Top 12 Production Team Leader Skills to Put on Your Resume
In the fast-paced world of production, having a resume that captures your leadership prowess is crucial for standing out. Highlighting your top production team leader skills effectively communicates your ability to drive efficiency, manage resources, and lead a team towards achieving operational excellence.
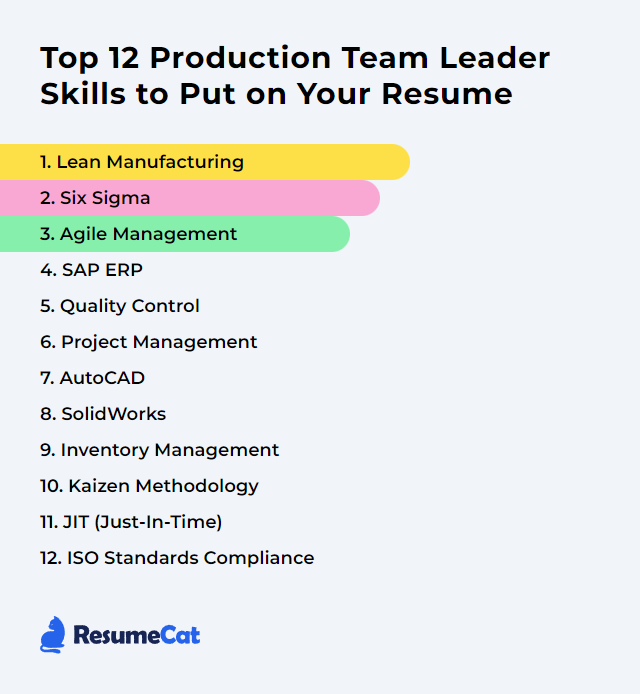
Production Team Leader Skills
- Lean Manufacturing
- Six Sigma
- Agile Management
- SAP ERP
- Quality Control
- Project Management
- AutoCAD
- SolidWorks
- Inventory Management
- Kaizen Methodology
- JIT (Just-In-Time)
- ISO Standards Compliance
1. Lean Manufacturing
Lean Manufacturing is a systematic approach to optimizing production processes by minimizing waste and maximizing efficiency, focusing on value creation for the customer. For a Production Team Leader, it involves leading and training teams to continuously identify and eliminate non-value-adding activities, improving workflow, quality, and productivity.
Why It's Important
Lean Manufacturing is important because it helps in reducing waste, improving efficiency, and increasing productivity, enabling a Production Team Leader to achieve higher quality output, lower costs, and faster delivery times, leading to enhanced customer satisfaction and competitive advantage.
How to Improve Lean Manufacturing Skills
To improve Lean Manufacturing as a Production Team Leader, focus on the following concise strategies:
Continuous Improvement (Kaizen): Encourage and facilitate continuous small improvements by the team. Foster an environment where every team member feels responsible for suggesting and implementing improvements. More on Kaizen
5S Methodology: Implement and maintain the 5S (Sort, Set in order, Shine, Standardize, Sustain) to improve efficiency and eliminate waste. This methodology helps in organizing the workplace in an efficient and safe manner. Learn about 5S
Value Stream Mapping: Identify and map all the steps in the production process, from material sourcing to final product delivery, to visualize waste and areas for improvement. Value Stream Mapping Guide
Just-In-Time (JIT) Production: Minimize inventory and reduce waste by producing just enough products, just in time to meet demand. This requires precise coordination and communication within the team. Understanding JIT
Empower Your Team: Empower your team members by involving them in decision-making processes, recognizing their contributions, and providing opportunities for learning and growth. This increases engagement and innovation. Team Empowerment Strategies
Root Cause Analysis: When problems occur, use tools like the Five Whys or Fishbone Diagram to dig deep and find the root cause, rather than just addressing symptoms. This leads to more effective long-term solutions. Root Cause Analysis Techniques
Cross-Training: Promote flexibility and resilience by cross-training your team members. This ensures that the production line can maintain efficiency even when facing absences or shifting demands. Benefits of Cross-Training
Integrating these strategies into your leadership approach can significantly enhance the lean manufacturing process, driving efficiency, reducing waste, and improving overall productivity.
