Top 12 Lean Consultant Skills to Put on Your Resume
In today's competitive job market, standing out as a lean consultant requires a unique set of skills that demonstrate your ability to optimize processes, reduce waste, and deliver value. Crafting your resume with these top lean consultant skills will not only showcase your expertise but also position you as a prime candidate for prospective employers.
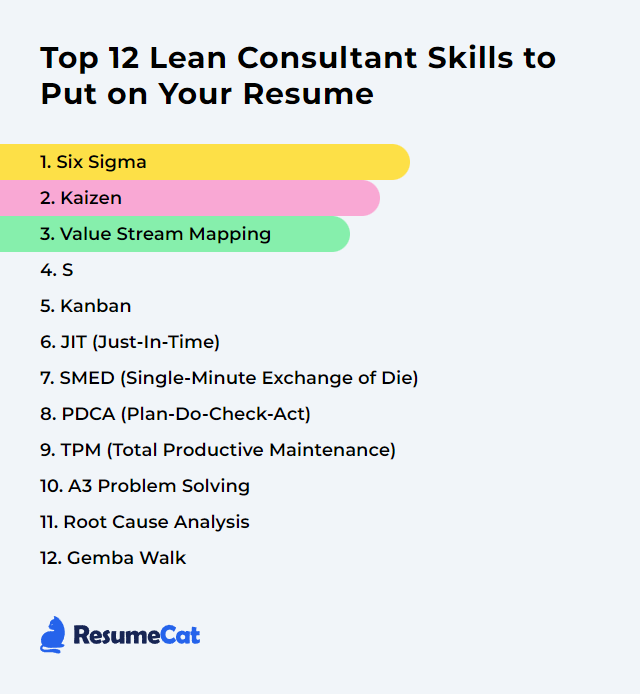
Lean Consultant Skills
- Six Sigma
- Kaizen
- Value Stream Mapping
- S
- Kanban
- JIT (Just-In-Time)
- SMED (Single-Minute Exchange of Die)
- PDCA (Plan-Do-Check-Act)
- TPM (Total Productive Maintenance)
- A3 Problem Solving
- Root Cause Analysis
- Gemba Walk
1. Six Sigma
Six Sigma is a data-driven methodology aiming at process improvement by eliminating defects and reducing variation, to enhance quality, efficiency, and customer satisfaction, crucial for Lean Consultants in streamlining operations and maximizing value.
Why It's Important
Six Sigma is important as it provides a systematic approach to reducing waste and variability in processes, leading to improved efficiency, quality, and customer satisfaction, which are critical objectives for a Lean Consultant.
How to Improve Six Sigma Skills
Improving Six Sigma involves enhancing its methodologies and tools to boost efficiency, reduce errors, and foster continuous improvement within organizations. As a Lean Consultant, consider focusing on the following key strategies:
Integrate Lean and Six Sigma: Combine Lean methodologies with Six Sigma to streamline processes, eliminate waste, and reduce variation. Lean Six Sigma provides a comprehensive approach for operational excellence.
Focus on Change Management: Implement effective change management strategies to ensure organizational buy-in and sustain improvements. Prosci’s ADKAR Model offers a framework for managing change.
Enhance Data Analysis Capabilities: Utilize advanced statistical tools and software for more accurate data analysis, driving better decision-making. Minitab is a popular choice for Six Sigma practitioners.
Develop Soft Skills: Beyond technical expertise, focus on developing soft skills like leadership, communication, and problem-solving among Six Sigma teams. ASQ Soft Skills provides resources for skill development.
Continuous Learning and Certification: Encourage continuous education and certification among team members to stay updated with the latest Six Sigma methodologies. IASSC Certification is globally recognized.
Customize Six Sigma Tools: Adapt and customize Six Sigma tools to fit the specific needs of your organization or industry for more effective implementation. iSixSigma offers resources and case studies.
Leverage Technology: Use technology to automate processes and collect real-time data for quicker and more accurate analysis. Smartsheet is an example of a project management tool that can support Six Sigma projects.
By focusing on these strategies, a Lean Consultant can significantly improve the implementation and effectiveness of Six Sigma within organizations, leading to better quality, efficiency, and customer satisfaction.
