Top 12 Bench Jeweler Skills to Put on Your Resume
Crafting a standout resume as a bench jeweler requires highlighting a unique blend of technical proficiency and artistic finesse. Showcasing your specialized skills not only demonstrates your capability in intricate jewelry making but also sets you apart in a competitive job market.
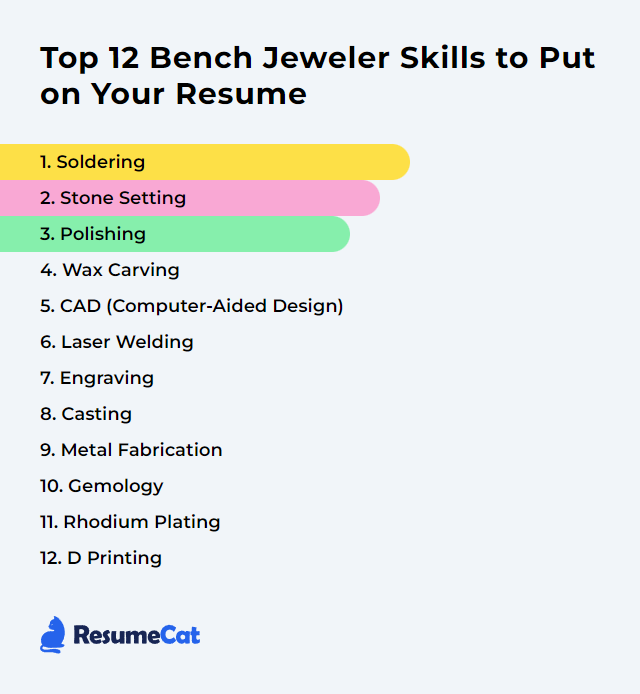
Bench Jeweler Skills
- Soldering
- Stone Setting
- Polishing
- Wax Carving
- CAD (Computer-Aided Design)
- Laser Welding
- Engraving
- Casting
- Metal Fabrication
- Gemology
- Rhodium Plating
- D Printing
1. Soldering
Soldering, in the context of bench jewelry, is a process where a jeweler uses a filler metal (solder) with a lower melting point than the adjoining metal pieces to join them together. This technique is essential for crafting and repairing jewelry, allowing for the precise and durable connection of components under controlled heat.
Why It's Important
Soldering is crucial for a bench jeweler as it allows for the precise and strong joining of metal pieces, essential in creating or repairing intricate jewelry designs, ensuring durability and aesthetic integrity.
How to Improve Soldering Skills
Improving soldering skills, especially for a bench jeweler, involves practice, precision, and the right tools. Here are concise tips:
Use Proper Tools: Invest in a high-quality soldering iron, solder, flux, and third-hand tool. Quality tools lead to better results.
Cleanliness: Ensure the surfaces to be soldered are clean and free of oxidation. Use a polishing cloth or a mild abrasive to clean the surfaces before soldering.
Flux Application: Apply flux to both the solder and the pieces you are joining. Flux prevents oxidation and improves solder flow.
Correct Solder Choice: Use the appropriate type of solder for your project. Jewelers typically use hard, medium, or easy solder, depending on the task.
Proper Heat Application: Heat the pieces evenly, not just the solder. Aim for a gradient where the solder flows towards the heat source.
Practice: Practice joining different types of metals and shapes to gain experience and improve your technique.
Join Community Workshops or Online Forums: Exchange tips and techniques with other professionals. Websites like Ganoksin offer resources and forums for jewelers.
Educational Videos and Tutorials: Watch tutorials from reputable sources to see different techniques in action. YouTube channels like Rio Grande provide valuable visual guides.
Remember, patience and consistent practice are key to mastering soldering in jewelry making.
