterilization Techniques Skills on Your Resume
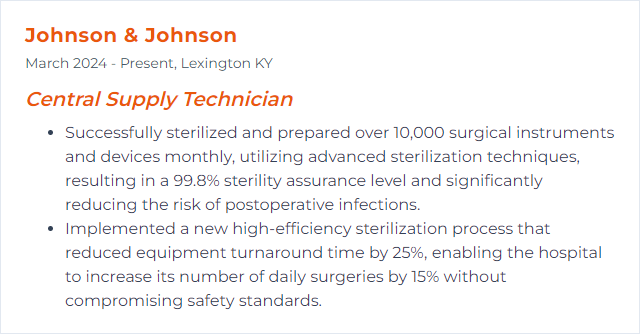
2. Inventory Management
Inventory Management, in the context of a Central Supply Technician, involves overseeing, organizing, and replenishing all medical supplies and equipment to ensure they are available and ready for use, while maintaining optimal stock levels and adhering to health standards.
Why It's Important
Inventory management is crucial for a Central Supply Technician because it ensures the timely availability of necessary medical supplies and equipment, minimizes waste and storage costs, and supports the seamless operation of healthcare services.
How to Improve Inventory Management Skills
Improving inventory management, especially for a Central Supply Technician, involves a few key strategies:
Streamline Ordering Processes: Use automated systems to track inventory levels and reorder supplies proactively. Inventory Management Systems can help.
Implement a First-In-First-Out (FIFO) System: Ensure older stock is used before newer stock to minimize waste. FIFO Method explains this in more detail.
Regular Audits and Cycle Counts: Conduct regular checks to ensure inventory accuracy, identifying discrepancies promptly. The Importance of Cycle Counting article discusses this.
Organize Supplies Efficiently: Keep the storage area organized and label everything clearly for easy access and tracking. 5S Methodology can be particularly helpful.
Training and Standard Operating Procedures (SOPs): Ensure all staff are trained in inventory management practices and adhere to SOPs. Creating Effective SOPs provides guidance.
By focusing on these areas, a Central Supply Technician can significantly improve efficiency and accuracy in inventory management.
How to Display Inventory Management Skills on Your Resume
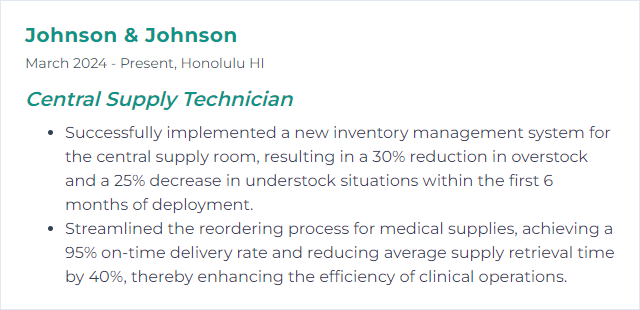
3. Surgical Instrumentation
Surgical instrumentation refers to the array of tools and devices specifically designed for use in surgical procedures. For a Central Supply Technician, it involves the sterilization, preparation, maintenance, and distribution of these instruments to ensure they are safe and ready for use in the operating room.
Why It's Important
Surgical instrumentation is crucial for a Central Supply Technician because it ensures that surgical tools are properly sterilized, maintained, and ready for use, guaranteeing safe and efficient surgical procedures.
How to Improve Surgical Instrumentation Skills
Improving surgical instrumentation involves several key steps, focusing on sterilization, maintenance, and handling. Here are concise strategies for a Central Supply Technician:
Enhance Sterilization Processes: Follow the latest CDC guidelines to ensure instruments are properly sterilized, reducing the risk of infection.
Regular Maintenance: Implement a routine check-up and maintenance schedule. The Association for the Advancement of Medical Instrumentation (AAMI) provides standards and resources for maintaining medical instruments.