How to Display Six Sigma Skills on Your Resume
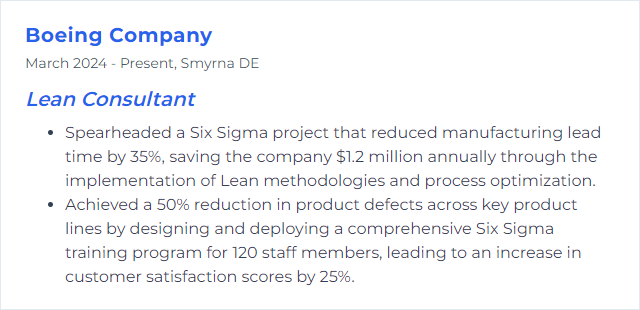
2. Kaizen
Kaizen is a Japanese philosophy that focuses on continuous, incremental improvement in processes, aiming to enhance efficiency and reduce waste, essential in Lean management practices.
Why It's Important
Kaizen is crucial for Lean Consultants as it fosters continuous improvement, enhances efficiency, reduces waste, and boosts productivity, directly contributing to the overall organizational success.
How to Improve Kaizen Skills
Improving Kaizen, a core Lean methodology focusing on continuous, incremental improvement, involves strategic, practical steps. As a Lean Consultant, focus on:
Leadership Engagement: Secure commitment from all levels of leadership to model and support Kaizen principles. Leadership's Role in Kaizen
Employee Empowerment: Empower employees by providing training, resources, and authority to identify and implement improvements. Empowering Employees
Structured Process: Implement a structured yet flexible Kaizen process that includes clear goals, roles, and metrics. Kaizen Implementation Guide
Continuous Learning: Foster a culture of continuous learning through regular training, knowledge sharing, and reflection sessions. Creating a Culture of Continuous Improvement
Feedback and Iteration: Encourage and act on feedback from all stakeholders, using it to iterate and refine processes continuously. Feedback for Continuous Improvement
Visual Management: Utilize visual management tools to track progress, identify issues quickly, and share successes. Visual Management Tools
Standardization and Documentation: Standardize successful improvements and document processes to ensure consistency and facilitate training. The Importance of Standard Work in Kaizen
Integration into Culture: Integrate Kaizen deeply into the organization's culture, making continuous improvement an everyday norm. Integrating Kaizen into the Corporate Culture
By focusing on these areas, a Lean Consultant can significantly enhance the effectiveness of Kaizen initiatives within an organization.
How to Display Kaizen Skills on Your Resume
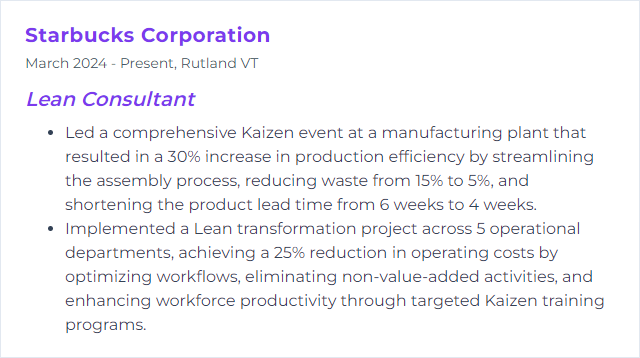
3. Value Stream Mapping
Value Stream Mapping (VSM) is a lean management tool used to visualize and analyze the steps involved in taking a product or service from its inception to the customer, with the goal of identifying and eliminating waste to optimize the overall process flow.
Why It's Important
Value Stream Mapping is important because it visually identifies all the steps in a process, pinpointing waste and inefficiencies, enabling targeted improvements towards leaner operations and value enhancement.
How to Improve Value Stream Mapping Skills
To improve Value Stream Mapping (VSM), follow these concise steps, tailored for a Lean Consultant:
Educate and Engage: Ensure all team members are trained on VSM principles. Use resources like the Lean Enterprise Institute (Lean Enterprise Institute) to provide foundational knowledge.
Select the Right Scope: Focus on a specific product family or service line to keep the mapping manageable and relevant.
Gather Accurate Data: Collect data on process times, wait times, and flow distances. Tools like time studies and process observations are crucial.
