Top 12 Quality Assurance Auditor Skills to Put on Your Resume
In today's competitive job market, standing out as a Quality Assurance Auditor requires showcasing a unique blend of skills on your resume. Highlighting your expertise in meticulous analysis, process improvement, and keen attention to detail can significantly elevate your candidacy, making you a top choice for employers in various industries.
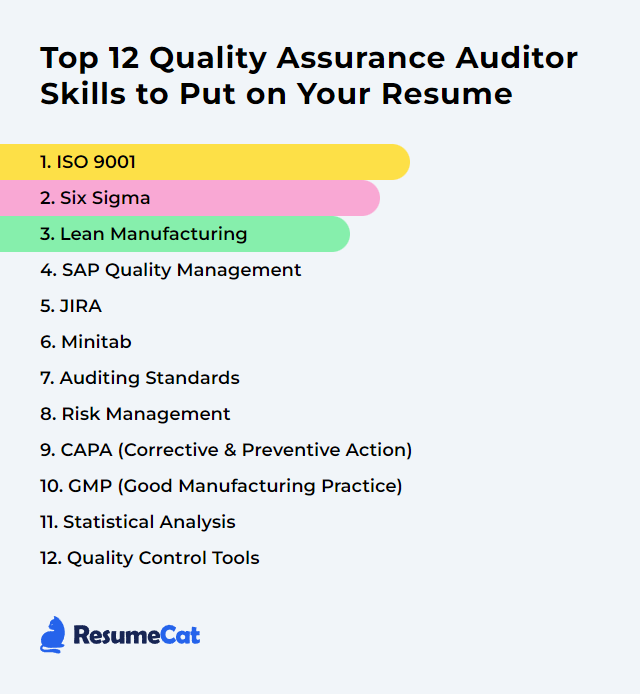
Quality Assurance Auditor Skills
- ISO 9001
- Six Sigma
- Lean Manufacturing
- SAP Quality Management
- JIRA
- Minitab
- Auditing Standards
- Risk Management
- CAPA (Corrective and Preventive Action)
- GMP (Good Manufacturing Practice)
- Statistical Analysis
- Quality Control Tools
1. ISO 9001
ISO 9001 is an international standard for quality management systems (QMS), specifying requirements for organizations to demonstrate their ability to consistently provide products and services that meet customer and regulatory requirements, aimed at enhancing customer satisfaction. For a Quality Assurance Auditor, it provides a framework and set of principles to assess an organization's processes and quality control measures to ensure they align with best practices for achieving quality objectives.
Why It's Important
ISO 9001 is important because it provides a universally recognized framework for establishing, implementing, and improving a quality management system, ensuring consistency, efficiency, and customer satisfaction in products and services, which is essential for a Quality Assurance Auditor to assess and enhance organizational performance and compliance.
How to Improve ISO 9001 Skills
Improving ISO 9001 involves a continuous effort to enhance the Quality Management System (QMS) processes to meet and exceed customer expectations efficiently. Here's a very short and concise guide tailored for a Quality Assurance Auditor:
Conduct Regular Audits: Regularly audit your QMS to identify areas for improvement, non-conformities, and best practices. Focus on both compliance and effectiveness of processes.
Engage Top Management: Ensure top management's commitment to the QMS by involving them in review meetings and decision-making processes. Their support is crucial for resource allocation and policy direction.
Employee Training: Continuously train employees on the importance of quality, their role in the QMS, and updates to ISO 9001 standards. Empowered employees contribute more effectively to process improvements.
Customer Feedback: Actively collect and analyze customer feedback to understand their needs and expectations. Use this information to make informed improvements to products and services.
Process Optimization: Regularly review and optimize processes for efficiency and effectiveness. Eliminate non-value-added activities and implement best practices.
Preventive Actions: Shift focus from corrective to preventive actions. Identify potential issues and implement changes to prevent them from occurring.
Management Review: Conduct management reviews of the QMS to ensure its continuing suitability, adequacy, and effectiveness. Use these reviews as opportunities for strategic planning and setting quality objectives.
Continuous Improvement: Foster a culture of continuous improvement by encouraging innovation and flexibility. Use tools like PDCA (Plan-Do-Check-Act) and Six Sigma for systematic improvements.
For detailed guidance and updates on ISO 9001, refer to ISO's official website and resources provided by the American Society for Quality (ASQ).