How to Display Soldering Skills on Your Resume
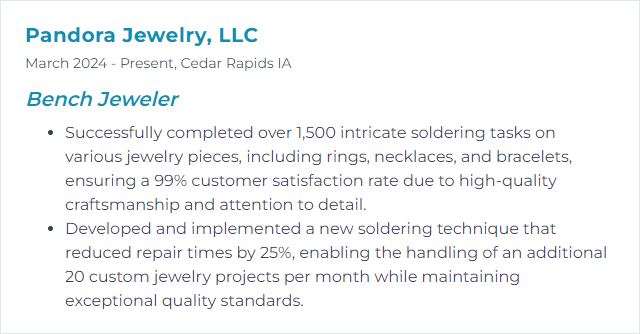
2. Stone Setting
Stone setting in the context of a bench jeweler refers to the process of securely placing and fixing gemstones or diamonds into a piece of jewelry, such as rings, necklaces, or earrings, using various techniques to ensure the stone is both highlighted and held firmly.
Why It's Important
Stone setting is crucial for a bench jeweler as it ensures the secure placement and enhanced presentation of gemstones in jewelry pieces, ultimately determining the item's durability, beauty, and customer satisfaction.
How to Improve Stone Setting Skills
Improving stone setting as a bench jeweler involves honing skills, embracing new techniques, and understanding the properties of both the stones and metals you're working with. Here are concise steps and resources to help enhance your stone setting abilities:
Practice Regularly: Mastery comes with repetition. Dedicate time to practice different types of settings on a variety of stones and metals.
Learn from Masters: Watch tutorials or take workshops from experienced jewelers. Websites like Ganoksin offer a wealth of learning materials.
Use the Right Tools: Invest in quality setting tools and maintain them well. Proper tools provide precision and minimize the risk of damaging stones.
Understand Materials: Knowing the characteristics of different gemstones and metals helps in choosing the right setting technique. The Gemological Institute of America (GIA) offers extensive resources.
Start Simple: Begin with simpler settings like bezel or prong before moving to more complex techniques like pavé or channel setting.
Attention to Detail: Pay close attention to the fit and finish. A well-set stone is secure and enhances the piece's overall beauty.
Seek Feedback: Join online forums or local jeweler communities to get feedback on your work and learn from the experience of others.
Stay Updated: Jewelry trends and techniques evolve. Subscribe to industry publications like Jewelry Making Daily to stay informed.
Improving stone setting is a continuous journey of learning and practice. Embrace every opportunity to refine your skills and stay curious about new methods and technologies in the field.
How to Display Stone Setting Skills on Your Resume
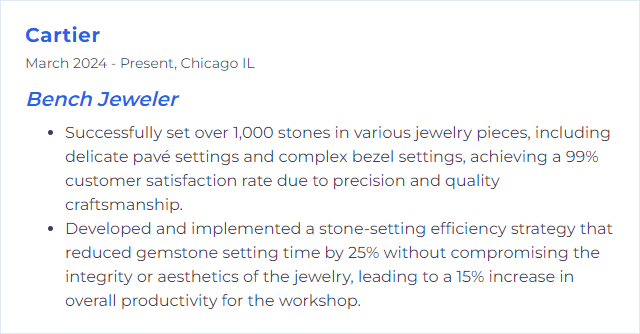
3. Polishing
Polishing, in the context of a bench jeweler, is the process of using abrasive materials and tools to smooth and enhance the shine and finish of jewelry pieces, making them visually appealing and free of scratches or marks.
Why It's Important
Polishing is crucial for a bench jeweler as it enhances the jewelry's appearance by removing scratches, restoring shine, and highlighting the craftsmanship, making the piece visually appealing and market-ready.
How to Improve Polishing Skills
Improving polishing skills as a bench jeweler involves a combination of proper tool selection, mastering techniques, and understanding the materials you are working with. Here's a concise guide:
Select the Right Tools and Compounds: Choose polishing wheels, buffs, and compounds appropriate for the material you're working on. Materials like gold, silver, and platinum each have different hardnesses and require specific abrasives.
Use a Multi-Step Process: Start with a coarse abrasive to remove scratches and imperfections, then progressively move to finer abrasives for a smooth finish. Finish with a polishing compound for a high shine.
