Top 12 Tooling Engineer Skills to Put on Your Resume
In today's competitive job market, standing out as a tooling engineer requires a blend of technical expertise and soft skills that appeal to potential employers. Highlighting the top skills on your resume can set you apart, showcasing your ability to not only excel in the intricacies of tooling engineering but also to contribute effectively to any team or project.
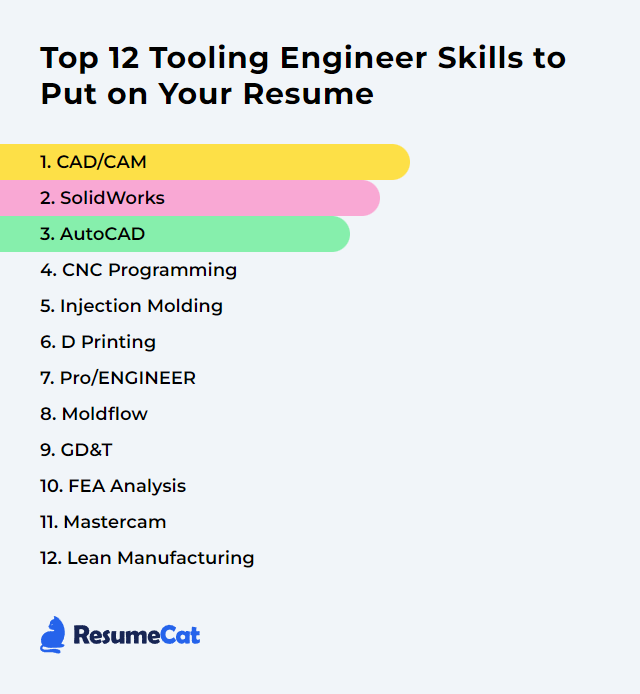
Tooling Engineer Skills
- CAD/CAM
- SolidWorks
- AutoCAD
- CNC Programming
- Injection Molding
- D Printing
- Pro/ENGINEER
- Moldflow
- GD&T
- FEA Analysis
- Mastercam
- Lean Manufacturing
1. CAD/CAM
CAD/CAM stands for Computer-Aided Design/Computer-Aided Manufacturing. For a Tooling Engineer, it involves using computer software to design tools, molds, and dies, and then using automated machinery to manufacture these designs with precision and efficiency.
Why It's Important
CAD/CAM is crucial for a Tooling Engineer because it enables precise design and manufacturing of tools, molds, and dies, ensuring high accuracy, efficiency, and reduced time from concept to production, leading to cost savings and improved product quality.
How to Improve CAD/CAM Skills
Improving CAD/CAM (Computer-Aided Design/Computer-Aided Manufacturing) as a Tooling Engineer involves enhancing design efficiency, manufacturing precision, and the integration between design and manufacturing processes. Here's a concise guide:
Upgrade Software and Hardware: Regularly update your CAD/CAM software to leverage the latest features and improve processing speed by upgrading your computer hardware. AutoDesk and SolidWorks are popular software options.
Utilize High-Quality Tool Libraries: Integrate comprehensive and updated tool libraries within your CAD/CAM software for accurate tool selection and machining strategies. Check resources like Harvey Performance Company for tool libraries.
Implement Standardized Design Processes: Standardize design processes to improve efficiency and consistency. Utilize templates and checklists to ensure all critical design aspects are covered. ASME provides standards that can be integrated into design processes.
Continuous Learning and Training: Stay updated with the latest CAD/CAM technologies and methodologies through continuous learning. Online platforms like Coursera and LinkedIn Learning offer courses on advanced CAD/CAM topics.
Optimize Tool Paths and Machining Strategies: Use simulation tools within CAD/CAM software to optimize tool paths and machining strategies, reducing machining time and increasing tool life. Mastercam offers advanced simulation options.
Collaboration and Integration Tools: Use collaboration tools for seamless integration between design and manufacturing teams. Cloud-based CAD/CAM solutions like Onshape facilitate real-time collaboration.
Customize CAD/CAM Macros and Scripts: Develop or use existing macros and scripts to automate repetitive tasks, improving design and manufacturing efficiency. Forums like CNCzone provide resources and community support for scripting.
Feedback Loop from Manufacturing Floor: Implement a feedback loop from the manufacturing floor back to the design phase to identify and rectify any design issues that could impact manufacturability. Tools like MES software can help in capturing manufacturing feedback.