How to Display ISO 9001 Skills on Your Resume
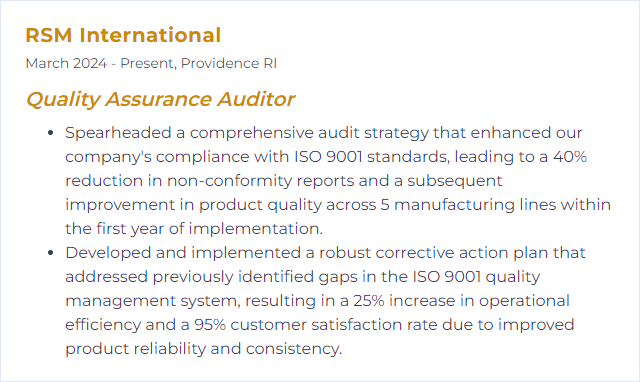
2. Six Sigma
Six Sigma is a data-driven methodology and set of tools aimed at process improvement by identifying and removing the causes of defects and minimizing variability in manufacturing and business processes, thereby ensuring quality and efficiency. For a Quality Assurance Auditor, it provides a structured approach to evaluate processes, measure performance against standards, and drive quality improvements.
Why It's Important
Six Sigma is important because it provides a structured, data-driven methodology for reducing defects, improving quality, and enhancing customer satisfaction, enabling Quality Assurance Auditors to ensure processes meet stringent quality standards effectively.
How to Improve Six Sigma Skills
To improve Six Sigma as a Quality Assurance Auditor, focus on the following short and concise strategies:
Enhance Understanding: Deepen your knowledge of Six Sigma methodologies by participating in advanced training programs. ASQ's Six Sigma Training offers comprehensive resources to refine your skills.
Implement DMAIC Rigorously: Ensure the DMAIC (Define, Measure, Analyze, Improve, Control) process is applied meticulously in projects. This structured approach is central to Six Sigma success. iSixSigma's DMAIC Overview provides a detailed guide.
Utilize Statistical Tools: Master statistical tools and software for quality improvement projects. Minitab is widely used for its powerful statistical capabilities in Six Sigma projects.
Focus on Customer Feedback: Incorporate customer feedback actively to align improvement efforts with customer expectations. Tools like SurveyMonkey can facilitate gathering and analyzing customer insights.
Promote Cross-Functional Collaboration: Foster collaboration across different departments to integrate diverse insights and expertise in the improvement process. Harvard Business Review's Insights on cross-functional teams offer strategies for effective collaboration.
Continuous Education: Stay updated with the latest trends, tools, and methodologies in Six Sigma and quality management by regularly accessing resources from Quality Magazine.
Implementing these strategies will significantly enhance your effectiveness as a Quality Assurance Auditor in applying Six Sigma methodologies.
How to Display Six Sigma Skills on Your Resume
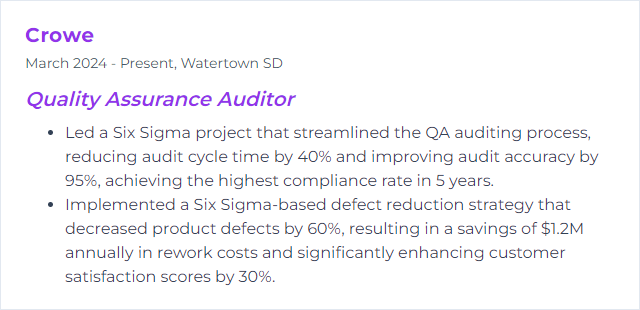
3. Lean Manufacturing
Lean Manufacturing is a systematic approach aimed at minimizing waste within manufacturing systems while simultaneously maximizing productivity. It focuses on enhancing quality and efficiency, ensuring value is defined from the customer's perspective. For a Quality Assurance Auditor, it emphasizes continuous improvement and the elimination of non-value-added activities to ensure consistent, high-quality outputs.
Why It's Important
Lean Manufacturing is important because it focuses on minimizing waste and maximizing efficiency in production processes, ensuring high-quality products are delivered consistently, which aligns with the goals of a Quality Assurance Auditor in monitoring and improving manufacturing standards.
How to Improve Lean Manufacturing Skills
Improving Lean Manufacturing, particularly from a Quality Assurance Auditor's perspective, involves focusing on continuous improvement and waste elimination to enhance product quality and manufacturing efficiency. Here are concise strategies:
Implement Kaizen: Encourage continuous, incremental improvements by involving all employees. Kaizen Institute offers insights on implementing this principle effectively.
Adopt Value Stream Mapping (VSM): Identify and minimize waste in the manufacturing process. The Lean Enterprise Institute provides resources on how to apply VSM.
