Top 12 Factory Worker Skills to Put on Your Resume
In today's competitive job market, standing out as a factory worker necessitates showcasing a blend of technical prowess and soft skills on your resume. Highlighting the top factory worker skills not only demonstrates your capability to potential employers but also underscores your commitment to excellence and efficiency in a fast-paced industrial environment.

Factory Worker Skills
- CNC Operation
- Welding (MIG/TIG)
- Assembly Line Efficiency
- Forklift Operation
- Quality Control
- Machine Maintenance
- Lean Manufacturing
- Six Sigma
- Inventory Management
- CAD Software
- Robotics Programming
- Safety Compliance
1. CNC Operation
CNC operation involves using computer-controlled machines to precisely cut, shape, and finish materials into parts or products, following programmed instructions without manual intervention.
Why It's Important
CNC operation is crucial for a factory worker because it enhances precision in manufacturing, increases production speed, and reduces manual labor, leading to more efficient, consistent, and high-quality production outcomes.
How to Improve CNC Operation Skills
Improving CNC operation involves enhancing efficiency, accuracy, and safety. Here are concise strategies for a factory worker:
Continuous Learning: Stay updated with the latest CNC technologies and techniques through online courses and tutorials. MasterClass and Udemy offer various relevant courses.
Routine Maintenance: Regularly clean and maintain your CNC machine to prevent breakdowns and ensure precision. The Haas Automation Maintenance page provides insights on upkeep.
Optimize Cutting Conditions: Adjust speed, feed, and depth according to material and tooling specifications. MachiningCloud is a great resource for tool selection and optimization.
Use High-Quality Tooling: Invest in quality cutting tools for better performance and longer life. Research options on MSC Industrial Supply or Sandvik Coromant.
Implement CAD/CAM Software: Utilize computer-aided design/manufacturing software for efficient programming and simulation. Explore options such as Autodesk Fusion 360 or SolidWorks.
Quality Control: Regularly inspect parts during production to maintain high-quality standards. Learn about quality control tools and techniques at ASQ.
Safety First: Always adhere to safety protocols to prevent accidents. OSHA’s Machine Guarding guidelines are crucial.
By focusing on these areas, factory workers can significantly improve their CNC operation efficiency, quality, and safety.
How to Display CNC Operation Skills on Your Resume
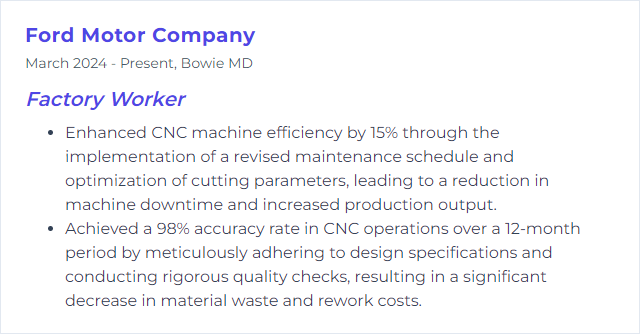
2. Welding (MIG/TIG)
Welding, specifically MIG (Metal Inert Gas) and TIG (Tungsten Inert Gas), are processes used to join metal parts. MIG welding uses a continuously feeding wire and shielding gas to melt and fuse materials together. TIG welding uses a non-consumable tungsten electrode and often requires a filler material, offering precise control for detailed welds. Both methods are essential in manufacturing for creating strong, durable joins in metal workpieces.
Why It's Important
Welding, including MIG and TIG techniques, is crucial for a factory worker because it enables the strong and precise joining of metal parts, essential for manufacturing durable and high-quality products.
How to Improve Welding (MIG/TIG) Skills
Improving MIG/TIG welding skills, especially for a factory worker, involves a combination of practice, knowledge enhancement, and adopting best practices. Here are concise tips:
Understand the Basics: Ensure a solid understanding of welding fundamentals. Miller Electric offers comprehensive guides on MIG and TIG welding basics.
Proper Equipment Setup: Correctly set up your welding machine. Lincoln Electric provides a guide on equipment setup for optimal performance.