By focusing on these areas, Tooling Engineers can significantly enhance their CAD/CAM capabilities, leading to improved design quality, reduced manufacturing times, and lower costs.
How to Display CAD/CAM Skills on Your Resume
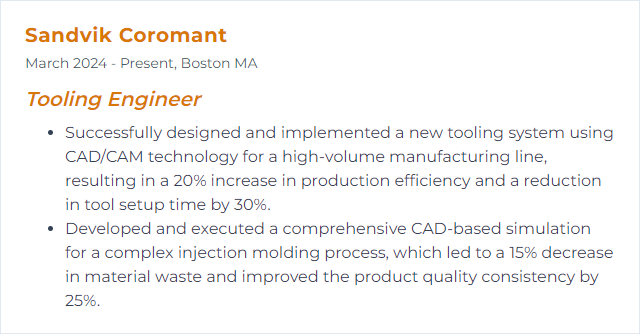
2. SolidWorks
SolidWorks is a computer-aided design (CAD) and engineering software used for creating 3D models and technical drawings, essential for tooling engineers in designing molds, dies, and other tooling components.
Why It's Important
SolidWorks is crucial for Tooling Engineers as it enables precise 3D modeling and simulation of tools, facilitating the design, optimization, and validation of molds, dies, and fixtures, thus improving efficiency, reducing production costs, and accelerating time-to-market.
How to Improve SolidWorks Skills
Improving your SolidWorks skills as a Tooling Engineer involves mastering several core areas: understanding tool design intricacies, enhancing modeling efficiency, and leveraging SolidWorks' advanced features for tooling applications. Here are concise strategies and resources:
Master Sketching and Modeling: Solid foundation in 3D sketching and part modeling is crucial. Focus on parametric design practices to make adaptable models.
Learn Advanced Assembly Techniques: Being proficient in handling complex assemblies can significantly improve your tool design process.
- Advanced Assembly Modeling
Utilize Mold Design Tools: SolidWorks offers specialized tools for mold design. Understanding these features can streamline your tooling projects.
Incorporate Simulation for Tooling: Use SolidWorks Simulation to predict how your designs will perform in the real world, reducing the need for physical prototypes.
- SolidWorks Simulation
Explore Customization and Automation: Automate repetitive tasks with macros or delve into API for custom tooling solutions.
- SolidWorks API
Stay Updated and Networked: Join SolidWorks forums and user groups to stay abreast of new features and best practices.
Focusing on these areas and utilizing the provided resources can significantly enhance your proficiency and efficiency in using SolidWorks for tooling engineering.
How to Display SolidWorks Skills on Your Resume
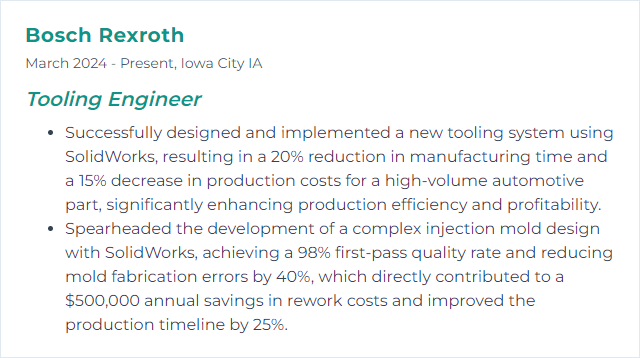
3. AutoCAD
AutoCAD is a computer-aided design (CAD) software used by tooling engineers for creating precise 2D and 3D drawings and models of tooling components and assemblies.
Why It's Important
AutoCAD is important for a Tooling Engineer as it enables precise design and modification of tools, molds, and dies, ensuring accuracy, efficiency in production processes, and facilitating the creation of complex geometries and dimensions critical for manufacturing high-quality products.
How to Improve AutoCAD Skills
To improve your AutoCAD skills as a Tooling Engineer, focus on the following strategies:
Enhance Basic Skills: Master the fundamentals of AutoCAD. Autodesk offers a comprehensive learning resource that covers everything from basic commands to advanced functions.
Customize Tool Palettes: Customize AutoCAD tool palettes to streamline your workflow. Autodesk provides a guide on creating and customizing tool palettes for more efficient operations.