Proper Handling and Storage: Use appropriate techniques for handling and storing instruments to prevent damage. The International Association of Healthcare Central Service Materiel Management (IAHCSMM) offers guidelines on best practices.
Training and Education: Continuously update your knowledge and skills through certified programs and workshops. The Certification Board for Sterile Processing and Distribution (CBSPD) and IAHCSMM offer certification and educational resources.
Implement a Quality Assurance Program: Regularly review and assess the sterilization and handling process to identify areas for improvement. This includes tracking the condition of instruments and monitoring sterilization effectiveness.
By focusing on these areas, a Central Supply Technician can significantly contribute to the improvement of surgical instrumentation, ensuring safety and efficiency in surgical procedures.
How to Display Surgical Instrumentation Skills on Your Resume
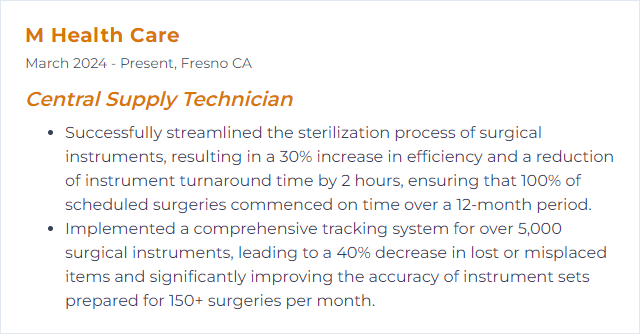
4. Aseptic Procedures
Aseptic procedures for a Central Supply Technician involve techniques and practices used to prevent contamination from pathogens. This includes sterilization and disinfection of medical instruments and equipment, ensuring a sterile environment to maintain patient safety during medical procedures.
Why It's Important
Aseptic procedures are crucial for a Central Supply Technician as they prevent the transmission of pathogens, ensuring that medical instruments and environments remain sterile. This reduces the risk of infections in patients, promoting safety and enhancing healthcare outcomes.
How to Improve Aseptic Procedures Skills
Improving aseptic procedures, especially for a Central Supply Technician, involves adhering to strict standards and protocols to prevent contamination and ensure patient safety. Here are concise strategies:
- Regular Training: Ensure ongoing training for all staff on the latest aseptic techniques and updates in sterilization procedures.
- Follow Protocols: Strictly adhere to sterilization protocols set by organizations such as the CDC and AAMI, including proper cleaning, disinfection, and storage of instruments.
- Monitor Sterilization Equipment: Regularly inspect and test sterilization equipment to ensure it's functioning correctly, following manufacturers' recommendations.
- Use of Indicators: Implement the use of biological and chemical indicators to verify the effectiveness of sterilization processes.
- Maintain a Clean Environment: Keep the sterilization and storage areas clean and organized, minimizing the risk of contamination.
- Personal Hygiene: Promote strict personal hygiene among staff, including hand hygiene and the use of personal protective equipment (PPE).
By focusing on these areas, Central Supply Technicians can significantly improve aseptic procedures, enhancing patient care quality and safety.
How to Display Aseptic Procedures Skills on Your Resume
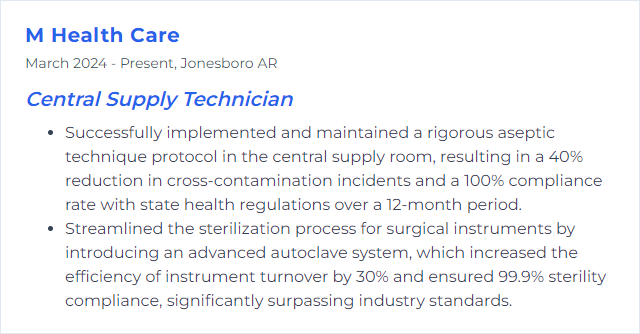
5. SPD Protocols
SPD protocols refer to the standardized procedures and guidelines used in the Sterile Processing Department to ensure the cleaning, sterilization, and distribution of medical and surgical instruments and equipment. These protocols are essential for maintaining the safety and effectiveness of medical devices, preventing infections, and ensuring patient safety. Central Supply Technicians must adhere to these protocols to ensure all instruments are properly processed and ready for use in medical procedures.
