Top 12 Mill Operator Skills to Put on Your Resume
In the competitive field of mill operation, having a standout resume is crucial for securing the best positions. Highlighting a strong set of specific skills can demonstrate your expertise and readiness to excel in this technically demanding role, making you a top candidate for potential employers.
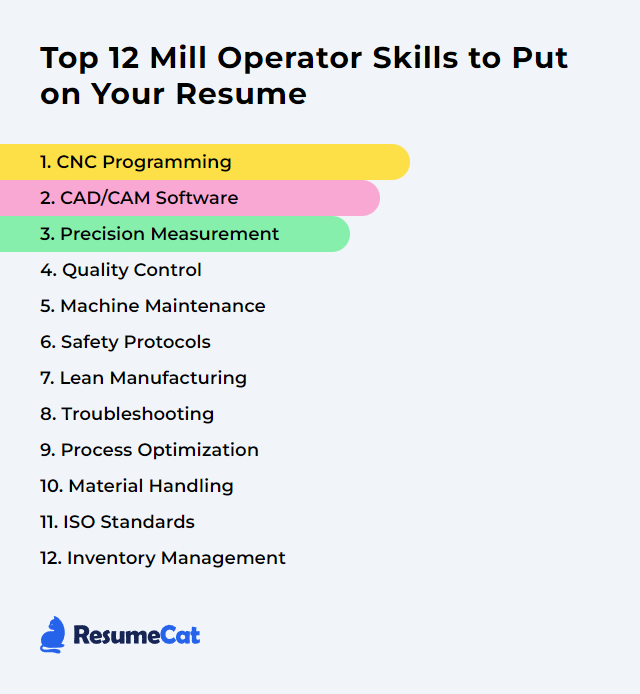
Mill Operator Skills
- CNC Programming
- CAD/CAM Software
- Precision Measurement
- Quality Control
- Machine Maintenance
- Safety Protocols
- Lean Manufacturing
- Troubleshooting
- Process Optimization
- Material Handling
- ISO Standards
- Inventory Management
1. CNC Programming
CNC programming for a mill operator involves creating computer instructions to precisely control the movements and operations of a CNC milling machine, enabling it to cut and shape material into a specified design or part.
Why It's Important
CNC programming is crucial for a Mill Operator as it precisely controls and automates milling machine operations, ensuring accurate, consistent, and efficient production of parts.
How to Improve CNC Programming Skills
Improving CNC programming for a Mill Operator involves enhancing efficiency, accuracy, and the overall quality of machining processes. Here are concise strategies:
Master CAD/CAM Software: Deepen your understanding of CAD/CAM software functionalities. Use tutorials from Autodesk to learn advanced techniques.
Optimize Toolpaths: Implement efficient toolpath strategies to reduce machining time and wear on tools. Explore Mastercam's Toolpaths for optimization techniques.
Utilize Simulation Tools: Use simulation tools to preemptively identify and correct potential errors or inefficiencies. Fusion 360 offers comprehensive simulation capabilities.
Stay Updated with Trends: The CNC field is continually evolving. Follow platforms like Modern Machine Shop for the latest industry trends and technologies.
Implement Standardization: Develop and adhere to a set of programming standards to ensure consistency and efficiency in your work. The National Institute for Metalworking Skills (NIMS) provides guidelines that can help in establishing such standards.
Enhance Communication: Effective communication with the machining team can provide insights into practical challenges, leading to more practical programming.
By focusing on these key areas, a Mill Operator can significantly improve their CNC programming skills and output.
How to Display CNC Programming Skills on Your Resume
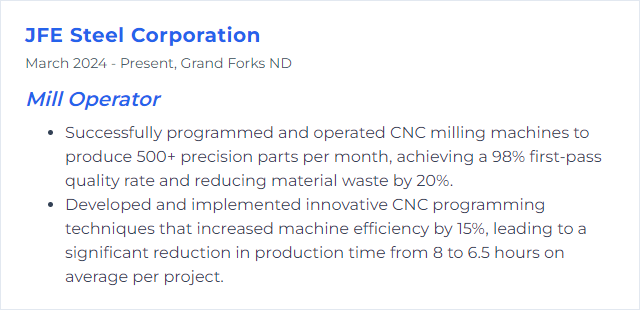
2. CAD/CAM Software
CAD/CAM software is a computer-aided design and manufacturing tool that allows mill operators to create designs, plan machining processes, and control CNC machine tools for efficient and precise production of parts.