Material Preparation: Clean and prepare materials before welding. This includes removing any coating and ensuring a good fit-up. Welding Tips and Tricks has practical advice on preparation.
Practice Consistently: Regular practice improves skill. Experiment with different angles, speeds, and settings.
Safety First: Always adhere to safety guidelines. The American Welding Society offers detailed safety and health fact sheets.
Seek Feedback and Further Training: Learn from experienced welders and consider additional training. The Hobart Institute of Welding Technology offers courses for advancing welding skills.
Stay Updated: Welding technology and techniques evolve. Follow industry updates through resources like Fabricating & Metalworking.
By focusing on these areas, factory workers can significantly improve their MIG/TIG welding skills, leading to higher quality work and increased productivity.
How to Display Welding (MIG/TIG) Skills on Your Resume
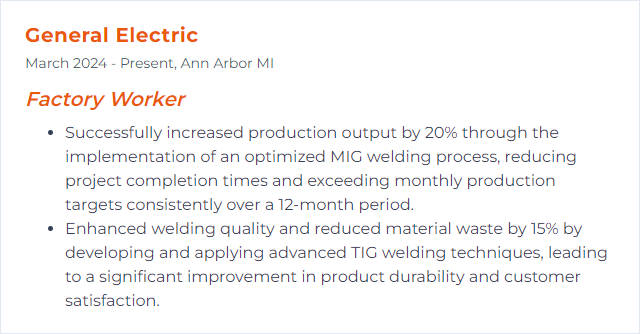
3. Assembly Line Efficiency
Assembly line efficiency refers to the effectiveness with which a production line operates to maximize output with minimal waste and downtime. For a factory worker, it means performing their part of the production process quickly and accurately, minimizing delays and errors, to ensure smooth and continuous product flow.
Why It's Important
Assembly line efficiency is crucial for a factory worker because it directly impacts productivity, reduces work fatigue, and increases the potential for higher earnings through more efficient production processes.
How to Improve Assembly Line Efficiency Skills
Improving assembly line efficiency involves several key strategies aimed at enhancing productivity and reducing waste. Here's a short and concise guide:
Optimize Workflow: Evaluate the assembly line to identify bottlenecks and streamline the workflow. Implementing lean manufacturing principles can significantly improve efficiency. Lean Manufacturing
Implement Automation: Where feasible, introduce automation to handle repetitive tasks, reducing human error and speeding up production. Automation in Manufacturing
Regular Maintenance: Ensure regular maintenance and upgrades of machinery to prevent breakdowns and maintain consistent production quality. Preventive Maintenance
Employee Training: Invest in continuous training for workers to improve their skills and adapt to new technologies or processes. Employee Training
Quality Control: Implement strict quality control measures at various stages of the production process to reduce defects and rework. Quality Control
Feedback and Communication: Encourage feedback from workers for insights on improving processes and maintain open lines of communication for better coordination. Effective Communication
By focusing on these areas, factory workers and management can work together to improve assembly line efficiency, leading to increased productivity and reduced costs.
How to Display Assembly Line Efficiency Skills on Your Resume
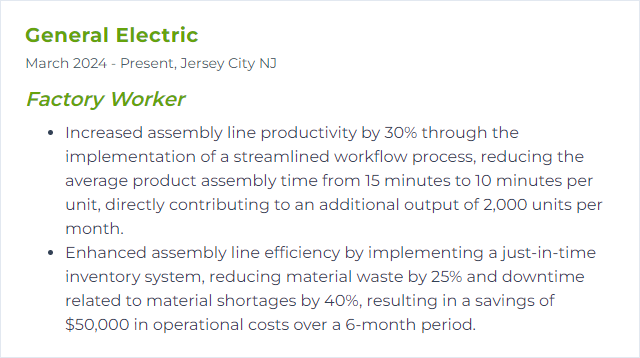
4. Forklift Operation
Forklift operation involves maneuvering a powered industrial truck equipped with a mast and an elevating load carriage to lift and transport materials across short distances within a factory or warehouse setting.