Standardize Processes: Ensure consistency and efficiency in production. The ISO standards can serve as a guideline for establishing and maintaining high-quality processes.
Utilize 5S Methodology: Organize the workplace for efficiency and effectiveness. There's a straightforward guide on 5S from the Environmental Protection Agency (EPA).
Apply Poka-Yoke (Mistake Proofing): Implement error-proofing methods to prevent defects. ASQ offers a primer on Poka-Yoke techniques.
Conduct Regular Audits: Use audits to identify areas for improvement and ensure adherence to lean principles. Auditing for Continuous Improvement by ASQ can guide auditors in this aspect.
Foster a Culture of Quality: Engage and train employees at all levels to prioritize quality and lean manufacturing principles. Lean Culture discusses cultivating this environment.
By focusing on these strategies, Quality Assurance Auditors can significantly contribute to enhancing lean manufacturing processes, leading to improved efficiency, reduced waste, and higher product quality.
How to Display Lean Manufacturing Skills on Your Resume
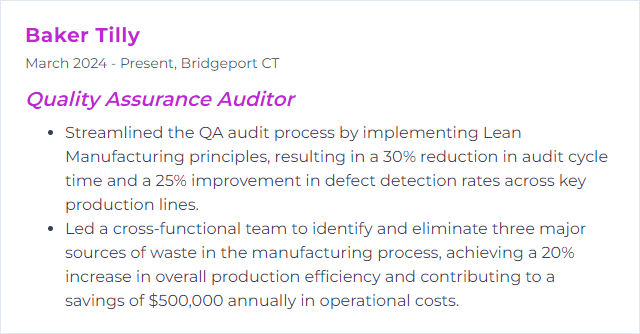
4. SAP Quality Management
SAP Quality Management (QM) is a component of the SAP ERP system designed to facilitate the planning, execution, and recording of quality control processes. It supports tasks such as quality planning, quality inspection, and quality control, enabling a Quality Assurance Auditor to ensure products and processes meet specified quality standards and regulatory requirements.
Why It's Important
SAP Quality Management (QM) is crucial for a Quality Assurance Auditor as it streamlines and automates the monitoring of quality standards, compliance, and processes within the organization. This ensures products meet regulatory requirements and customer expectations, reducing defects and enhancing customer satisfaction.
How to Improve SAP Quality Management Skills
Improving SAP Quality Management (QM) involves several steps geared towards enhancing the effectiveness and efficiency of quality assurance processes. For a Quality Assurance Auditor, focusing on these key actions can significantly optimize the SAP QM module:
Understand SAP QM Configuration: Gain a deep understanding of the SAP QM module's configuration settings. Tailor them to meet your organization's specific quality management needs. SAP's official configuration guide is a useful resource.
Integrate QM with Other Modules: Ensure seamless integration of the QM module with other relevant SAP modules like Materials Management (MM) and Production Planning (PP) for streamlined operations. SAP's integration guide provides insights into how these modules can work together effectively.
Leverage Data Analytics: Utilize SAP's analytics tools to monitor quality performance and identify areas for improvement. SAP's Advanced Analytics can help in deriving actionable insights from quality data.
Implement Automation: Where possible, automate routine QM tasks to increase efficiency and reduce human errors. SAP's Intelligent Robotic Process Automation offers solutions that can be customized for quality management tasks.
Continuous Training: Ensure ongoing training for all users of the SAP QM module to keep them updated on new features and best practices. SAP offers training and certification that can be particularly beneficial.
Regular Audits and Reviews: Conduct regular audits and reviews of the QM processes and system configurations to ensure they align with the changing business and regulatory requirements. Adopt a continuous improvement approach.
Engage with SAP Community: Participate in SAP QM forums and communities to share experiences and learn from peers. The SAP Community is a valuable resource for insights and solutions.
By focusing on these areas, a Quality Assurance Auditor can significantly contribute to enhancing the effectiveness of SAP Quality Management within their organization.
How to Display SAP Quality Management Skills on Your Resume
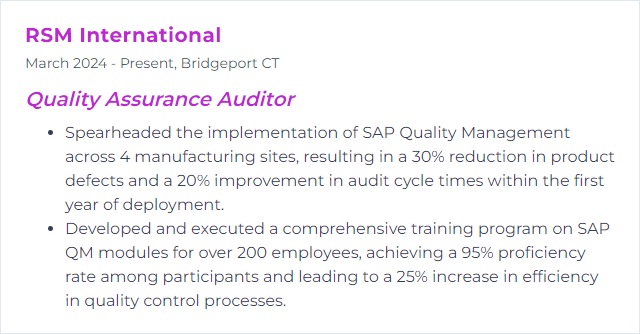
5. JIRA
JIRA is a project management and issue tracking software primarily used for bug tracking, project management, and operational workflow within software development and quality assurance processes. It enables tracking of individual tasks, sprints, and user stories, facilitating collaboration and ensuring quality standards are met throughout the development lifecycle.