Why It's Important
CAD/CAM software is crucial for a Mill Operator as it streamlines the design and manufacturing process, allowing for precise control over machining operations, reducing material waste, improving efficiency, and enabling the creation of complex designs that would be difficult to achieve manually.
How to Improve CAD/CAM Software Skills
Improving CAD/CAM software for a Mill Operator involves enhancing usability, precision, and integration capabilities. Here are concise ways to achieve this:
User Interface Improvement: Simplify the user interface to make it more intuitive for Mill Operators. Incorporating customizable toolbars and shortcut keys can significantly reduce design time and improve efficiency. Fusion 360 is an example of software with a user-friendly interface.
Enhanced Simulation Tools: Implement advanced simulation tools that can accurately predict tool paths, material removal rates, and potential collisions. This not only saves time but also reduces material waste. Mastercam's Simulation capabilities are a good reference.
Improved Integration with Hardware: Ensure seamless integration with a wide range of milling machines, including older models. This involves supporting various file formats and communication protocols. SolidCAM integrates well with numerous CNC machines.
Comprehensive Training Resources: Offer extensive and easily accessible training materials, including video tutorials, webinars, and interactive learning modules. This helps Mill Operators to quickly master the software. GibbsCAM provides varied learning resources.
Regular Updates and Feedback Loop: Regularly update the software to include new features, fix bugs, and improve performance. Establish a feedback loop with users to understand their needs and challenges. CAMWorks frequently updates its software based on user feedback.
By focusing on these areas, CAD/CAM software can be significantly improved to meet the specific needs of Mill Operators, enhancing their productivity and overall work quality.
How to Display CAD/CAM Software Skills on Your Resume
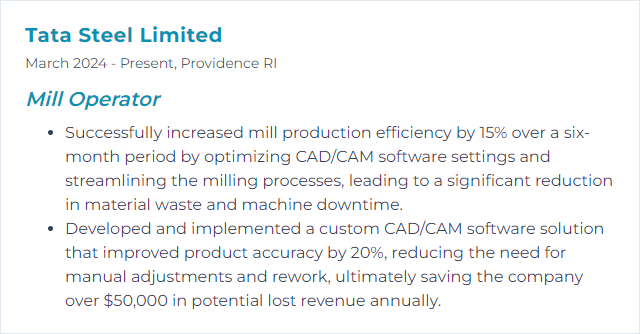
3. Precision Measurement
Precision measurement for a mill operator involves the use of highly accurate tools and techniques to ensure that the dimensions of milled materials meet strict specifications with minimal tolerance for error.
Why It's Important
Precision measurement is crucial for a Mill Operator because it ensures the accuracy and consistency of material dimensions, leading to high-quality products, reduced material waste, and increased efficiency in production processes.
How to Improve Precision Measurement Skills
To improve precision measurement as a Mill Operator, follow these concise steps:
Regular Calibration: Ensure all measuring instruments are regularly calibrated against standards. NIST offers guidelines on calibration frequencies and methodologies.
Use Appropriate Tools: Select the right tools for measurement. Digital calipers, micrometers, and dial indicators provide higher precision. Mitutoyo and Starrett are reputable manufacturers.
Environmental Control: Maintain a stable environment. Temperature, humidity, and vibration can affect measurements. Fluke provides tools for monitoring environmental conditions.
Operator Training: Ensure operators are well-trained in measurement techniques and tool handling. Precision Measuring and Gaging offers online courses tailored for mill operators.
Regular Maintenance: Keep the milling machine and tools in good condition. Proper maintenance reduces errors. The Machinery's Handbook provides comprehensive maintenance tips.
Data Analysis: Use statistical tools to analyze measurement data for consistency and accuracy improvement. Minitab offers statistical software for process improvement.
By implementing these practices, you will enhance the precision of measurements, ultimately improving the quality and consistency of your milling operations.