How to Display Lean Manufacturing Skills on Your Resume
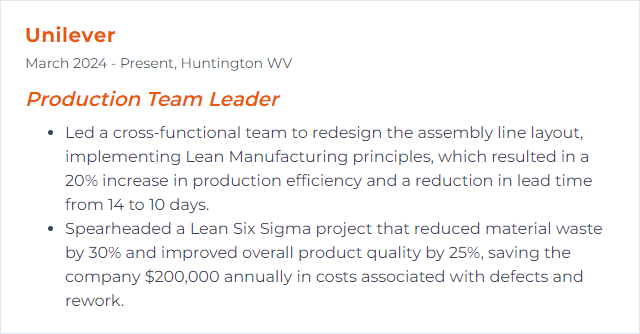
2. Six Sigma
Six Sigma is a data-driven methodology and set of tools aimed at improving production processes by reducing defects and variability, ensuring quality control, and enhancing efficiency, directly supporting a Production Team Leader's goals to achieve operational excellence and customer satisfaction.
Why It's Important
Six Sigma is important for a Production Team Leader because it provides a systematic approach to reducing defects, improving processes, and increasing efficiency, leading to higher product quality, customer satisfaction, and cost savings.
How to Improve Six Sigma Skills
To improve Six Sigma as a Production Team Leader, focus on:
Education and Certification: Enhance your understanding and skills in Six Sigma methodologies by pursuing relevant certifications (e.g., Yellow Belt, Green Belt).
Process Mapping: Employ process mapping to identify inefficiencies and areas for improvement in your production processes.
Data Analysis: Leverage statistical analysis tools like Minitab for data-driven decision-making, identifying root causes, and forecasting improvements.
Employee Involvement: Foster a culture of continuous improvement by involving your team in idea generation and problem-solving activities (Kaizen).
Communication and Feedback: Maintain open channels of communication with your team and stakeholders to gather feedback and implement changes effectively.
Benchmarking: Regularly compare your processes with industry best practices to identify areas for improvement.
Integrating these strategies will enhance your Six Sigma implementation, leading to higher efficiency and quality in your production processes.
How to Display Six Sigma Skills on Your Resume
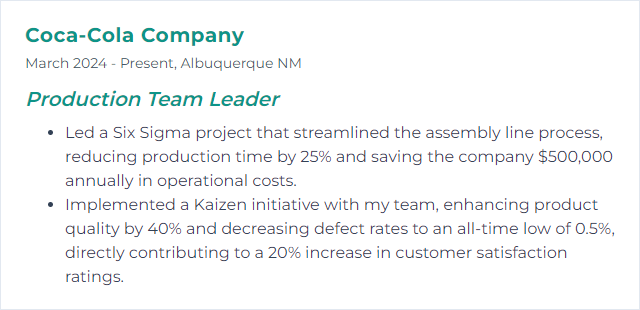
3. Agile Management
Agile Management is a flexible and iterative approach to project management, focusing on delivering value through collaborative, cross-functional teams. It emphasizes adaptability to change, continuous improvement, and customer satisfaction. For a Production Team Leader, it means leading by facilitating rapid, incremental progress, empowering team members, and actively responding to evolving project requirements.
Why It's Important
Agile Management is important for a Production Team Leader because it enhances flexibility, improves product quality, accelerates time to market, fosters collaboration, and enables better response to customer feedback and market changes.
How to Improve Agile Management Skills
Improving Agile Management, especially for a Production Team Leader, involves focusing on enhancing collaboration, flexibility, and continuous improvement. Here are concise strategies with relevant resources:
Foster a Collaborative Environment: Encourage open communication and teamwork. Use tools like Trello or Jira to track progress and facilitate collaboration.