Why It's Important
JIRA is important for a Quality Assurance Auditor because it enables effective tracking and management of bugs, tasks, and project progress, ensuring quality standards are met through detailed reporting and collaboration functionalities.
How to Improve JIRA Skills
Improving JIRA for a Quality Assurance Auditor involves optimizing issue tracking, workflow customization, and enhancing reporting features. To achieve this:
Customize Dashboards: Tailor JIRA dashboards to display relevant quality assurance metrics and issues for quick overview. Atlassian Documentation on Dashboards
Workflow Customization: Adapt workflows to mirror the QA process accurately, ensuring that every step from bug reporting to resolution is tracked. Workflow Customization Guide
Use of JIRA Query Language (JQL): Master JQL to create advanced searches for tracking defects, test cases, and ensuring no issue is missed. JQL Search Documentation
Integration with Test Management Tools: Integrate JIRA with external test management tools (e.g., Zephyr, Xray) to streamline the testing process. Zephyr for JIRA, Xray Test Management
Automate Repetitive Tasks: Utilize JIRA’s automation feature to automate repetitive tasks such as issue transitions and notifications. JIRA Automation Documentation
Enhance Reporting: Utilize and customize JIRA’s reporting features to generate insightful reports on bug trends, project statuses, and QA progress. Reporting in JIRA
Continuous Feedback Loop: Implement a feedback loop from the QA team back into the development process to continually refine and improve the process. Implementing Feedback Loops
By focusing on these areas, a Quality Assurance Auditor can significantly enhance the efficiency and effectiveness of using JIRA for quality assurance purposes.
How to Display JIRA Skills on Your Resume
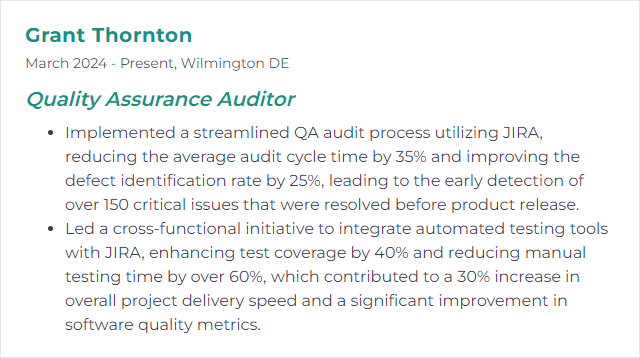
6. Minitab
Minitab is a statistical software tool used for data analysis, designed to help professionals in quality assurance and improvement processes by facilitating the analysis of data, identification of trends, and prediction of patterns, thus supporting decision-making and operational excellence.
Why It's Important
Minitab is important for a Quality Assurance Auditor because it provides powerful statistical analysis tools for monitoring quality, identifying trends, and evaluating process performance, thereby ensuring products or services meet desired specifications and standards.
How to Improve Minitab Skills
Improving your proficiency with Minitab as a Quality Assurance Auditor involves a blend of deepening your statistical knowledge, mastering Minitab features, and staying updated with new functionalities. Here’s a concise guide:
Understand Statistical Fundamentals: Strengthen your grasp of statistical concepts relevant to quality assurance, such as control charts, process capability, and hypothesis testing. This foundational knowledge is crucial for effectively applying Minitab's tools. Khan Academy's Statistics and Probability course is a free resource to brush up on these concepts.
Official Minitab Training: Enroll in Minitab's official training programs. These courses range from introductory to advanced levels, focusing on practical applications in quality improvement projects. Explore the available training sessions here.
Practice with Real Data: Apply what you learn by working on projects with real data. This hands-on approach will improve your skills in data analysis, interpretation, and decision-making. You can find datasets for practice on websites like Kaggle.
Join Minitab User Community: Engage with the Minitab user community to exchange knowledge, tips, and experiences. This can provide insights into advanced techniques and novel applications of Minitab in quality assurance. Join the community here.
Stay Updated: Minitab regularly updates its software to include new features and improvements. Keep yourself updated by exploring the latest versions and updates on the Minitab Blog, which also offers valuable tips and case studies.