How to Display Precision Measurement Skills on Your Resume
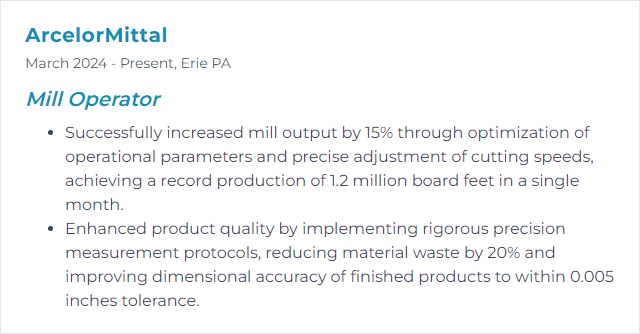
4. Quality Control
Quality control for a Mill Operator involves systematically monitoring and evaluating the production process to ensure that the output meets established standards of quality, consistency, and safety.
Why It's Important
Quality control is essential for a Mill Operator to ensure the production of consistent, high-quality products, minimize waste, reduce costs, and meet customer satisfaction and regulatory standards.
How to Improve Quality Control Skills
Improving quality control, especially for a Mill Operator, involves a focused approach on precision, process optimization, and continuous learning. Here are concise steps:
Standardize Processes: Develop and adhere to standard operating procedures (SOPs) for consistency. ISO standards can guide quality benchmarks.
Regular Maintenance: Ensure equipment is routinely checked and maintained to prevent faults that could compromise quality. Machinery Lubrication offers insights on equipment maintenance.
Quality Training: Invest in regular training for operators on quality control measures and updates in milling technology. Tooling U-SME provides industry-specific training courses.
Implement Inspection at Every Stage: From raw materials to finished products, perform quality checks at every stage. ASQ has resources on inspection strategies.
Use of Technology: Incorporate technology like automated inspection systems and software for real-time quality monitoring. LNS Research discusses technology in manufacturing.
Feedback Loop: Establish a system for collecting and analyzing feedback from both customers and the production floor to continually adjust and improve processes. Harvard Business Review provides insights on feedback systems.
Each of these steps, when implemented diligently, can significantly enhance the quality control measures in a mill operation, ensuring product consistency and customer satisfaction.
How to Display Quality Control Skills on Your Resume
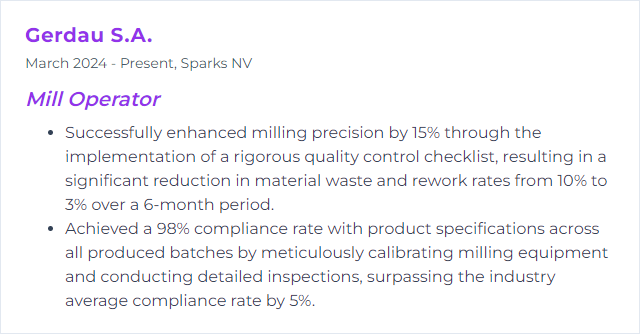
5. Machine Maintenance
Machine maintenance for a Mill Operator involves the regular inspection, cleaning, lubrication, and repair of milling equipment to ensure optimal operation, prevent breakdowns, and extend the machine's lifespan.
Why It's Important
Machine maintenance is crucial for a Mill Operator to ensure consistent operational efficiency, minimize downtime, and prolong the lifespan of the machinery, thereby safeguarding productivity and reducing costly repairs.
How to Improve Machine Maintenance Skills
To improve machine maintenance as a Mill Operator, focus on the following concise strategies:
Regular Inspections: Conduct routine inspections to identify wear and tear early. Machinery Lubrication offers insights on how to spot potential issues.
Preventive Maintenance: Implement a preventive maintenance schedule based on the manufacturer's recommendations. Reliable Plant provides strategies for creating effective maintenance plans.
Lubrication: Ensure machines are properly lubricated to reduce friction and wear. Lubes'n'Greases is a resource for selecting the right lubricants.
Operator Training: Train operators on correct machine usage and early problem detection. Tooling U-SME offers courses designed for manufacturing professionals.
Maintenance Records: Keep detailed records of all maintenance activities to track machine health over time. Plant Services discusses best practices in maintenance documentation.
By focusing on these areas, you can significantly improve the longevity and performance of milling machines.