Why It's Important
SPD protocols are crucial for a Central Supply Technician as they ensure the proper sterilization, preparation, and distribution of medical instruments and supplies, preventing infection and ensuring patient safety and high-quality care.
How to Improve SPD Protocols Skills
Improving Sterile Processing Department (SPD) protocols involves enhancing the efficiency, safety, and compliance of the sterilization process. For a Central Supply Technician, focusing on the following key areas can lead to significant improvements:
Education and Training: Ensure all staff are up-to-date with the latest sterilization techniques and standards. Regular training sessions can help maintain high standards.
Standardization: Implement standard operating procedures (SOPs) for all processes to minimize variability and ensure consistency in practices.
Equipment Maintenance: Regularly maintain and inspect sterilization equipment to ensure it operates efficiently and effectively, following manufacturers' recommendations.
Quality Control: Incorporate rigorous quality control measures, including biological indicators and chemical integrators, to monitor sterilization effectiveness.
Communication: Foster clear and open communication among team members to improve workflow and address issues promptly.
Compliance: Stay informed about and comply with relevant regulations and guidelines from bodies such as the CDC, FDA, and AAMI.
By focusing on these areas, a Central Supply Technician can play a pivotal role in enhancing SPD protocols, leading to improved patient safety and operational efficiency.
How to Display SPD Protocols Skills on Your Resume
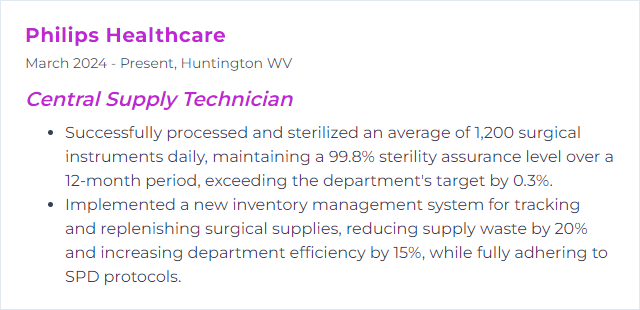
6. HLD Processes
HLD Processes, in the context of a Central Supply Technician, refer to High-Level Disinfection processes. These are critical sterilization procedures aimed at eliminating all microorganisms, except for a small number of bacterial spores, from medical instruments and equipment to ensure they are safe for patient use. This involves the use of chemical disinfectants or heat under strictly controlled conditions.
Why It's Important
High-Level Disinfection (HLD) processes are crucial for a Central Supply Technician to ensure that medical instruments and equipment are safe for patient use by effectively eliminating all microorganisms, except for a small number of bacterial spores, thereby reducing the risk of infections and ensuring patient safety.
How to Improve HLD Processes Skills
Improving High-Level Disinfection (HLD) processes for a Central Supply Technician involves enhancing efficiency, ensuring compliance with standards, and maintaining safety. Here are concise strategies:
Regular Training: Ensure ongoing training for technicians on HLD protocols and updates in standards to prevent errors and improve compliance.
Standardization: Adopt standardized procedures across all levels to minimize variability and enhance consistency in HLD processes.
Quality Control: Implement regular quality control checks and audits to ensure adherence to HLD protocols and identify areas for improvement.
Use of Technology: Leverage technology for automated tracking and monitoring of equipment through the disinfection process, reducing human error and increasing efficiency.
Feedback Loop: Establish a feedback mechanism for frontline staff to report issues or suggest improvements in the HLD process, promoting a culture of continuous improvement.
Maintenance of Equipment: Ensure regular maintenance and validation of disinfection equipment to keep them functioning at optimal levels, preventing malfunctions and ensuring effective disinfection.