Embrace Change: Be open to adapting plans based on feedback and changing circumstances. The Agile Manifesto emphasizes responding to change over following a plan.
Continuous Improvement: Implement regular retrospectives to identify what went well and what can be improved. The Retrospective Guide from Scrum.org provides a framework.
Empower Your Team: Give team members the autonomy to make decisions. This Harvard Business Review article discusses creating a culture of empowerment.
Focus on Customer Value: Prioritize work that delivers the most value to the customer. The Lean Agile Institute provides principles on focusing on customer value.
Utilize Agile Metrics: Track progress and productivity using Agile metrics. The Agile Alliance offers insights into various Agile metrics.
By implementing these strategies, a Production Team Leader can enhance Agile management practices, leading to more efficient and effective team performance.
How to Display Agile Management Skills on Your Resume
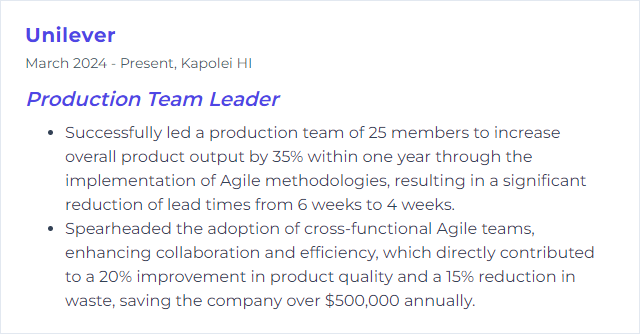
4. SAP ERP
SAP ERP is a comprehensive enterprise resource planning software that integrates all facets of business operations, including production, inventory, sales, and finance, enabling a Production Team Leader to efficiently manage and optimize manufacturing processes, resources, and workflow for improved productivity and performance.
Why It's Important
SAP ERP is crucial for a Production Team Leader as it integrates all facets of production management, enabling real-time tracking of operations, resources, and inventory. This ensures efficient production planning, timely execution, and optimal resource utilization, significantly enhancing productivity and decision-making.
How to Improve SAP ERP Skills
To improve SAP ERP for a Production Team Leader, focus on:
Training: Enhance team skills through targeted SAP training courses. Understanding SAP's full capabilities ensures better use and problem-solving skills.
Customization: Tailor SAP ERP interfaces and workflows to match the production team's specific needs. SAP's customization guide provides insights on how to adapt the system.
Integration: Streamline processes by integrating SAP ERP with other tools and platforms the production team uses. SAP Integration Suite offers solutions for seamless connectivity.
Automation: Implement automation within SAP ERP for repetitive tasks to save time and reduce errors. Explore SAP Intelligent Robotic Process Automation for potential applications.
Performance Monitoring: Utilize SAP's built-in analytics and reporting tools to monitor and improve production performance. The SAP Performance Optimization Guide is a valuable resource.
Feedback Loop: Establish a feedback mechanism for the production team to report issues or suggest improvements in SAP ERP usage. This continuous improvement approach ensures the system evolves to meet the team's changing needs.
By focusing on these areas, a Production Team Leader can significantly enhance the effectiveness of SAP ERP for their team.
How to Display SAP ERP Skills on Your Resume
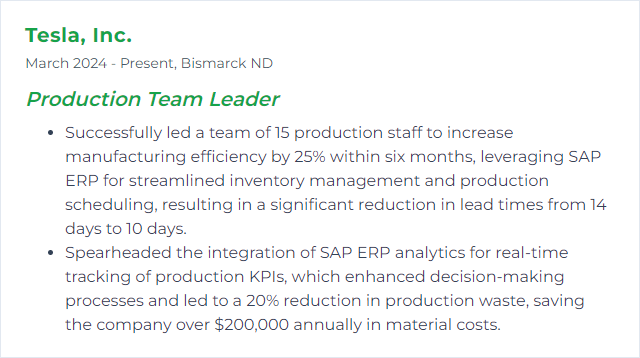
5. Quality Control
Quality Control (QC) involves the processes and procedures a Production Team Leader implements to ensure the products meet specific standards of quality before being delivered to customers. It focuses on identifying defects and preventing quality issues during the manufacturing process.