How to Display Machine Maintenance Skills on Your Resume
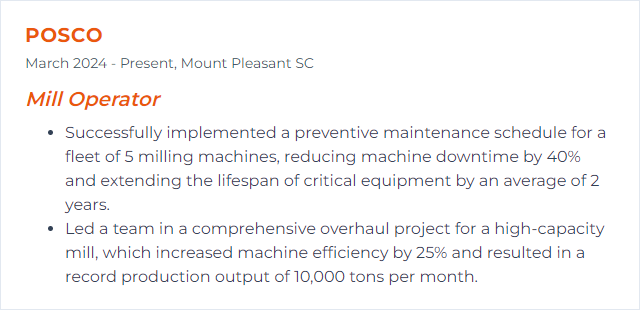
6. Safety Protocols
Safety protocols for a Mill Operator are guidelines and procedures designed to minimize risks and ensure the safe operation of milling equipment, including wearing appropriate personal protective equipment (PPE), following machinery operating instructions, conducting regular maintenance checks, and adhering to emergency response plans.
Why It's Important
Safety protocols are crucial for a mill operator to minimize the risk of accidents, ensure a safe working environment, protect equipment from damage, and comply with legal and regulatory standards.
How to Improve Safety Protocols Skills
Improving safety protocols for a Mill Operator involves several key steps aimed at minimizing risks and ensuring a safe working environment. Here’s a concise guide to enhancing safety measures:
Risk Assessment: Conduct regular risk assessments to identify potential hazards specific to mill operations.
Training and Education: Implement a comprehensive safety training program that includes handling equipment, emergency response, and hazard recognition.
Equipment Maintenance: Ensure regular maintenance and inspection of machinery to prevent malfunctions and accidents.
Safety Gear: Mandate the use of appropriate personal protective equipment (PPE) such as gloves, goggles, and hearing protection.
Emergency Preparedness: Develop and practice emergency response plans for incidents like fires, equipment failures, and chemical spills.
Communication: Foster open communication channels for employees to report hazards or suggest improvements without fear of reprisal.
Continuous Improvement: Regularly review and update safety protocols based on new safety information, incidents, and employee feedback.
By implementing these steps, you can create a safer work environment for mill operators and reduce the likelihood of accidents and injuries.
How to Display Safety Protocols Skills on Your Resume
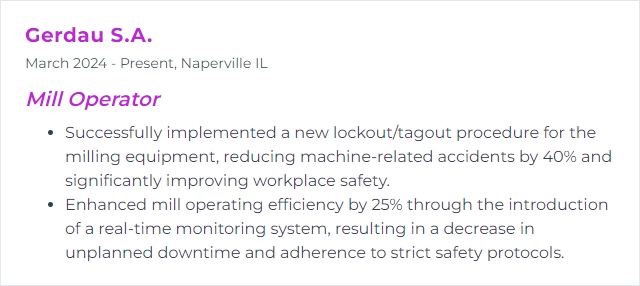
7. Lean Manufacturing
Lean Manufacturing is a systematic approach aimed at minimizing waste within manufacturing systems while maximizing productivity. For a Mill Operator, it means focusing on streamlining operations, reducing unnecessary steps, and improving efficiency in the milling process to produce more with less waste and lower costs.
Why It's Important
Lean Manufacturing is important for a Mill Operator because it streamlines production processes, reduces waste, increases efficiency, and improves product quality. This leads to higher productivity, lower costs, and better customer satisfaction.
How to Improve Lean Manufacturing Skills
To improve Lean Manufacturing for a Mill Operator, focus on these concise strategies:
- Continuous Improvement: Regularly analyze and improve processes using tools like Kaizen to reduce waste and increase efficiency.
- 5S Methodology: Implement 5S (Sort, Set in order, Shine, Standardize, Sustain) to organize the workplace, ensuring safety and efficiency.
- Value Stream Mapping: Identify and eliminate waste in the production process through Value Stream Mapping, optimizing the flow from raw material to finished product.
- Preventive Maintenance: Adopt a Preventive Maintenance schedule to reduce machine downtime and maintain consistent quality and productivity.
- Cross-training: Enhance flexibility and responsiveness by cross-training employees, enabling them to perform multiple tasks and operate different machines as needed.
Implementing these strategies can significantly enhance the efficiency and productivity of mill operations within the framework of Lean Manufacturing.
