Top 12 Instrumentation Technician Skills to Put on Your Resume
Aspiring to excel as an instrumentation technician requires a unique blend of technical knowledge, analytical prowess, and practical skills. The ability to articulate these competencies effectively on your resume can set you apart in the competitive job market, highlighting your readiness to tackle the complexities of managing and maintaining sophisticated instrumentation systems.
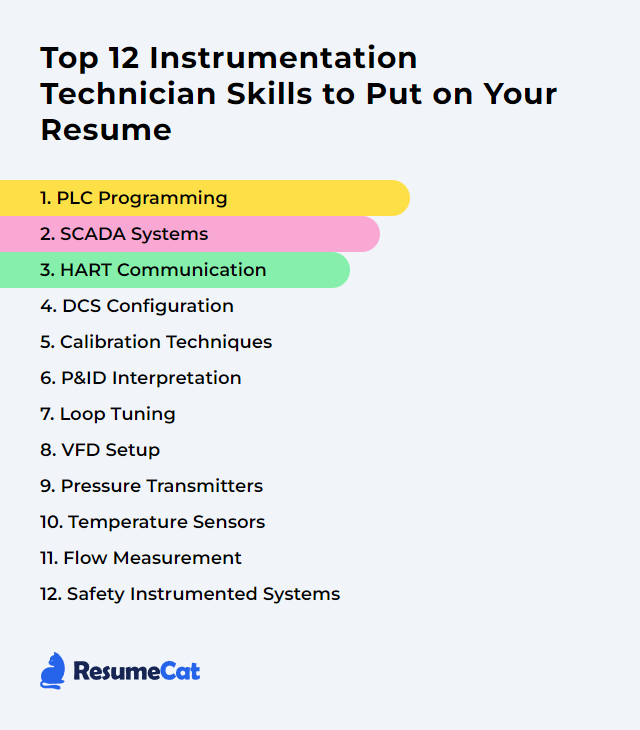
Instrumentation Technician Skills
- PLC Programming
- SCADA Systems
- HART Communication
- DCS Configuration
- Calibration Techniques
- P&ID Interpretation
- Loop Tuning
- VFD Setup
- Pressure Transmitters
- Temperature Sensors
- Flow Measurement
- Safety Instrumented Systems
1. PLC Programming
PLC programming involves creating and editing the software code used to control the operations of a Programmable Logic Controller (PLC), which automates industrial and mechanical processes in manufacturing, production, and other environments. For an Instrumentation Technician, it means designing, implementing, and troubleshooting the logic and sequences that dictate how machinery and processes respond to various inputs and conditions.
Why It's Important
PLC programming is crucial for an Instrumentation Technician because it enables the automation, control, and monitoring of industrial processes and machinery, ensuring efficiency, safety, and reliability in operations.
How to Improve PLC Programming Skills
Improving your PLC (Programmable Logic Controller) programming skills as an Instrumentation Technician involves continuous learning and practical application of best practices. Here are concise tips:
Understand Basics Thoroughly: Master the fundamentals of PLCs, including their architecture, input/output modules, and basic programming concepts. PLC Academy offers a solid starting point.
Learn Ladder Logic: Focus on mastering Ladder Logic, the most common PLC programming language. Practice by solving real-world problems. PLCdev has useful resources.
Study Structured Text: For more complex logic, understanding Structured Text can be beneficial. AutomationDirect provides a good introduction.
Hands-On Practice: Apply what you've learned by working on mini-projects or simulations. Platforms like PLCSimulator allow you to practice without physical PLCs.
Understand Industrial Networks: Knowledge of communication protocols (e.g., Profibus, Profinet, Ethernet/IP) used in your field enhances your ability to integrate PLCs with other systems. RealPars often covers such topics.
Stay Updated: Technologies and standards evolve, so stay informed about new PLC features and programming techniques through forums like PLCTalk.
Seek Feedback: Share your code and solutions with peers or on forums. Constructive criticism is invaluable for improvement.
Continuous Learning: Enroll in advanced courses or certifications focused on PLC programming. Online platforms like Udemy and Coursera offer relevant courses.
By following these steps and utilizing the provided resources, you'll be on your way to enhancing your PLC programming skills.