Use Minitab Support: Leverage Minitab’s customer support for specific queries or challenges you face. Their support team can provide guidance tailored to your needs. Access support here.
By following these steps, you can significantly enhance your Minitab skills, thereby improving your efficiency and effectiveness as a Quality Assurance Auditor.
How to Display Minitab Skills on Your Resume
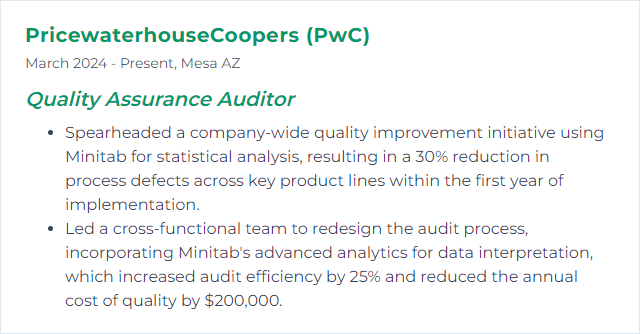
7. Auditing Standards
Auditing Standards are formal guidelines that define the principles and procedures to be followed by auditors when conducting an audit. These standards ensure consistency, reliability, and quality of audits, guiding auditors in their assessment of an organization's processes, controls, and records to verify compliance with established criteria, policies, and regulations.
Why It's Important
Auditing Standards are important for Quality Assurance Auditors as they ensure reliability, consistency, and accuracy in the auditing process, thereby upholding the credibility and quality of the audit outcomes.
How to Improve Auditing Standards Skills
Improving auditing standards, particularly for a Quality Assurance (QA) Auditor, involves continuously updating practices to ensure they align with current industry standards and technological advancements. Here are concise strategies to achieve this:
Continuous Education: Auditors should regularly update their knowledge through courses and certifications from reputable organizations. The Institute of Internal Auditors and ASQ offer various resources for auditors to stay current.
Adopting Technology: Embrace auditing software and tools that automate processes and improve accuracy. Tools like ACL and TeamMate help in data analysis and audit management.
International Standards: Ensure adherence to international standards like ISO 9001 for quality management systems, which provide a framework for quality assurance and continuous improvement.
Peer Review and Feedback: Implement a system for peer review and seek feedback from auditees to identify areas of improvement. The Peer Review Program by AICPA is a good reference.
Ethical Conduct and Independence: Uphold the highest standards of ethics and maintain independence to ensure unbiased auditing. The International Ethics Standards Board for Accountants offers guidance on ethical practices.
Risk-Based Auditing: Focus on risk-based auditing approaches to prioritize areas with higher risks. Resources like ISACA provide insights on incorporating IT governance and risk management.
By implementing these strategies, QA Auditors can enhance their auditing standards, ensuring they provide value and contribute to the continuous improvement of the organizations they audit.
How to Display Auditing Standards Skills on Your Resume
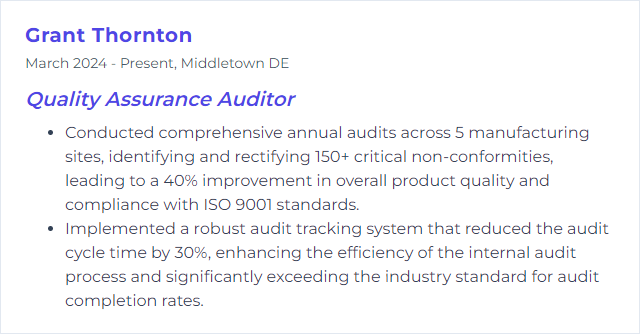
8. Risk Management
Risk Management, in the context of a Quality Assurance Auditor, involves identifying, assessing, and prioritizing risks to quality, followed by coordinating and applying resources to minimize, monitor, and control the probability or impact of undesirable events.
Why It's Important
Risk management is crucial for a Quality Assurance Auditor as it enables the identification, assessment, and prioritization of potential risks, ensuring that quality standards are maintained and regulatory requirements are met, thereby preventing errors, reducing the likelihood of non-compliance, and safeguarding product integrity and consumer safety.
How to Improve Risk Management Skills
Improving risk management, especially for a Quality Assurance Auditor, involves a systematic approach to identifying, analyzing, and responding to project risks. Here are concise steps to enhance risk management:
Identify Risks: Systematically identify potential risks that could affect the project or process. Use techniques like brainstorming, expert judgment, and checklists.