How to Display Lean Manufacturing Skills on Your Resume
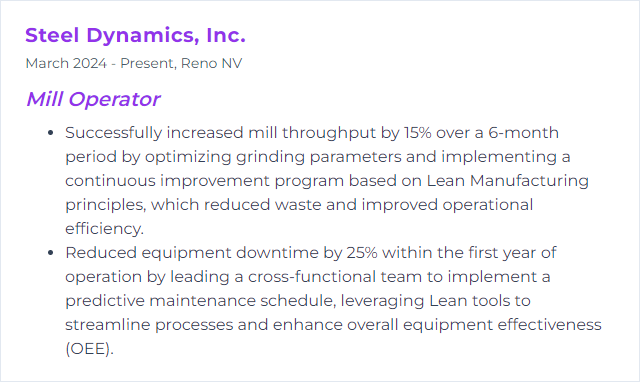
8. Troubleshooting
Troubleshooting, in regards to a Mill Operator, involves systematically diagnosing and resolving problems or malfunctions within the milling equipment and processes to ensure optimal operation and productivity.
Why It's Important
Troubleshooting is crucial for a Mill Operator as it enables the quick identification and resolution of issues, ensuring the mill operates efficiently, minimizes downtime, and maintains product quality.
How to Improve Troubleshooting Skills
Improving troubleshooting skills, especially for a Mill Operator, involves a focused approach to identifying, analyzing, and solving problems in the milling process. Here’s a concise guide:
Understand the Process: Gain a thorough understanding of the milling process, equipment, and systems. Familiarity with operation manuals can be invaluable. The Society for Mining, Metallurgy & Exploration offers resources and literature.
Systematic Approach: Adopt a systematic approach to troubleshooting such as the Six-Step Troubleshooting Method which emphasizes understanding the problem, planning the approach, and testing solutions.
Critical Thinking: Enhance critical thinking skills. Critical Thinking Web offers free online courses and exercises.
Hands-On Experience: Gain as much hands-on experience as possible. Real-world problem-solving sharpens your skills. Participate in forums like Eng-Tips to share experiences and solutions with other professionals.
Stay Updated: Stay updated with the latest technologies and practices in milling operations. International Milling Directory provides a wealth of resources and updates in the milling industry.
Training and Education: Continuously seek out training opportunities. Online platforms like Coursera and edX offer courses related to manufacturing, engineering, and problem-solving techniques.
Improving troubleshooting skills is a continuous process that involves learning, practice, and application of various strategies and methods tailored to the complexities of milling operations.
How to Display Troubleshooting Skills on Your Resume
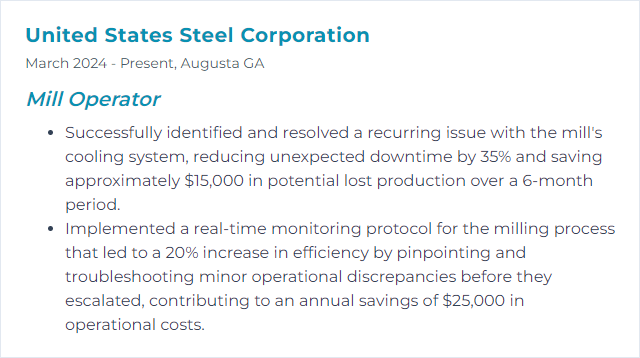
9. Process Optimization
Process optimization for a Mill Operator involves systematically improving milling operations to increase efficiency, reduce waste, and enhance product quality, aiming for cost-effective and optimal production outcomes.
Why It's Important
Process optimization is crucial for a Mill Operator as it enhances efficiency, reduces costs, and improves product quality, enabling a more competitive and profitable operation.
How to Improve Process Optimization Skills
Improving process optimization for a Mill Operator involves enhancing efficiency, reducing waste, and increasing productivity through strategic adjustments and technology integration. Here's a concise guide:
Data Analysis: Utilize real-time data analytics to monitor performance and identify inefficiencies. Tools like PI System can track and visualize operational data.
Automation: Implement automation for repetitive tasks to improve precision and reduce human error. Explore solutions like Rockwell Automation for industry-specific automation technologies.
Lean Manufacturing: Adopt lean manufacturing principles to eliminate waste and streamline operations. The Lean Enterprise Institute offers resources and workshops on applying lean thinking.
Predictive Maintenance: Use predictive maintenance tools to preemptively address equipment issues, minimizing downtime. IBM’s Predictive Maintenance solutions offer insights into equipment health.
Training and Development: Continuously train staff on best practices and new technologies. Platforms like Coursera and edX offer courses relevant to manufacturing and process optimization.