Utilize Software Tools: Leverage VSM software for efficiency and clarity. Lucidchart (Lucidchart) offers specialized features for VSM.
Involve Cross-Functional Teams: Include diverse perspectives from different departments to ensure a comprehensive view of the value stream.
Identify Waste: Use the mapping process to pinpoint areas of waste in terms of Lean's eight wastes. This identification is pivotal for improvement.
Develop a Future State Map: Design a future state map that addresses the identified waste and outlines a plan for a leaner process.
Create an Implementation Plan: Develop a clear, actionable plan with specific steps, responsibilities, and timelines to achieve the future state.
Monitor and Adjust: Use KPIs to track progress towards the future state. Be prepared to adapt the plan based on feedback and new insights.
Continuous Improvement: Treat VSM as an ongoing process, regularly updating maps and plans to reflect changes and improvements in the process.
For further learning and examples, consider visiting the American Society for Quality (ASQ) for detailed guides and case studies on VSM.
How to Display Value Stream Mapping Skills on Your Resume
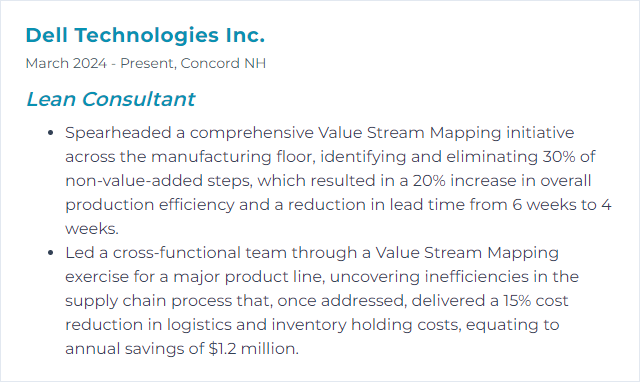
4. S
In the context of a Lean Consultant, "S" typically refers to the first step in the 5S methodology: Sort (Seiri). This involves organizing the workplace by removing unnecessary items and clutter to enhance efficiency and safety.
Why It's Important
S is crucial for a Lean Consultant as it stands for "Sort," the first step in the 5S methodology, which aims to eliminate unnecessary items from the workspace, thus enhancing efficiency and focus by organizing the environment.
How to Improve S Skills
Improving "S" (Sustain) in the context of a Lean Consultant involves ensuring the continuous application and commitment to Lean methodologies within an organization. Here is a very short and concise strategy:
Educate Continuously: Provide ongoing training and resources to keep everyone updated on Lean practices. Lean Enterprise Institute offers extensive resources.
Standardize Processes: Establish clear, documented standards for tasks and processes. Guidelines from ASQ can be helpful.
Implement Visual Controls: Use tools like 5S or Kanban to make deviations from the standard immediately visible. Kanbanize explains the application of Kanban in Lean management.
Regular Audits and Reviews: Schedule frequent audits to ensure adherence to Lean principles. The Kaizen Institute provides insights on continuous improvement audits.
Promote a Culture of Accountability: Encourage teams to take responsibility for sustaining Lean practices. Harvard Business Review offers articles discussing leadership and accountability.
Leverage Technology: Utilize Lean management software for tracking progress and identifying areas for improvement. iAuditor by SafetyCulture is an example of an auditing app.
Celebrate Successes: Recognize and reward teams and individuals for successfully sustaining Lean improvements.
By focusing on education, standardization, visual controls, regular audits, accountability, technology, and recognition, a Lean Consultant can effectively sustain Lean methodologies within an organization.
How to Display S Skills on Your Resume
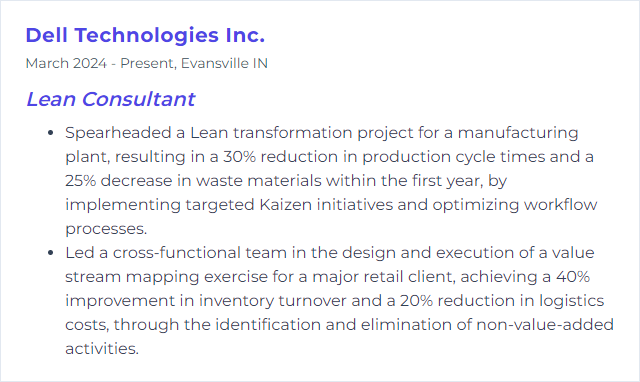
5. Kanban
Kanban is a visual workflow management method for defining, managing, and improving services that deliver knowledge work, aiming to help you visualize your work, maximize efficiency, and improve continuously. It originates from lean manufacturing principles and is used to balance demands with available capacity and improve the flow of work.