Why It's Important
Forklift operation is crucial for a factory worker as it enables efficient material handling, reduces manual labor, enhances safety in moving heavy loads, and improves productivity and workflow within the facility.
How to Improve Forklift Operation Skills
Improving forklift operation for a factory worker involves enhancing safety, efficiency, and skill. Follow these concise steps:
Get Certified: Obtain proper forklift certification through accredited programs. This ensures you understand the basics of operation and safety. OSHA Forklift Training provides guidelines and resources.
Regular Maintenance: Ensure the forklift is in optimal condition by performing pre-use inspections and regular maintenance. Forklift Maintenance Tips offer a checklist to follow.
Practice Safe Operation: Always adhere to safety protocols, like wearing seat belts, observing speed limits, and following factory floor guidelines. NIOSH Workplace Safety & Health Topics outlines best practices.
Continual Learning: Stay updated on new forklift technologies and operational techniques by attending workshops or online courses. Material Handling Education Foundation, Inc. provides resources for ongoing education.
Efficient Operation: Learn and apply techniques for efficient material handling, such as proper stacking and load management. Efficient Forklift Use offers tips to enhance productivity.
By focusing on certification, maintenance, safety, continual learning, and efficient operation, a factory worker can significantly improve their forklift operation skills.
How to Display Forklift Operation Skills on Your Resume
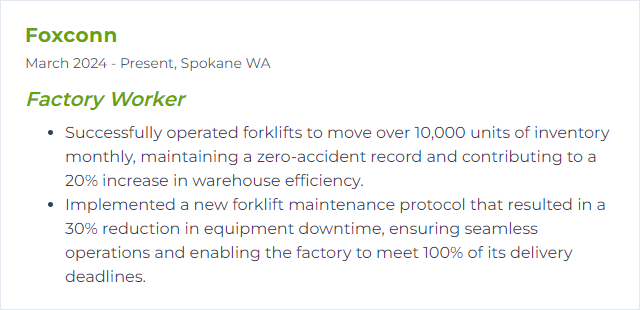
5. Quality Control
Quality Control is the process of ensuring that products meet specified standards of quality and safety before they are shipped to customers, involving inspections, testing, and corrective actions as needed.
Why It's Important
Quality Control is important because it ensures the products we manufacture meet the required standards, reducing waste, avoiding costly errors, and maintaining customer satisfaction and trust.
How to Improve Quality Control Skills
Improving Quality Control as a factory worker involves a focused approach on precision, awareness, and continuous learning. Here are concise steps to enhance Quality Control:
Understand Specifications: Familiarize yourself with the product specifications and standards. Quality Standards provide a reference point for the expected quality.
Use the Right Tools: Ensure you're equipped with the correct tools and equipment. Proper tools reduce errors. Learn more about quality tools at ASQ’s Quality Resources.
Regular Training: Engage in regular training sessions. Continuous learning through platforms like Coursera can keep you updated on the latest QC techniques.
Perform Self-Checks: Regularly check your work against quality standards. Immediate self-checks prevent errors from moving down the production line.
Feedback Loop: Participate in feedback loops. Reporting issues and providing suggestions can lead to process improvements. Learn about feedback systems at Feedback Loops in Manufacturing.
Maintain a Clean Workspace: A clean and organized workspace prevents accidents and mistakes. 5S Methodology helps in maintaining an efficient and safe working environment.
Team Communication: Effective communication with your team ensures everyone is aligned with the quality goals. Explore Team Communication Strategies for better collaboration.
By integrating these steps into your daily routine, you can significantly contribute to improving Quality Control in your factory setting.
How to Display Quality Control Skills on Your Resume
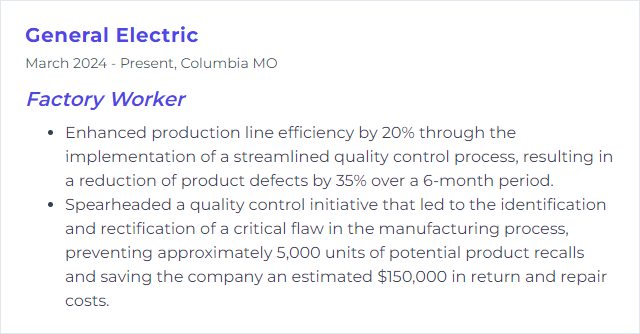
6. Machine Maintenance
Machine maintenance is the routine care, checking, and repairing of machinery to ensure it operates smoothly, safely, and efficiently.