Energy Efficiency: Optimize energy use to reduce costs and environmental impact. The U.S. Department of Energy provides guidance on energy efficiency in manufacturing.
Quality Control: Implement advanced quality control measures to ensure product consistency and reduce waste. ASQ Quality Resources is a good starting point for quality improvement tools and techniques.
By focusing on these areas, a Mill Operator can significantly enhance process optimization, leading to a more efficient, productive, and cost-effective operation.
How to Display Process Optimization Skills on Your Resume
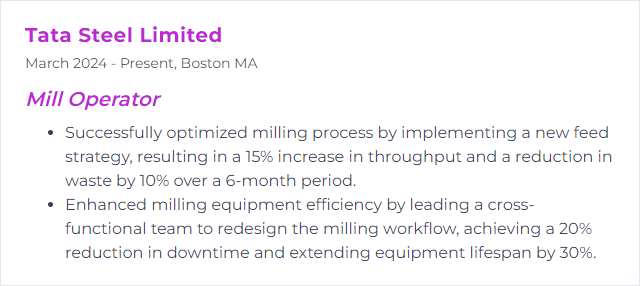
10. Material Handling
Material handling in the context of a Mill Operator refers to the process of moving, controlling, protecting, and storing materials (such as raw materials, work-in-progress, and finished goods) within the mill environment. This includes tasks such as loading raw materials into machines, transferring intermediate products between processes, and preparing finished products for storage or shipment, often utilizing equipment like conveyors, hoists, and forklifts.
Why It's Important
Material handling is important for a Mill Operator because it ensures efficient, safe, and timely movement of materials, which directly impacts productivity, reduces operational costs, and minimizes the risk of workplace injuries.
How to Improve Material Handling Skills
To improve material handling for a Mill Operator, focus on these key strategies:
Automate Processes: Integrate automation tools and equipment (e.g., conveyors, robotic arms) to reduce manual handling and increase efficiency. Automation in Material Handling
Implement Lean Practices: Adopt lean manufacturing principles to minimize waste and optimize workflow. This includes organizing tools and materials for easy access and minimal movement. Lean Manufacturing Principles
Regular Training: Ensure operators are regularly trained on the latest material handling techniques and safety protocols. Material Handling Training
Use of Ergonomic Tools: Invest in ergonomic tools and equipment to reduce physical strain and improve handling efficiency. Ergonomics in the Workplace
Maintenance and Upgrades: Regularly maintain and upgrade machinery and equipment to ensure optimal performance and reduce downtime. Maintenance Best Practices
By focusing on these areas, a Mill Operator can significantly improve material handling in their operations.
How to Display Material Handling Skills on Your Resume
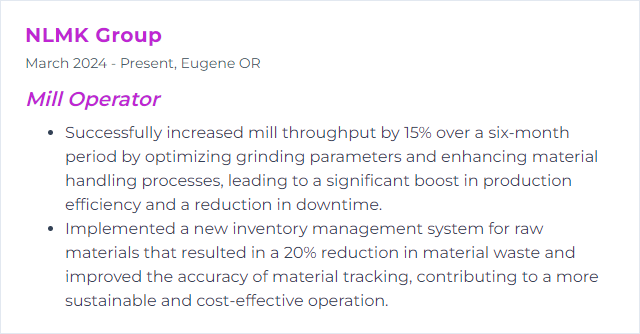
11. ISO Standards
ISO standards are internationally agreed-upon norms and specifications that ensure quality, safety, and efficiency across various industries, including milling. They help a mill operator by providing consistent guidelines for processes, materials, and products, thereby improving operational efficiency, product quality, and safety.
Why It's Important
ISO Standards ensure consistent quality, safety, and efficiency in operations, helping Mill Operators to meet international expectations, reduce errors, and enhance customer satisfaction.