How to Display PLC Programming Skills on Your Resume
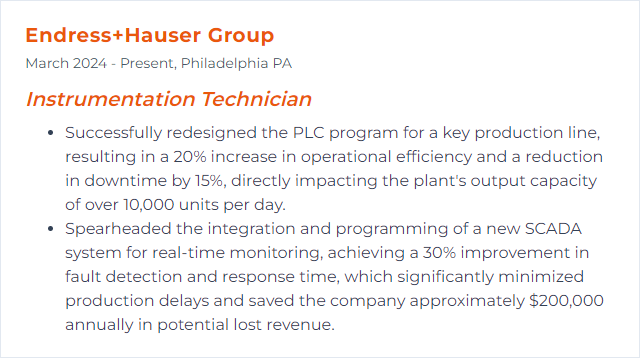
2. SCADA Systems
SCADA (Supervisory Control and Data Acquisition) systems are computer-based systems used by instrumentation technicians to monitor and control industrial processes, gather and process real-time data, and ensure efficient and safe operation of equipment in various sectors like water treatment, power generation, and manufacturing.
Why It's Important
SCADA systems are crucial for Instrumentation Technicians because they enable the centralized monitoring and control of industrial processes and equipment, ensuring operational efficiency, safety, and reliability.
How to Improve SCADA Systems Skills
Improving SCADA (Supervisory Control and Data Acquisition) systems involves enhancing their efficiency, reliability, and security. Here’s a brief guide tailored for an Instrumentation Technician:
Upgrade Hardware: Regularly update PLCs, RTUs, and network components to support newer protocols and technologies. Selecting PLCs.
Enhance Security: Implement robust cybersecurity measures including firewalls, VPNs, and intrusion detection systems. Regularly update software to patch vulnerabilities. Cybersecurity for SCADA Systems.
Optimize Network Architecture: Design a resilient network architecture with redundancy and failover capabilities to minimize downtime. Network Design Considerations.
Implement Data Analytics: Utilize advanced data analytics and machine learning algorithms to predict equipment failures and optimize processes. Leveraging Data in SCADA.
Regular Training and Updates: Ensure continuous education on the latest technologies and best practices for all technicians and operators. Training for SCADA.
Improve Human-Machine Interface (HMI): Design intuitive and user-friendly interfaces for better decision-making and easier control. Effective HMI Design.
By focusing on these areas, an Instrumentation Technician can significantly contribute to the improvement of SCADA systems, enhancing overall operational efficiency, reliability, and security.
How to Display SCADA Systems Skills on Your Resume
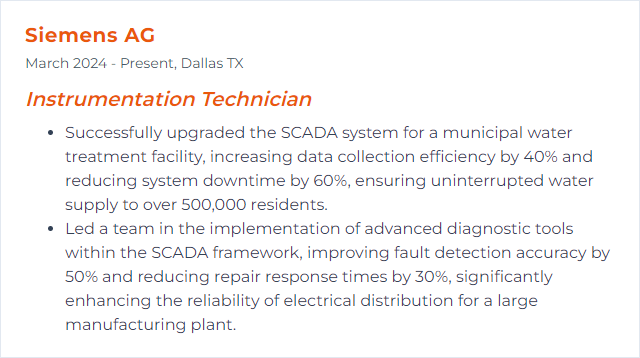
3. HART Communication
HART Communication (Highway Addressable Remote Transducer) is a digital communication technology used for sending and receiving digital information across analog wiring between smart devices and control or monitoring systems. This allows for two-way field communication, enabling not only device monitoring but also configuration and diagnostics over existing 4-20mA signal paths. For an Instrumentation Technician, this means the ability to access and adjust device settings, perform troubleshooting, and enhance process control without interrupting the analog signal.
Why It's Important
HART (Highway Addressable Remote Transducer) Communication is important for an Instrumentation Technician because it enables two-way digital communication over existing analog wiring, allowing for real-time access to device diagnostics, configuration, and process information without interrupting the analog signal. This enhances troubleshooting, maintenance, and calibration efficiency.
How to Improve HART Communication Skills
To improve HART (Highway Addressable Remote Transducer) Communication, follow these concise steps:
Update Device Firmware: Ensure all your HART devices are running on the latest firmware version. Manufacturers often release updates that enhance communication efficiency and compatibility. Consult the manufacturer's website for firmware updates.
Use Quality Cables and Connectors: Opt for high-quality, shielded twisted-pair cables and ensure connectors are properly installed to minimize noise and signal degradation. Belden offers a range of suitable cables.