Why It's Important
Quality Control is crucial as it ensures the products meet specific standards and requirements, reducing defects and customer complaints. This leads to higher customer satisfaction, loyalty, and repeat business, ultimately enhancing the company's reputation and profitability. For a Production Team Leader, it helps in managing resources efficiently, improving production processes, and fostering a culture of continuous improvement among the team.
How to Improve Quality Control Skills
Improving Quality Control as a Production Team Leader involves several focused strategies to ensure products meet or exceed customer expectations and standards. Here are concise steps you can take:
Educate and Train Team: Ensure your team is well-informed about quality standards and techniques. Invest in regular training sessions.
Implement Quality Standards: Adopt and adhere to industry-specific quality standards such as ISO 9001.
Use Quality Tools: Utilize tools like Six Sigma and Lean manufacturing to identify and eliminate waste and defects.
Continuous Monitoring and Feedback: Implement real-time monitoring systems and establish a feedback loop for ongoing improvement. Tools like SPC (Statistical Process Control) can be useful.
Supplier Quality Management: Ensure your suppliers meet quality standards. Supplier evaluations and audits are key.
Foster a Quality Culture: Encourage a culture that prioritizes quality in every task. Creating a culture of quality requires commitment and communication.
Regular Reviews and Improvements: Conduct regular quality audits and reviews to identify areas for improvement.
By focusing on these areas, you can significantly improve the quality control process within your production team.
How to Display Quality Control Skills on Your Resume
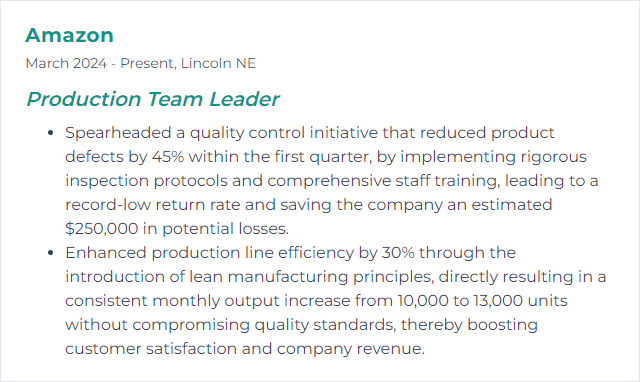
6. Project Management
Project management involves planning, executing, and overseeing tasks to achieve specific goals within a set timeline and budget, ensuring the efficient production and delivery of products or services. For a Production Team Leader, it means coordinating team efforts to meet project objectives, managing resources, and ensuring quality output on schedule.
Why It's Important
Project management is crucial for a Production Team Leader as it ensures efficient coordination of tasks, resources, and timelines, leading to the successful completion of projects while meeting quality, budget, and deadline goals.
How to Improve Project Management Skills
Improving project management, especially for a Production Team Leader, involves a focused approach on planning, execution, and team collaboration. Here are concise strategies with relevant resources:
Define Clear Objectives: Start by setting clear, achievable goals. Smartsheet's guide on goal setting can help streamline this process.
Effective Communication: Foster an environment of open communication. Asana's communication tips offer strategies for improving team interactions.
Utilize Project Management Tools: Adopt tools like Trello or Jira to organize tasks, deadlines, and responsibilities efficiently.
Monitor Progress Regularly: Keep track of project progress and adjust plans as necessary. Tools like Monday.com provide visual progress tracking.
Risk Management: Anticipate potential problems and have contingency plans in place. ProjectManager.com's risk management guide offers insights on identifying and managing risks.
Delegate Effectively: Match tasks with team members' skills and capacities. MindTools on delegation explains how to do this effectively.