Use Macros and Scripts: Automate repetitive tasks with macros and scripts. Learn about AutoCAD scripting on the Autodesk Knowledge Network.
Implement Add-ons and Extensions: Explore and implement AutoCAD add-ons and extensions specific to tooling design. Autodesk App Store offers a variety of tooling and mold design add-ons that can enhance your design capabilities.
Practice 3D Modeling: Advance your 3D modeling skills by practicing and utilizing AutoCAD’s 3D tools. Autodesk provides resources for 3D modeling that can help refine your designs.
Stay Updated: Keep abreast of the latest AutoCAD updates and features. Autodesk’s official blog offers insights into new features and tips for enhancing productivity.
Join Forums and Communities: Engage with AutoCAD forums and communities. Autodesk Community’s AutoCAD forum is a valuable resource for advice, tips, and networking with other professionals.
By following these strategies and utilizing the resources provided, you can significantly improve your AutoCAD skills as a Tooling Engineer.
How to Display AutoCAD Skills on Your Resume
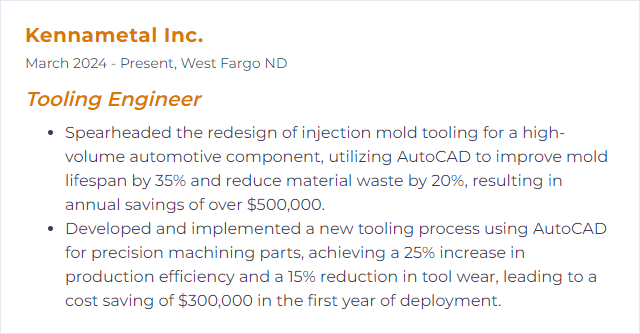
4. CNC Programming
CNC programming is the process of creating coded instructions (G-code) for controlling automated machine tools in the manufacturing process, allowing for precision machining of parts to exact specifications. For a Tooling Engineer, it involves designing and optimizing these instructions to improve tool performance, efficiency, and product quality.
Why It's Important
CNC programming is crucial for a Tooling Engineer as it enables precise control over machine tools, ensuring accurate, repeatable, and efficient production of complex parts and tools, optimizing both quality and productivity in manufacturing processes.
How to Improve CNC Programming Skills
Improving CNC programming requires a combination of enhancing skills, utilizing advanced software, and adopting best practices. Here's a concise guide:
Continuous Learning: Stay updated with the latest CNC technologies and programming techniques through online courses and tutorials. Websites like Coursera and Udemy offer courses tailored to CNC programming.
Master CAM Software: Proficiency in Computer-Aided Manufacturing (CAM) software is crucial. Explore and master industry-leading tools such as Mastercam, Fusion 360, or SolidCAM, depending on your specific needs.
Simulation Tools: Use simulation software to test and verify your programs before actual machining. This minimizes errors and material waste. VERICUT is a powerful option for simulating CNC machining.
Optimize Toolpaths: Focus on optimizing toolpaths for efficiency and reduced machining time. Tools like HyperMILL offer advanced strategies for efficient toolpath generation.
Implement Standardization: Develop and implement a standardized coding practice within your team. This improves readability and maintainability of the programs. Resources like the National Institute for Metalworking Skills (NIMS) can offer guidelines.
Collaborate and Share Knowledge: Join forums and communities such as CNCzone or Practical Machinist to share insights, solve problems, and learn from the experiences of others.
Feedback Loop: Establish a feedback loop with the machining floor. Direct feedback from machinists can provide valuable insights for improving your CNC programs.
Automation Tools: Look into automation tools to streamline repetitive tasks in the programming process. This can significantly increase productivity and reduce errors.
By focusing on these areas, a Tooling Engineer can significantly improve their CNC programming skills and contribute to more efficient and effective machining processes.