Maintain Equipment: Keep your polishing wheels clean and free from contamination to prevent scratches and ensure an even polish.
Technique Matters: Apply consistent pressure and keep the piece moving to avoid uneven areas or overheating, which can cause warping or discoloration.
Safety First: Always wear protective eyewear, a dust mask, and ensure proper ventilation to avoid inhaling metal particles or compounds.
For more detailed guidance:
Ganoksin, an extensive resource for jewelers, offers detailed articles and community advice on polishing techniques: Ganoksin Polishing
Rio Grande, a supplier for jewelers, provides tutorials and product recommendations for polishing: Rio Grande Polishing
Jewelry Making Journal, for practical tips and step-by-step guides on jewelry polishing and other techniques: Jewelry Making Journal Tips
Mastering polishing requires practice, patience, and attention to detail. Continuously learning and experimenting with different techniques and materials will improve your skills over time.
How to Display Polishing Skills on Your Resume
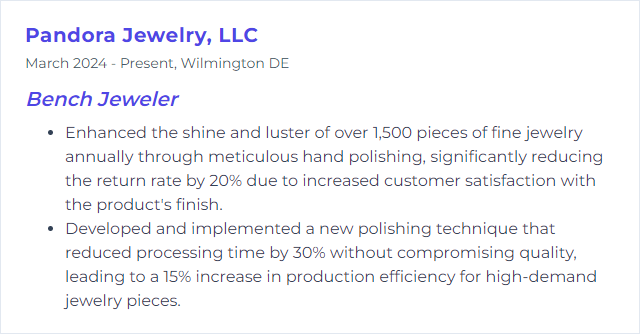
4. Wax Carving
Wax carving, in the context of bench jewelers, is the process of shaping and detailing a piece of wax into a desired jewelry design. This carved wax model is then used in casting to create the final metal jewelry piece through a process known as lost-wax casting. Wax carving allows jewelers to achieve intricate details and complex shapes that might be difficult to create directly in metal.
Why It's Important
Wax carving is essential for a bench jeweler as it allows for the precise and customizable creation of jewelry models. This step is crucial for casting intricate designs in metal, enabling the jeweler to achieve detailed craftsmanship and personalized pieces for clients.
How to Improve Wax Carving Skills
Improving wax carving skills, especially for a bench jeweler, involves practice, precision, and learning advanced techniques. Here are concise steps and resources:
Basic Skills: Start with mastering basic carving techniques. Focus on understanding different wax types and their properties. Ganoksin provides a broad range of tutorials and articles.
Use the Right Tools: Invest in high-quality carving tools. The right tools can make a significant difference. Understand the purpose of each tool. For tool recommendations, visit Rio Grande.
Practice Design Transfer: Practice transferring your designs accurately onto wax. This precision is crucial for the final piece. For design transfer techniques, Jewelry Making Daily offers useful guides.
Learn to Add Texture and Details: Master techniques for adding textures and fine details to your carvings. This can elevate your work significantly. Jewellers Academy has tutorials on adding details and textures.
Understand Casting Process: A good wax carving will result in a good cast. Familiarize yourself with the casting process to understand how your wax model translates into metal. The American Jewelry Institute provides insights into the casting process.
Take Advanced Workshops and Courses: Continuous education is key. Look for workshops and courses that focus on advanced wax carving techniques. Craftsy and GIA offer courses ranging from beginner to advanced levels.
Practice, Practice, Practice: There's no substitute for practice. Regularly challenge yourself with new designs and techniques.
By following these steps and utilizing the resources, you can significantly improve your wax carving skills as a bench jeweler.