Why It's Important
Machine maintenance is crucial for ensuring safety, preventing costly downtime, and maintaining productivity and product quality in a factory setting.
How to Improve Machine Maintenance Skills
To improve machine maintenance, a factory worker should:
Adhere to a Preventive Maintenance Schedule: Regularly check and service machines as per the manufacturer’s guidelines to prevent breakdowns. Preventive Maintenance Guide
Use Condition Monitoring: Employ sensors and IoT devices to monitor machine performance and predict failures before they occur. Condition Monitoring Basics
Keep Machines Clean: Ensure machines are free from dust, debris, and lubricant build-up that can cause wear and tear. Importance of Cleanliness
Train and Educate: Constantly update skills and knowledge on the latest maintenance techniques and machine handling. Maintenance Training Tips
Implement a CMMS: Use a Computerized Maintenance Management System for efficient tracking and management of maintenance activities. Introduction to CMMS
Regularly Update Maintenance Records: Accurately document maintenance activities, issues, and solutions for future reference. Maintenance Record Keeping
Follow Safety Protocols: Always adhere to safety guidelines to prevent accidents during maintenance. Safety Protocols
By integrating these strategies, a factory worker can significantly improve machine maintenance, ensuring operational efficiency and extending the lifespan of machinery.
How to Display Machine Maintenance Skills on Your Resume
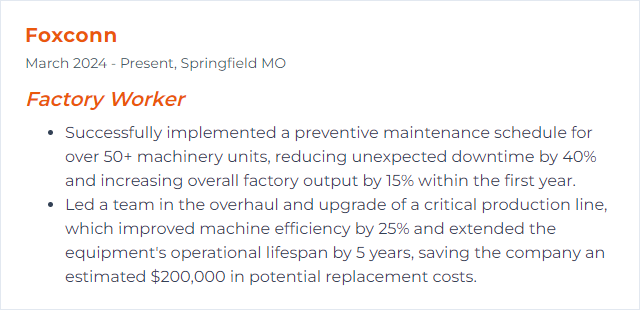
7. Lean Manufacturing
Lean Manufacturing is a method that focuses on reducing waste and improving efficiency in production processes to make better products faster and at a lower cost.
Why It's Important
Lean Manufacturing minimizes waste and improves efficiency, allowing for faster production times, higher quality products, and a safer, more organized workplace, directly benefiting factory workers by enhancing job satisfaction and security.
How to Improve Lean Manufacturing Skills
Improving Lean Manufacturing, especially from a factory worker's perspective, involves focusing on continuous improvement, waste reduction, and enhancing process efficiency. Here are concise strategies:
Embrace Continuous Improvement: Continuously seek ways to improve your daily tasks and workflows. Suggest improvements based on your observations (Kaizen).
Reduce Waste: Identify and eliminate waste in your processes, including excess motion, overproduction, and waiting times (The 7 Wastes of Lean).
Standardize Work: Develop and follow standard operating procedures to ensure consistency and efficiency in your tasks (Standardized Work).
Use Visual Management: Utilize visual aids like signs, labels, and color codes to streamline workflow and communication (Visual Management).
Participate in Training: Engage in lean manufacturing training programs to understand lean principles and tools more deeply (Lean Training).
By actively participating in these strategies, factory workers can contribute significantly to the advancement of lean manufacturing in their workplaces.