How to Display CNC Programming Skills on Your Resume
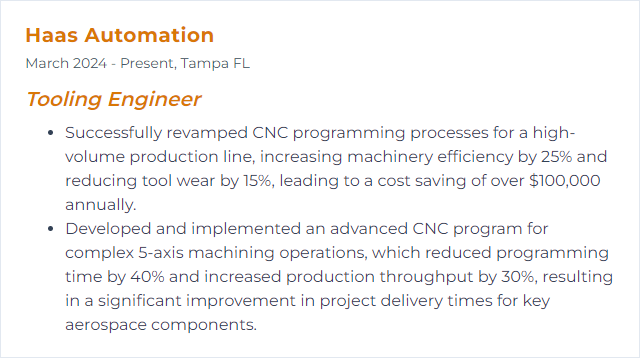
5. Injection Molding
Injection molding is a manufacturing process used to produce parts by injecting molten material into a mold, where it cools and solidifies into the desired shape. For a Tooling Engineer, it involves designing and creating the molds (tooling) that define the part geometry and ensuring they meet precise specifications for successful production.
Why It's Important
Injection molding is crucial for a Tooling Engineer because it enables the efficient, precise, and scalable production of complex parts with tight tolerances, optimizing tool design and manufacturing processes for high-volume production.
How to Improve Injection Molding Skills
Improving injection molding involves optimizing the mold design, material selection, and processing conditions to enhance product quality and manufacturing efficiency. As a Tooling Engineer, focus on:
Design Optimization: Use simulation tools like Moldflow to analyze and optimize the mold design for uniform cooling, minimal warpage, and reduced cycle times.
Material Selection: Choose materials that match the product requirements and molding conditions. Consult material databases like MatWeb for properties and processing parameters.
Mold Maintenance: Regularly inspect and maintain molds to ensure they are in optimal condition. Implement predictive maintenance strategies using insights from sources like ToolingDocs.
Process Optimization: Use scientific molding principles to fine-tune processing parameters such as temperature, pressure, and injection speed for optimal flow and cooling. Resources like Paulson Training Programs offer valuable insights.
Training and Development: Invest in ongoing education and training for the team. Platforms like Plastics Training Academy at UMass Lowell provide courses on advanced injection molding techniques.
By focusing on these areas, a Tooling Engineer can significantly improve the performance and efficiency of injection molding operations.
How to Display Injection Molding Skills on Your Resume
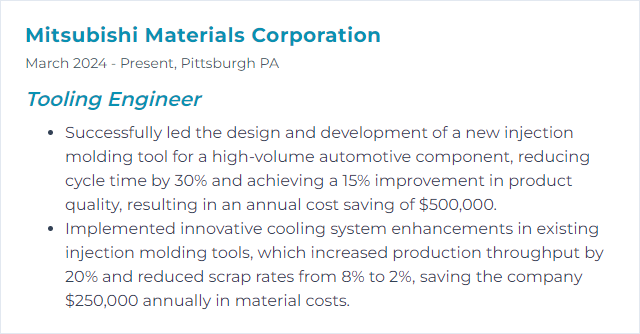
6. D Printing
3D printing, in the context of a Tooling Engineer, is a manufacturing process that creates physical objects from digital designs by layering materials. It enables the rapid prototyping and production of complex tooling components with reduced lead times and costs.
Why It's Important
3D printing is important for a Tooling Engineer because it allows for rapid prototyping, customization, and complexity in tool design, reducing lead times and costs, while improving efficiency and innovation in tool production.
How to Improve D Printing Skills
Improving 3D printing, especially from a Tooling Engineer's perspective, involves optimizing print quality, speed, and material properties. Here are concise strategies:
Material Selection: Choose the right material for the specific application, considering strength, flexibility, and thermal properties. Material Guide
Printer Calibration: Regularly calibrate your 3D printer to ensure accuracy in dimensions and layer adhesion. Calibration Tips
Layer Height and Infill Optimization: Adjust layer height and infill settings based on the required balance between print strength and speed. Optimization Techniques
Post-Processing Techniques: Implement post-processing methods such as sanding, painting, or chemical smoothing to enhance surface finish. Post-Processing Guide
Software and Slicing Settings: Use advanced slicing software with optimized settings for supports, print speed, and temperature control. Slicing Software
Design for Additive Manufacturing (DfAM): Employ DfAM principles to reduce material use, decrease print time, and improve part functionality. DfAM Strategies
By focusing on these areas, Tooling Engineers can significantly improve the efficiency, quality, and application of 3D printed parts.