Continuous Learning and Improvement: Encourage feedback and learn from each project. Harvard Business Review's article on learning to learn enhances this approach.
By implementing these strategies, a Production Team Leader can significantly improve project management outcomes.
How to Display Project Management Skills on Your Resume
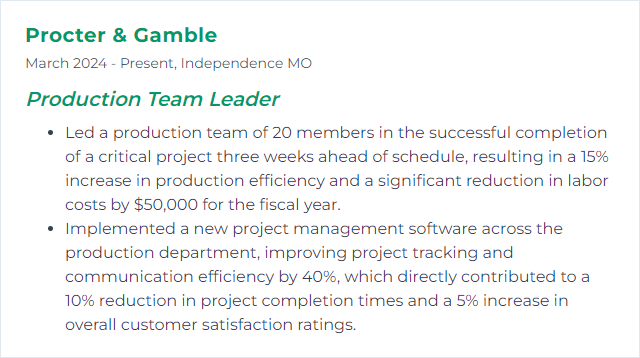
7. AutoCAD
AutoCAD is a computer-aided design (CAD) software used for creating precise 2D and 3D drawings, essential for planning, designing, and optimizing production processes.
Why It's Important
AutoCAD is crucial for a Production Team Leader as it enables precise, efficient design and modification of production layouts and machinery parts, ensuring optimal workflow, reducing material waste, and improving product quality.
How to Improve AutoCAD Skills
To improve AutoCAD for a Production Team Leader, consider the following concise strategies:
- Enhance Skills: Encourage team members to participate in AutoCAD training courses to keep their skills updated and improve productivity.
- Customize Tool Palettes: Customize AutoCAD tool palettes for specific project needs to streamline workflows.
- Implement CAD Standards: Develop and enforce CAD standards to ensure consistency and efficiency in the production process.
- Use AutoCAD Mobile App: Leverage the AutoCAD mobile app for on-the-go access and collaboration, enhancing communication and flexibility.
- Automate Repetitive Tasks: Utilize AutoLISP scripts to automate repetitive tasks, saving time and reducing errors.
- Regularly Update Software: Ensure your team is using the latest version of AutoCAD, taking advantage of new features and improvements.
By focusing on these areas, a Production Team Leader can significantly improve the efficiency and productivity of their AutoCAD operations.
How to Display AutoCAD Skills on Your Resume
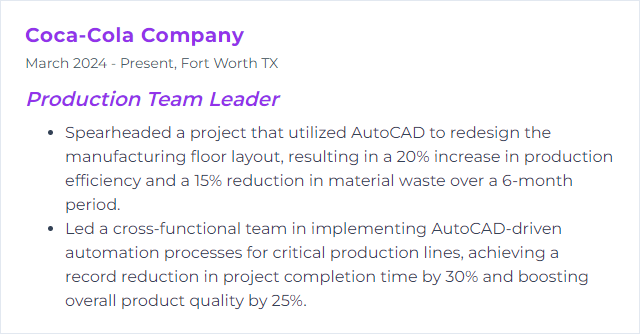
8. SolidWorks
SolidWorks is a computer-aided design (CAD) and computer-aided engineering (CAE) software program used for creating 2D and 3D models and technical drawings, primarily for mechanical design and product development. It enables production team leaders to visualize, simulate, and manage engineering projects, facilitating efficient design, prototyping, and production processes.
Why It's Important
SolidWorks is essential for a Production Team Leader because it enables efficient design, simulation, and modification of products before manufacturing, ensuring cost-effective production, quality assurance, and faster time-to-market.
How to Improve SolidWorks Skills
Improving SolidWorks for a Production Team Leader involves enhancing efficiency, collaboration, and data management. Here are concise strategies:
Training: Invest in SolidWorks training for your team to boost productivity and ensure they are up-to-date with the latest features and best practices.
Templates and Standards: Create and utilize custom templates and standards to streamline design processes and maintain consistency across projects.