How to Display Lean Manufacturing Skills on Your Resume
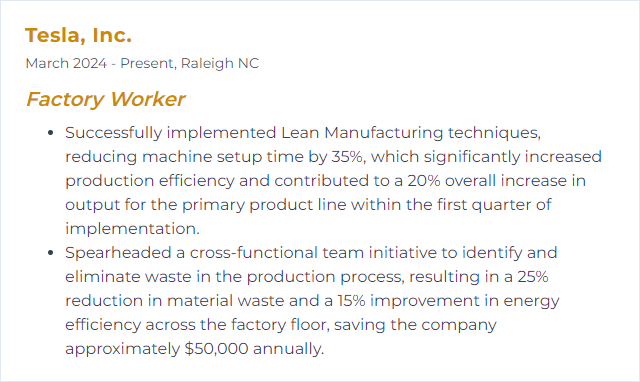
8. Six Sigma
Six Sigma is a set of techniques and tools aimed at improving manufacturing processes, reducing defects, and ensuring quality, aiming to increase efficiency and product quality on the factory floor.
Why It's Important
Six Sigma is important for a factory worker because it aims to reduce errors and improve product quality, leading to safer working conditions and more consistent, efficient production processes.
How to Improve Six Sigma Skills
Improving Six Sigma as a factory worker involves focusing on reducing waste, enhancing quality, and streamlining processes. Here are concise steps:
Understand Fundamentals: Familiarize yourself with the basics of Six Sigma principles. ASQ’s Six Sigma resources are a good starting point.
Identify Areas for Improvement: Look for processes that frequently result in defects or inefficiencies. Tools like Pareto Charts can help prioritize issues.
Engage in Team Collaboration: Participate in or suggest regular team meetings to discuss process improvements. Use platforms like Slack for continuous communication.
Implement 5S Methodology: Adopt the 5S (Sort, Set in order, Shine, Standardize, Sustain) approach to organize and streamline your workspace. Lean Manufacturing Tools offers detailed insights.
Seek Training and Certification: While more relevant for those looking to take a leadership role in Six Sigma projects, gaining a Six Sigma Certification can provide valuable knowledge and skills.
Use Six Sigma Tools: Employ Six Sigma tools such as Fishbone Diagrams for problem-solving and Control Charts for monitoring process variations.
Provide Feedback and Suggestions: Use your frontline experience to offer actionable feedback to management on potential improvements.
Embrace Continuous Learning: Stay informed about the latest techniques and tools in Six Sigma and lean manufacturing through platforms like Coursera and edX.
By actively engaging with these steps, factory workers can contribute significantly to Six Sigma initiatives, driving efficiency and quality improvements in manufacturing processes.
How to Display Six Sigma Skills on Your Resume
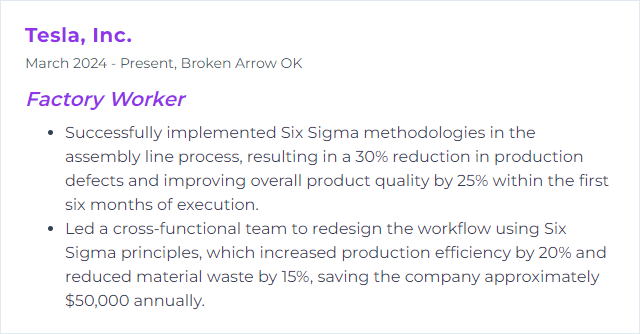
9. Inventory Management
Inventory management for a factory worker involves tracking and organizing materials and products to ensure that the right amount is available for production and that there's no overstocking or running out of supplies.
Why It's Important
Inventory management is crucial for a factory worker because it ensures the right materials are available when needed, preventing work stoppages and maximizing productivity.
How to Improve Inventory Management Skills
Improving inventory management, especially from a factory worker perspective, involves a mix of organization, technology, and process optimization. Here are concise tips:
Utilize Inventory Management Software: Adopt software that provides real-time tracking of inventory levels and materials. This guide from Software Advice offers a comparison of inventory management software options.
Implement Lean Inventory Practices: Reduce waste and improve efficiency by adopting lean inventory methods. Lean.org provides resources and principles on lean thinking and practices.
Regular Inventory Audits: Conduct regular checks to reconcile physical stock with inventory records. Squareup’s guide outlines steps for performing an inventory audit.
Improve Forecasting: Use historical data and trends to better predict inventory needs. This article from the Balance Small Business explains demand forecasting basics.