How to Display D Printing Skills on Your Resume
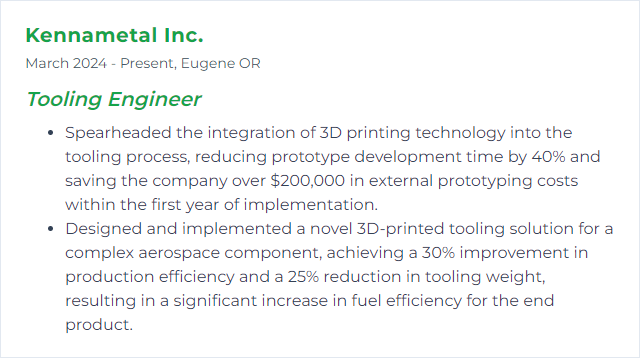
7. Pro/ENGINEER
Pro/ENGINEER, now known as PTC Creo, is a 3D CAD software tool designed for product design and development, offering advanced capabilities for modeling, simulation, and analysis. For a Tooling Engineer, it is particularly useful for designing complex tooling and molds, enabling efficient creation and modification of the geometries required for manufacturing processes.
Why It's Important
Pro/ENGINEER (now known as PTC Creo) is important for a Tooling Engineer because it provides powerful, integrated 3D CAD/CAM/CAE solutions, enabling the efficient design, simulation, and manufacturing of complex tooling and molds. This accelerates the development process, enhances precision, and reduces production costs.
How to Improve Pro/ENGINEER Skills
To improve your use of Pro/ENGINEER (now known as PTC Creo) as a Tooling Engineer, consider the following strategies:
Enhance Skills with Training: Enroll in PTC University courses to deepen your understanding of advanced Pro/ENGINEER functionalities specific to tooling design.
Utilize Extensions: Leverage Pro/ENGINEER's Mold Analysis Extension to simulate and refine mold designs directly within the software, enhancing tooling precision and efficiency.
Customize Your Workspace: Tailor the user interface and toolbars to better suit your workflow. PTC’s guide on customization can streamline your tooling design process.
Implement Best Practices: Adopt tooling design best practices such as using parametric and feature-based design principles to ensure flexible and easily modifiable tooling designs. The PTC Community provides insights and tips from fellow engineers.
Stay Updated: Always use the latest version of the software to take advantage of new features and improvements. Check PTC’s Release Notes regularly for updates relevant to tooling engineering.
Use Simulation Tools: Integrate with PTC’s Creo Simulate to perform stress, thermal, and vibration analysis on your tooling designs to ensure they meet required specifications and standards.
Network and Collaborate: Join forums and discussion groups like the PTC Community to exchange knowledge, tips, and tricks with other professionals in your field.
By focusing on continuous learning, leveraging available software extensions, and engaging with the engineering community, you can significantly enhance your proficiency and efficiency in using Pro/ENGINEER for tooling design.
How to Display Pro/ENGINEER Skills on Your Resume
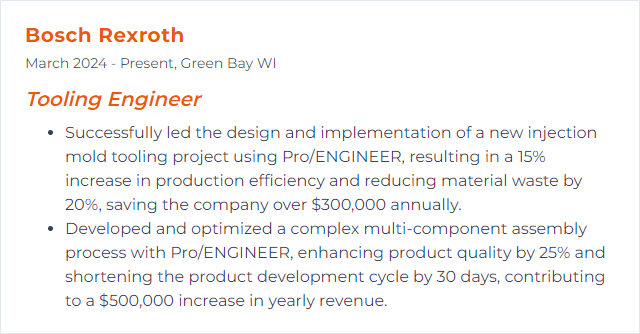
8. Moldflow
Moldflow is a simulation software used by tooling engineers to predict and optimize the injection molding process, enabling analysis of material flow and cooling to improve mold design, part quality, and manufacturability.
Why It's Important
Moldflow is important for a Tooling Engineer because it enables the prediction and optimization of plastic injection molding processes, identifying potential manufacturing issues and improving mold design, leading to reduced development time, cost savings, and enhanced product quality.
How to Improve Moldflow Skills
Improving Moldflow for a Tooling Engineer involves enhancing simulation accuracy and efficiency by focusing on key areas:
Mesh Optimization: Ensure the mesh is fine enough to capture details critical to flow and cooling, but not so fine that it unnecessarily increases computation time. Autodesk provides guidelines for mesh preparation.
Material Selection: Use accurate material data. When specific material data is unavailable, consider conducting material characterization tests. Autodesk Moldflow has a comprehensive material database that can be used for simulation.