How to Display Wax Carving Skills on Your Resume
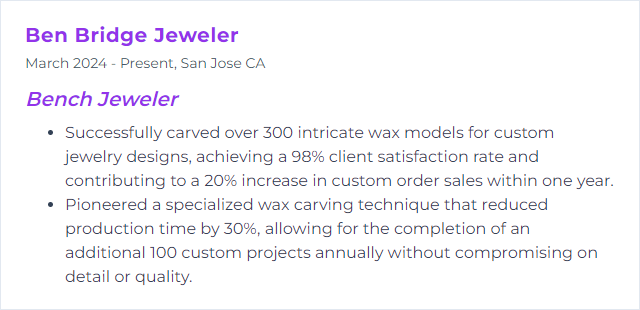
5. CAD (Computer-Aided Design)
CAD (Computer-Aided Design) for a Bench Jeweler is a digital tool used to design, modify, and visualize jewelry pieces in 3D before they are physically crafted, enhancing precision and allowing for intricate detailing.
Why It's Important
CAD (Computer-Aided Design) is important for a bench jeweler because it enables precise, customizable design creation, streamlines the production process, and enhances the ability to visualize and modify intricate details before crafting the physical piece, ultimately saving time and resources.
How to Improve CAD (Computer-Aided Design) Skills
Improving your CAD skills as a bench jeweler involves continuous learning and practice, focusing on jewelry-specific software, and leveraging online resources and communities. Here's a concise guide to enhance your CAD capabilities:
Master the Basics: Start with foundational courses to understand the core principles of the CAD software you're using. Websites like JewelryCADtraining offer tutorials tailored for jewelers.
Practice Regularly: Consistent practice is key. Work on a variety of projects to apply different features and tools of the software.
Online Tutorials and Courses: Utilize platforms like Udemy or Lynda.com for advanced courses that focus on jewelry design.
Join Online Forums and Communities: Platforms like Ganoksin or the 3Design Forum are great for connecting with other professionals, sharing experiences, and getting feedback on your work.
Stay Updated: Follow industry blogs and websites to stay informed about the latest CAD software updates and techniques. Companies like Gemvision regularly update their software and offer valuable resources.
Experiment with Different Software: Don't limit yourself to one tool. Experiment with other CAD software like Rhino, MatrixGold, or 3Design to find what suits your design style and needs best.
Feedback and Critique: Share your designs with peers or mentors for constructive criticism. This can help you see your work from a different perspective and improve your skills.
By following these steps and dedicating time to learn and practice, you can significantly improve your CAD skills for jewelry design.
How to Display CAD (Computer-Aided Design) Skills on Your Resume
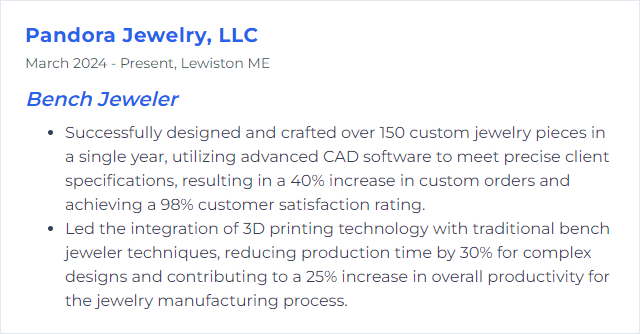
6. Laser Welding
Laser welding is a precision technique used by bench jewelers to join or fill metals with a focused, high-energy laser beam, allowing for detailed work on small or delicate jewelry pieces without damaging surrounding areas.
Why It's Important
Laser welding is important for a bench jeweler because it allows for precise, localized welding of small or delicate pieces without damaging surrounding areas, enabling intricate repairs and the creation of complex designs with high-quality finishes.
How to Improve Laser Welding Skills
To improve laser welding for bench jewelers, consider the following short and concise tips:
Proper Training: Invest in training to understand the nuances of laser settings for different materials. LaserStar offers specialized courses.
Material Preparation: Ensure surfaces are clean and properly aligned. Use a jeweler's loupe for precision.
Pulse Shaping: Adjust the pulse shape to match the material's properties. Many modern laser welders have built-in settings. Check the manufacturer's guidelines.