Analyze Risks: Evaluate the likelihood and impact of identified risks. Tools like Risk Matrix and SWOT analysis can be helpful. Risk Matrix Guide.
Prioritize Risks: Not all risks are equal. Use qualitative and quantitative risk analysis to prioritize them based on their impact and likelihood. Prioritizing Guide.
Develop Risk Responses: Create strategies for dealing with high-priority risks. Strategies include avoiding, mitigating, transferring, or accepting risks. Risk Response Strategies.
Implement Risk Responses: Execute the risk response plans and allocate resources to manage the risks effectively.
Monitor and Review: Regularly monitor risks and their responses. Update risk management plans as needed to address new or changing risks. Monitoring and Reviewing.
Continuous Improvement: Learn from risk management outcomes and incorporate lessons learned into future risk management activities. Tools like After Action Reviews (AAR) can facilitate this. Continuous Improvement in Risk Management.
Training and Awareness: Ensure all team members are aware of the importance of risk management and are trained in identifying and managing risks. Risk Management Training (PDF).
Incorporating these steps into your risk management process will help in effectively managing risks, ultimately leading to successful project outcomes and continuous quality improvement.
How to Display Risk Management Skills on Your Resume
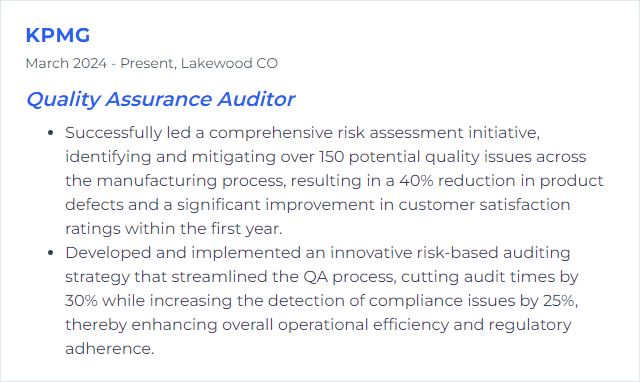
9. CAPA (Corrective and Preventive Action)
CAPA (Corrective and Preventive Action) is a quality management process that identifies, addresses, and eliminates the causes of detected nonconformities or other undesirable situations to prevent recurrence (corrective action) and to prevent occurrence (preventive action), ensuring continuous improvement and compliance in quality assurance systems.
Why It's Important
CAPA is essential for a Quality Assurance Auditor as it identifies, corrects, and eliminates recurring issues, ensuring compliance and improving the overall quality and safety of products or services.
How to Improve CAPA (Corrective and Preventive Action) Skills
Improving CAPA (Corrective and Preventive Action) involves a systematic approach focusing on identifying root causes, implementing effective solutions, and ensuring continuous improvement. Here's a very short and concise guide tailored for a Quality Assurance Auditor:
Root Cause Analysis: Utilize tools like the 5 Whys or Fishbone Diagrams to thoroughly understand the underlying issues.
Risk Assessment: Prioritize actions based on risk, using techniques like FMEA (Failure Mode and Effects Analysis).
Action Plan Development: Design corrective (fix current problem) and preventive (avoid recurrence) actions that are specific, measurable, achievable, relevant, and time-bound (SMART).
Implementation and Monitoring: Ensure effective implementation of actions and monitor the outcomes. Utilize Project Management Tools for tracking progress.
Effectiveness Verification: Validate the effectiveness of the CAPA through follow-up and use of Quality Metrics.
Documentation and Communication: Document all steps and communicate findings and status updates to relevant stakeholders. Consider ISO 9001 guidelines for documentation practices.
Continuous Improvement: Adopt a culture of continuous improvement, leveraging Lean Six Sigma methodologies to enhance processes and CAPA efficacy over time.
For a Quality Assurance Auditor, focusing on these steps within a structured CAPA system ensures compliance, improves product quality, and enhances customer satisfaction.