Why It's Important
Kanban is important because it enables continuous, visual workflow management and optimization, reduces waste, and enhances efficiency, aligning with Lean principles for maximizing value and minimizing inefficiencies.
How to Improve Kanban Skills
To improve Kanban, focus on the following strategies:
Visualize Workflow: Use a Kanban board with clear columns for each stage of the workflow. This helps in identifying bottlenecks and inefficiencies. Trello and Jira are popular tools for creating digital Kanban boards.
Limit Work in Progress (WIP): Set limits on the number of tasks in each stage to prevent overloading team members and to ensure smooth flow of work. This encourages task completion and reduces cycle time.
Manage Flow: Regularly monitor the flow of work through the Kanban board to identify areas of delay. Adjust WIP limits and redistribute resources as necessary to optimize flow.
Make Policies Explicit: Clearly define the criteria for moving tasks between stages on the Kanban board. This ensures consistency and helps in identifying areas for improvement.
Implement Feedback Loops: Regular retrospectives can help in identifying improvements. Use the feedback to refine processes, WIP limits, and the overall workflow.
Improve Collaboratively: Engage the whole team in the process of continuous improvement. Encourage suggestions and experiments to find better workflows and solutions.
For a comprehensive guide on implementing and improving Kanban, refer to Kanban University's resources and LeanKit for practical insights on Kanban in action.
How to Display Kanban Skills on Your Resume

6. JIT (Just-In-Time)
JIT (Just-In-Time) is a lean manufacturing strategy aimed at reducing waste and improving efficiency by producing goods only as they are needed, minimizing inventory levels and streamlining production processes.
Why It's Important
JIT minimizes waste and reduces costs by producing only what is needed, when it's needed, enhancing efficiency and value in Lean processes.
How to Improve JIT (Just-In-Time) Skills
Improving JIT (Just-In-Time) involves enhancing the efficiency and responsiveness of the production process to minimize waste and align production with customer demand. Here are concise strategies for a Lean Consultant:
Streamline Supply Chain: Collaborate closely with suppliers to ensure timely and flexible material delivery. Implement Supplier Kanban systems for smoother flow.
Implement Pull Systems: Transition from push (based on forecasts) to pull systems (based on actual demand) to reduce overproduction and inventory levels.
Optimize Inventory Management: Use techniques like ABC analysis to prioritize items and reduce excess inventory, aligning production closer to demand.
Enhance Quality Control: Adopt Total Quality Management (TQM) to reduce defects and rework, ensuring the right quality is achieved the first time.
Continuous Improvement (Kaizen): Foster a culture of continuous improvement by encouraging employee feedback and Kaizen initiatives to identify and eliminate waste in the production process.
Flexible Workforce: Train employees in multiple skills to ensure they can rotate across different tasks, enhancing adaptability and reducing bottlenecks.
Leverage Technology: Implement Advanced Planning and Scheduling (APS) systems for real-time visibility and better decision-making.
By focusing on these areas, a Lean Consultant can significantly enhance JIT effectiveness, leading to reduced costs, improved quality, and greater customer satisfaction.
How to Display JIT (Just-In-Time) Skills on Your Resume
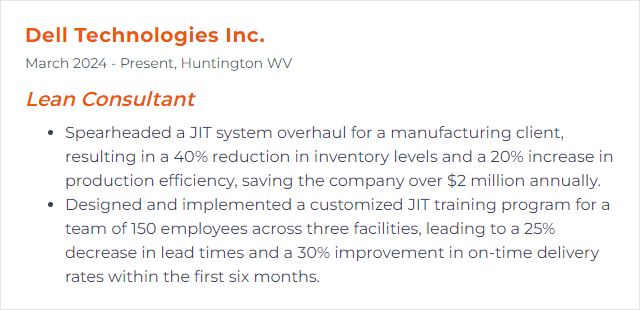
7. SMED (Single-Minute Exchange of Die)
SMED, or Single-Minute Exchange of Die, is a lean manufacturing process aimed at reducing equipment setup times to under 10 minutes, thereby minimizing production downtime and increasing efficiency.