Process Parameters: Input realistic process parameters that closely mimic the actual injection molding process. This includes injection time, melt and mold temperature, and packing pressure. Autodesk offers insights into setting accurate process parameters.
Cooling System Design: Optimize cooling channel layout to ensure uniform cooling, which is vital for minimizing warpage and reducing cycle times. Autodesk has resources on cooling system design.
Warpage Analysis: Use warpage analysis to predict and mitigate part deformation by adjusting process parameters, cooling line layout, or by considering changes in part design or material. Further guidance can be found in Autodesk’s warpage analysis section.
Collaborate and Iterate: Collaboration with design and manufacturing teams is crucial. Use Moldflow insights to drive discussions and iterative improvements. Autodesk Moldflow facilitates collaboration.
Training and Continuous Learning: Stay updated with the latest Moldflow features and best practices through Autodesk’s training and certification programs.
By focusing on these areas, a Tooling Engineer can significantly improve Moldflow simulations, leading to more accurate predictions and more efficient mold designs.
How to Display Moldflow Skills on Your Resume
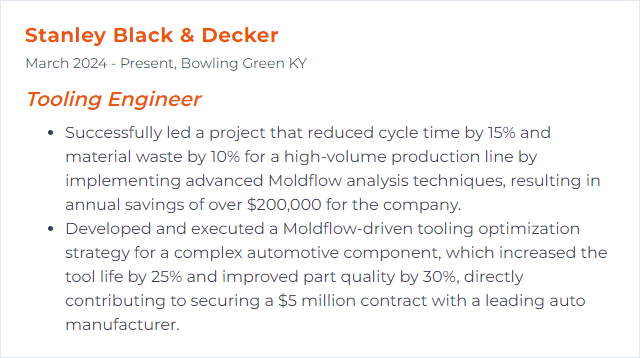
9. GD&T
GD&T (Geometric Dimensioning and Tolerancing) is a symbolic language used in engineering drawings to precisely describe the size, form, orientation, and location of product features with respect to the function and assembly of parts. For a Tooling Engineer, GD&T provides a clear and concise way to communicate design intent for manufacturing and inspection of tools and parts, ensuring accuracy, interchangeability, and optimal functionality.
Why It's Important
GD&T (Geometric Dimensioning and Tolerancing) is crucial for a Tooling Engineer because it ensures precision and consistency in manufacturing processes by clearly defining design intent, tolerances, and assembly requirements, thus minimizing errors, enhancing interchangeability, and reducing costs.
How to Improve GD&T Skills
Improving GD&T (Geometric Dimensioning and Tolerancing) skills, especially for a Tooling Engineer, involves understanding the principles of design, manufacturing processes, and quality control. Here’s a concise guide:
Educate Yourself: Start with the basics of GD&T. Online courses and webinars can be very helpful. ASME offers a range of courses ASME GD&T Training.
Practice and Application: Apply what you learn in real-world scenarios. Use CAD software to practice creating and interpreting GD&T symbols. Autodesk has resources that could be helpful Autodesk Knowledge Network.
Use Standards: Familiarize yourself with the latest ASME Y14.5 standards. The ASME website is a great resource for getting access to these standards.
Join Communities: Engage with online forums and communities where professionals discuss their GD&T challenges and solutions. LinkedIn groups and the Eng-Tips Forums can be a good start.
Feedback and Mentorship: Seek feedback from more experienced colleagues and consider finding a mentor. Regularly discuss your drawings and designs to understand your areas of improvement.
Continuous Learning: GD&T is an evolving field. Keep yourself updated with the latest trends, tools, and technologies through professional development resources and workshops.
By following these steps and actively seeking out learning opportunities, you can significantly improve your GD&T skills as a Tooling Engineer.
How to Display GD&T Skills on Your Resume
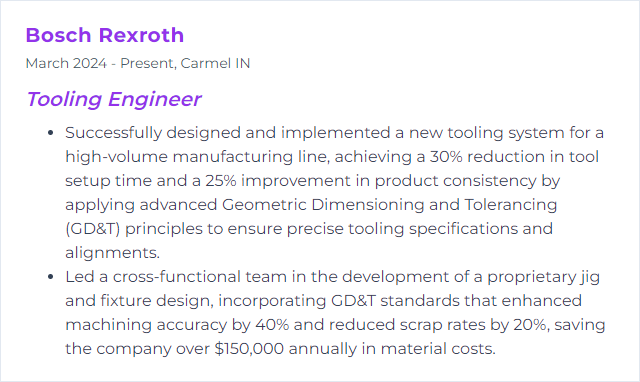
10. FEA Analysis
FEA (Finite Element Analysis) is a computerized method used by tooling engineers to predict how a tool will react to real-world forces, vibration, heat, fluid flow, and other physical effects. It helps in optimizing design and testing for strength, durability, and performance before manufacturing.