Proper Grounding and Shielding: Implement proper grounding techniques and use shielded cables to protect against electromagnetic interference (EMI). This grounding and shielding guide provides essential tips.
Avoid Overloading the Loop: Ensure the loop is not overloaded with too many devices, as this can impair communication. Follow the manufacturer's recommendations on the maximum number of devices per loop.
Regular Calibration and Maintenance: Regularly calibrate HART devices and perform preventive maintenance to ensure optimal performance. This calibration guide from Fluke offers best practices.
Use a HART Modem for Configuration: A dedicated HART modem can facilitate better communication for device configuration and troubleshooting. The FieldComm Group lists compatible modems.
Training and Knowledge: Stay updated with the latest HART communication protocols and troubleshooting techniques through continuous learning. The International Society of Automation (ISA) offers courses and certifications.
By following these steps, you can enhance the reliability and efficiency of your HART communication network.
How to Display HART Communication Skills on Your Resume
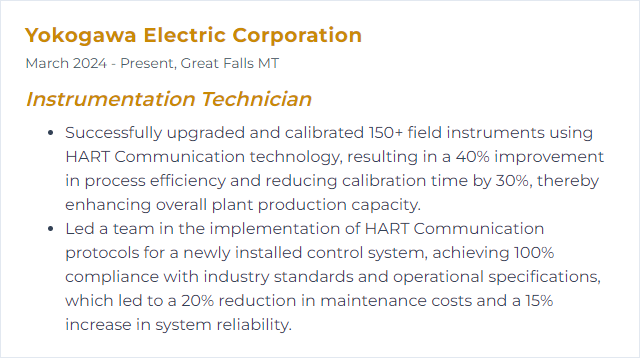
4. DCS Configuration
DCS (Distributed Control System) configuration involves setting up and defining the parameters and control strategies of various interconnected components in a DCS to manage and control industrial processes. This includes configuring input/output (I/O) modules, control loops, process alarms, operator interfaces, and network settings to ensure efficient, reliable, and safe operation of the plant. For an Instrumentation Technician, it involves the practical application of configuring hardware and software elements to achieve desired process control and monitoring.
Why It's Important
DCS (Distributed Control System) configuration is crucial because it ensures accurate process control, system reliability, and safety. For an Instrumentation Technician, proper DCS configuration allows for efficient monitoring, troubleshooting, and maintenance of the system, optimizing plant performance and minimizing downtime.
How to Improve DCS Configuration Skills
Improving a Distributed Control System (DCS) configuration involves optimizing system performance, enhancing process control, and ensuring system reliability. As an Instrumentation Technician, here are concise steps to improve DCS Configuration:
Understand System Architecture: Gain a comprehensive understanding of your DCS architecture. Knowing how components interact helps in pinpointing areas for improvement. Emerson's DCS Architecture Overview can provide insights.
Regular System Diagnostics and Maintenance: Perform regular diagnostics and preventive maintenance to identify and fix issues before they escalate. Yokogawa's Maintenance Guide offers practical maintenance tips.
Software Updates and Patches: Ensure your DCS software is up to date with the latest patches and updates for enhanced performance and security. Siemens' Software Update Service provides a structured approach.
Optimize Control Loops: Regularly review and optimize control loop configurations to ensure process efficiency and stability. Control Engineering's Loop Tuning Fundamentals can help understand and apply optimization techniques.
Network Optimization: Optimize network configurations to reduce latency and improve data integrity. Cisco's Industrial Network Design guides on setting up efficient industrial networks.
Enhance Security Measures: Implement robust security measures to protect against cyber threats. ISA/IEC 62443 Standards provide frameworks for industrial network security.
Training and Skill Development: Continuously improve your skills and knowledge related to DCS systems. ISA Training and Education offers courses on various aspects of control systems and instrumentation.
Leverage Advanced Analytics: Use data analytics tools for predictive maintenance and process optimization. Honeywell's Advanced Analytics demonstrates how to leverage data for operational improvements.
By systematically applying these steps, you can enhance the performance and reliability of your DCS configuration.