Why It's Important
SMED (Single-Minute Exchange of Die) significantly reduces equipment setup times, enabling more flexible and efficient production processes. This lean tool minimizes downtime, increases machine utilization, and supports just-in-time production, ultimately reducing costs and improving delivery performance.
How to Improve SMED (Single-Minute Exchange of Die) Skills
Improving SMED (Single-Minute Exchange of Die) involves streamlining the process of changing over from one production setup to another. Here's a concise guide for a Lean Consultant:
Observe and Document: Record the current changeover process in detail, capturing every step to identify wasteful activities. SMED Guide
Separate Internal from External Activities: Distinguish between activities that can be done while the machine is running (external) and those that can only be performed when it's stopped (internal). Aim to increase the former. SMED Overview
Convert Internal to External: Redesign procedures so that more preparation can occur without stopping the machine. This might involve using quick clamps or pre-setting tools. SMED Conversion Tips
Standardize Functions and Use of Tools: Ensure tools are readily available, and standardize their use. This reduces time looking for or adjusting tools during a changeover. Lean Manufacturing Tools
Implement Parallel Processing: Where possible, have multiple tasks completed simultaneously, rather than sequentially, to reduce total setup time. Lean Production Techniques
Streamline Remaining Steps: Continuously look for ways to simplify and speed up the remaining internal activities, such as optimizing movements or using more efficient tools. Continuous Improvement
Train and Empower Employees: Ensure all team members are trained in SMED techniques and empowered to suggest improvements. This creates a culture of continuous improvement. Employee Empowerment
Regularly Review and Optimize: Continuously monitor the changeover process, seeking feedback from operators and implementing incremental improvements. Kaizen
Incorporating these strategies can significantly reduce changeover times, enhancing flexibility and efficiency in production processes.
How to Display SMED (Single-Minute Exchange of Die) Skills on Your Resume
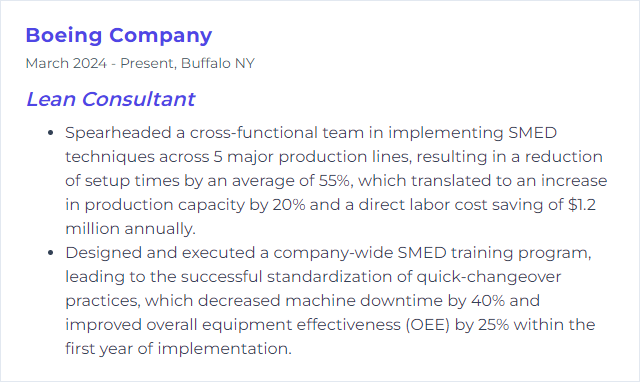
8. PDCA (Plan-Do-Check-Act)
PDCA (Plan-Do-Check-Act) is a four-step management method used for continuous improvement of processes and products, involving planning an action, implementing the action, checking the outcomes against expected results, and taking corrective actions as necessary before planning the next cycle of improvement.
Why It's Important
The PDCA cycle is important for Lean Consultants because it provides a systematic, iterative framework for continuous improvement and problem-solving. It ensures efficient process optimization, reduces waste, and enhances value delivery to customers.
How to Improve PDCA (Plan-Do-Check-Act) Skills
Improving the PDCA (Plan-Do-Check-Act) cycle involves enhancing each of its four phases to be more efficient, effective, and adaptable. For a Lean Consultant, focusing on integrating Lean principles at each stage can significantly optimize the process. Here's a concise guide:
Plan: Clearly define objectives, establish metrics, and develop a detailed plan that incorporates Lean tools like value stream mapping. Incorporate thorough root cause analysis techniques such as 5 Whys to ensure the plan addresses the core issues.
Do: Implement the plan on a small scale first to minimize risk. Utilize Kaizen for continuous, incremental improvements, ensuring team engagement and applying Lean principles to streamline processes.
Check: Use real-time data and KPIs to monitor progress. Adopt visual management tools for easy tracking and engage teams in reviewing outcomes against expected results to foster a culture of transparency and accountability.