Enhance Employee Training: Ensure workers are trained on best practices in inventory management. OSHA offers training resources that can be adapted for inventory management practices.
Adopt Automation and IoT: Utilize automation and Internet of Things (IoT) devices for tracking and managing inventory efficiently. IoT For All shares insights on how IoT can transform inventory management.
By integrating these strategies, factory workers can contribute significantly to improving inventory management systems.
How to Display Inventory Management Skills on Your Resume
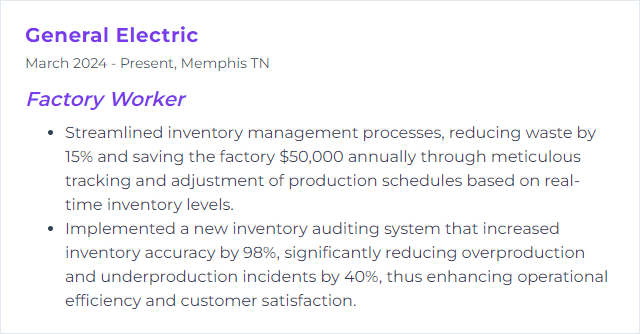
10. CAD Software
CAD software, short for Computer-Aided Design software, is a tool used to create, modify, and analyze precise drawings and technical designs, helping in planning and visualizing projects before they are built or manufactured.
Why It's Important
CAD software is important for factory workers because it allows for precise design and modification of parts or products, improves communication through detailed visualizations, and enhances productivity by streamlining the manufacturing process.
How to Improve CAD Software Skills
Improving CAD software for factory workers involves focusing on usability, integration, and training enhancements to accommodate their specific needs. Here's a concise guide:
User-Friendly Interface: Simplify the interface to focus on tools and features most relevant to factory workers. This can include customizable toolbars and easy-to-navigate menus. Autodesk discusses interface customization for enhanced usability.
Enhanced Integration: Ensure CAD software integrates seamlessly with manufacturing systems (like CAM or CNC software) for efficient design-to-production workflows. SOLIDWORKS offers solutions on integration for streamlined processes.
Real-Time Collaboration: Implement features that allow for real-time collaboration among workers, engineers, and designers. This enhances problem-solving and design efficiency. Onshape emphasizes collaboration in CAD software.
Mobile Access: Provide mobile access to CAD files and tools, enabling factory workers to view and comment on designs directly from the factory floor. Fusion 360 supports mobile access for on-the-go design reviews.
Training and Support: Offer tailored training programs and resources to help factory workers get the most out of the CAD software. Regular updates and support can help address specific challenges they face. Siemens provides industry-focused training solutions.
By focusing on these areas, CAD software can be more effectively tailored to the needs of factory workers, enhancing productivity and efficiency in the manufacturing process.
How to Display CAD Software Skills on Your Resume
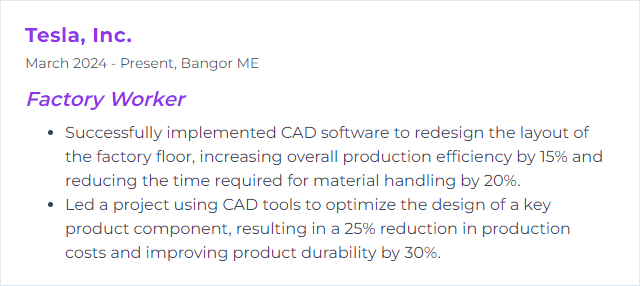
11. Robotics Programming
Robotics programming involves writing the instructions or code that control a robot's actions and decisions, enabling it to perform tasks in a factory setting, such as assembling products, handling materials, or conducting inspections.
Why It's Important
Robotics programming is crucial for factory workers as it enhances efficiency and precision in production processes, reduces human error, and minimizes the risk of workplace injuries by automating repetitive and hazardous tasks.
How to Improve Robotics Programming Skills
Improving robotics programming, especially for a factory worker, involves a mix of foundational learning, hands-on practice, and continuous skill upgrades. Here’s a concise guide:
Foundational Learning: Start with understanding the basics of robotics and programming languages commonly used, such as Python or C++. MIT's Introduction to Robotics offers a comprehensive start.