PDM System: Implement a Product Data Management (PDM) system to efficiently manage and share design data, reducing errors and saving time.
Performance Evaluation: Regularly review and optimize your SolidWorks settings and hardware based on the SolidWorks Performance Test to ensure the software runs smoothly and efficiently.
Collaboration Tools: Leverage collaboration tools like SolidWorks Collaborative Business Innovator on the 3DEXPERIENCE platform to enhance teamwork and project management.
Automation: Utilize SolidWorks APIs for custom automation scripts and macros to speed up repetitive tasks and improve accuracy.
Feedback Loop: Establish a feedback loop with your design team to continuously identify bottlenecks and areas for improvement in your SolidWorks workflow.
By focusing on these areas, a Production Team Leader can significantly enhance the efficiency and effectiveness of their team's use of SolidWorks.
How to Display SolidWorks Skills on Your Resume
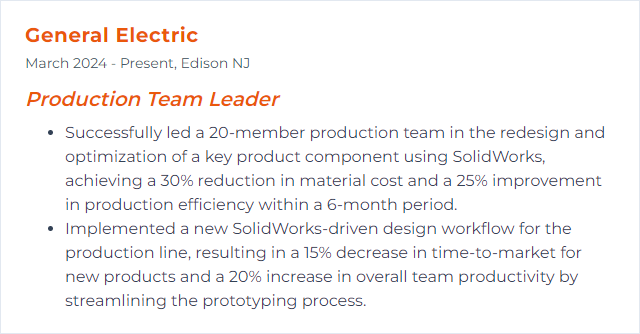
9. Inventory Management
Inventory management is the process of overseeing and controlling the ordering, storage, and use of components that a company uses in the production of the items it sells, as well as the management of finished products that are ready for sale. For a Production Team Leader, it involves ensuring that the right quantity of materials is available at the right time to meet production schedules while minimizing holding costs and avoiding shortages.
Why It's Important
Inventory management is crucial for a Production Team Leader as it ensures the right materials are available when needed, preventing production delays, minimizing excess stock and storage costs, and optimizing the production process for efficiency and cost-effectiveness.
How to Improve Inventory Management Skills
Improving inventory management involves optimizing the balance between stock availability and the costs of holding inventory. As a Production Team Leader, focus on the following strategies:
Implement Just-In-Time (JIT) Inventory: JIT minimizes inventory levels by ordering parts only as needed for production. Learn more about JIT.
Use Inventory Management Software: Automate tracking of inventory levels, orders, sales, and deliveries. Tools like Fishbowl and NetSuite offer comprehensive solutions. Explore Fishbowl and NetSuite options.
Conduct Regular Audits: Regularly reconcile inventory data through physical counts and compare with what's recorded in your system. Here's how to conduct inventory audits.
Improve Forecasting: Use historical sales data, market trends, and seasonality to predict future inventory needs. Forecasting techniques can guide you.
Adopt ABC Analysis: Categorize inventory into three categories (A, B, and C) based on importance and value. Focus more on 'A' items. ABC Analysis explained.
Enhance Supplier Relationships: Strong relationships can lead to better prices, terms, and reliability. Building supplier relationships.
Train Your Team: Ensure your team understands inventory management practices and the importance of accuracy. Effective training strategies.
By strategically implementing these practices, you can significantly improve inventory management in your production environment.
How to Display Inventory Management Skills on Your Resume
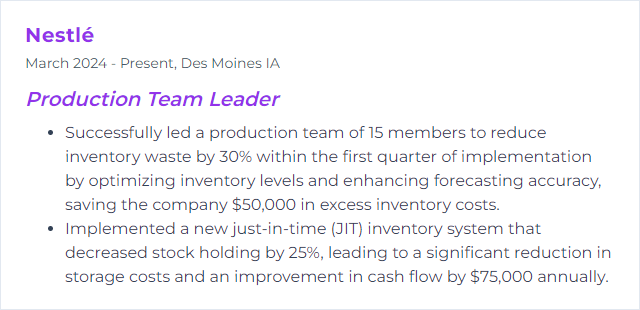
10. Kaizen Methodology
Kaizen Methodology is a continuous improvement strategy that involves every employee - from upper management to the production line workers - in an effort to reduce waste and improve efficiency, quality, and safety. For a Production Team Leader, it means actively engaging and empowering the team to identify and solve problems incrementally to enhance production processes and outcomes.