Act: Based on the review, take corrective actions. Standardize successful practices and document lessons learned. Leverage A3 Problem Solving to facilitate effective decision-making and ensure continuous improvement.
For a Lean Consultant, the key to enhancing PDCA is to deeply integrate Lean thinking and tools at each stage, promote a culture of continuous improvement, and ensure active participation from all team members. Engaging in regular training and staying updated with Lean methodologies through resources like the Lean Enterprise Institute can also provide fresh insights and strategies for PDCA optimization.
How to Display PDCA (Plan-Do-Check-Act) Skills on Your Resume
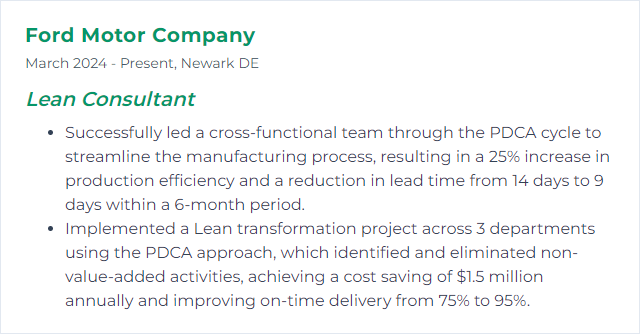
9. TPM (Total Productive Maintenance)
TPM (Total Productive Maintenance) is a Lean manufacturing approach aimed at maximizing equipment effectiveness and minimizing downtime through systematic maintenance, involving all employees from operators to top management. It focuses on proactive and preventive maintenance to improve productivity and quality.
Why It's Important
TPM is important because it enhances equipment reliability and efficiency, reduces downtime and defects, and supports continuous improvement, aligning with Lean principles to maximize value and minimize waste.
How to Improve TPM (Total Productive Maintenance) Skills
Improving Total Productive Maintenance (TPM) as a Lean Consultant involves several key steps focused on optimizing equipment efficiency and minimizing downtime in manufacturing processes. Here's a concise guide:
Education and Training: Implement comprehensive training programs for all employees to ensure they understand TPM principles and techniques. Focus on fostering a proactive maintenance culture. TPM Training Guide
Small Group Activities: Encourage the formation of cross-functional teams to identify areas for improvement and develop solutions collaboratively. This enhances ownership and participation. Cross-Functional Team Guide
Focused Improvement (Kaizen): Use Kaizen to systematically eliminate waste and inefficiencies in maintenance activities, aiming for continuous improvement. Kaizen Guide
Autonomous Maintenance: Train operators to perform basic maintenance, enabling them to identify and address issues promptly. This reduces downtime and improves machine performance. Autonomous Maintenance Steps
Planned Maintenance: Develop a data-driven planned maintenance schedule based on historical performance and predictive analysis to prevent unexpected equipment failures. Planned Maintenance Overview
Quality Maintenance: Implement measures to ensure that machines are always capable of producing products to specification, reducing the rate of defects. Quality Maintenance Principles
TPM in Administrative and Support Areas: Extend TPM principles to administrative and support functions to improve the overall efficiency of the organization. TPM Beyond Manufacturing
Safety, Health, and Environment: Integrate safety and environmental considerations into all aspects of TPM to ensure a safe and sustainable workplace. Safety and Health in TPM
Use of Technology and Data Analytics: Leverage the latest technology such as IoT (Internet of Things) and data analytics for real-time monitoring and predictive maintenance. IoT in Maintenance
Regular Review and Adjustment: Continuously review the effectiveness of TPM activities and adjust strategies based on performance data and changing business needs. TPM Review Process
Focusing on these areas will help enhance the effectiveness of TPM initiatives, leading to improved machine reliability, reduced waste, and better overall productivity.