How to Display CAPA (Corrective and Preventive Action) Skills on Your Resume
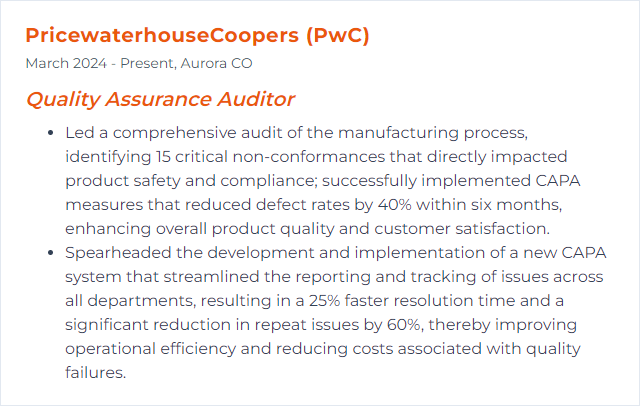
10. GMP (Good Manufacturing Practice)
GMP (Good Manufacturing Practice) is a system for ensuring products are consistently produced and controlled according to quality standards. It is designed to minimize the risks involved in any production process that cannot be eliminated through testing the final product. For a Quality Assurance Auditor, GMP represents the guidelines to audit against for verifying that the operational processes and procedures are in compliance with predefined quality criteria to ensure product safety and efficacy.
Why It's Important
GMP (Good Manufacturing Practice) is crucial as it ensures products are consistently produced and controlled according to quality standards, minimizing risks involved in production that cannot be eliminated through testing the final product. This foundation of quality assurance protects consumer safety and upholds product integrity.
How to Improve GMP (Good Manufacturing Practice) Skills
Improving Good Manufacturing Practice (GMP) involves several key steps that can be effectively implemented by a Quality Assurance Auditor to ensure compliance and enhance the quality of products. Here's a very short and concise guide:
Continuous Training: Ensure that all personnel, from the top management to the operational level, receive ongoing GMP training relevant to their roles. This helps maintain a high level of GMP awareness and compliance (FDA Training).
Regular Audits: Conduct regular internal and external GMP audits to identify non-compliance issues and areas for improvement. Use findings to implement corrective actions promptly (ISPE Guidelines).
Documentation: Maintain comprehensive, clear, and up-to-date documentation for all processes, procedures, and changes. This ensures traceability and accountability (ICH Guidelines).
Quality Risk Management: Implement a proactive approach to identifying, assessing, and managing risks to product quality throughout the product lifecycle (ICH Q9).
Feedback and CAPA: Establish a robust system for feedback, complaints, and non-conformity reports. Implement a Corrective and Preventive Action (CAPA) system to address issues systematically and prevent recurrence (FDA CAPA Guidance).
Supplier Quality Management: Carefully assess and monitor suppliers and subcontractors to ensure they meet your GMP standards. Quality agreements and regular audits are critical (EMA Guidelines).
Continuous Improvement: Foster a culture of continuous improvement by regularly reviewing processes, systems, and outcomes for potential enhancements.
By focusing on these areas, a Quality Assurance Auditor can significantly contribute to the improvement of GMP within their organization.
How to Display GMP (Good Manufacturing Practice) Skills on Your Resume
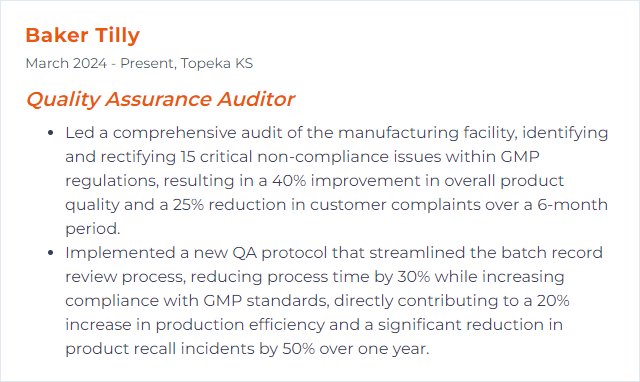
11. Statistical Analysis
Statistical analysis is the process of collecting, examining, interpreting, and presenting numerical data to uncover patterns, trends, and relationships, aiding in decision-making and quality improvement efforts within quality assurance contexts.
Why It's Important
Statistical analysis is crucial for a Quality Assurance Auditor as it enables the identification and quantification of process variations and defects, ensuring product consistency, reliability, and adherence to quality standards. It facilitates data-driven decision-making for continuous improvement and regulatory compliance.
How to Improve Statistical Analysis Skills
Improving statistical analysis, especially for a Quality Assurance Auditor, involves enhancing both the understanding and application of statistical tools and techniques. Here's a concise guide:
Enhance Statistical Knowledge: Strengthen your foundation in statistics. Khan Academy offers comprehensive lessons on statistical concepts.
Utilize Software Tools: Become proficient in statistical software like Minitab or R, which are crucial for efficient data analysis.
Understand Quality Standards: Familiarize yourself with quality standards relevant to your industry, as they often dictate the statistical methods to be used. The American Society for Quality (ASQ) provides resources and training.