Why It's Important
Kaizen methodology is important for a Production Team Leader because it promotes continuous, incremental improvements in processes, enhancing efficiency, reducing waste, and improving productivity and teamwork on the production floor.
How to Improve Kaizen Methodology Skills
To improve Kaizen methodology as a Production Team Leader, focus on the following steps:
Educate Your Team: Ensure all team members understand the Kaizen principles and their benefits. Engage them in continuous learning.
Set Clear Goals: Define clear, achievable goals related to productivity, quality, or waste reduction. Use SMART criteria for goal setting.
Implement 5S: Start with the 5S technique (Sort, Set in order, Shine, Standardize, Sustain) to organize and streamline the work environment.
Encourage Small Improvements: Motivate your team to suggest and implement small improvements continuously. This can be done through suggestion boxes or regular team meetings.
Utilize Visual Management: Implement visual management tools like Kanban boards to make workflows and progress visible to everyone.
Measure and Analyze: Regularly measure the outcomes of implemented changes and analyze data to understand their impact. Tools like Pareto charts can be helpful.
Celebrate Successes: Recognize and celebrate improvements, no matter how small, to keep the team motivated.
Iterate and Standardize: Once an improvement proves successful, standardize the process and iterate to find further improvements.
By following these steps and fostering a culture of continuous improvement, you can enhance the effectiveness of Kaizen in your production team.
How to Display Kaizen Methodology Skills on Your Resume
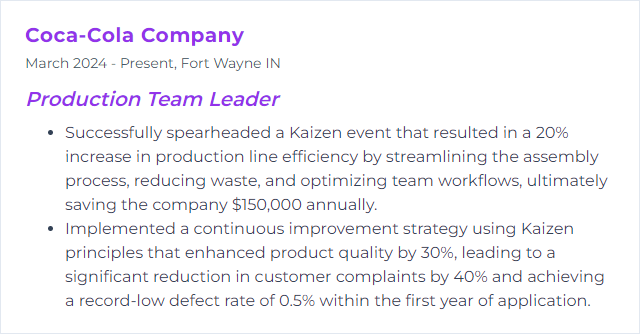
11. JIT (Just-In-Time)
JIT (Just-In-Time) is a production strategy aimed at reducing inventory and increasing efficiency by receiving goods and producing items only as they are needed for immediate use or sale, minimizing waste and reducing costs.
Why It's Important
JIT (Just-In-Time) is important because it reduces inventory costs, increases efficiency, and improves product quality by producing goods only as they are needed, minimizing waste and enhancing responsiveness to customer demand.
How to Improve JIT (Just-In-Time) Skills
To improve JIT (Just-In-Time) in a production environment, a Production Team Leader should focus on the following strategies:
Streamline Supply Chain: Partner closely with suppliers to ensure timely and reliable delivery of materials. Supply Chain Management.
Implement Kanban Systems: Utilize Kanban cards or digital tools to visualize workflow and balance production load. Kanban Tool.
Optimize Inventory Levels: Regularly review and adjust inventory levels to minimize excess while avoiding shortages. Inventory Management Guide.
Enhance Quality Control: Implement continuous improvement and quality control measures to reduce defects and rework. Total Quality Management.
Train and Empower Employees: Foster a culture of continuous improvement and empower employees to identify and solve JIT-related issues. Employee Empowerment.
Leverage Technology: Use ERP and JIT-specific software to improve planning, scheduling, and real-time tracking. ERP Software.