How to Display TPM (Total Productive Maintenance) Skills on Your Resume
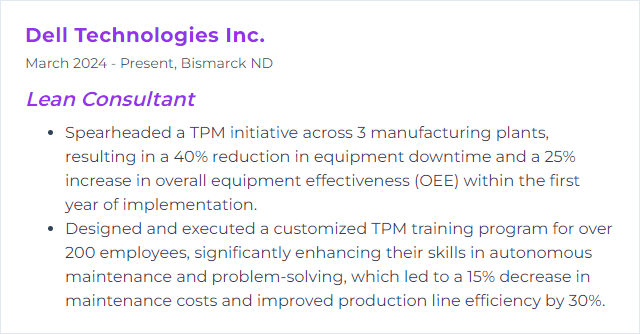
10. A3 Problem Solving
A3 Problem Solving is a structured, Lean methodology used by consultants to systematically address complex problems, improve processes, and implement solutions. It involves documenting the problem-solving process on a single A3-size paper (11x17 inches), facilitating clarity, focus, and collaboration. The approach typically follows steps such as background, current condition, root cause analysis, goal setting, action plan development, implementation, and follow-up, aligning with Lean principles to eliminate waste and optimize efficiency.
Why It's Important
A3 Problem Solving is crucial for a Lean Consultant because it provides a structured and efficient framework for identifying, analyzing, and resolving issues, thereby streamlining processes, reducing waste, and enhancing overall organizational performance in alignment with Lean principles.
How to Improve A3 Problem Solving Skills
To improve A3 Problem Solving as a Lean Consultant, follow these concise steps:
Define the Problem Clearly: Start with a clear, concise statement of the actual problem, focusing on specifics rather than assumptions. Problem Statement Guide.
Gather Data Rigorously: Collect data related to the problem to understand its magnitude and implications. Use tools like the 5 Whys or Fishbone Diagram for root cause analysis. Data Collection Techniques.
Set a Goal: Define a measurable goal that addresses the problem identified. This sets a clear target for the problem-solving effort. SMART Goals.
Analyze the Problem: Dive deep into the root causes of the problem using the data collected. Employ tools such as Pareto Charts or Cause and Effect diagrams. Root Cause Analysis Tools.
Develop Countermeasures: Brainstorm and select solutions that directly address the root causes. Prioritize actions based on impact and feasibility. Countermeasures Selection.
Implement Solutions: Develop an implementation plan with clear responsibilities and timelines. Ensure all stakeholders are on board. Implementation Planning Guide.
Monitor Results and Process: Track the impact of the solutions against the goal set. Use visual management tools for ongoing monitoring. Visual Management Tools.
Standardize Successful Practices: Once a solution proves successful, standardize the process to prevent recurrence of the problem. Standardization Techniques.
Reflect and Learn: Finally, reflect on the problem-solving process to glean lessons learned and apply them to future problems. Reflection Techniques.
By following these steps systematically, a Lean Consultant can enhance their A3 Problem Solving process, leading to more efficient and effective resolutions.
How to Display A3 Problem Solving Skills on Your Resume
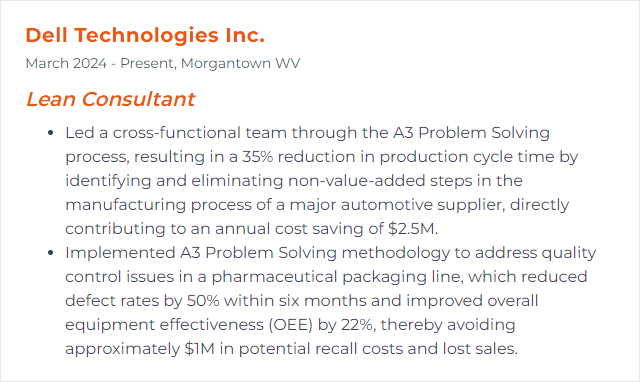
11. Root Cause Analysis
Root Cause Analysis (RCA) is a systematic process used by Lean Consultants to identify the underlying reasons for a problem or inefficiency within an organization, aiming to implement long-term solutions that eliminate these core issues and promote continuous improvement.
Why It's Important
Root Cause Analysis (RCA) is crucial for a Lean Consultant as it identifies the underlying reasons for problems or inefficiencies, allowing for the development of effective, long-term solutions that enhance process efficiency and reduce waste, aligning with Lean principles.
How to Improve Root Cause Analysis Skills
Improving Root Cause Analysis (RCA) involves enhancing the process of identifying the fundamental reasons for issues or faults. For a Lean Consultant, focusing on these strategies can lead to more effective problem-solving:
Define the Problem Clearly: Start with a clear, concise problem statement that describes the issue in detail. This helps in focusing the RCA process.