Continuous Learning: Stay updated with the latest in statistical methods and quality assurance trends through webinars and courses from platforms like Coursera or edX.
Practice Data Interpretation: Improve your data interpretation skills by regularly analyzing real-world data sets related to your field. This enhances your ability to draw meaningful conclusions and make informed decisions.
Peer Review: Engage in peer reviews of statistical analysis within your network or through professional forums such as Cross Validated, a Q&A site for statisticians.
Ethical Considerations: Understand the ethical implications of your analyses. The American Statistical Association provides guidelines for ethical statistical practice.
By focusing on these areas, a Quality Assurance Auditor can significantly improve their statistical analysis skills, leading to more accurate and reliable quality assessments.
How to Display Statistical Analysis Skills on Your Resume
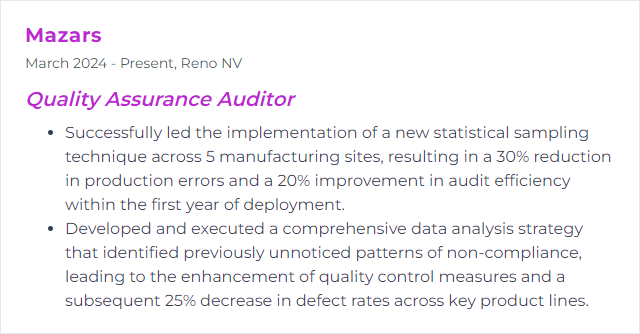
12. Quality Control Tools
Quality Control Tools are techniques and instruments used by Quality Assurance Auditors to analyze, measure, and monitor the quality of processes and products, ensuring they meet specified standards and requirements. These tools help in identifying defects, analyzing root causes, and implementing corrective actions to maintain or improve quality.
Why It's Important
Quality Control Tools are essential for a Quality Assurance Auditor as they provide systematic methods to identify, analyze, and correct defects, ensuring that products or services meet specified quality standards, thereby minimizing errors and enhancing customer satisfaction.
How to Improve Quality Control Tools Skills
Improving Quality Control Tools involves a systematic approach focused on enhancing the efficiency and effectiveness of the tools used in monitoring and improving product or service quality. Here are concise steps tailored for a Quality Assurance Auditor:
Educate and Train: Ensure all team members are well-trained on the latest quality control methodologies and tools. Continuous education on ASQ (American Society for Quality) can keep the team updated.
Implement Statistical Process Control (SPC): Utilize SPC to monitor and control quality by tracking process behavior. Learn more about SPC at MoreSteam.
Adopt Lean Six Sigma Principles: Integrate Lean Six Sigma to eliminate waste and reduce variation in processes. A useful resource is iSixSigma.
Regular Audits and Reviews: Conduct regular audits and utilize the findings to improve processes. Guidance on conducting effective audits can be found at ISO (International Organization for Standardization).
Use Quality Management Software: Implement software tools designed for quality management to streamline processes and improve tracking. Explore options at Capterra.
Feedback Loops: Create mechanisms for timely feedback from customers and employees to identify areas for improvement quickly.
Benchmarking: Regularly compare your quality metrics against industry standards or leaders. The Benchmarking Network can be a starting point.
Root Cause Analysis (RCA): When issues arise, utilize RCA tools like the 5 Whys or Fishbone Diagram to identify and address the underlying causes. MindTools offers a good overview.
Continuous Improvement (Kaizen): Foster a culture of continuous improvement within your organization. Kaizen principles are well explained at Kaizen Institute.
Invest in Technology and Innovation: Stay abreast of the latest technological advancements that can improve quality control processes. Engaging with TechCrunch or Wired can keep you updated on technology trends.
By focusing on these areas, a Quality Assurance Auditor can significantly enhance the effectiveness of Quality Control Tools within their organization.
How to Display Quality Control Tools Skills on Your Resume
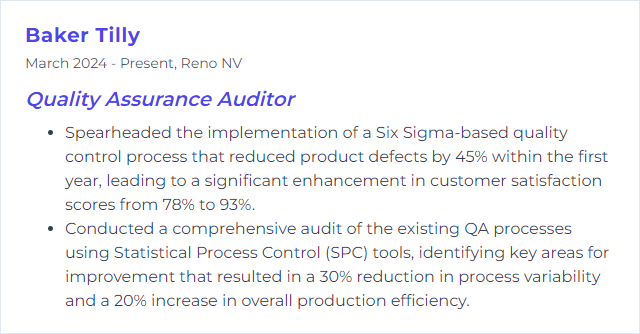