Regularly Review Processes: Continuously analyze and refine production processes to eliminate waste and inefficiencies. Process Improvement.
By focusing on these areas, a Production Team Leader can enhance JIT efficiency, reduce waste, and improve productivity.
How to Display JIT (Just-In-Time) Skills on Your Resume
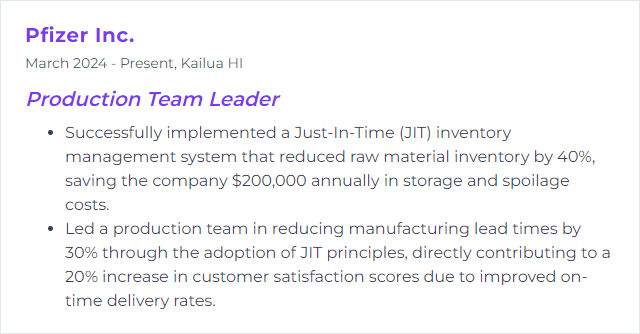
12. ISO Standards Compliance
ISO Standards Compliance refers to the adherence of a production team and its processes to internationally recognized guidelines and practices set by the International Organization for Standardization (ISO). These standards ensure quality, safety, efficiency, and consistency in production activities, aiming to enhance product quality, reduce waste, and increase customer satisfaction. Compliance involves implementing, maintaining, and continuously improving processes to meet specific ISO standards relevant to the production field.
Why It's Important
ISO standards compliance ensures consistent quality, efficiency, and safety in production processes, enhancing product reliability, customer satisfaction, and market competitiveness — crucial for a Production Team Leader in maintaining operational excellence and regulatory adherence.
How to Improve ISO Standards Compliance Skills
Improving ISO Standards Compliance for a Production Team Leader involves a focused approach on understanding, implementing, and maintaining the requirements of the relevant ISO standards. Here's a concise guide:
Educate Yourself and Your Team: Start with comprehensive training about the specific ISO standards applicable to your production processes. ISO's official site provides resources and training materials.
Implement a Quality Management System (QMS): Develop and implement a QMS that aligns with ISO requirements, such as ISO 9001 for quality management. Documentation, process control, and continuous improvement are key components. The ISO 9000 family page offers guidance.
Regular Audits and Reviews: Conduct internal audits to review compliance with ISO standards and identify areas for improvement. Use the findings to enhance your processes continually. ISO's auditing standards can provide a framework.
Engage with Certified Bodies for External Audits: Schedule external audits with ISO-certified bodies to gain an unbiased view of your compliance level and receive certification. The International Accreditation Forum (IAF) lists accredited certification bodies.
Foster a Culture of Continuous Improvement: Encourage feedback and suggestions from your team for improving processes and compliance. Implementing a Kaizen or continuous improvement approach can be beneficial.
Stay Updated on Standards and Regulatory Changes: ISO standards can evolve, so it's crucial to stay informed about any updates or changes. Regularly visit ISO's website and subscribe to relevant newsletters for updates.
By focusing on these steps, a Production Team Leader can significantly improve their team's compliance with ISO standards, leading to better quality, efficiency, and market credibility.
How to Display ISO Standards Compliance Skills on Your Resume
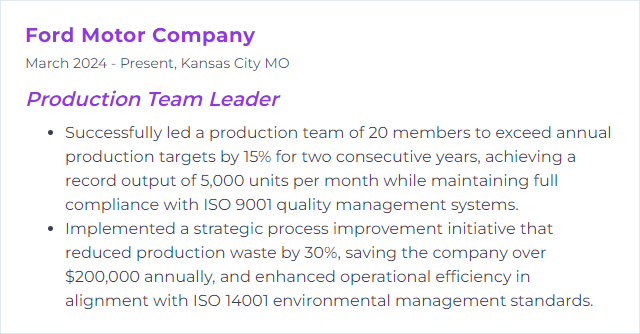