How to Display DCS Configuration Skills on Your Resume
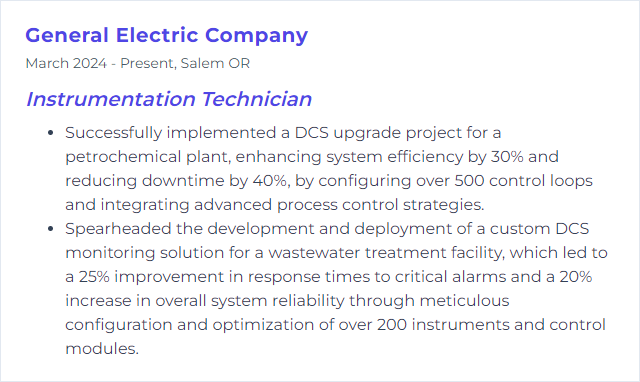
5. Calibration Techniques
Calibration techniques involve a set of procedures used by instrumentation technicians to adjust and verify the accuracy of measuring instruments. These techniques ensure that instruments produce results within specified tolerances by comparing them against known standards or reference instruments. Calibration involves adjustment, testing, and documentation processes to ensure instruments perform correctly and reliably within their operational environment.
Why It's Important
Calibration techniques are important for an Instrumentation Technician because they ensure the accuracy and reliability of measuring instruments, guaranteeing that measurements are consistent with standards or specifications, thereby maintaining process safety, quality control, and regulatory compliance.
How to Improve Calibration Techniques Skills
Improving calibration techniques for an Instrumentation Technician involves focusing on accuracy, consistency, and adherence to standards. Here are concise strategies:
Use Traceable Standards: Ensure all calibration equipment is traceable to national or international standards. This ensures the accuracy and reliability of your calibrations. NIST provides guidelines and traceability paths.
Regular Calibration: Calibrate instrumentation regularly to maintain accuracy over time. Scheduling depends on the manufacturer's recommendations and the instrument's usage frequency. Fluke offers insight into calibration frequency and practices.
Proper Environment: Perform calibrations in a controlled environment. Temperature, humidity, and electrical interference can affect calibration accuracy. ISA provides standards on environmental conditions for calibration.
Adequate Training: Ensure technicians are well-trained on the latest calibration techniques and understand the principles behind the instruments they are calibrating. Continuous education can be found through organizations like ISA.
Use Quality Equipment: Invest in high-quality calibration equipment with proven accuracy and reliability. Regular maintenance and checks on this equipment are also crucial.
Document Procedures: Develop and follow detailed calibration procedures. This ensures consistency and repeatability in calibrations. ISO standards often outline proper documentation practices.
Review and Adjust: Regularly review calibration data and procedures to identify trends or recurring issues that may indicate a need for process adjustments.
Peer Review: Have calibration work reviewed by another qualified technician to ensure accuracy and adherence to procedures.
By focusing on these areas, an Instrumentation Technician can significantly enhance the accuracy, reliability, and efficiency of their calibration techniques.
How to Display Calibration Techniques Skills on Your Resume
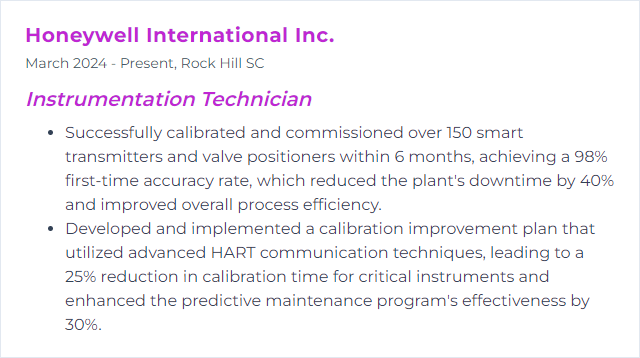
6. P&ID Interpretation
P&ID Interpretation for an Instrumentation Technician involves reading and understanding Piping and Instrumentation Diagrams to identify and analyze the layout of pipes, instruments, and control systems within a facility, ensuring proper installation, maintenance, and troubleshooting of instrumentation and control equipment.
Why It's Important
P&ID interpretation is crucial for an Instrumentation Technician because it enables the understanding of process flows, equipment relationships, and control system architecture, essential for installing, troubleshooting, and maintaining instrumentation accurately and safely.
How to Improve P&ID Interpretation Skills
Improving P&ID (Piping and Instrumentation Diagram) interpretation, especially for an Instrumentation Technician, involves enhancing familiarity with symbols, understanding system layout, and continuous practice. Here's a concise guide:
Learn the Symbols: Begin with mastering common symbols used in P&IDs for instruments, valves, pumps, and piping. Engineering.com provides resources and articles that may include symbol guides.