Clear Communication: Maintain clear and effective communication among staff regarding roles, responsibilities, and updates in HLD processes to avoid confusion and enhance team efficiency.
By focusing on these areas, Central Supply Technicians can significantly improve HLD processes, ensuring patient safety and compliance with regulatory standards.
How to Display HLD Processes Skills on Your Resume
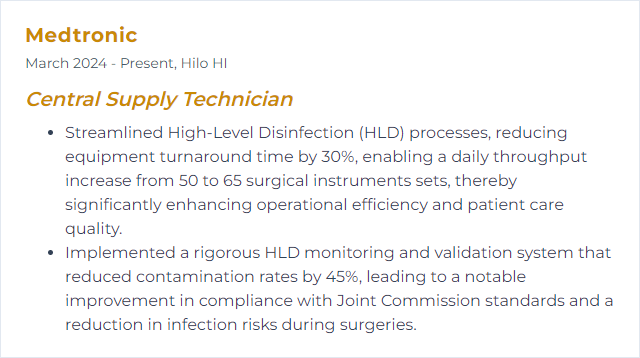
7. Medical Terminology
Medical terminology is the specialized language used to describe the human body, its functions, diseases, procedures, and equipment, essential for a Central Supply Technician to accurately identify, manage, and communicate about medical supplies and equipment.
Why It's Important
Medical terminology is crucial for a Central Supply Technician because it ensures accurate communication and understanding of medical instruments and supplies, enhances efficiency in fulfilling requests from medical staff, and minimizes errors in the sterilization and distribution process, ultimately contributing to patient safety and effective healthcare delivery.
How to Improve Medical Terminology Skills
Improving medical terminology, particularly for a Central Supply Technician, is crucial for effective communication and performance. Here are concise steps with resources:
Utilize Online Courses: Platforms like Coursera and edX offer courses on medical terminology that are structured to improve your understanding gradually.
Reference Medical Dictionaries: Keep a medical dictionary or use online resources such as Merriam-Webster's Medical Dictionary for quick reference and clarification of terms.
Practice with Flashcards: Use flashcards for memorization and recall. Websites like Quizlet have pre-made flashcards on medical terminology.
Engage in Continuous Learning: Subscribe to medical newsletters or websites like Medical News Today to stay updated with new terms and healthcare information.
Join Professional Networks: Participate in forums and groups on platforms like LinkedIn to engage with peers and learn from their experiences and knowledge.
Focusing on these steps can significantly enhance your comprehension and usage of medical terminology in your role as a Central Supply Technician.
How to Display Medical Terminology Skills on Your Resume
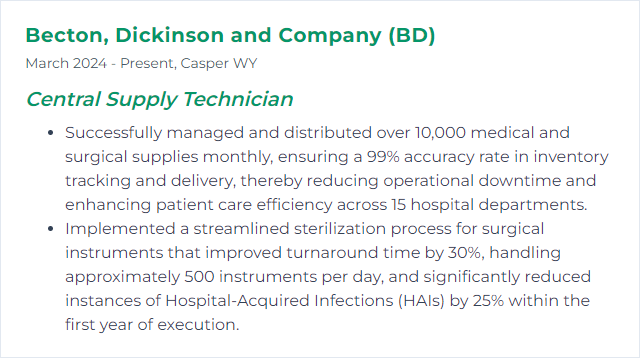
8. Quality Assurance
Quality Assurance (QA) in the context of a Central Supply Technician involves ensuring that all medical and surgical supplies and equipment are properly sterilized, maintained, and distributed according to established health and safety standards to guarantee patient safety and support effective medical procedures.
Why It's Important
Quality Assurance (QA) is crucial for a Central Supply Technician as it ensures the sterility and functionality of medical instruments and supplies, directly impacting patient safety and the success of medical procedures.