Parametric Optimization: Experiment with power, speed, and focus to find the optimal settings for your specific application. This guide from OR Laser provides a starting point.
Regular Maintenance: Keep your laser welder clean and calibrated. Refer to the maintenance section of your welder's manual, often available on the manufacturer's website.
Use of Assist Gas: For certain materials, using an assist gas like argon can improve weld quality by preventing oxidation. Weld Guru explains its benefits.
Invest in Quality Optics: High-quality optics ensure consistent laser delivery. Contact your welder's manufacturer for replacement and upgrade options.
By focusing on these areas, bench jewelers can significantly enhance their laser welding capabilities, leading to better quality and more efficient production.
How to Display Laser Welding Skills on Your Resume
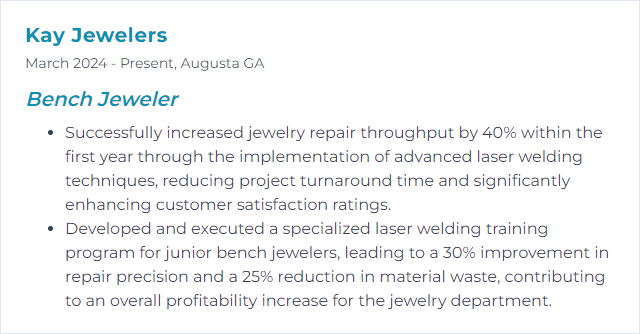
7. Engraving
Engraving, in the context of a bench jeweler, refers to the art of incising a design onto a hard, usually flat surface, by cutting grooves into it. This technique is used to decorate metal jewelry items such as rings, bracelets, and pendants with patterns, inscriptions, or images.
Why It's Important
Engraving adds personalized detail and uniqueness to jewelry pieces, enhancing their sentimental value and aesthetic appeal for customers.
How to Improve Engraving Skills
Improving engraving skills for a bench jeweler involves practice, the right tools, and continuous learning. Here are concise steps and resources:
Practice Regularly: Consistent practice on different materials enhances precision and skill. Start with simpler designs before moving to complex patterns.
Use Quality Tools: Invest in high-quality gravers, magnification tools, and a comfortable workbench. Proper lighting and an ergonomic setup are crucial. Rio Grande and Gesswein offer professional-grade tools.
Learn from Experts: Attend workshops or online courses from established institutions or experts. Websites like Ganoskin provide tutorials and forums for jewelers.
Understand Material Properties: Different materials require specific techniques. Experiment with various metals to understand how they respond to engraving.
Incorporate Technology: Consider integrating technology such as laser engravers or computer-aided design (CAD) software to expand your capabilities. JewelryCADTraining offers courses on mastering CAD for jewelry design.
Stay Inspired: Follow renowned jewelers and engravers on platforms like Instagram or Pinterest for inspiration and emerging trends.
Join Professional Communities: Engage with online forums and local jewelry-making communities to exchange knowledge and techniques. The Engraver's Cafe is an excellent resource for engravers to discuss and learn.
By focusing on these areas, bench jewelers can significantly enhance their engraving skills and produce intricate, high-quality work.
How to Display Engraving Skills on Your Resume
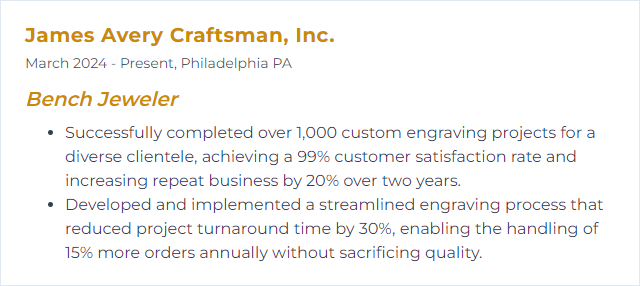
8. Casting
Casting in the context of a bench jeweler involves melting metal and pouring it into a mold to form a specific jewelry piece or component. This technique is used to create intricate designs and shapes that might be difficult to achieve through direct metal fabrication.