Why It's Important
FEA (Finite Element Analysis) is crucial for a Tooling Engineer because it enables the prediction and optimization of tool performance, stress distribution, and potential failure points, ensuring tool durability, efficiency, and cost-effectiveness in manufacturing processes.
How to Improve FEA Analysis Skills
Improving FEA (Finite Element Analysis) for a Tooling Engineer involves enhancing model accuracy, computational efficiency, and result interpretation. Here are concise strategies:
Mesh Refinement: Optimize mesh size and density for critical areas to improve accuracy without significantly increasing computational time. ANSYS Meshing Guide.
Material Properties: Use accurate and comprehensive material data, including temperature-dependent properties if applicable, to closely represent real-world behavior. MatWeb for Material Properties.
Boundary Conditions: Apply realistic boundary conditions and loads that accurately reflect the operational environment of the tool. Solid Mechanics and its Applications.
Simulation Software Capabilities: Utilize advanced features and solvers specific to your FEA software that are most suitable for your analysis type. Comparison of Software.
Validation and Calibration: Regularly validate and calibrate your FEA models with experimental data or known benchmarks to ensure accuracy. NAFEMS Benchmarks.
Post-Processing Tools: Use advanced post-processing tools for better visualization and interpretation of results, facilitating more informed decisions. ParaView.
Continued Learning and Training: Stay updated with the latest FEA techniques, software updates, and best practices through ongoing education. FEA Online Courses.
By focusing on these aspects, a Tooling Engineer can significantly improve the reliability and accuracy of FEA analyses.
How to Display FEA Analysis Skills on Your Resume
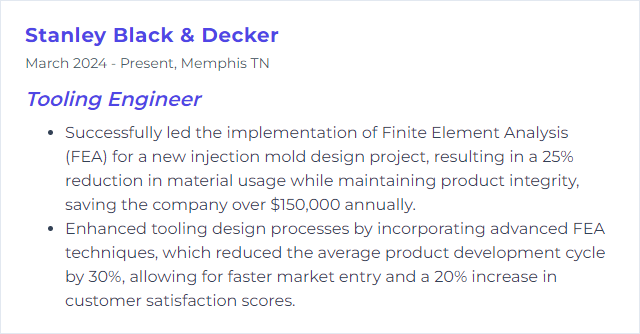
11. Mastercam
Mastercam is a computer-aided manufacturing (CAM) software used by tooling engineers to design, simulate, and program machining operations for CNC (Computer Numerical Control) machines, facilitating the creation of precise tooling and fixtures.
Why It's Important
Mastercam is crucial for a Tooling Engineer because it provides advanced CAD/CAM software solutions for designing, simulating, and optimizing machining paths, significantly improving tooling design precision, manufacturing efficiency, and product quality.
How to Improve Mastercam Skills
Improving your proficiency in Mastercam as a Tooling Engineer involves a combination of training, practice, and leveraging resources effectively. Here are concise steps to enhance your Mastercam skills:
Official Training: Start with Mastercam's own training solutions, including online tutorials and local training to understand the fundamentals and advanced features.
Practice Projects: Apply your skills on real-world or simulated projects to gain practical experience.
Online Forums and Communities: Engage with the Mastercam Forum and other online communities like CNCZone to exchange tips, tricks, and solutions.
Webinars and Workshops: Attend webinars and workshops hosted by Mastercam for insights on new features and advanced techniques.
Certification: Consider obtaining a Mastercam Certification to validate your skills and knowledge.
Software Updates: Regularly update your software to the latest version to utilize new tools and improvements.
Custom Macros and Scripts: Learn to write custom scripts or macros to automate repetitive tasks and improve efficiency.
Feedback Loop: Implement a feedback loop from your manufacturing floor back to design to continuously improve and optimize tool paths and machining strategies.