Understand System Flow: Grasping how systems operate within the P&ID, including process flow directions, is crucial. ISA (International Society of Automation) offers resources and training aimed at understanding system operations.
Study Standards: Familiarize yourself with relevant standards, such as ISA-5.1 for instrumentation symbols and nomenclature. Documentation and courses can be found on ISA’s website.
Practical Application: Apply your knowledge by practicing with actual P&IDs. Websites like PlantDesignHub may offer sample P&IDs for study.
Continuous Learning: P&ID interpretation skills improve with experience and ongoing education. Consider enrolling in online courses focused on P&ID from platforms like Udemy or Coursera.
By focusing on these areas, an Instrumentation Technician can significantly enhance their P&ID interpretation skills.
How to Display P&ID Interpretation Skills on Your Resume
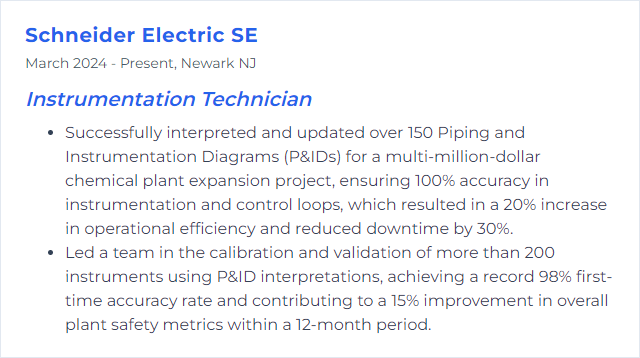
7. Loop Tuning
Loop tuning is the process of adjusting the parameters of a control loop (P, I, D - Proportional, Integral, Derivative) to optimize the performance of a control system, ensuring it responds accurately and efficiently to changes in setpoint or process disturbances.
Why It's Important
Loop tuning is essential for ensuring process control systems operate efficiently, accurately, and reliably, minimizing process variability, optimizing performance, and ensuring safety and product quality.
How to Improve Loop Tuning Skills
Improving loop tuning involves optimizing the performance of control loops to enhance process stability, efficiency, and safety. Here are concise steps that an Instrumentation Technician can take, along with relevant external resources for deeper insights:
Understand the Process: Gain a clear understanding of the process dynamics and the role of the loop in question. Process Dynamics and Control
Identify Loop Type: Determine whether it's a PID (Proportional, Integral, Derivative) loop or another type for appropriate tuning strategy. PID Control
Gather Data: Collect process data, including response times and steady-state errors, necessary for tuning. Loop Tuning Fundamentals
Select a Tuning Method: Choose an appropriate tuning method such as Ziegler-Nichols, Cohen-Coon, or model-based tuning depending on your specific loop and process requirements. Tuning Methods
Apply Initial Settings: Based on the selected method, calculate and apply initial PID settings. PID Tuning Guide
Iterate and Adjust: Monitor the loop performance and iteratively adjust PID settings to minimize overshoot, settle time, and steady-state error. Iterative Loop Tuning
Use Software Tools: Consider using software tools for simulation and tuning to achieve more accurate results. Software Tools for Loop Tuning
Document Changes: Keep detailed records of the tuning process and results for future reference and continuous improvement. Documentation Best Practices
By following these steps and utilizing the resources provided, an Instrumentation Technician can effectively improve loop tuning, resulting in optimized process control and performance.
How to Display Loop Tuning Skills on Your Resume
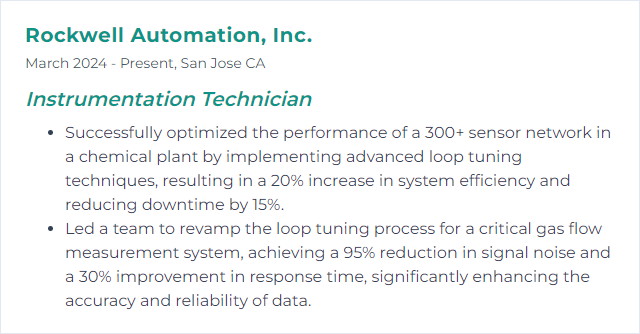
8. VFD Setup
A VFD (Variable Frequency Drive) setup involves configuring a system to control the speed and torque of electric motors by varying the input frequency and voltage. For an Instrumentation Technician, this means installing the VFD, programming it according to motor specifications, and ensuring it communicates correctly with control systems to adjust motor operation based on process requirements.