Why It's Important
Casting is important for a bench jeweler because it allows for the precise creation of intricate and unique jewelry designs by transforming molten metal into specific shapes using molds, ensuring both creativity and efficiency in production.
How to Improve Casting Skills
Improving casting in bench jewelry involves enhancing both the technical precision and the creative execution of your pieces. Here are concise tips:
Master Mold Making: Ensure your molds are flawless by investing in high-quality materials and practicing precise mold-making techniques. Ganoksin offers detailed insights into mold making and casting.
Invest in Quality Materials: Use high-grade metals and casting investment to reduce flaws. The GIA provides resources on material properties and selection.
Control Temperature and Humidity: Maintain an optimal casting environment to prevent metal and investment defects. Rio Grande shares tips on setting up your workspace.
Polish and Prepare Wax Models: Ensure your wax models are smooth and free of defects before casting; this directly impacts the final product's quality. Check out Stuller's resources for wax preparation techniques.
Invest in a Good Casting Machine: High-quality equipment can significantly improve casting outcomes. Explore options and reviews on Jewelry Tools.
Experiment with Casting Techniques: Learn and experiment with different casting techniques, such as vacuum or centrifugal casting, to find what best suits your work. The Society of North American Goldsmiths (SNAG) provides resources and workshops.
Continual Learning: Jewelry making and casting are ever-evolving fields. Engage in continuous learning through workshops, courses, and tutorials. Craftsy offers various online classes on jewelry making.
Join Professional Communities: Connect with other professionals through forums and social media groups for tips, advice, and feedback. Orchid Community by Ganoksin is an excellent place to start.
By focusing on these areas, bench jewelers can significantly improve their casting skills and the quality of their jewelry pieces.
How to Display Casting Skills on Your Resume
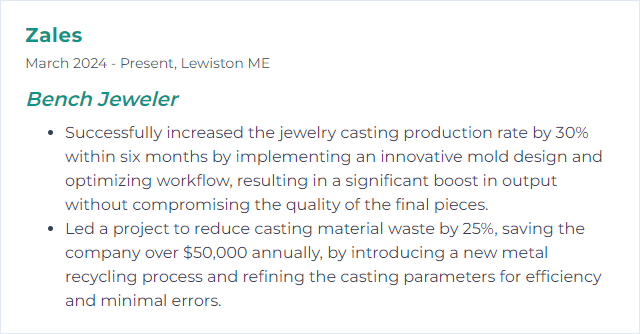
9. Metal Fabrication
Metal fabrication in the context of a bench jeweler involves cutting, shaping, and joining metal pieces using various techniques and tools to create jewelry. This process can include soldering, forging, casting, and polishing to achieve the desired design and finish.
Why It's Important
Metal fabrication is crucial for a bench jeweler as it involves the precise cutting, shaping, and assembling of metals to create intricate jewelry pieces, allowing for the customization of designs and the realization of artistic visions with high-quality craftsmanship.
How to Improve Metal Fabrication Skills
Improving metal fabrication in the context of bench jewelry involves enhancing precision, efficiency, and creativity. Here are concise strategies:
Upgrade Tools and Equipment: Invest in high-quality tools and modern equipment like precision lasers and micro motors for detailed work. Rio Grande and Gesswein offer a wide range of specialized jewelry tools and equipment.
Enhance Skills through Education: Continuously learn new techniques and stay updated with industry trends through online courses and workshops. Websites like Ganoksin provide valuable resources and tutorials.
Implement CAD Software: Use Computer-Aided Design (CAD) software to improve design accuracy and efficiency. MatrixGold is popular among jewelers for its powerful features tailored to jewelry design.
Practice Lean Manufacturing: Adopt lean manufacturing principles to reduce waste and improve workflow efficiency. Resources like The Lean Jewel offer insights into applying these practices in jewelry making.
Focus on Quality Control: Establish a rigorous quality control process to ensure every piece meets high standards. This involves regular inspection and testing of materials and finished products.