By focusing on these areas, you can significantly enhance your Mastercam skills, contributing to more efficient and innovative tooling solutions.
How to Display Mastercam Skills on Your Resume
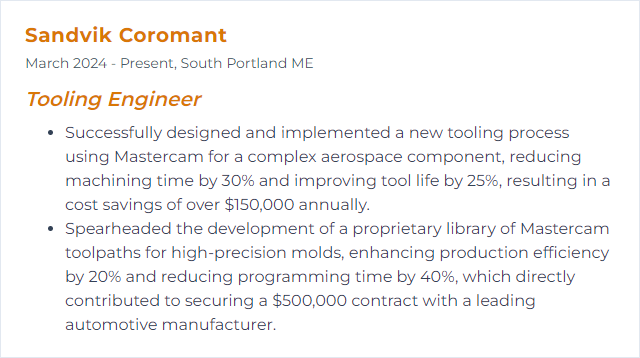
12. Lean Manufacturing
Lean Manufacturing is a systematic approach aimed at reducing waste and improving efficiency in production processes, focusing on maximizing value to the customer. For a Tooling Engineer, it involves designing and managing tooling processes to minimize downtime, reduce defects, and ensure rapid changeovers, thereby enhancing productivity and product quality.
Why It's Important
Lean Manufacturing is crucial for a Tooling Engineer as it streamlines production processes, reduces waste and tool downtime, and optimizes tool usage and maintenance, leading to increased efficiency, cost savings, and higher quality products.
How to Improve Lean Manufacturing Skills
Improving Lean Manufacturing, especially for a Tooling Engineer, involves optimizing processes, reducing waste, and enhancing productivity. Here are concise strategies:
Continuous Improvement (Kaizen): Embrace Kaizen by continually seeking ways to improve manufacturing processes and tooling efficiency. Kaizen Institute
5S Methodology: Implement the 5S (Sort, Set in order, Shine, Standardize, Sustain) to organize the workplace, ensuring tools and materials are easily accessible and workspaces are optimized for efficiency. Lean Production
Value Stream Mapping: Analyze and design the flow of materials and information required to bring a product to a customer. This helps identify and eliminate waste. Lean Enterprise Institute
Standard Work: Develop and use standard operating procedures for tooling operations to ensure consistent quality and efficiency. SME
Total Productive Maintenance (TPM): Focus on preventive maintenance to reduce machine downtime and increase productivity. Involve operators in routine maintenance. Reliable Plant
Cross-Training: Enhance flexibility and resilience by cross-training employees, allowing them to perform multiple job functions within the manufacturing process. Tooling U-SME
Root Cause Analysis: When problems occur, use tools like the 5 Whys or fishbone diagram to identify and address the underlying causes, preventing recurrence. ASQ
Collaborative Robotics (Cobots): Integrate cobots to work alongside humans for repetitive or potentially hazardous tasks, improving safety and efficiency. Robotic Industries Association
Lean Six Sigma: Combine Lean manufacturing principles with Six Sigma methodologies to improve quality and efficiency by eliminating defects and reducing variability. ASQ Lean Six Sigma
Innovation and Technology Adoption: Stay abreast of the latest tooling technologies and manufacturing innovations that can streamline production processes. Manufacturing Innovation Blog
By focusing on these areas, a Tooling Engineer can significantly impact the efficiency and effectiveness of manufacturing operations within the lean manufacturing framework.
How to Display Lean Manufacturing Skills on Your Resume
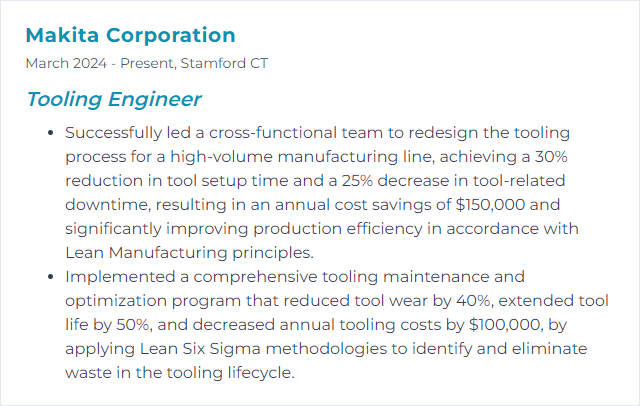