Use the Right Tools: Employ various RCA tools like the 5 Whys, Fishbone Diagram, and Pareto Analysis to explore all possible root causes.
Gather and Analyze Data: Collect data related to the problem to identify patterns or anomalies. Data analysis tools can offer insights into the root causes.
Engage the Team: Involve team members from different functions who are close to the problem. Their insights can provide valuable perspectives.
Focus on Process Improvements: Aim for solutions that enhance processes, eliminating the root cause and preventing recurrence.
Implement and Monitor Solutions: After identifying root causes, implement solutions and monitor their effectiveness over time to ensure the problem is resolved.
Continuously Improve: RCA is not a one-time activity. Continuously look for ways to improve the process and prevent future issues.
For more practical insights and methodologies, explore resources from Lean Enterprise Institute and American Society for Quality (ASQ). These platforms offer extensive guidance, tools, and examples for conducting effective RCA in a Lean context.
How to Display Root Cause Analysis Skills on Your Resume
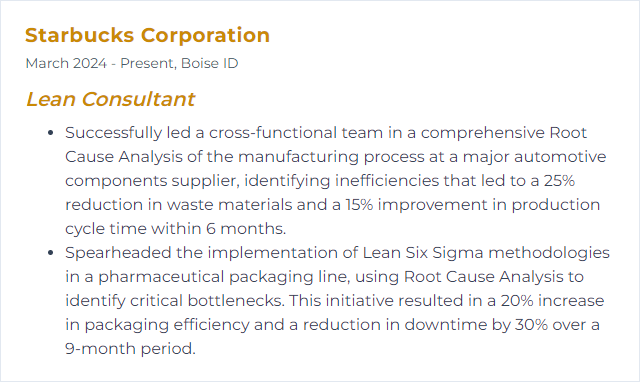
12. Gemba Walk
A Gemba Walk is a practice where Lean Consultants go directly to the shop floor or place of work (the "gemba" in Japanese, meaning "the real place") to observe processes, engage with employees, and identify opportunities for continuous improvement in efficiency, quality, and waste reduction.
Why It's Important
A Gemba Walk is crucial for a Lean Consultant because it provides direct observation of processes and work activities, enabling real-time insights and identification of waste, inefficiencies, and opportunities for continuous improvement directly at the source of value creation.
How to Improve Gemba Walk Skills
Improving Gemba Walks involves a strategic approach focused on engagement, observation, and continuous improvement. Here’s a concise guide for a Lean Consultant:
Preparation: Before the walk, clearly define the objectives and inform the team to ensure openness and readiness for improvement. Learn more about preparation.
Observation: Focus on the process, not the people. Use all your senses to observe the flow of work, identifying wastes and opportunities for improvement. Observation tips.
Ask Questions: Utilize open-ended questions to understand the reasons behind current practices. Encourage team members to suggest improvements. Effective questioning.
Respect and Engage: Show respect to all employees, valuing their input and engaging them in problem-solving. Building respect.
Follow-up: Document findings and follow up on the action items. Visible follow-through builds trust and encourages participation in future walks. Follow-up strategies.
Continuous Learning: Regularly review and adapt the Gemba Walk process based on feedback and results to foster a culture of continuous improvement. Continuous Improvement.
By focusing on these areas, a Lean Consultant can significantly enhance the effectiveness of Gemba Walks, driving meaningful improvements in processes and culture.
How to Display Gemba Walk Skills on Your Resume
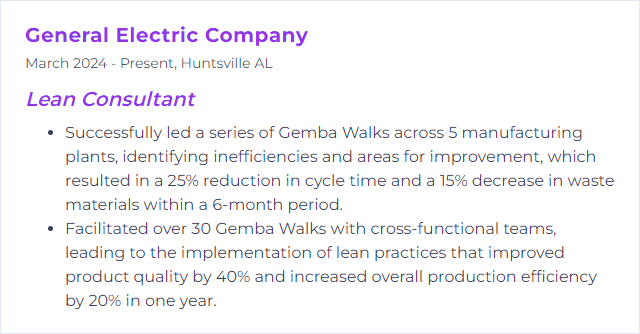