By incorporating these strategies, bench jewelers can significantly enhance their metal fabrication processes, leading to higher quality products and improved customer satisfaction.
How to Display Metal Fabrication Skills on Your Resume
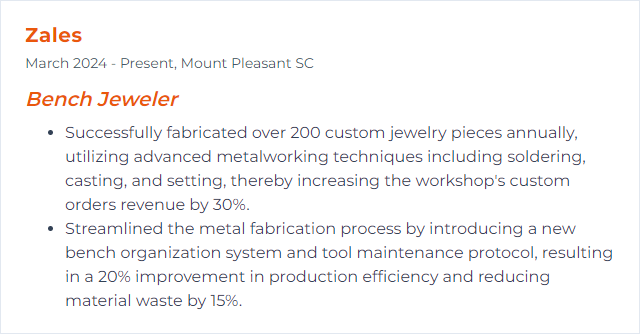
10. Gemology
Gemology is the scientific study and identification of gemstones, focusing on their characteristics, authenticity, and value, essential for bench jewelers in crafting and appraising jewelry accurately.
Why It's Important
Gemology is important for a Bench Jeweler because it provides the expertise to identify, authenticate, and evaluate gemstones, ensuring the quality and value of the jewelry pieces they craft or repair. This knowledge is essential for maintaining trust with customers and for the jeweler's reputation.
How to Improve Gemology Skills
Improving gemology skills as a bench jeweler involves continuous education, practice, and the use of advanced tools. Here’s a concise guide:
Education: Enroll in accredited gemology courses to understand gemstone properties, identification, and grading. The Gemological Institute of America (GIA) offers reputable courses.
Practice: Regularly examine a variety of gemstones to hone identification and grading skills. Practice using tools like loupes, microscopes, and spectrometers.
Networking: Join gemological associations, such as the International Gem Society (IGS), to connect with experts and stay updated on industry trends.
Technology: Invest in advanced gemological tools and software for accurate analysis and identification. Familiarize yourself with the latest developments in gem treatment and synthetic gems.
Ethics: Stay informed about ethical sourcing and the environmental impact of gemstones to make responsible choices in your work.
By focusing on education, practical experience, networking, and ethical practices, bench jewelers can significantly enhance their gemology skills.
How to Display Gemology Skills on Your Resume
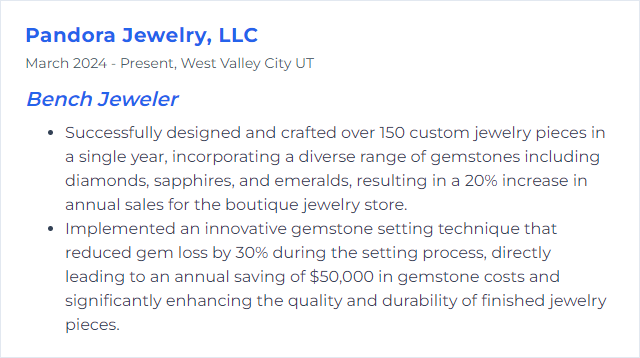
11. Rhodium Plating
Rhodium plating is a process used by bench jewelers to coat jewelry, typically made of white gold or silver, with a layer of rhodium. This plating enhances the jewelry's surface, providing a brighter finish, increased scratch resistance, and protection against tarnishing.
Why It's Important
Rhodium plating is important for a bench jeweler because it enhances the durability, luster, and scratch resistance of jewelry, particularly white gold pieces, ensuring a longer-lasting, brilliant finish.
How to Improve Rhodium Plating Skills
Improving rhodium plating involves ensuring proper surface preparation, using high-quality plating solutions, and maintaining optimal plating conditions. Here's a concise guide:
- Surface Preparation: Clean the jewelry thoroughly to remove oils, dirt, and oxidation. Use ultrasonic cleaning followed by electrocleaning for best results.