How to Improve ISO Standards Skills
Improving adherence to ISO standards for a Mill Operator involves a focused approach on enhancing quality, safety, and efficiency within the operational processes. Here's a concise guide:
Understand and Implement ISO Requirements: Begin by thoroughly understanding the specific ISO standards applicable to your milling operations (such as ISO 9001 for quality management systems). Ensure all processes align with these standards. ISO 9001 Overview
Continuous Training: Regularly train and retrain employees on ISO standards, emphasizing the importance of quality and safety in their daily tasks. ISO Training Resources
Process Optimization: Continually assess and optimize milling operations to enhance efficiency, quality, and compliance with ISO standards. Incorporate lean manufacturing principles if applicable. Lean Manufacturing Guide
Quality Control and Assurance: Implement stringent quality control (QC) and quality assurance (QA) measures, conducting regular audits and inspections to ensure standards are met or exceeded. Quality Management Principles
Engage with ISO Bodies and Communities: Stay updated on changes and improvements to ISO standards by engaging with ISO bodies and communities relevant to the milling industry. Participate in forums and workshops to share knowledge and experiences. ISO Community Engagement
Customer Feedback and Continuous Improvement: Use customer feedback to identify areas for improvement in meeting ISO standards. Implement a continuous improvement approach (e.g., PDCA - Plan, Do, Check, Act) to address these areas effectively. PDCA Cycle
Document Management: Ensure all processes, changes, and compliance efforts are well-documented according to ISO requirements. This facilitates audits and helps in maintaining a clear roadmap of compliance and improvement efforts. ISO Document Management
By focusing on these key areas, a Mill Operator can significantly improve their adherence to ISO standards, leading to enhanced operational efficiency, safety, and product quality.
How to Display ISO Standards Skills on Your Resume
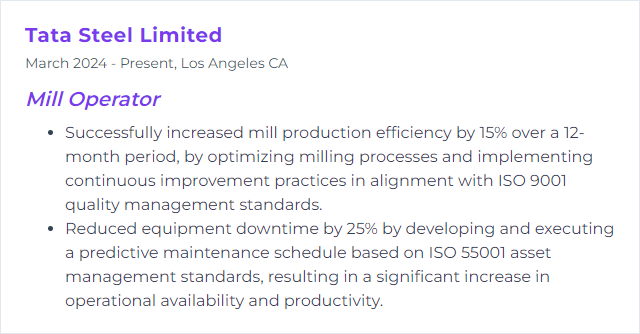
12. Inventory Management
Inventory management, for a mill operator, involves tracking and controlling the raw materials, finished products, and supplies needed for production, ensuring optimal stock levels to meet demand without overstocking.
Why It's Important
Inventory management is crucial for a Mill Operator as it ensures the optimal supply of materials for production, minimizes storage costs, prevents stockouts or excess inventory, and ultimately supports continuous, efficient operations and customer satisfaction.
How to Improve Inventory Management Skills
Improving inventory management, especially for a Mill Operator, involves optimizing the balance between supply and demand to ensure operational efficiency. Here are concise steps:
Automate Inventory Tracking: Implement an Inventory Management System that automatically updates stock levels in real-time, reducing manual errors.
Demand Forecasting: Use historical sales data to predict future demand accurately, allowing for better planning and stock optimization.
Regular Audits: Conduct regular inventory audits to reconcile physical stock with recorded inventory, identifying discrepancies early.
Supplier Management: Develop strong relationships with suppliers for reliable delivery schedules, which helps in avoiding stockouts or overstock situations.
Lean Inventory: Implement a lean inventory strategy, keeping stock levels minimal but sufficient to meet demand, reducing holding costs.
Continuous Improvement: Adopt a culture of continuous improvement (Kaizen), regularly reviewing and optimizing inventory management practices.
By applying these strategies, a Mill Operator can significantly improve inventory management, ensuring that the right amount of materials is available when needed, while also minimizing costs and enhancing productivity.
How to Display Inventory Management Skills on Your Resume
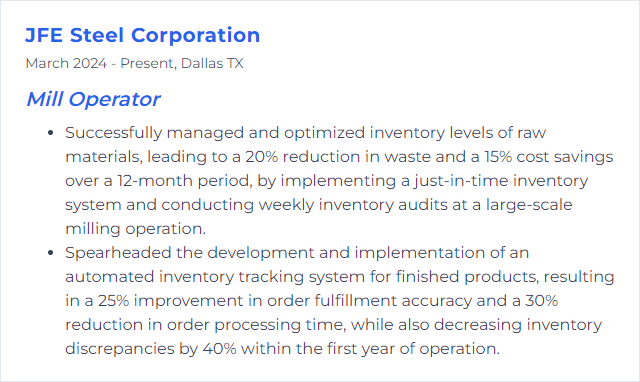