How to Improve Quality Assurance Skills
Improving Quality Assurance (QA) as a Central Supply Technician involves focusing on key areas such as standardization, continuous education, and meticulous tracking of processes and outcomes. Here are concise strategies:
Implement Standard Operating Procedures (SOPs): Develop and adhere to SOPs for all central supply tasks to ensure consistency and quality. CDC's Guidelines offer comprehensive standards for cleaning, disinfection, and sterilization.
Continuous Training: Engage in ongoing training programs to stay updated with the latest best practices in sterilization and infection control. The IAHCSMM provides valuable resources and certification programs for Central Supply Technicians.
Quality Control Checks: Regularly perform quality control checks on equipment and supplies to detect and rectify issues promptly. The AAMI offers standards and guidelines that are essential for maintaining equipment reliability and safety.
Feedback Loops: Establish a system for receiving and acting on feedback from healthcare staff regarding the quality and availability of supplies. This helps in identifying areas for improvement.
Audit and Review: Conduct periodic audits of processes and review procedures to identify inefficiencies and areas for improvement. The Joint Commission provides accreditation and certification that signify compliance with high performance standards.
By focusing on these areas, a Central Supply Technician can significantly enhance the quality assurance in their domain, ensuring that healthcare practices are safe, efficient, and compliant with regulatory standards.
How to Display Quality Assurance Skills on Your Resume
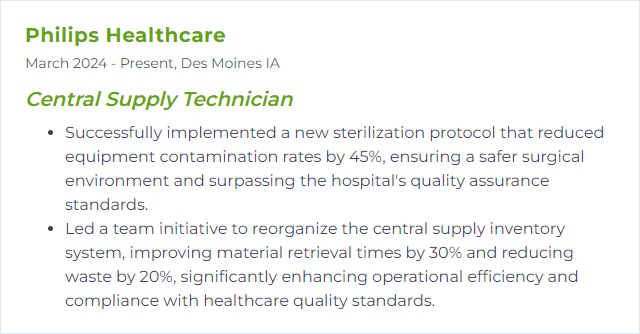
9. Equipment Operation
Equipment Operation, in the context of a Central Supply Technician, refers to the proficient use and maintenance of sterilization machines, washing equipment, and other medical supply processing tools to ensure the cleanliness and functionality of medical instruments and equipment.
Why It's Important
Equipment operation is crucial for a Central Supply Technician as it ensures the proper sterilization, preparation, and distribution of medical instruments, maintaining a safe and efficient healthcare environment.
How to Improve Equipment Operation Skills
To improve equipment operation as a Central Supply Technician, follow these concise steps:
Adhere to Manufacturer's Guidelines: Always follow the manufacturer's instructions for operation, maintenance, and sterilization to ensure equipment longevity and proper functioning.
Regular Maintenance and Checks: Schedule and perform regular maintenance checks to identify and rectify issues before they escalate, ensuring equipment is always in optimal condition.
Proper Training: Ensure all technicians receive ongoing training on the latest equipment and industry best practices to maintain high operational standards.
Utilize Equipment Logs: Keep detailed logs for each piece of equipment to track usage, maintenance, and any issues, facilitating proactive management and accountability.
Quality Assurance Programs: Implement a quality assurance program to systematically review and improve equipment handling, sterilization processes, and technician performance.
By focusing on these key areas, Central Supply Technicians can significantly improve the operation and reliability of their equipment.
How to Display Equipment Operation Skills on Your Resume
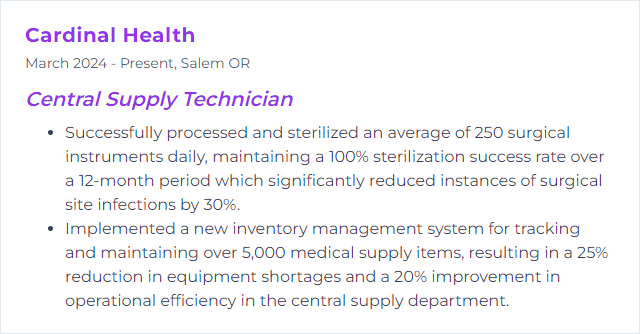
10. Compliance Standards
Compliance standards for a Central Supply Technician refer to the set of regulations and guidelines established by healthcare authorities and institutions to ensure the sterilization, preparation, and distribution of medical and surgical supplies meet safety, hygiene, and quality requirements. These standards aim to prevent infection and ensure patient safety.