Why It's Important
A VFD (Variable Frequency Drive) setup is crucial for an Instrumentation Technician because it allows precise control of motor speed, enhances process efficiency, reduces energy consumption, and prolongs equipment lifespan.
How to Improve VFD Setup Skills
Improving a Variable Frequency Drive (VFD) setup involves optimizing its configuration for efficient and reliable operation. Here's a concise guide tailored for an Instrumentation Technician:
Read the Manual: Start with the manufacturer's manual. It contains specific instructions and parameters for optimization.
Correct Parameter Settings: Fine-tune parameters like acceleration/deceleration rates, maximum/minimum frequency, and motor control method to match the application requirements. Parameter Optimization Guide.
Ensure Proper Ventilation: Overheating reduces efficiency and lifespan. Ensure the VFD is installed in a well-ventilated area or use additional cooling if necessary. VFD Cooling and Ventilation.
Use EMC Filters: To mitigate electromagnetic interference, which can affect other instrumentation and control systems, install EMC (Electromagnetic Compatibility) filters. EMC Filters Introduction.
Regular Maintenance: Schedule regular inspections for connections, dust buildup, and component wear. Use a thermal camera to detect overheating components. Preventive Maintenance Guide.
Update Firmware: Ensure the VFD's firmware is up to date. Manufacturers often release updates that improve performance and add new features. Firmware Update Best Practices.
Harmonics Mitigation: Install harmonic filters or use multi-pulse VFD arrangements to reduce the effects of harmonics on the power system. Harmonics and Solutions.
Network Integration: Integrate the VFD with the plant's control network for better monitoring and control. Use appropriate communication protocols and ensure secure configurations. Industrial Network Integration.
By following these steps, an Instrumentation Technician can significantly improve the performance and reliability of a VFD setup, ensuring it meets the application's demands efficiently.
How to Display VFD Setup Skills on Your Resume
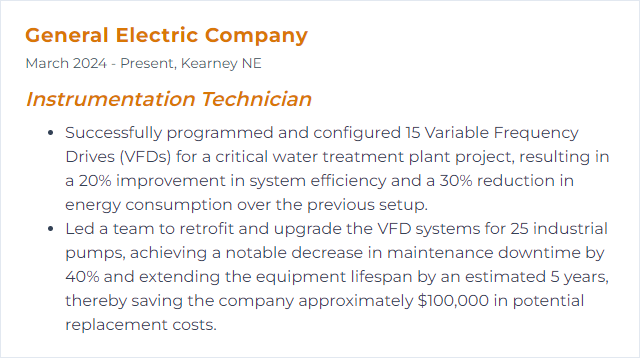
9. Pressure Transmitters
Pressure transmitters are devices used to measure the pressure of liquids, gases, or steam and convert this measurement into an electrical signal for monitoring and control purposes in various industrial applications.
Why It's Important
Pressure transmitters are crucial for accurately monitoring and controlling process pressure in industrial systems, ensuring safety, efficiency, and product quality. They provide real-time data for system adjustments and preventive maintenance, essential for an Instrumentation Technician's work in maintaining system integrity and performance.
How to Improve Pressure Transmitters Skills
Improving pressure transmitters involves several key steps focused on accuracy, reliability, and efficiency. Here's a concise guide:
Calibration: Regularly calibrate pressure transmitters to ensure accurate readings. Use a trusted calibration standard. Fluke Calibration offers comprehensive tools and information.
Installation: Properly install pressure transmitters to avoid measurement errors. Ensure the transmitter is mounted according to the manufacturer's recommendations. Emerson's Installation Guide provides best practices.
Maintenance: Perform routine maintenance to prevent failures. This includes cleaning, checking for leaks, and inspecting wiring. Yokogawa's Maintenance Tips can be a valuable resource.
Environmental Protection: Protect transmitters from extreme temperatures and corrosive environments. Consider protective enclosures. WIKA's Guide discusses environmental considerations.
Update Firmware/Software: Ensure the transmitter's firmware or software is up-to-date for optimal performance. Refer to the manufacturer's website for updates.
Training: Stay informed about the latest techniques and technologies. Continuous learning can significantly improve handling and troubleshooting skills. ISA Training offers courses in instrumentation and control.