Hands-On Practice: Apply your knowledge through projects or simulations. Platforms like Tinkercad allow you to experiment with circuits and code online.
Specialize in Industrial Robotics: Familiarize yourself with specific robots used in factories. Universal Robots Academy offers modules on programming collaborative robots.
Stay Updated: Robotics technology evolves rapidly. Follow IEEE Robotics and Automation Society for the latest research and trends.
Networking and Community Learning: Engage with communities on platforms like Robotics Stack Exchange to solve doubts and learn from experiences of others.
Remember, consistent practice and staying abreast of new technologies are key to excelling in robotics programming in a factory setting.
How to Display Robotics Programming Skills on Your Resume
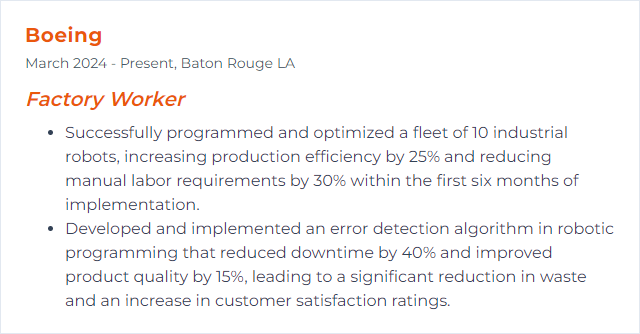
12. Safety Compliance
Safety Compliance, in the context of a factory worker, refers to adhering to established health and safety standards and regulations to protect workers from hazards and ensure a safe working environment.
Why It's Important
Safety compliance is crucial for factory workers to prevent accidents, reduce the risk of injuries, and ensure a safe working environment, ultimately protecting workers' health and well-being.
How to Improve Safety Compliance Skills
Improving safety compliance for a factory worker involves a multi-faceted approach focusing on education, environment, and enforcement. Here’s a concise guide:
Education and Training: Regularly conduct safety training sessions to educate workers on potential hazards and safe practices. Use interactive methods like simulations for better engagement (OSHA Training).
Safety Equipment: Ensure all workers are equipped with the necessary personal protective equipment (PPE) and understand how to use it correctly (NIOSH PPE).
Workplace Safety Standards: Adhere to workplace safety standards and regulations. Regularly inspect and maintain machinery and equipment to prevent malfunctions (ISO Safety Standards).
Safety Signs and Instructions: Clearly mark hazardous zones and provide detailed safety instructions throughout the workplace (ANSI Safety Signs).
Emergency Preparedness: Develop and regularly update emergency plans. Conduct drills to ensure everyone knows their role in an emergency (Ready.gov Business).
Feedback and Reporting: Encourage open communication about safety concerns. Implement a straightforward process for reporting hazards or incidents without fear of reprisal (OSHA Whistleblower Protection).
Health and Well-being Programs: Support worker health and well-being through programs that promote physical and mental health, recognizing that a healthy worker is a safer worker (CDC Workplace Health Promotion).
Safety Culture: Foster a culture that prioritizes safety, where every employee from management down is engaged in creating a safe working environment (NIOSH Safety Culture).
By integrating these elements, a factory can significantly improve safety compliance, creating a safer workplace for all employees.
How to Display Safety Compliance Skills on Your Resume
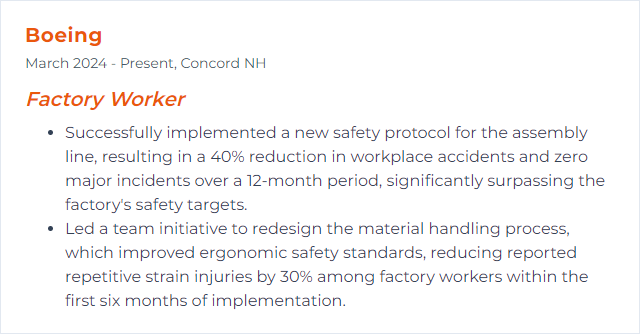