Why It's Important
Compliance standards ensure a Central Supply Technician adheres to established policies and procedures that promote patient safety, prevent infections, and guarantee the effective sterilization and distribution of medical supplies and equipment. This adherence helps maintain a high level of care and trust within healthcare settings.
How to Improve Compliance Standards Skills
To enhance compliance standards for a Central Supply Technician, focus on these key areas:
Education and Training: Regularly update and participate in continuing education programs to stay informed about the latest compliance standards and best practices in sterilization and infection control. Association for the Advancement of Medical Instrumentation (AAMI) provides resources and certifications relevant to central service technicians.
Adherence to Protocols: Strictly follow established protocols and guidelines for sterilization, equipment handling, and inventory management. The Centers for Disease Control and Prevention (CDC) offers comprehensive guidelines on disinfection and sterilization.
Quality Control and Assurance: Implement rigorous quality control measures to ensure that all equipment and instruments meet the required sterilization standards. Use resources from organizations like the International Association of Healthcare Central Service Materiel Management (IAHCSMM) for standards and certification.
Audit and Feedback: Regularly conduct internal audits and participate in external audits to identify compliance gaps. Use the feedback for continuous improvement.
Documentation: Maintain meticulous records of sterilization processes, equipment maintenance, and compliance training activities to ensure accountability and traceability.
Focusing on these areas, supported by continuous education and adherence to established protocols, will significantly improve compliance standards for a Central Supply Technician.
How to Display Compliance Standards Skills on Your Resume
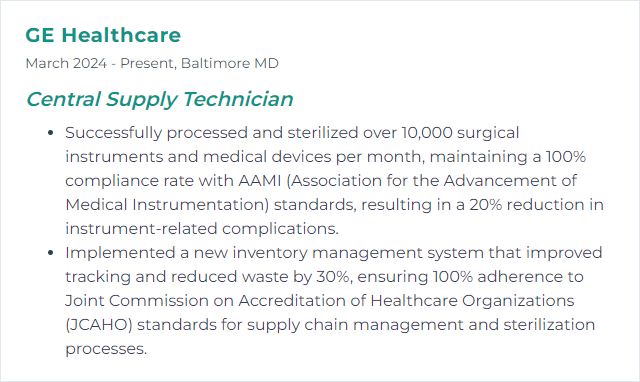
11. Data Entry
Data entry, in the context of a Central Supply Technician, involves accurately recording and updating information related to medical supplies, equipment inventory, sterilization processes, and distribution records into a digital database or tracking system.
Why It's Important
Data entry is crucial for a Central Supply Technician as it ensures accurate tracking and management of medical supplies, enabling efficient inventory control, timely order fulfillment, and adherence to regulatory standards, ultimately supporting optimal patient care.
How to Improve Data Entry Skills
Improving data entry for a Central Supply Technician involves enhancing accuracy, speed, and efficiency. Follow these concise steps:
Standardize Processes: Implement standardized procedures for data entry tasks to minimize errors. CDC Guidelines can help ensure compliance with best practices for infection control that impacts data recording.
Use Data Entry Software: Adopt specialized data entry software designed for healthcare settings to streamline tasks and reduce manual errors.
Training and Education: Regularly train staff on new technologies and protocols. Resources like AAMI offer courses and certifications for Central Service Technicians.
Implement Double-Checking Systems: Encourage a culture of peer review where entries are double-checked to ensure accuracy.
Regular Audits: Conduct regular audits of data entered to identify areas for improvement. The Joint Commission provides standards and resources that can guide quality improvement efforts.