Remember, each step is crucial for the optimal performance of pressure transmitters, enhancing system reliability, and minimizing downtime.
How to Display Pressure Transmitters Skills on Your Resume
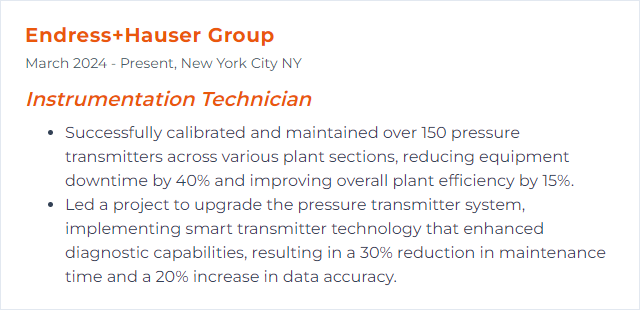
10. Temperature Sensors
Temperature sensors are devices used by instrumentation technicians to measure and monitor the temperature of a system or process, converting the temperature into a readable signal for control or display purposes.
Why It's Important
Temperature sensors are crucial for monitoring and controlling processes accurately, ensuring safety, product quality, and energy efficiency in various industrial applications.
How to Improve Temperature Sensors Skills
Improving temperature sensors involves enhancing accuracy, response time, stability, and environmental robustness. As an Instrumentation Technician, consider the following steps:
Calibration: Regularly calibrate sensors to maintain accuracy. Use industry standards for guidance. NIST's Calibration Services provides a comprehensive approach.
Installation: Correct placement avoids heat sources or cold spots affecting readings. ISA's Installation Practices offers guidelines.
Shielding and Wiring: Use shielding to protect against electromagnetic interference and choose appropriate wiring to minimize resistance changes. Omega's Guide on Thermocouple Wiring is a practical resource.
Sensor Selection: Choose the right type of sensor (e.g., RTD, thermistor, thermocouple) for your application's temperature range and accuracy requirements. Sensors Magazine provides insights into sensor types and applications.
Environmental Compensation: Implement algorithms or devices that compensate for environmental effects, such as humidity and pressure, on temperature readings. Texas Instruments' Sensor Solutions offer various options for compensation.
Maintenance: Regularly inspect, clean, and replace sensors to prevent drift and ensure longevity. Fluke's Maintenance Tips can help with best practices.
By focusing on these areas, you can significantly improve the performance and reliability of temperature sensors in your applications.
How to Display Temperature Sensors Skills on Your Resume
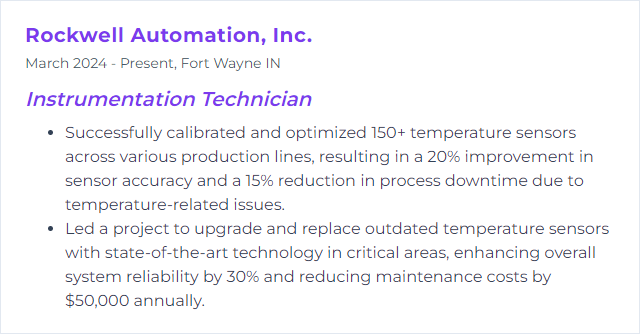
11. Flow Measurement
Flow measurement refers to the quantification of bulk fluid movement, involving the determination of the amount of fluid (liquid, gas, or vapor) passing through a point or a pipeline over time. It is crucial for process control, safety, and accounting purposes in various industries. Instruments used include flow meters, which technicians install, calibrate, and maintain to ensure accurate and reliable measurements.
Why It's Important
Flow measurement is crucial for ensuring accurate process control, optimizing system performance, and guaranteeing safety and regulatory compliance in various industrial applications.
How to Improve Flow Measurement Skills
Improving flow measurement involves several key steps focused on accuracy, calibration, maintenance, and technology upgrades. Here's a concise guide:
Calibration: Regularly calibrate flow meters to ensure accuracy. Calibration should be done against a known standard. NIST offers guidelines and standards for calibration processes.
Maintenance: Perform routine maintenance to prevent and address wear, corrosion, or buildup that might affect measurement accuracy. ISA provides resources on maintenance best practices.
Selection: Choose the right flow meter for your specific application, considering fluid properties, flow range, and environmental conditions. Flow Control Network offers insights on selecting appropriate flow measurement technologies.