- Bath Maintenance: Use a high-quality rhodium plating solution and keep the bath at the manufacturer's recommended temperature and pH levels. Regularly filter the solution to remove contaminants.
- Plating Parameters: Follow the recommended voltage and plating time closely. Typically, a lower voltage for a longer time yields a smoother and more durable finish.
- Rinsing and Drying: After plating, rinse the jewelry in distilled water and dry it using a gentle, non-abrasive method to prevent spotting.
- Equipment and Safety: Ensure all plating equipment is in good condition and use proper safety gear, including gloves and eye protection.
For more detailed guidance and specific techniques, refer to professional resources:
- Rio Grande's Rhodium Plating Guide provides detailed instructions and product recommendations.
- Ganoksin offers comprehensive articles and community advice on various jewelry techniques, including rhodium plating.
- The Jewelry Making Journal is another valuable source for tips and tutorials on jewelry finishing, including rhodium plating tips.
Remember, practice and consistency are key to achieving a high-quality rhodium finish.
How to Display Rhodium Plating Skills on Your Resume
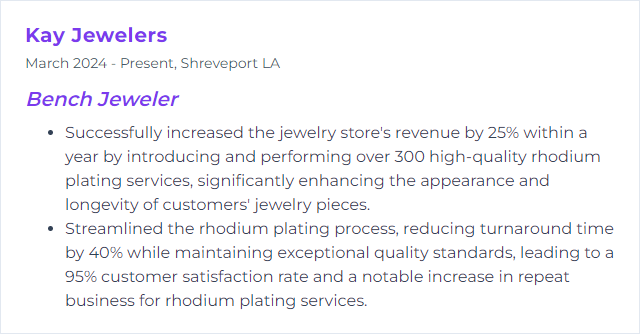
12. D Printing
3D printing for a bench jeweler is a technology that allows for the creation of intricate jewelry designs by printing them layer-by-layer in a variety of materials, including metals and resins, directly from digital models. This process enables high precision, customization, and efficient production of complex pieces without the need for traditional manual sculpting and molding techniques.
Why It's Important
3D printing is important for a bench jeweler because it enables precise, custom jewelry designs to be created quickly and cost-effectively, transforming ideas into tangible pieces without the need for traditional, labor-intensive crafting methods.
How to Improve D Printing Skills
Improving 3D printing for a bench jeweler involves focusing on precision, material choices, and post-processing techniques to create high-quality jewelry pieces. Here are concise recommendations:
Optimize Resolution: Use a 3D printer with high resolution (25 microns or lower) for intricate details. Formlabs offers printers suitable for fine jewelry applications.
Select Appropriate Materials: Choose casting resins specifically designed for jewelry, ensuring clean burnout and fine details. B9Creations provides resins optimized for jewelry casting.
Post-Processing Techniques: Invest time in cleaning and curing your prints. Techniques include UV curing and using isopropyl alcohol baths. All3DP outlines various methods.
Software Precision: Utilize CAD software with jewelry-specific tools for precise designs. MatrixGold is highly regarded in the jewelry industry.
Continuous Learning: Stay updated with the latest in 3D printing technology and materials by following relevant blogs and forums. 3DPrint.com is a good resource.
Implementing these tips can significantly enhance the quality and efficiency of 3D printed jewelry pieces.
How to Display D Printing Skills on Your Resume
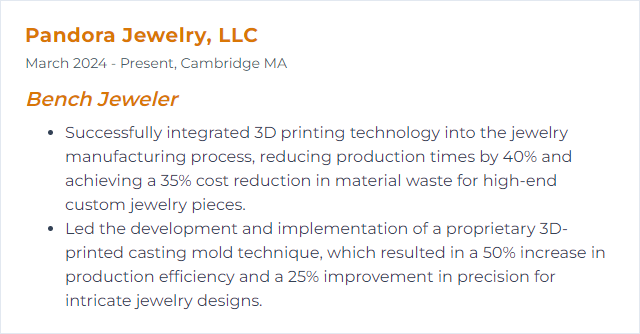