Feedback Mechanism: Establish a feedback mechanism for the technicians to report issues and suggest improvements in the data entry process.
By focusing on these steps, Central Supply Technicians can significantly improve their data entry practices, contributing to better patient care and operational efficiency.
How to Display Data Entry Skills on Your Resume
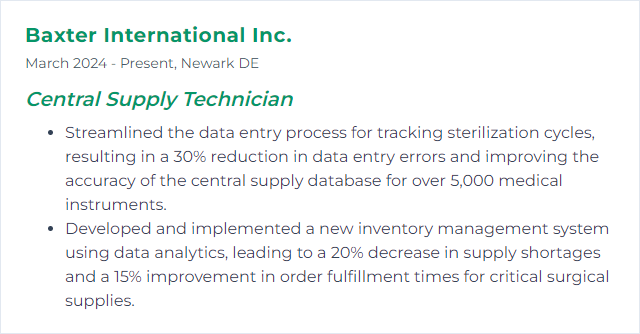
12. Material Management
Material management, in the context of a Central Supply Technician, involves the systematic approach to planning, procuring, storing, and providing the essential materials and equipment needed in healthcare settings to ensure efficient and effective operations.
Why It's Important
Material Management is crucial for a Central Supply Technician as it ensures the timely availability of necessary medical supplies and equipment, maintaining cost-effectiveness and operational efficiency, while also supporting infection control and patient care standards.
How to Improve Material Management Skills
Improving material management, especially for a Central Supply Technician, involves enhancing inventory accuracy, streamlining procurement processes, and ensuring the efficient distribution and sterilization of supplies. Here are concise strategies:
Implement an Inventory Management System: Utilize software to track inventory levels, orders, and supplies in real-time. This reduces overstock and stockouts, ensuring optimal inventory levels. Example systems: Oracle NetSuite.
Adopt Lean Inventory Techniques: Embrace lean principles by minimizing waste and improving processes. This includes just-in-time inventory to reduce storage costs and ensure supplies are fresh. Learn more about lean inventory: Lean Production.
Enhance Supplier Relationships: Develop strong relationships with suppliers for better pricing, reliability, and quality of medical supplies. This includes negotiating contracts and maintaining open lines of communication. Guidance on supplier relationships: APICS for Supply Chain Management.
Standardize Materials: Work towards standardizing materials and supplies across departments. This reduces complexity and costs associated with managing a wide variety of items. Explore standardization benefits: AHRMM.
Continuous Training and Education: Ensure continuous professional development to stay updated with the latest material management practices and technologies. Relevant certifications and training can be found at ISM - Institute for Supply Management.
Implement Quality Control Measures: Establish strict quality control measures for receiving, storing, and distributing materials. This ensures that only high-quality supplies are used, reducing the risk of infection or complications. Overview on quality control: ASQ Quality Control.
Use Data Analytics: Leverage data analytics to predict demand, analyze supply chain efficiency, and identify areas for improvement. This informed decision-making leads to better material management. Introduction to data analytics in supply chain: MIT Data Analytics.
By adopting these strategies, Central Supply Technicians can significantly improve material management, contributing to better patient care and operational efficiency.
How to Display Material Management Skills on Your Resume
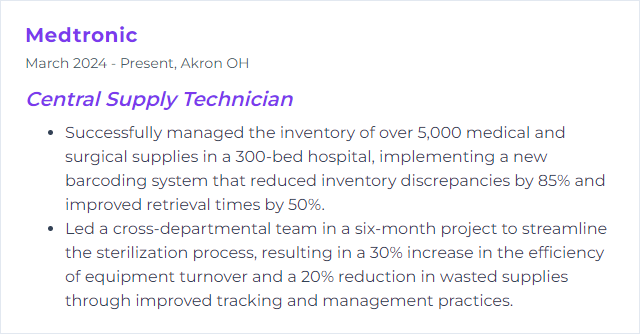