Installation: Ensure proper installation according to manufacturer guidelines. Incorrect installation can significantly affect performance. Engineering Toolbox provides general tips on installation practices.
Use of Diagnostics: Modern flow meters come with diagnostic capabilities. Use these features to detect issues early and ensure optimal performance. Emerson has resources on advanced diagnostic features of flow meters.
Upgrade Technology: Consider upgrading to more advanced flow meter technologies that offer better accuracy, reliability, and ease of use. Endress+Hauser showcases the latest advancements in flow measurement technology.
By focusing on these areas, you can significantly improve the accuracy and reliability of your flow measurement systems.
How to Display Flow Measurement Skills on Your Resume
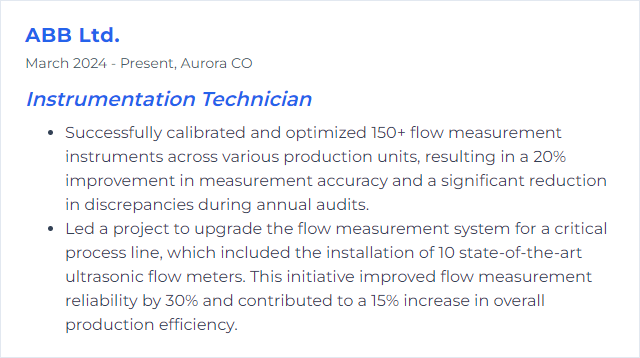
12. Safety Instrumented Systems
Safety Instrumented Systems (SIS) are engineered sets of hardware and software controls that are specifically designed to mitigate unsafe conditions in industrial processes by bringing the process to a safe state when predetermined conditions are violated. For an Instrumentation Technician, SIS involves the installation, maintenance, and testing of these safety-critical systems to ensure they function correctly and respond as expected during abnormal conditions to protect people, equipment, and the environment.
Why It's Important
Safety Instrumented Systems (SIS) are crucial because they provide automated protection against potentially hazardous conditions, ensuring the safety of personnel, equipment, and the environment by taking corrective actions to mitigate risks during process anomalies or failures.
How to Improve Safety Instrumented Systems Skills
Improving Safety Instrumented Systems (SIS) involves ensuring they are capable of effectively reducing risks to acceptable levels. Here’s a concise guide tailored for an Instrumentation Technician:
Understand and Apply Standards: Get familiar with relevant standards such as IEC 61511 and ISA 84.00.01. These provide the framework for designing, implementing, and maintaining SIS.
Regular Testing and Maintenance: Perform periodic testing and preventive maintenance as recommended by the manufacturer and best practices. This ensures the system's reliability and availability. ISA offers resources and guidelines on effective maintenance strategies.
Systematic Safety Lifecycle Management: Implement a safety lifecycle approach as outlined in standards, from hazard and risk assessment through decommissioning. The CCPS provides resources on managing the safety lifecycle effectively.
Continuous Training: Stay updated with the latest technologies, standards, and best practices through ongoing education. Organizations like ISA offer specialized training courses for instrumentation technicians.
Layer of Protection Analysis (LOPA): Utilize LOPA to evaluate the effectiveness of safety layers and ensure the SIS is capable of mitigating identified risks. Resources on LOPA can be found through AIChE’s CCPS.
Functional Safety Assessment and Audits: Regularly conduct functional safety assessments and audits to verify that the SIS meets all the requirements and functions as intended. Guidance on assessments and audits is available from IEC and ISA.
By focusing on these key areas, an Instrumentation Technician can significantly contribute to enhancing the safety and reliability of Safety Instrumented Systems.
How to Display Safety Instrumented Systems Skills on Your Resume
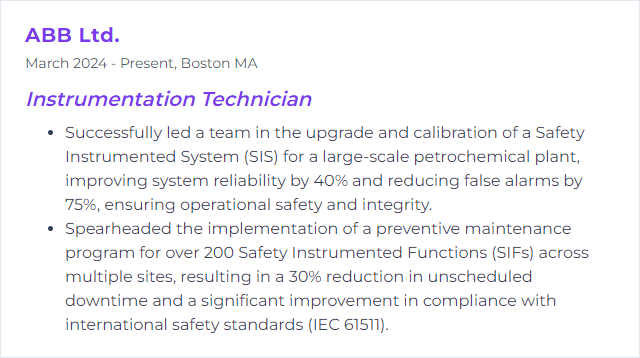